یکی از روشهای متداول برای فرم دهی و ساخت قطعات فلزی در ابعاد، اشکال و اندازههای متنوع، ریخته گری است. از زمانهای گذشته تا امروز، برای ساخت قطعات فلزی از مواد و فلزات مذاب مختلف استفاده میشد که پس از ریختن این مواد به داخل قالبهای مخصوص، قطعات تشکیل میشدند. ریخته گری، عملیات حاصل از تزریق مواد مذاب در قالب و شکل گیری آنها است.
ریخته گری به روشهای مختلف و با استفاده از قالبهایی با جنسهای متنوع انجام میشود. در این مقاله، یکی از روشهای متداول ریخته گری با نام ریخته گری چدن معرفی شده است. اگر میخواهید با این روش، ویژگیها و کاربردهایش بیشتر آشنا شوید، مطالعه این مقاله را از دست ندهید.
ریخته گری چدن چیست؟
چدن (Cast Iron) یکی از آلیاژهای پرکاربرد آهن است که از ترکیب آهن، کربن و سیلیسیم تشکیل میشود. ریخته گری چدن نیز یکی از روشهای متداول ریخته گری است که با استفاده از آن قطعات فلزی فرمدار ساخته میشوند. در واقع به شکلگیری و سخت شدن قطعات چدنی در فرایند ریخته گری، ریخته گری چدن میگویند.
ریخته گری چدن با استفاده از قالبهای ماسهای متداولتر است و غالبا در آن از ماسههایی استفاده میشود که مقاومت بیشتری نسبت به حرارت بالا داشته باشند؛ زیرا دمای ذوب چدن بسیار بیشتر از دمای ذوب آهن است.
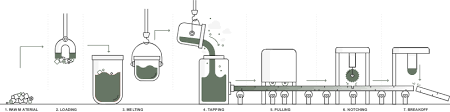
چدن قابلیت ریخته گری بسیار خوبی دارد. قطعاتی که با استفاده از چدن ساخته میشوند، غالبا دارای خاصیت ضد لرزشی هستند و در برابر خوردگی و پوسیدگی بسیار مقاوم میباشند. به همین دلیل ریخته گری قطعات چدنی کاربرد بسیاری در صنایع مختلف دارد.
انواع چدن در ریخته گری
چدن یکی از پرکاربردترین آلیاژهای آهن است که براساس شکل مقطعی و رنگ به دستههای مختلفی تقسیمبندی میشود. هر یک از انواع چدنها دارای ویژگیهای متفاوتی هستند. به عنوان مثال، برخی از گروههای چدن با افزودن آلیاژهایی مانند منگنز و گوگرد مقاومت بالاتری نسبت به سایر انواع چدنها دارند.
معروفترین و پرکاربردترین انواع چدن در ریخته گری عبارتند از:
چدن سفید (White Cast Iron)
اگر فرایند سرد شدن فلز با سرعت بیشتری انجام شده و میزان کربن نیز کاهش پیدا کند، چدن سفید به دست میآید. سطح شکست در این آلیاژها سفید است و به همین دلیل به نام چدن سفید شناخته میشوند. بیشترین قسمت کربنهای موجود در چدنهای سفید به صورت نیمه پایدار رسوب میکنند. همچنین کربیتها نیز در این چدنها آزاد هستند و باعث میشود که سختی و مقاومت آنها در برابر سایش افزایش پیدا کند. به همین دلیل معمولا از این چدنها در ساخت قطعاتی که نیاز به سختی و مقاومت بالایی در برابر سایش دارند، استفاده میشود. اما چقرمگی این چدنها پایین است که برای بهبود آن غالبا مقداری نیکل و کروم به ترکیب چدن افزوده میشود.
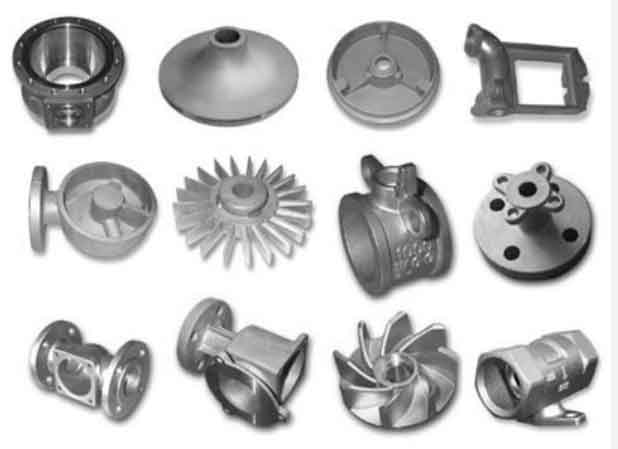
چدنهای سفید سه نوع غیر آلیاژی، کم آلیاژ و پرآلیاژ را شامل میشوند. چدنهای سفید غیر آلیاژی زمینه پرلیتی ریزی دارند. چدنهای پر آلیاژ یا نایهارد نیز مقدار 15 تا 30 درصد کروم را شامل میشوند و دو نوع کروم دار و نیکل کروم دارند.
چدنهای سفید پرآلیاژ کروم دار در مقابل اسیدهایی مانند اسید نیتریک بسیار مقاوم هستند و شامل 1 تا 4 درصد کروم میباشند. گرچه ممکن است برای افزایش مقاومت به خوردگی، اکسایش و سایش نیز میزان کروم آنها به 15 تا 35 درصد نیز افزایش پیدا کند. چدنهای سفید پر آلیاژ نیکل کروم نیز علاوه بر کروم شامل مقداری نیکل هستند که باعث پایداری گرافیت آنها شده و مقاومت به خوردگی و اکسایش را نیز افزایش میدهد.
چدنهای سفید بسیار ترد هستند و دارای سختی و مقاومت بالایی میباشند. به همین دلیل کاربردهای متنوعی در صنایع مختلف اعم از ساخت پرهها، غلتکها، پمپها، میلههای بالابر و… دارند. در واقع از این چدنها در مواردی استفاده میشود که نیاز به مقاومت بالا در برابر سایش سطحی وجود داشته باشد.
چدن خاکستری (Gray Cast Iron)
سطح مقطع شکست این چدنها و شکل گرافیت آنها خاکستری است و به همین دلیل با نام چدن خاکستری شناخته میشوند. چدنهای خاکستری در برابر سایش و درجه حرارت بالا بسیار مقاوم هستند و استحکام مکانیکی مطلوبی دارند. معمولا از این چدنها در ریخته گری فلزاتی استفاده میشود که دمای ذوب آنها 1250 درجه سانتیگراد باشد. از دیگر ویژگیهای چدنهای خاکستری میتوان به خاصیت الاستیک، جذب ارتعاش بالا و قابلیت ماشینکاری و تراشکاری آنها اشاره کرد.
چدنهای خاکستری دارای سیالیت بالاتری هستند و ریخته گری مقاطع پیچیده و نازک با استفاده از آنها آسانتر انجام میشود. غالبا از این چدنها زمانی استفاده میشود که استحکام فشاری بالا و پایداری ابعاد بهتر در قطعه مورد نظر نیاز باشد.
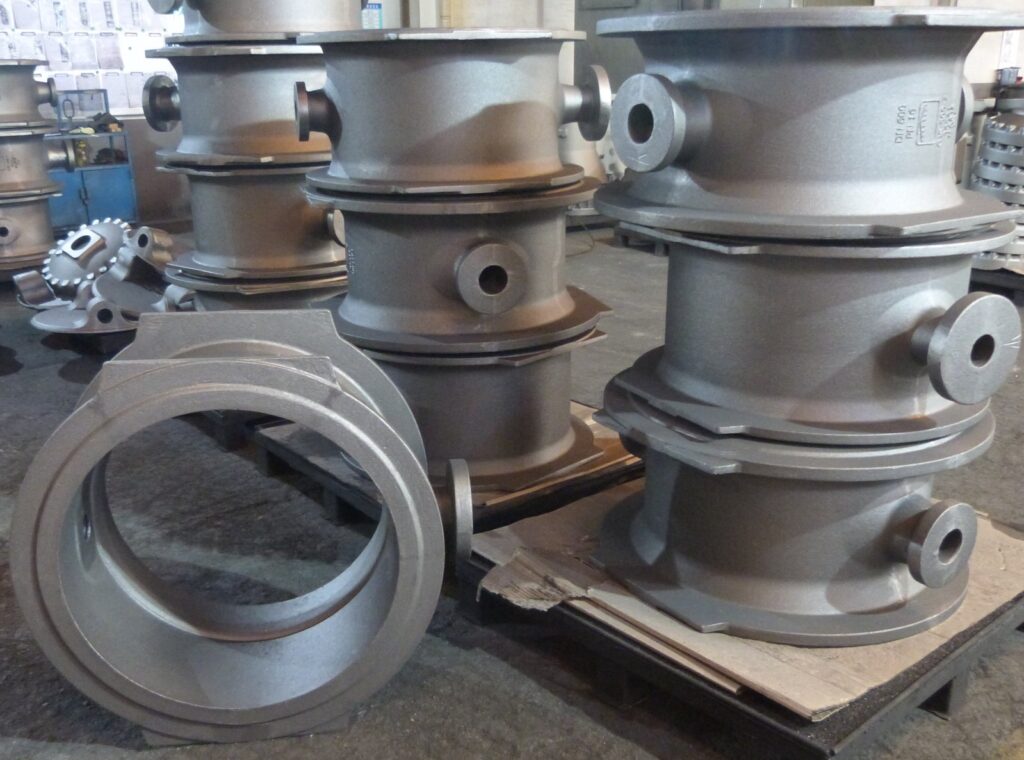
چدنهای خاکستری بر مبنای حداقل استحکام کششی انواع مختلفی دارند و بر این اساس به دو نوع هایپو یوتکتیک و هایپر یوتکتیک دستهبندی میشوند. به طور کلی چدن با 2 درصد سیلیس، ترکیب یوتکتیکی با 3.6 درصد کربن را دارد. اگر میزان این ترکیب بالاتر از میزان اصلی باشد، هایپر یوتکتیک و اگر پایینتر باشد، هایپو یوتکتیک است. همچنین براساس شکل نیز چدنهای خاکستری چهار نوع چدن خاکستری خاص، چدن خاکستری نیکلی، چدن خاکستری آب سرد و چدن خاکستری مقاوم به سایش را شامل میشوند.
این چدنها در صنایع مختلف بخصوص در مواردی که به ماشینکاری، جذب ارتعاش و انتقال حرارت بالا نیاز باشد، کاربرد دارند. از جمله متداولترین کاربرد آنها میتوان به ساخت پوسته گیربکس، دیسک ترمز، منیفولد، ظروف آشپزخانه مانند قابلمه، چرخ، بلوکهای سیلندر و… اشاره کرد.
چدن چکش خوار (Malleable Cast Iron)
چدنهای چکش خوار یا چدنهای مالیبل در ساختار خود دارای گرافیت نسبتا کروی هستند و به همین دلیل قابلیت کششی و انعطافپذیری بالایی دارند. این چدنها به سادگی به شکلهای پیچیده تغییر شکل میدهند و خم میشوند؛ بدون اینکه دچار ترکیدگی و یا شکستگی شوند. به همین دلیل با نام چدن چکش خوار شناخته میشوند.
از جمله ویژگیهای این چدنها میتوان به قابلیت ریخته گری بالا، چقرمگی مطلوب، قابلیت شکلپذیری بالا، مقاومت در برابر خوردگی و یکنواختی کامل ناشی از عملیات حرارتی اشاره کرد. این چدنها نیز براساس حداقل استحکام کششی دستهبندی متنوعی اعم از نوع نشکن و خاکستری را شامل میشوند.
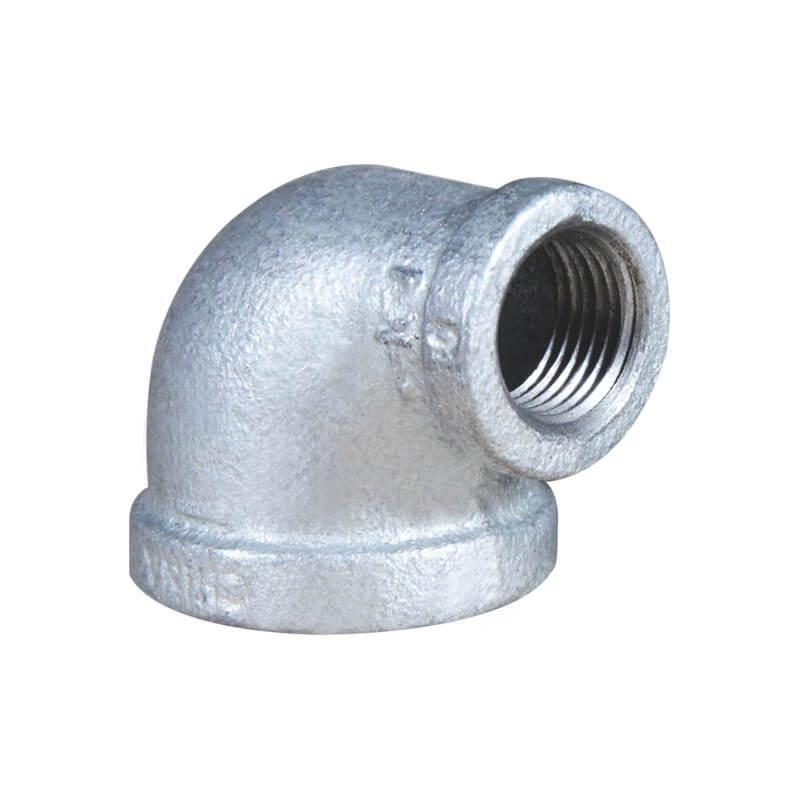
چدن چکش خوار در صنایع مختلف اعم از ساخت قطعات پرتابل مانند صندلیها، میزها، قطعات هنری، قطعات خودرو، واگنهای راه آهن، قطعات تحت فشار بالا، اهرمها، محورها و دندههای چرخ، کفشک ترمز و… کاربرد دارد. خواص و کاربردهای این چدن کاملا به درجه حرارت، پردازش و مقدار کربن آنها بستگی دارد
چدن گرافیت فشرده (Compressed graphite Cast Iron)
چدنهای گرافیت فشرده ساختاری لوزی شکل یا ستارهای شکل دارند. ظاهر این چدنها، چیزی بین ساختار چدنهای خاکستری و چدنهای سفید است. چدنهای گرافیت سفید از ترکیب چدن همراه با سیلیسیم، منگنز و مولیبدن به دست میآیند. این عناصر باعث میشوند که گرافیت ریز شده و در نتیجه آن باعث فشرده شدن ساختار گرافیت میشوند.
به دلیل این ویژگی، این چدنها در برابر شوکهای حرارتی بسیار مقاوم هستند و غالبا از آنها در ساخت قطعاتی استفاده میشوند که نیاز به مقاومت در شرایط حرارتی بالا دارند. چدنهای گرافیت فشرده، در برابر شوک و خوردگی مقاومت بالاتری نسبت به چدنهای خاکستری دارند، اما فرآیند تولید آنها هزینههای بیشتری را نسبت به چدنهای خاکستری شامل میشود.
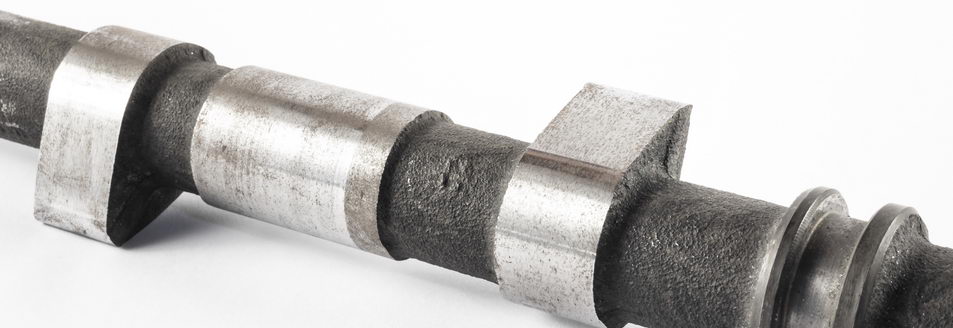
از ویژگیهای مهم دیگر این چدنها میتوان به مقاومت مکانیکی بالای آنها و مقاومت آنها در برابر خوردگی اشاره کرد. به دلیل این ویژگیها نیز از چدنهای گرافیت فشرده در ساخت قطعاتی که نیاز به مقاومت در برابر خوردگی دارند، استفاده میشود. از جمله کاربردهای متداول این چدنها میتوان به کاربرد آنها در ساخت قطعات سیستم ترموکوپل و دیسک، قطعات مورد نیاز در صنایع نفت گاز، قطعات مربوط به ماشین آلات، قطعات خودرو، قطعات صنعتی، قطعات مورد استفاده در صنعت هوا و فضا و… اشاره کرد.
چدن نشکن (Unbreakable Cast Iron)
چدن نشکن یا چدن داکتیل (Ductile Cast Iron)، از لحاظ ترکیب شیمیایی مشابه با چدن خاکستری است اما میزان گوگرد و فسفر آن کمتر است. ساختار این چدن با سایر چدنها تفاوت دارد و از استحکام بالاتری برخوردار میباشد. گرافیت موجود در ساختار چدنهای نشکن، کروی شکل میباشد و این ساختار باعث شده است که خواص و ساختار منحصر به فردی داشته باشند.
یکی از مهمترین ویژگیهای چدنهای نشکن، مقاومت بالای آنها در برابر ضربه و سایش است. در واقع قطعاتی که با استفاده از این چدنها ساخته میشوند، در مقایسه با قطعاتی که با چدن خاکستری ساخته میشوند، 3 برابر مقاومت بیشتری دارند. از دیگر ویژگیهای آنها میتوان به نقطه ذوب پایین، ماشین کاری مطلوب، مقاومت بالای در برابر سایش، استحکام و چقرمگی بالا و سیالیت و قابلیت ریخته گری خوب آنها اشاره کرد.
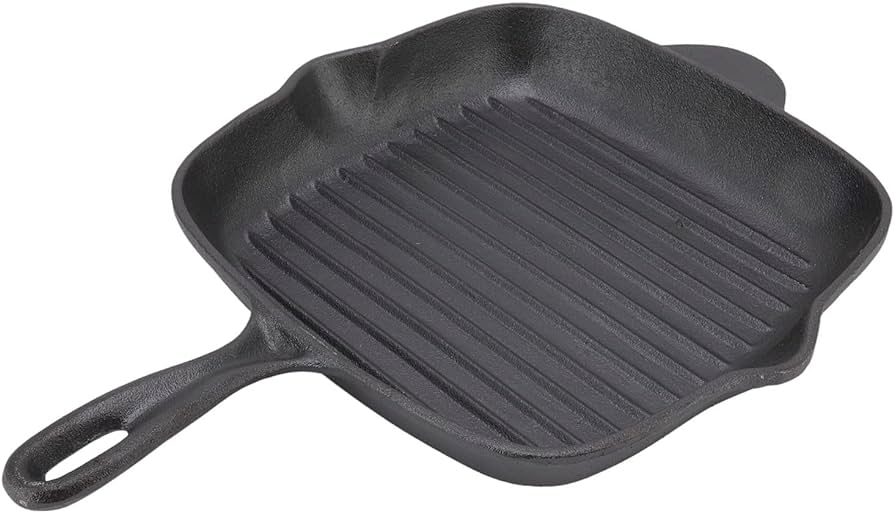
این چدنها انواع بسیار متنوعی اعم از چدنهای نشکن فریتی، آستنیتی، پرلیتی، مارتنزیتی، بینیتی و چدنهای نشکن آستمپرشده دارند که هر کدام ویژگیها و خواص بخصوصی را داشته و در کاربردهای مختلف مورد استفاده قرار میگیرند.
چدنهای نشکن نیز کاربردهای متنوعی در صنایع مختلف دارند که از جمله این کاربردها میتوان به استفاده از آنها در ساخت قطعات هیدرولیکی، پمپها، انواع ظروف و قالبها، چرخ دنده، بدنه شیرها و تلمبهها، غلتکها و میلنگها، چرخ دندههایی با استحکام بالا و… اشاره کرد.
روشهای انجام ریخته گری چدن
در ریخته گری چدن غالبا از عناصر آهن و سیلیسیم در کنار چدن استفاده میشود. برای تولید قطعات با استفاده از روش ریخته گری چدن روشهای مختلفی وجود دارد که از جمله متداولترین آنها میتوان به روشهای زیر اشاره کرد:
روش داکتیل
در روش داکتیل یا نشکنسازی، عناصری مانند منیزیم و سدیم به چدن افزوده شده و باعث تغییر کلی ساختار چدن میشوند. منیزیم باعث تغییر ساختار چدن شده و آن را کروی شکل میکند. همچنین باعث افزایش استحکام چدن در برابر کشش و خمشدن میشود و ساختار شکنندگی چدن را از بین میبرد.
روش ماسه حساس به CO2
اصلیترین موادی که برای قالب گیری در این روش مورد استفاده قرار میگیرند، ماسههای سیلیسی هستند. همچنین از چسبهای سیلیکات سدیم در این روش استفاده میشود. این چسبها با دمش گاز CO2 باعث ایجاد سیلیس شده و باعث میشوند که ذرات ماسه به هم چسبیده شوند و بعد از خروج قطعه نیز جای ماسه روی بدنه قالب باقی نمیماند. همچنین این روش دقت ابعادی بالاتر و تراشکاری کمتری را شامل شده و باعث میشود که در مرحله ریخته گری نیاز به استفاده از درجه وجود نداشته باشد.
روش ماهیچههای محافظ
ماهیچه یک بخش جدا از قالب است که باعث ایجاد محفظه داخلی در قطعات توخالی میشود. همچنین در قطعاتی که زائدههای خارجی آنها در یک سطح قرار ندارند، به جای قطعات آزاد از ماهیچه استفاده میشود. در مواردی که قطعات دارای شکل پیچیده هستند و در مواردی که نیاز به استحکام بالا در قالب وجود داشته باشد، به عنوان قسمتی از قالب یا تمام آن از ماهیچه استفاده میشود. اگر قالب ماهیچه پیچیده باشد و امکان کوبیدن ماسه به روش دستی وجود نداشته باشد، ماسه با فشار باد و در حالت دمش به قالب تزریق میشود.
فرآیند ریخته گری چدن
همانطور که خواندید، ریخته گری چدن به روشهای مختلفی انجام میشود؛ اما به طور کلی در ریخته چدن مراحل زیر دنبال میشوند:
مرحله اول: طراحی و تولید قالب اصلی
یکی از اصلیترین مراحل و ابتداییترین مرحله در ریخته گری، طراحی قالب است. طراحی و تولید قالبها دارای اهمیت زیادی است؛ زیرا اگر فرایند طراحی و یا تولید قالبها به درستی انجام نشود، قطعه نهایی نیز کیفیت مطلوب را نخواهد داشت. مواد اولیه که در تولید قالب مورد استفاده قرار میگیرند، با یکدیگر متفاوت بوده و بسته به نوع و کاربردشان به کار برده میشوند. قالبها دو نوع قالبهای موقت و دائمی دارند که هر کدام از آنها خود شامل انواع مختلفی هستند. قالبهای موقت، همانطور که از نامشان پیداست در تولید تعداد محدودی از قطعات مورد استفاده قرار میگیرند؛ در صورتی که قالبهای دائمی میتوانند در تولید تعداد زیادی قطعه استفاده شوند.
مرحله دوم: تولید درجه ریخته گری با دستگاه ریخته گری
درجه (فلاسک) ریخته گری، دستگاه ریخته گری یک طرفه است که برای قالب گیری استفاده میشود. استفاده از این دستگاه در ریخته گری ماسهای اهمیت بیشتری دارد. درجه یک چهار کلاف فلزی است که قالب اصلی را در بر میگیرد. ساخت درجه بر اساس مقدار ماسه و ارتفاع آن، ساخته میشود. این دستگاهها بسته به طرح و ابعادشان انواع مختلفی دارند. به عنوان مثال در ساخت بدنه آنها ممکن است از مواد مختلفی مانند مس و آلومینیوم استفاده شود.
انواع درجه ریخته گری عبارتند از:
- درجه گرانوله: برای آخال زدایی یا سربارهگیری از آلومینیوم استفاده میشود.
- درجه پودری: از نظر عملکرد همانند درجه گرانوله است. در برخی از انواع آن برای سربارهگیری و آخال زدایی از آلیاژ و مس استفاده میشود.
- درجه گرانوله و پودری: فاقد سدیم و کلسیم است و در آن برای سربارهگیری از آلومینیوم استفاده میشود.
پس از ساخت درجه، قالب اصلی درون آن قرار گرفته و قالب گیری آغاز میشود.
ریخته گری آلومینیوم یکی دیگر از انواع ریخته گری ها می باشد.
مرحله سوم: قالب گیری با ماسه ریخته گری
در این مرحله، درجه، قالب گیری شده و ماسههای CO2 به نحوی روی درجه قرار میگیرند که کل قالب پوشش داده شود. در برخی موارد برای افزایش ضخامت ماسه به آن ماسه بادی اضافه میشود که باعث سادگی تخریب قالب شده و هزینه ساخت قالب را کاهش میدهد. پس از آن ماسه با استفاده از کوبه کاملا فشرده میشود. پس از کوبیدن ماسه نیز، گاز CO2 به آن تزریق میشود تا کاملا سفت و محکم شود. برای اینکه فرایند تزریق گاز با سرعت بیشتری انجام شود، در قالب سوراخهایی ایجاد شده و گاز به داخل این سوراخها تزریق میشود. پس از تزریق گاز نیز قالب کاملا محکم میشود.
مرحله چهارم: ذوب چدن
در این مرحله، ضایعات بلوک و آهن جمع آوری شده و به کوره انتقال پیدا میکنند. با بالا رفتن دمای کوره، ضایعات آهنی و چدنی ذوب میشوند. معمولا دمای مورد نیاز برای ذوب چدن 1200 درجه سانتیگراد است؛ اما در برخی کارخانههای ریخته گری از دمای 1400 درجه سانتیگراد استفاده میشود. در واقع، دمای ذوب به مواد موجود در کوره بستگی دارد. در زمان ذوب مواد، غالبا مقداری کربن و سیلیس با توجه به یک سری استانداردها، به این مواد اضافه میشوند. در برخی کارخانهها این مواد ذوب شده به شمشهای چدنی تبدیل میشوند و در برخی کارخانهها این مواد مذاب مستقیما به قالبها منتقل میشوند.
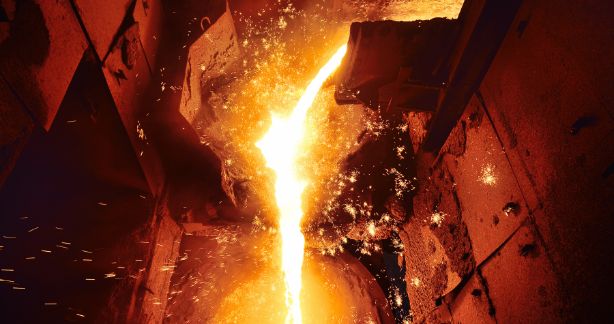
مرحله پنجم: جداسازی قالب ریخته گری
پس از اینکه مواد مذاب به داخل قالب ریخته گری ، ریخته شدند، سخت شده و باید از قالب جدا شوند. برای جدا کردن درجه از قالب اصلی روشهای مختلفی وجود دارد. این کار هم به صورت دستی و هم به صورت مکانیکی قابل انجام است. در روش دستی، درجه با دست از قالب جدا میشود. در روش مکانیکی نیز از لرزش دستگاه ویبراتور برای جدا کردن درجه از قالب استفاده میشود.
مرحله ششم: پرداخت قطعه
پس از جدا سازی قطعه ریخته گری شده از قالب، باید نقصهای احتمالی قطعه برطرف شده، سطح قطعه صاف و براق شود و وضعیت ظاهری قطعه بهبود پیدا کند. پرداخت قطعه فلزی در افزایش مقاومت آن بسیار تاثیرگذار است و باعث افزایش مقاومت قطعه در برابر سایش، خوردگی و تغییر شکل میشود. برای پرداخت قطعه، ابتدا یک لایه نازک برای پنهانسازی نقصها روی آن ریخته میشود. پس از آن نیز با استفاده از روشهای مختلف اعم از استفاده از دستگاه ریخته گری شات بلاست، آبکاری، برسکاری، پولیش، سنگزنی و پرداخت لرزهای، سطح قطعه کاملا تمیز و یکنواخت میشود.
کاربرد ریخته گری چدن
چدن کاربردهای متنوعی در صنایع مختلف دارد و غالبا از این متریال در ساخت قطعاتی استفاده میشود که کمتر به خواص ساختاری توجه شده و بیشتر به سختی و مقاومت سایشی بالا نیاز دارند. استفاده از چدن در ریخته گری قطعات به دلیل ویژگیهای مطلوب در کنار هزینه کمیکه شامل میشود، بسیار رایج است. بسته به چدن مورد استفاده و ویژگیهای مختلفی که هر یک از انواع چدن دارند، کاربرد ریخته گری چدن را میتوان در موارد زیر دسته بندی کرد:
چدن خاکستری: این چدن مقاومت بالایی در برابر سایش دارد و از آن غالبا برای ساخت بلوک موتور و سرسیلندر، منیفولد، مشعل گاز، جعبه دنده، محفظه و… استفاده میشود.
چدن سفید: این چدن شکننده است اما در برابر سایش بسیار مقاوم میباشد. از چدن سفید در تولید آستر آسیاب، نازلهای شات بلاست، کفشک ترمز راه آهن، محفظه پمپ دوغاب، رول آسیاب نورد و سنگ شکن بسیار استفاده میشود.
چدن داکتیل: همانطور که خواندید چدنهای داکتیل یا نشکن دارای انواع مختلفی هستند که هر یک از انواع آن دارای ویژگیهای مخصوص خود میباشند. به طور کلی، چدنهای داکتیل از انعطافپذیری مطلوبی برخوردار هستند، در برابر سایش مقاوم بوده و ماشینکاری و شکلپذیری آسانی دارند. از این چدن غالبا برای ساخت بند فرمان، قطعات گاو آهن، میل لنگ، چرخ دندههای سنگین، اجزای سیستم تعلیق خودرو و کامیون، قطعات هیدرولیک و لولای درب خودرو استفاده میشود.
چدن چکش خوار: از این چدنها برای ساخت سطوح باربر سنگین، زنجیرها، چرخ دندهها، میلههای اتصال، قطعات محرکه و محور، قطعات راه آهن، ماشین آلات کشاورزی و ساختمانی استفاده میشود.
چدن گرافیت فشرده: این چدن ترکیبی از ویژگیهای چدن خاکستری و چدن سفید را دارد و دارای استحکام و هدایت حرارتی مطلوبی است. از این چدن برای ساخت بلوکها و قالبهای موتور دیزل، آستر سیلندر، دیسکهای ترمز برای قطار، منیفولدهای اگزوز و صفحات دنده در پمپهای فشار قوی استفاده میشود.
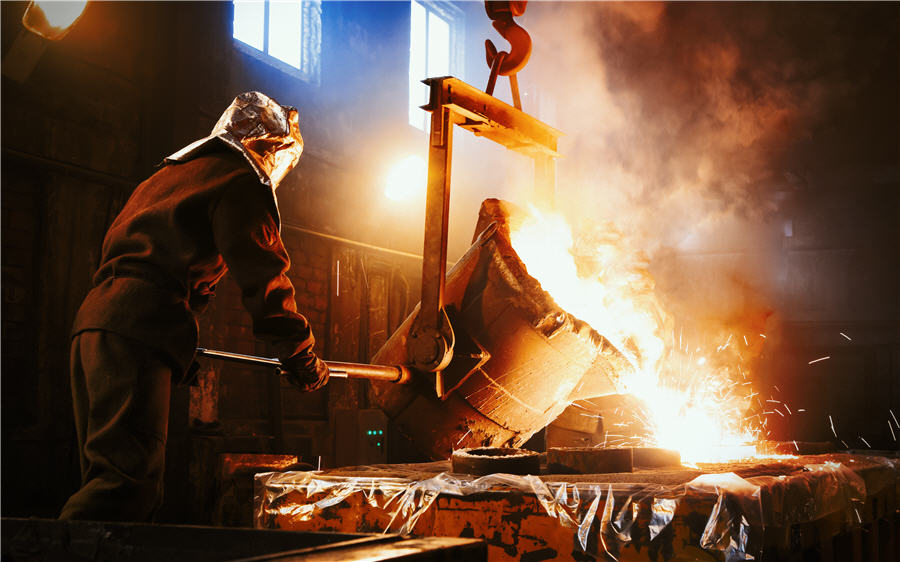
مزایا و معایب ریخته گری چدن با دستگاه ریخته گری چدن
ریخته گری چدن ویژگیها و مزایای فوقالعادهای که دارد؛ که از جمله مهمترین آنها میتوان به موارد زیر اشاره کرد:
- چدن دارای خواص ریخته گری مطلوبی است.
- چدن در مقادیر زیادی موجود است و میتوان از آن برای تولید قطعات در تیراژ بالا استفاده کرد.
- ابزاری که برای ریخته گری چدن مورد استفاده قرار میگیرند در دسترس و ارزان هستند.
- هزینه نهایی تولید محصول با استفاده از این فرایند مقرون به صرفه است.
- تولید قطعات با اشکال، اندازهها و ابعاد مختلف با استفاده از فرایند ریخته گری چدن غالبا امکانپذیر است.
- همچنین غالبا نیاز به ماشین کاری ثانویه در تولید قطعات به روش ریخته گری چدن وجود ندارد.
- استحکام چدن در حدود 3 تا 5 برابر بیشتر از فولاد است.
- انواع چدن بخصوص چدن خاکستری قابلیت ماشین کاری مطلوبی دارند.
- چدن و قطعات تولید شده با استفاده از چدن مقاومت بسیار بالایی در برابر سایش دارند.
- انواع چدن در برابر تغییر شکل مقاومت مطلوبی داشته و غالبا دارای انعطافپذیری بالایی هستند.
در کنار تمامیاین مزایا، ریخته گری چدن یک سری معایب را نیز شامل میشود که عبارتند از:
- چدن مستعد زنگزدگی است.
- استحکام کششی چدن غالبا ضعیف است.
- چدن در برابر ضربه مقاومت پایینی دارد.
- در مقایسه با فولاد، چدن از قابلیت ماشین کاری کمتری برخوردار است.
- چدن سفید غیرقابل ماشین کاری است.
- انواع چدن غالبا شکنندگی بالایی دارند.
سوالات متداول
چدن خاکستری چیست؟
چدن خاکستری یکی از انواع چدن مورد استفاده در ریخته گری است که دمای ذوبی در حدود 1250 درجه سانتیگراد داشته و سختی و استحکام بالایی دارد. این چدن، خاصیت الاستیک و جذب ارتعاش مطلوبی داشته و قابلیت ماشین کاری خوبی دارد. چدن خاکستری همچنین در مقابل فرسودگی و فشار نیز مقاوم است اما قابلیت چکش خواری ندارد. از چدن خاکستری در ریخته گری به طور متعدد برای تولید قطعات موتور ماشین، سر سیلندر، کاسه چرخ و غیره استفاده میشود.
ترکیبات چدن چیست؟
چدنها غالبا در ترکیب خود 2 تا 4 درصد کربن و 1 تا 3 درصد سیلیسیم دارند. کربنهای موجود در چدنها به صورت سمنتیت و یا به صورت گرافیت هستند. گرافیت پایدارترین حالت کربن است. وجود کربن به شکل سمنتیت یا گرافیت کاملا به ترکیب شیمیایی و فرآیند انجماد یا همان نرخ سرد شدن بستگی دارد. هرچه نرخ انجماد بیشتر باشد، سمنتیت بیشتری تشکیل خواهد شد. از طرفی، هرچه نرخ انجماد کمتر باشد، احتمال تشکیل گرافیت بیشتر میشود.
تفاوت بین چدن و فولاد چیست؟
مهمترین تفاوت بین چدن و فولاد، میزان درصد کربن موجود در آنها است. فولاد حداکثر دارای 2 درصد کربن است اما چدن بین 2 تا 4 درصد کربن در ساختار خود دارد. کربن نقطه ذوب پایینتری از فولاد دارد و میتواند در هر شکلی ریخته شود؛ زیرا در زمان انجماد انقباض کمتری دارد. از لحاظ خواص مکانیکی نیز چدن استحکام فشاری بالاتری دارد و فولاد دارای استحکام کششی بیشتری است.
جمع بندی
همانطور که خواندید، ریخته گری چدن یکی از روشهای ساخت فلزات است که با استفاده از آن میتوان قطعات فلزی متنوعی را در ابعاد و اندازههای مختلف و حتی با پیچیدهترین اشکال تولید کرد. قالبهایی که در این روش مورد استفاده قرار میگیرند، غالبا از جنس ماسه، خاک رس و یا فلز هستند. چدن، بسته به ساختار و ترکیبی که دارد، دارای خواص و ویژگیهای مختلفی است که هر کدام از انواع چدنها کاربردهای متنوعی در صنایع مختلف دارند.