یکی از ابتداییترین فرایندهای ماشین کاری، فرایند تراشکاری است که با استفاده از آن، ماده اولیه یا همان قطعه کار چرخش داده میشود و به وسیله یک ابزار برنده که جنس آن سختتر از قطعه کار است، سطح آن با حرکت خطی برش داده شده و قطعه نهایی ساخته میشود.
اگر میخواهید با این فرایند، ویژگیها و کاربردهایش بیشتر آشنا شوید مطالعه این مقاله از فبرینو را از دست ندهید.
تراشکاری چیست؟
به فرایند براده برداری، شکلدهی و شیارزنی سطوح داخلی و خارجی قطعات فلزی و غیرفلزی، تراشکاری (turning) گفته میشود که با استفاده از یکسری ماشین آلات و ابزارآلات مخصوص، توسط فردی به نام تراشکار انجام میشود.
در این فرایند، ابزار تراش روی قطعه مورد نظر اعمال شده و مواد اضافی را به منظور رسیدن به شکل و ابعاد مورد نظر حذف میکند. دستگاهی که در این فرایند مورد استفاده قرار میگیرد غالبا یک دستگاه تراش است که به وسیله حرکت دو محوره چرخشی و خطی، ابزار تراش را در تماس با قطعه قرار میدهد. در واقع محور حرکت قطعه کار میتواند خط صاف یا در راستای مجموعهای از منحنیها و زوایا باشد.
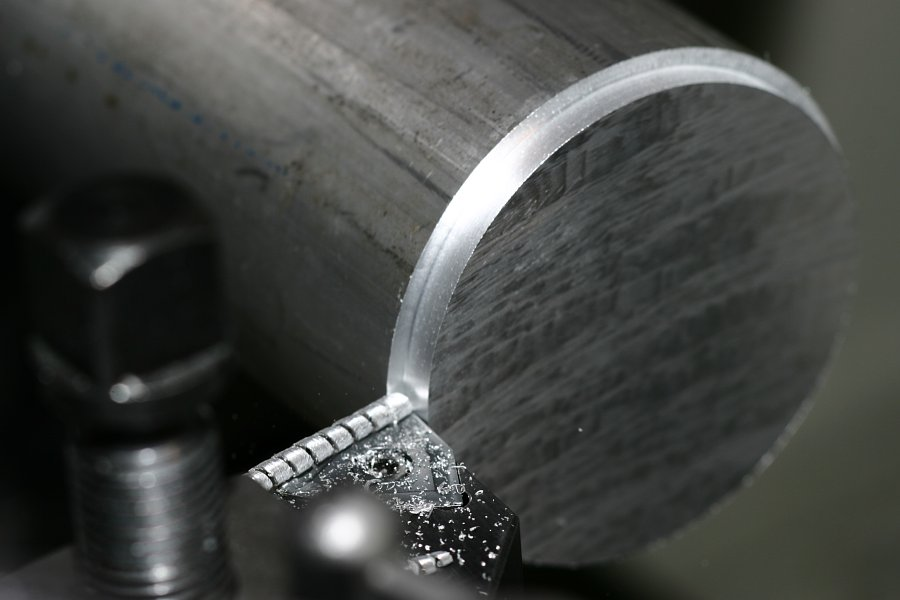
حذف لایه اضافی از قطر بیرون قطعه در این فرایند غالبا به شکل استوانهای است؛ اما برای ایجاد اشکال دیگر نیز قابل استفاده میباشد. برای کاهش قطر قطعه کار و ایجاد یک سطح صاف روی فلز فرایند تراشکاری بسیار کاربردی میباشد و اغلب به گونهای چرخانده میشود که بخشهای مجاور قطرهای متفاوتی نسبت به یکدیگر داشته باشند. تراش کاری در واقع برادهبرداری سطح خارجی قطعه کار است و به براده برداری سطح داخلی قطعه کار، بورینگ گفته میشود.
این فرایند هم به صورت دستی و هم به صورت اتوماتیک قابل انجام است. در روش سنتی، تراش کاری به شکل دستی و با استفاده از یک ماشین تراش معمولی انجام میشود که غالبا به نظارت مداوم اپراتور نیاز دارد. در حالت اتوماتیک نیز تراش کاری قطعات غالبا با کمک دستگاههای CNC انجام میشود.
تراشکاری یکی از قدیمیترین روشهای فرمدهی قطعات است که به دلیل ویژگیهای فوق العاده و قابلیتهایی که دارد، امروزه نیز به عنوان یک روش پرکاربرد در تولید شناخته میشود.
فرایند تراشکاری
دستگاههای تراش قدیمیترین ابزارهای تراشکاری و ماشین کاری هستند که فرایندهای تراش کاری غالبا توسط این دستگاهها انجام میشود. با فرایندهای تراش کاری میتوان اشکال مختلفی مانند سیلندر، مخروط، منحنی و یا شیاردار را تولید کرد.
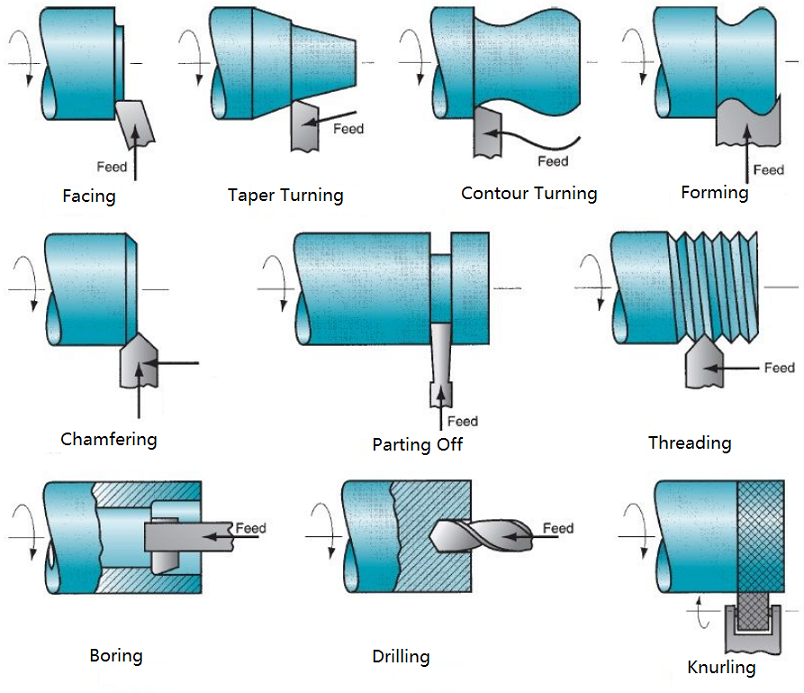
تراشکاری با فرایندهای مختلفی قابل انجام است که از جمله رایجترین این فرایندها میتوان به موارد زیر اشاره کرد:
- روتراشی: در این فرایند تراشکاری، یک ابزار چرخشی تک نقطهای در امتداد قطعه کار، به صورت محوری حرکت کرده و باعث جدا شدن مواد میشود. در اینصورت اشکال مختلفی اعم از پلهها، مخروطیها و خطوط با این فرایند ایجاد خواهند شد. این ویژگیها غالبا در عمق شعاعی کوچک برش ماشینکاری شده و تا رسیدن به قطر نهایی روتراشی چندین بار انجام میشود.
- تراشکاری مخروطی: فرایند مخروطی یک شکل استوانهای ایجاد میکند. در این فرایند به تدریج قطر قطعه از یک سر به سر دیگر کاهش مییابد.
- پیشانی تراشی: پیشانی قسمت ابتدایی یا انتهایی قطعه کار است. در این فرایند یک ابزار چرخشی تک نقطهای در امتداد انتهای قطعه به صورت شعاعی حرکت کرده و یک لایه نازک از مواد را جدا میکند. با این کار سطح کار کاملا صاف خواهد شد. عمق پیشانی معمولا بسیار کوچک است و ممکن است در یک گذر، ماشینکاری شده یا با ماشین کاری در عمق محوری کوچکتر به آن برسد.
- شیار تراشی: در این فرایند، قلم شیار تراش داخل قطعه در امتداد شعاع آن نفوذ میکند و روی سطح خارجی قطعه استوانهای، شیاری برابر با پهنای قلم ایجاد میشود.
- بورینگ: در فرایند بورینگ یک ابزار تراشکاری به صورت محوری وارد قطعه کار شده و قطعه را در امتداد یک سطح داخلی برش میدهد. با این کار اشکالی مانند پلهها، مخروطیها و خطوط ایجاد میشوند. ابزار مورد استفاده در این فرایند یک ابزار حفاری برش تک نقطهای است که میتوان از آن با تنظیم سر مته، برای برش قطر دلخواه استفاده کرد. عملیات بورینگ یا حفاری غالبا پس از سوراخکاری انجام میشود تا قطر قطعه بزرگتر شده یا ابعاد دقیقتری در قطعه ایجاد شود.
- پیچ تراشی: برای انجام این فرایند از رندههای پیچبری استفاده شده که جزئی از رندههای فرم هستند. در استفاده از آنها، باید فرم لبه برنده رنده با فرم شیار دندانه پیچ مطابقت داشته باشد. در اینصورت با استفاده از ابزار مخصوص و میله هادی، از روشهای گرداندن قطعه یا از ساعت پیچ تراشی استفاده شده و پیچ تراشیده میشود.
- برق کاری: در فرایند اندازهگیری، مقداری از فلز از سوراخی که قبلا حفر شده است، جدا میشود. از این فرایند برای ایجاد سوراخهای داخلی با قطرهای بسیار دقیق استفاده میشود. به عنوان مثال، در ابتدا یک سوراخ با مته با اندازه متفاوتی ایجاد شده و سپس به ابعاد دقیق تبدیل میشود.
- قلاویز زنی: در این فرایند، یک قلاویز صورت محوری، از قسمت انتهایی قطعه کار وارد آن شده و رزوههایی داخل سوراخ موجود تراش میدهد. قلاویز مورد استفاده در این فرایند باید هم قطر با متهای که سوراخ را ایجاد کرده است، باشد.
- آجزنی: در این فرایند روی قطعه کار، شیارهای منظمی با اشکال مورد نیاز ایجاد میشوند.
انواع تراشکاری
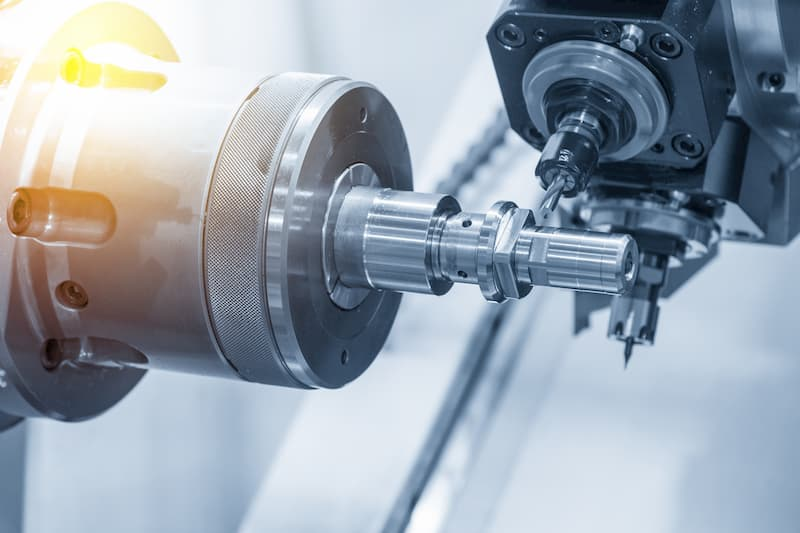
در حالت کلی، تراشکاری شامل سه نوع مختلف، تراش کاری دستی، تراش کاری با فرز و تراش کاری CNC است؛ که در ادامه هر یک از این تراشکاریها معرفی شدهاند.
- تراشکاری دستی: این نوع همان حالت سنتی است که در آن فرایندهای تراش کاری به صورت دستی و توسط ماشین تراشهای معمولی انجام میشوند. استفاده از این نوع تراشکاری غالبا نیاز به نظارت مداوم اپراتور دارد.
- تراشکاری فرز: فرزکاری برای برداشتن براده و صیقل دادن به سطوح با استفاده از دستگاهی به نام ماشین فرز انجام میشود. این ماشینها، براساس نوع قرارگیری تیغه فرز به دو نوع ماشین فرز افقی و ماشین فرز عمودی دستهبندی میشوند. در ماشینهای فرز افقی تیغه فرز به شکل افقی و در ماشینهای فرز عمودی تیغه فرز به شکل عمودی است.
- تراشکاری CNC: یکی از پرکاربردترین روشها در تراشکاری، استفاده از دستگاه تراشکاری CNC است. در فرایند تراشکاری CNC، میلههای مواد در یک حفره نگهداری شده و برای جدا کردن مواد و ایجاد شکل مورد نظر در قطعه از ابزارهای متناسب روی آن استفاده میشود. در این میان، یک محور در حال حرکت، به طور مداوم چرخانده خواهد شد.
با این کار، یک ساختار همانند یک برجک با ابزار متصل برنامه ریزی شده است و با نوار مواد خام حرکت کرده و منجر به حذف مواد میشود. در نتیجه، طرح برنامهریزی شده ایجاد خواهد شد.
ابزارهای تراشکاری
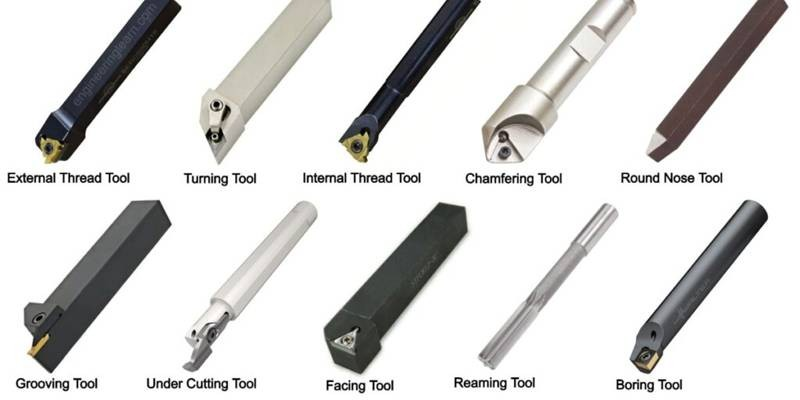
همانند تمامی فرایندهای صنعتی، برای انجام فرایندهای تراشکاری نیز، نیاز به استفاده از یکسری ابزار مخصوص وجود دارد؛ که رایجترین آنها عبارتند از:
- دستگاه تراش: از مهمترین ابزارهای تراش کاری است که قطعات کوچک روی این دستگاه نصب شده و آپشنهای جدیدی به آن اضافه میکنند. دستگاههای تراش کاری شکلها و اندازههای مختلفی دارند؛ اما کاربرد آنها به یکدیگر مرتبط است. با استفاده از آنها میتوان انواع مواد مختلف اعم از فلز و چوب را برش و تراش داده و شکلهای مختلفی مانند مخروط، استوانه و… روی آنها ایجاد کرد.
- دستگاه فرز: این دستگاه نیز یک دستگاه پرکاربرد برقی است که از لحاظ ظاهری بسیار شبیه به یک دریل رومیزی میباشد. از این دستگاه غالبا روی سطوحی نه چندان سخت، با کیفیت بالا استفاده میشود.
دستگاه فرز، سه محور حرکتی دارد که به کاربر این امکان را میدهد تا بتواند سطوح مختلف را شکل داده یا آنها را صیقل دهد. استفاده از این دستگاه هم به صورت ثابت و هم به صورت متحرک امکانپذیر است؛ به اینصورت که هم میتوان دستگاه را به قطعه نزدیک کرده و هم امکان نزدیک کردن و حرکت دادن قطعه وجود دارد.
- مته: این ابزار از مهمترین اجزای دریل است که به طور گسترده در سوراخکاری اشیاء مورد استفاده قرار میگیرد. با استفاده از مته میتوان سوراخهایی با سایزها و اندازههای متفاوت از نظر عمیق، طول و قطر ایجاد کرد. امکان نصب این ابزار روی دستگاههای مختلفی اعم از دریل، فرز، دستگاههای تراشکاری و… وجود دارد. از این ابزار برای سوراخکاری سطوح مختلفی مانند بتن، آهن، چوب، آلومینیوم، مس، مصالح ساختمانی و… استفاده میشود.
- تیغچه: از این ابزار در تراش کاری برای برش فلزات استفاده میشود. در صورت کند شدن تیغچه امکان تیز کردن مجدد سر آن وجود دارد.
- گیره: از ابزار گیره در تراش کاری برای نگه داشتن قطعات کار در جای خود استفاده میشود. این ابزار انواع و اندازههای گوناگونی دارند که میتوان از آنها در کاربردهای مختلف استفاده کرد. گیرهها همچنین از دو فک تشکیل شده و با یک مکانیسم پیچ و مهره یا سایر مکانیزمها به یکدیگر متصل شدهاند. فکها در گیره میتوانند از مواد مختلفی مانند چوب، فلز یا پلاستیک ساخته شوند.
انواع جنس ابزار تراشکاری
ابزارهای تراشکاری از جنسهای مختلفی تشکیل شدهاند که از مهمترین و رایجترین آنها میتوان به موارد زیر اشاره کرد:
- فولاد ابزار غیر آلیاژی (ws)
این نوع فولاد شامل 0.5 تا 1.5 درصد کربن است که در برابر دما غالبا تا 250 درجه سانتیگراد، سختی خود را حفظ میکند. از ابزار با جنس فولاد غیر آلیاژی، در تراش کاری فولاد نرم اعم از فولادهای آلیاژی کم کربن میتوان استفاده کرد.
- فولاد ابزار آلیاژی
این فولاد علاوه بر کربن شامل فلزات دیگری مانند کرم، ولفرام، وانادیوم، مولیبدن و کبالت آلیاژ شدهاند و دو نوع فولادهای کم آلیاژ و پرآلیاژ دارند. فولادهای کم آلیاژ غالبا تا 300 درجه سانتیگراد سختی خود را حفظ میکنند و فولادهای پرآلیاژ نیز میتوانند سختی خود را غالبا تا 600 درجه سانتیگراد حفظ کنند.
- فلزات سخت
این فلزات از مخلوط پودر کاربید برخی فلزات دیرگداز مانند کاربید، ولفرام، تیتان، تانتال، مولیبدن و وانادیوم همراه با پودر کبالت به عنوان چسب تولید میشوند. فلزات سخت ویژگیهایی اعم از سختی زیاد و مقاومت بالا در برابر سایش دارند. همچنین میتوانند تا 900 درجه سانتیگراد سختی خود را حفظ کنند.
- فلزات سرامیکی
قسمت عمده این فلزات از اکسید فلزات، آلومینیوم، سیلیسیم و کرم به عنوان فلزات سخت تشکیل میشود. مقاومت این فلزات بیشتر است و در برابر سایش 5 تا 10 برابر سختی بیشتری نسبت به فلزات سخت دارند؛ تا جایی که میتوانند تا 1200 درجه سانتیگراد، سختی خود را حفظ کنند. فلزات سرامیکی غالبا برای تراشیدن فولادهای سختکاری شده، استفاده میشوند.
دستگاه تراش
یکی از دستگاههای صنعتی پرکاربرد دستگاه تراش است که برای تراشکاری یا همان براده برداری در اثر چرخش قطعه، به کار گرفته میشود. کار اصلی دستگاههای تراش، تراش فلزات است که امروزه به دلیل گسترش مواد با خواص دیگر مانند مواد پلاستیکی، پلیمری و… از این دستگاه میتوان در برش این مواد نیز استفاده کرد.
دستگاه تراش در مرکز خود دارای یک نگهدارنده است که کاربرد آن را راحتتر کرده و عمل تراش را آسان میکند. در استفاده از این دستگاهها، میزان دقت و سرعت عمل بسیار اهمیت دارد و یک دستگاه تراش خوب با داشتن این ویژگیها شناخته میشود.
ماشین تراش به تراش عمومی، تراش دقیق و تراش با دقت بالا تقسیم می شود . ماشین های تراش دقیق و با دقت بالا معمولا بر اساس ماشین های تراش دقیق معمولی هستند.
16 نوع ماشین تراش
انواع دستگاه تراش
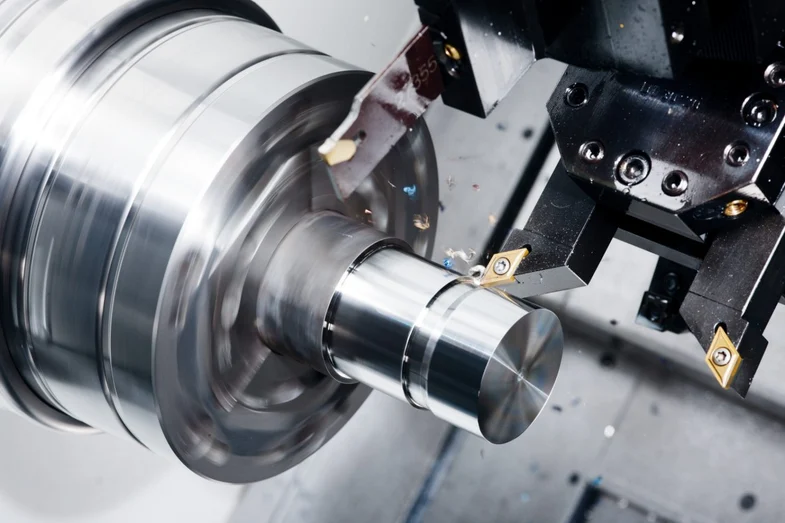
دستگاههای تراش براساس عوامل مختلف اعم از نوع عملیات ماشین کاری، اندازه و… انواع مختلفی دارند؛ که در ادامه رایجترین آنها معرفی شدهاند.
- دستگاه تراش مرکزی (Center lathe)
با استفاده از دستگاههای تراش مرکزی میتوان عملیاتی مانند تراشکاری، شیارزنی، رزوه کشی و… را انجام داد و به همین دلیل این دستگاهها کاربرد گستردهای در صنایع مختلف دارند. مکانیزم حرکت این دستگاه وابسته به چرخ دنده و قرقره است. در نمونههای اولیه این دستگاه برای تامین انرژی از موتور بخار استفاده میشد و به همین دلیل با نام تراش موتوری نیز شناخته میشود.
- دستگاه تراش سرعتی (Speed lathe)
این دستگاهها غالبا به صورت دستی کنترل شده و با آنها میتوان در سرعتهای بسیار بالا کار کرد. نمونههای رایج این دستگاه غالبا سرعتی بین 1200 تا 3600 دور در دقیقه را ارائه میدهند. دستگاههای تراش سرعتی برای پرداختکاری روی قطعات چوبی بسیار مناسب هستند و مکانیزم سادهای دارند. همچنین امکان استفاده از این دستگاه در تراش قطعات با عمق زیاد غالبا وجود ندارد. کار کردن با دستگاه تراش سرعتی نیاز به مهارت بالایی داشته و از آنها بیشتر در نجاریها و کارگاههای ریسندگی استفاده میشود.
- دستگاه کاپستان (Capstan and Turret lathe)
از این دستگاه تراش که به نوعی نمونه توسعه یافته دستگاه تراش مرکزی است، غالبا برای ماشین کاری قطعات بزرگ استفاده میشود. دستگاه کاپستان دارای قطر کارگیر یا محل نگهداری بزرگی است که قطعه را در دستگاه نگه داشته و ارتفاع نسبتا زیادی دارد. نسبت به دستگاههای دیگر، طول محور اصلی این دستگاه نیز بزرگتر است و امکان کنترل قطعات با طول بزرگ به راحتی روی آن فراهم میباشد.
در ماشینکاری قطعات بزرگ با این دستگاه نیازی به دور موتور بالای دستگاه تراش وجود ندارد. همچنین توان برادهبرداری این دستگاه بیشتر است و به سادگی امکان ماشین کاری روی قطعات بزرگ را فراهم میکند.
- دستگاه تراش ابزارسازی (Toolroom lathe)
این دستگاه بسیار مشابه با دستگاه تراش مرکزی است؛ اما در این دستگاه قطعات با دقت بیشتری طراحی و تولید میشوند. دستگاه تراش ابزارسازی در مقایسه با سایر دستگاهها قیمت بالاتری داشته و برای ماشین کاری با دقت بسیار بالا کاربرد دارد. محدوده سرعت عملکرد این دستگاه از دور موتورهای کم تا بیش از 2500 دور در دقیقه است. غالبا برای ماشینکاری قالب در صنایع مختلف از دستگاه تراش ابزارسازی استفاده میشود.
- دستگاه تراش رومیزی (Bench lathe)
این دستگاه ابعاد کوچکی داشته و روی میز قرار میگیرد. کاربرد و قطعات مورد استفاده از آن تقریبا مشابه با دستگاه تراش مرکزی است؛ با این تفاوت که دقت عملیات ماشین کاری با استفاده از این دستگاه غالبا کمتر از دستگاه تراش مرکزی است. دستگاههای تراش رومیزی قیمت مناسبی داشته و غالبا برای استفاده در کارگاههای خانگی بهترین گزینه محسوب میشوند.
- دستگاه تراش اتوماتیک (Automatic lathe)
یکی از بروزترین انواع دستگاه تراش، دستگاه تراش اتوماتیک است که امکان انجام عملیات ماشین کاری به صورت خودکار با استفاده از آن کاملا فراهم میباشد. با استفاده از این دستگاه، کار تراشکاری برای اپراتور سادهتر انجام شده و امکان کنترل چند دستگاه به طور همزمان فراهم میشود. این دستگاه وزن بسیار بالایی دارد اما سرعت عملکرد آن غالبا زیاد است.
قبل از استفاده از دستگاه تراش اتوماتیک، اپراتور باید تنظیمات لازم را روی آن انجام داده تا دستگاه به طور کاملا اتوماتیک عملیات را اجرا کند. همچنین امکان انجام انواع عملیات ماشین کاری توسط این دستگاهها به سادگی فراهم است.
- دستگاه تراش مخصوص (Special lathe)
برای انجام برخی عملیات تراشکاری نیاز به استفاده از ماشین تراش مخصوص وجود دارد. انواع دستگاههای تراش مخصوص رایج شامل دستگاههای تراش عمومی، دستگاههای چرخدار، دستگاههای چند محوره، دستگاههای تراش دو ردیفه و دستگاههای تراش ردیاب میباشند که برای تولید انواع قطعات بزرگ که نیاز به ماشینکاری پیچیده دارند، مورد استفاده قرار میگیرند.
- دستگاه تراش سی ان سی (CNC lathe)
این دستگاه یکی از پیشرفتهترین و جدیدترین انواع دستگاه تراش است که ماشینکاری در آنها با برنامه نویسی کامپیوتری انجام شده و کاربرد زیادی دارند. با استفاده از این دستگاهها عملیات تراشکاری با سرعت و دقت بسیار بالایی انجام میشود. از دستگاههای CNC به سادگی میتوان در تولید انبوه انواع مختلف قطعات استفاده کرد.
کاربرد انواع تراشکاری
تراشکاری عملیاتی رایج در صنایع امروزی است که کاربردهای بسیاری دارد. همانطور که خواندید، ابزارهای مورد استفاده در تراش کاری انواع مختلفی دارند که در کاربردهای متفاوت مورد استفاده قرار میگیرند. ابزارها و دستگاههای پیچیده تراش کاری نسبت به دستگاههای سادهتر از ساختار و روش پیچیدهتری نیز برخوردار میباشند. ماشین تراش که یک ابزار پیچیده است به عنوان یک دستگاه صنعتی در تراش یا برش بدون برادهبرداری کاربرد داشته و از آن در تولید و ساخت قطعات دوار استفاده میشود. در واقع، تقریبا تمامی قطعات دوار با استفاده از این ماشین ساخته میشوند.
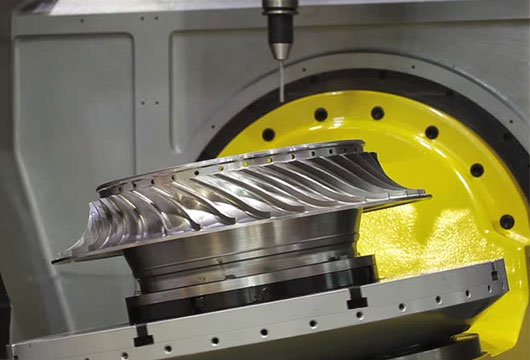
از ماشینهای تراشکاری غالبا برای ماشین کاری فلزات و شکل دادن به قطعات فولادی و آهنی مختلف و یا برای خراطی و نجاری اعم از ایجاد اشکال استوانهای و متقارن از صفحات چوبی، استفاده میشود. قطعات استوانهای که به کمک تراشکاری ساخته میشوند، دارای ویژگیهایی مانند رزوه، سوراخ، پله و… هستند. این قطعات غالبا در تعداد کم تولید میشوند و برای تولید نمونههای پروتوتایپ یا اولیه قطعات سفارشی مانند شفتها و اتصالات از تراشکاری بسیار بهره میبرند.
فرایند تراشکاری همچنین به عنوان یک فرایند تکمیلی در اضافه کردن ویژگیها روی قطعاتی استفاده میشود که شکل اولیه آنها با استفاده از روشهای دیگری مانند ریخته گری، برجینگ و یا محصولات نیمساخته تولید شدهاند.
از جمله رایجترین قطعات صنعتی ساخته شده به کمک تراشکاری میتوان به موارد زیر اشاره کرد:
- قطعات خودرو اعم از میل لنگ، میل بادامک، شاتون، پیستون، چرخ دنده، خار، سوپاپ، مهره، پیچ و برش
- قطعات پزشکی مانند ایمپلنت، پروتز، تجهیزات دندانپزشکی و ابزار جراحی
- تجهیزات صنعتی مانند پمپ، موتور، کمپرسور، شیر، دیفرانسیل، توربین، گیربکس و فن
- قطعات ماشین آلات مانند شفت، یاتاقان، بلبرینگ، پولی، کوپلینگ، پیچ، مهره، خار و بوش
- ابزار آلات مانند مته، چکش، آچار، رنده، فرز، قلاویز، تیغ فرز و سوهان
- قطعات هنری و تزئینی مانند مجسمه، ظروف، جواهرات و آلات موسیقی
- قطعات چوبی مانند نرده، پله، پایه مبل و دسته صندلی
در واقع، تراشکاری در صنایع مختلف بسیار کاربرد دارد و قطعات متنوع بسیار زیادی با استفاده از این فرایند تولید میشوند که در بالا تنها به رایجترین آنها اشاره شد.
مزایا و معایب
همانند تمامی فرایندهای صنعتی، فرایند تراشکاری نیز شامل یکسری ویژگیهای مختلف است. از جمله مهمترین مزایای این فرایند میتوان به موارد زیر اشاره کرد:
- امکان استفاده از تراشکاری برای انواع مواد وجود دارد و از آن علاوه بر تراشکاری فلزات میتوان برای تراشکاری چوب، پلاستیک و… نیز استفاده کرد.
- تراشکاری دقت بسیار بالایی دارد و قطعاتی که با استفاده از این فرایند ساخته میشوند غالبا دارای تلرانسهای بسیار دقیقی هستند.
- زمان تولید با استفاده از فرایند تراشکاری به دلیل سرعت بسیار بالای این فرایند، بسیار کوتاه است.
- استفاده از فرایند تراشکاری نیاز به اپراتور ماهر ندارد و اپراتورها تنها با گذراندن دورههای اموزشی کوتاه میتوانند از دستگاههای تراش به خوبی استفاده کنند.
- در این فرایند، قابلیت تنظیم سرعت بردارهبرداری وجود دارد و به سادگی میتوان سرعت آن را تنظیم کرد.
در کنار تمامی این مزایا، تراشکاری یکسری معایب را نیز شامل میشود؛ که عبارتند از:
- از فرایند تراشکاری تنها میتوان برای تراشکاری قطعاتی که قابلیت چرخش دارند، استفاده کرد.
- برای تولید یک قطعه، تراشکاری میتواند تنها یکی از فرایندهای مورد نیاز باشد و در کنار آن چندین فرایند دیگر انجام شود.
- قیمت تجهیزات در این فرایند بسیار بالا است و ماشینهای تراش، به خصوص ماشینهای CNC، غالبا قیمت بالایی دارند.
- ابزار در این فرایند استهلاک بالایی دارند و در واقع حرکت تکراری ابزار در فرایند تراشکاری منجر به استهلاک بالای این ابزار میشود.
- در این فرایند، همانند بسیار از فرایندهای ماشین کاری، مقداری ضایعات فلزی اعم از تراشه یا براده تولید میشود.
سوالات متداول
تراشکاری سنتی و صنعتی چه تفاوتی با یکدیگر دارند؟
در تراشکاری صنعتی، فرایند تراشکاری به صورت دستی و با استفاده از دستگاه تراش دستی انجام میشود. در اینصورت نیاز به حضور مداوم اپراتور وجود خواهد داشت. اما در تراشکاری صنعتی، تمام مراحل این فرایند کاملا به صورت اتوماتیک و با استفاده از دستگاههای تراش اتوماتیک انجام میشود که از رایجترین آنها میتوان به دستگاه تراش CNC اشاره کرد.
چه مهارتهایی برای انجام تراشکاری مورد نیاز است؟
تراشکار و یا اپراتور ماهر تراشکاری باید در زمینه این فرایند دانش کافی داشته و همچنین تجربه عملی مفیدی برای انجام این فرایند داشته باشد. از طرفی، داشتن نیروی جسمانی، داشتن توانایی لازم در نقشه خوانی و نقشه کشی، توانایی انجام کارهای فلزکاری، جوشکاری، سرویسدهی دستگاهها و آج زدن قطعهها و داشتن آشنایی کافی با متریالهای صنعتی اعم از انواع فلزات و یا انواع پلیمرهای صنعتی و آشنایی با دستگاههای مختلف تراشکاری از دیگر مهارتهای لازم برای انجام فرایند تراشکاری است.
تراشکاری در چه صنایعی کاربرد دارد؟
در فرایند تراشکاری از ابزارها و دستگاههای متنوعی استفاده میشود که هر کدام ویژگیهای خاص خود را دارند. به همین دلیل این فرایند در صنایع مختلف بسیاری اعم از ساخت و تولید قطعات صنعتی، ساخت ماشین آلات، ابزارآلات، خودروها، صنایع تجهیزات پزشکی و… کاربرد دارد.
انواع مختلف تراشکاری چیست؟
تراشکاری انواع مختلفی اعم از تراشکاری دستی، تراشکاری فرز و تراشکاری CNC را شامل میشود که هر کدام بسته به ویژگیهایشان در کاربردهای مختلف مورد استفاده قرار میگیرند.
جمع بندی
تراشکاری فرایندی است که از آن به روش برادهبرداری یا با استفاده از ماشین تراشکاری، برای شکلدهی فلزات استفاده میشود. در این فرایند، فلز عمدتا به شکل استوانه بوده و با قدرت و سرعت معینی میچرخد. در اینصورت با حرکت تیغچههای تراشکاری روی قطعه، عملیات براده برداری با عمق و سرعت معینی انجام خواهد شد. فرایند تراشکاری انواع مختلفی داشته و در آن از ابزارهای گسترده و متنوعی استفاده میشود؛ به همین دلیل در صنایع مختلف بسیار پر کاربرد است.
برای انواع برشکاری و ماشین کاری با دقت بالا برای ساخت انواع ابزارآلات و قطعات با فبرینو تماس بگیرید. پروژه کوچک و بزرگ خود را به ما بسپارید و از ایده تا اجرا با خیالی آسوده پروژه خود را با فبرینو دنبال کنید.