برای ساخت قطعات فلزی، روشهای زیادی وجود دارد که یکی از متداول ترین این روشها ریخته گری است. ریخته گری یکی از قدیمیترین روشهای تولید قطعات و ابزارهای فلزی است که بسیار کاربرد دارد. ریخته گری روشهای مختلفی را بسته به جنس مواد، فرایند ساخت، کاربرد، قطعه نهایی تولید شده و… شامل میشود که از رایج ترین این روشها میتوان به ریخته گری ماسه ای اشاره کرد.
اگر میخواهید با روش ریخته گری ماسه ای، ویژگیها و کاربردهای این روش بیشتر آشنا شوید، مطالعه این مقاله را از دست ندهید.
روش ریخته گری ماسه ای چیست؟
ریخته گری ماسه ای (Sand Casting) یک فرآیند ریخته گری است که در آن از قالبهای ماسه ای برای ایجاد قطعه فلزی مورد نظر استفاده میشود. با استفاده از این روش میتوان قطعات و ابزارهای فلزی متنوعی را در صنایع مختلف، با استفاده از قالبهای ماسه ای تولید کرد.
روش ریخته گری ماسه ای قدمت بالایی دارد به طوری که این روش در چین باستان ظهور پیدا کرده است. به دلیل اهمیت افزایش تولید قطعات فلزی و اهمیت مقرون به صرفه بودن ساخت آنها، این روش کاربرد گسترده ای در صنایع تولیدی دارد؛ تا جایی که امروزه این روش به عنوان کاربردی ترین و رایج ترین روش تولید قطعات فلزی شناخته شده و مورد استفاده قرار میگیرد.
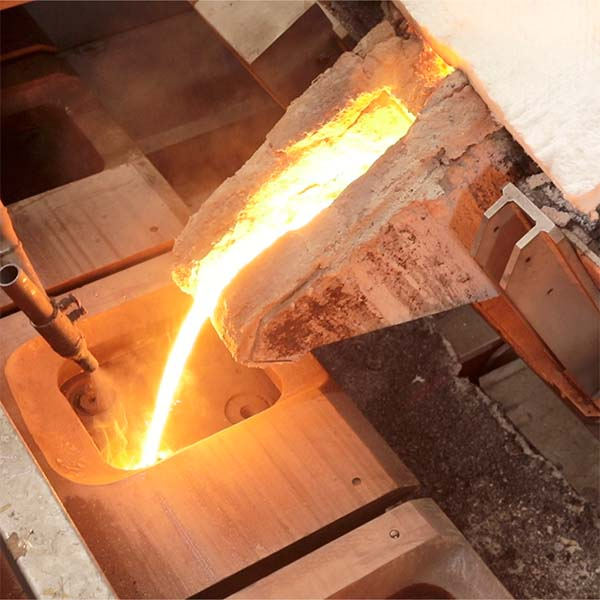
ماسه ای که در این روش مورد استفاده قرار میگیرد، نسبتا ارزان است و عایق بندی خوبی دارد. کیفیت مواد اولیه مورد استفاده و کیفیت ماسه ای که برای قالب مورد استفاده قرار میگیرد، در کیفیت قطعه نهایی تولید شده تاثیرگذار خواهد بود. همچنین این فرایند باید با رعایت یک سری قواعد، همراه با مهارت و تجربه بالا امجام شود تا نتیجه مطلوبی را ارائه دهد.
ماسههای مورد استفاده در طراحی و ساخت مدل در ریخته گری ماسه ای
برای انتخاب ماسه مناسب ریخته گری عوامل متعددی مورد بررسی قرار میگیرند. مهم ترین عامل در انتخاب ماسه دانههای آن است. برای این منظور میتوان گفت که هر چه ماسه دارای دانههای ریزتر و گردتری باشد، قابلیت فشردگی بیشتری داشته و با استفاده از آن، سطح قالب صاف تر خواهد بود. در نتیجه ماسههایی که دانههای ریزی دارند استحکام قالب را افزایش میدهند؛ اما این ماسه قابلیت نفوذ پذیری کمیدارند. قابلیت نفوذ پذیر یا نشت پذیری قالبها و یا ماهیچهها این امکان ا ایجاد میکند که گازها و بخارهای آب ایجاد شده هنگام فرایند ریخته گری، به راحتی خارج شوند.
از طرفی، قالب باید قابلیت متلاشی شدن خوبی داشته باشد تا به هنگام خنک شدن امکان انقباض قطعه ریخته گری شده، به سادگی فراهم شود. در این صورت از ایجاد مسائلی مانند پارگی گرم (Hot Tear) یا ترک جلوگیری خواهد شد.
در نتیجه، انتخاب ماسه مناسب برای قالب ریخته گری بسیار دارای اهمیت است و باید قبل از قالب گیری ماسه آماده شود. در این صورت، ماسههایی که برای این فرایند مورد استفاده قرار میگیرند، باید خواص زیر را دارا باشند:
- نسوز باشند و بدون سوختن و یا از بین رفتن بتوانند دمای بالای مواد مذاب را تحمل کنند.
- انسجام و چسبندگی مطلوبی داشت باشند و بتوانند الگوهایی که در آنها ساخته میشوند را به خوبی حفظ کنند.
- قابلیت نفوذ پذیری داشته باشند به صورتی که گازهای شکل گرفته هنگام ریخته گری از داخل قالب و حفرههای آن به خوبی خارج شوند.
- قابلیت تخریب داشته باشند و پس از انقباض قطعه منجمد شده به سادگی تخریب شوند.
معمولا برای تولید قالب ماسه ای از ماسههای سیلیسی، زیرکنی، الیواین و کرومیتی استفاده شده و این ماسهها به صورتی با یکدیگر و یا با مواد دیگر ترکیب میشوند که بتوانند خواص بالا را ارائه دهند.
انواع ماسهها کاملا نسوز هستند و قابلیت انسجام و چسبندگی مورد نیاز در قالبهای ماسه ای نیز از ترکیب ماسهها با خاکهای رسی مانند بنتونیت، کائولینیت؛ ایلیت همراه با رطوبت ایجاد میشود. نفوذپذیری قالب نیز به عواملی مانند اندازه ذرات ماسه، مقدار و نوع رس یا ماده اتصال دهنده مورد استفاده، میران فشرده سازی و میزان رطوبت بستگی دارد. همچنین قابلیت تخریب قالب یا افزایش یک سری مواد طبیعی مانند سلولز که با حرارت سوخته و از بین میرود، تامین خواهد شد.
یکی از متداول ترین ماسههایی که در فرایند ریخته گری مورد استفاده قرار میگیرد، ماسه تر (Green Sand) است که از ترکیب 88 درصد ماسه سیلیسی، 9 درصد خاک رس و 3 درصد آب ساخته میشود که غالبا برای ترکیب آنها از میکسرهای مولر (muller mixer) استفاده میشود.
انواع ماسهها برای ریخته گری
ماسههایی که در فرایند ریخته گری مورد استفاده قرار میگیرند، براساس ویژگیهایشان انواع مختلفی دارند.
انواع ماسه از نظر نحوه یافت و دسترسی
این دسته بندی از ماسهها موارد زیر را شامل میشود:
ماسه طبیعی:
این ماسهها مستقیما از منابع طبیعی استخراج میشوند. از جمله این ماسهها میتوان به ماسههای کنار رودخانه و ماسههای بادی اشاره کرد که هیچگونه کار اضافی روی آنها انجام نمیشود. تنها این ماسهها برای بررسی عدم وجود آهک آزمایش میشوند. ماسههای رودخانه ای میزان گردی بیشتری داشته و شسته شده اند؛ به همین دلیل میتوانند در کیفیت سطحی قطعه تولید شده موثر باشند و به همین دلیل بیشتر مورد استفاده قرار میگیرند. در ماسههای بادی نیز مقداری خاک رس وجود داشته که منجر به افزایش خاصیت چسبندگی این ماسهها میشود.
ماسه مصنوعی:
ماسههای مصنوعی با شکستن سنگهای گرانیتی به دست میآیند. برای این منظور، منابع طبیعی شناسایی شده و برای حذف ناخالصیهایی مانند آهک، این ماسهها الک میشوند. در نهایت نیز خرد شده و گرد میشوند. ویژگی برتر ماسههای مصنوعی قابلیت تحمل دمای بالاتر این ماسهها است.
انواع ماسه از نظر شکل ظاهری
براساس این ویژگی، ماسهها به انواع زیر تقسیم بندی میشوند:
ماسههای گرد:
شکل ماسههای گرد در زیر میکروسکوپ، کروی شکل است. این ماسهها کیفیت سطحی بهتری را ایجاد میکنند و قابلیت عبور گاز از آنها بهتر است. اغلب ماسههای مصنوعی از انواع ماسههای گرد هستند.
ماسههای شبه گرد:
این نوع ماسهها در برخی قسمتها گرد هستند و در برخی قسمتها گوشه دار میباشند.
ماسههای گوشه دار:
این نوع ماسهها کاملا گوشه دار هستند و کاملا در هم چفت میشوند. همچنین ماسههای گوشه دار در برابر حرکات مذاب، فشار مذاب، حمل و نقل و سایر موارد استحکام بیشتری دارند اما گاز کمتری را از خود عبور میدهند.
ماسههای مخلوط:
این نوع ماسهها شکل خاصی نداشته و ترکیبی از سه نوع دیگر ماسهها را شامل میشوند.

انواع ماسه از نظر ترکیب شیمیایی
متداول ترین دسته بندی ماسههای ریخته گری مربوط به دسته بندی آنها براساس ترکیب شیمیایی است. بر این اساس ماسههای ریخته گری به موارد زیر تقسیم بندی میشوند:
ماسه سیلیسی (SiO2):
ماسه سیلیسی بیشترین کاربرد را در ریخته گری فلزات دارد. این ماسه ارزان قسمت است و دارای وزن سبکی میباشد. همچنین ساختار آن در دردماهای مختلف دچار تغییر میشود. به صورتی که این ماسه در دمای بالا، غالبا بالای 573 درج دچار تغییر شکل میشود و ممکن است ترک خورده و مواد مذاب از آن جاری شود.
این تغییر ساختار و فاز ماسه سیلیسی منجر به افزایش قابل توجه حجم آن میشود. اما از آنجایی که مماسه یک هادی حرارتی ضعیف است، تنها ماسه ای که در مجاورت حفره قرار گرفته باشد، داغ شده و منبسط میشود. باقی قسمتهای ماسه، غالبا خنک مانده و منبسط نمیشود. در این صورت ایجاد فشار مکانیکی زیادی میشود. به دلیل این گرمایش ناهموار، ممکن است ماسه در سطح حفره بشکند یا خم شود.
انبساط ماسه بیشتر برای قطعاتی رخ میدهد که سطحی بزرگ و مسطح دارند؛ زیرا انبساط قابل توجهی در یک سمت واحد رخ میدهد. با افزودن مواد مختلف به ماسه سیلیسی نیز میتوان به سادگی خواص آن را تغییر داد.
ماسه شاموتی (3Al2O3.SiO2)
این ماسهها مرغوبیت بیشتری نسبت به ماسههای سیلیسی دارند. ماسههای شاموتی دارای دیرگذاری هستند که مقدار آن هرچه بیشتر باشد، برای فرایند ریخته گری بهتر است. این ماسهها دارای انبساط و انقباض هستند و ترک میخورند. از این ماسهها که نارنجی رنگ هستند، غالبا در ریخته گری به صورت آجر و بدنه کوره استفاده میشود. ماسههای شاموتی بیشتر برای ریخته گری قطعات فولادی بخصوص فولاد آلیاژی و کم کربن مورد استفاده قرار میگیرند.
ماسه زیرکُنی (ZrO2.SiO2)
این ماسهها از ترکیب دو سنگ آذرین و سنگهای دگرگون شده، تولید میشوند. ماسههای زیرکنی قابلیت انتقال حرارت بالایی دارند و بهتر و سریع ماسه سیلیسی میتوانند مواد مذاب را سرد کنند. این قابلیت ماسههای زیرکُنی باعث شده است که قطعاتی که با استفاده از آنها ساخته میشود، خواص مکانیکی بهتری داشته باشد. نقطه ذوب این ماسهها بسیار بالا است و به سادگی ذوب نمیشوند؛ اما این ماسهها به دلیل قیمت بسیار بالایی که دارند، کمتر مورد استفاده قرار میگیرد. همچنین در صورت استفاده غالبا از این ماسه تنها برای لایه فوقانی استفاده میشود, تا هزینه استفاده از انها کاهش پیدا کند.
ماسه کرومیتی (FeCr2O4)
ماسه کرومیتی رنگ سیاهی دارد و از ویژگیهای آن میتوان به پایداری حرارت مناسب، انتقال حرارت مطلوب و نقطه ذوب بالا اشاره کرد. درصد سیلیکای این ماسه بسیار بسیار پایین است اما دمای ذوب بالایی در حدود 1850 درجه سلسیوس دارد. با استفاده از ماسه کرومیتی امکان ایجاد عیب در گاز مواد مذاب وجود دارد و از آن برای تولید ماهیچههایی که مقابل دمای بالا قرار میگیرند، استفاده میشود. همچنین قیمت آن نیز بالاتر است و به همین دلیل غالبا برای فولادهای آلیاژهای گران قیمت و یا برای ساخت مغزه از آن استفاده میشود.
ماسه اولیوین (2FeO.SiO2) + (2MgO.SiO2)
کیفیت این ماسهها چیزی بین ماسههای زیرکنی و ماسههای سیلیسی است. ماسههای الیوین سفید رنگ هستند و دیر گذاری بالایی دارند. پایداری این ماسهها از ماسههای سیلیسی کمتر است. همچنین انبساط حرارتی کمتری نسبت به ماسههای کرومیتی و زیرکنی دارند.
انواع قالب ریخته گری ماسه
قالبهایی که در ریخته گری ماسه ای مورد استفاده قرار میگیرند، براساس ویژگیها و کاربردهایشان انواع مختلفی دارند. متداول ترین این قالبها را میتوان در موارد زیر دسته بندی کرد:
قالبهای ماسه تر (Green Sand Molds)
ریخته گری با قالب ماسه تر متداول ترین روش مورد استفاده در ریخته گری فلزات آهنی و غیرآهنی است. برای ساخت این غالبها غالبا از ماسه، خاک رس، آب و مواد افزودنی استفاده میشود. ریته گری با استفاده از این قالبها از ارزان تری روشهای ریخته گری است که هزینه ابزارکمیرا نیز شامل میشود.

از قالبهای ماسه ای تر غالبا میتوان برای ریخته گری تمام فلزات، به جز تیتانیوم، استفاده کرد. همچنین در استفاده از این روش برای تعیین اندازه، شکل، وزن و پیچیدگی قطعه، محدودیت کمیوجود دارد. محدودیت طراحی در روش قالبهای ماسه تر، زبری سطح بالا و دقت ابعادی پایینی را شامل میشود . غالبا نیاز به ماشینکاری در استفاده از آن وجود ندارد. از این روش میتوان هم برای تولید قطعات در تیراژهای پایین و هم در تیراژهای بالا استفاده کرد. مهم ترن محدودیتهای این روش امکان وجود رطوبت بالای قالب و استحکام پایین آن است.
قالبهای ماسه خشک (Dry Sand Molds)
برخی از قالبهای ماسه ای قبل از مذاب ریزی در اجاق خشک میشوند؛ که به آنها قالبهای ماسه خشک گفته میشود. این قالبها از قالبهای ماسه ای تر استحکام بیشتری دارند. همچنین دقت ابعادی و صافی سطح در آنها بالاتر است. اما امکان واپیچش قالب در استفاده از آنها وجود دارد. به دلیل تلاشی پذیری کمتر قالب، قطعات که با استفاده از این روش ریخته گری میشوند، بیشتر در معرض پارگی انقباض میباشند. در این روش، به دلیل وجود زمان لازم برای خشک کردن قالب، آهنگ تولید پایین تر است.
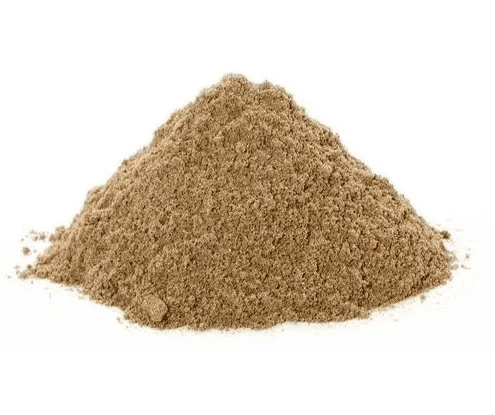
قالبهای سطح خشک (Skin-Dried Molds)
در ریخته گری با استفاده از این قالبها، سطوح قالب به دو روش خشک میشود؛ یا در معرض هوا قرار گرفته یا درون شعله ای که معمولا تا 13 میلی متر عمق دارد، قرار میگیرند. این قالبها غالبا برا تولید قطعات فولادی بزرگ استفاده میشوند؛ زیرا دمای ذوب ریزی فولادها بیشتر از چدن است. در برخی مواقع در استفاده از این قالبها برای بهبود خاصیت دیرگدازی، قبل از خشک کردن، سطوح توسط محلولی غنی از سیلیس یا ماسه پایدار گرمایی زیرکنی پوشش داده میشوند. همچنین برای بهبود بیشتر سطح و افزایش استحکام آن پس از خشک شدن نیز میتوان از بایندرها شامل ملاس، روغن بزرک یا آرد ذرت استفاده کرد.
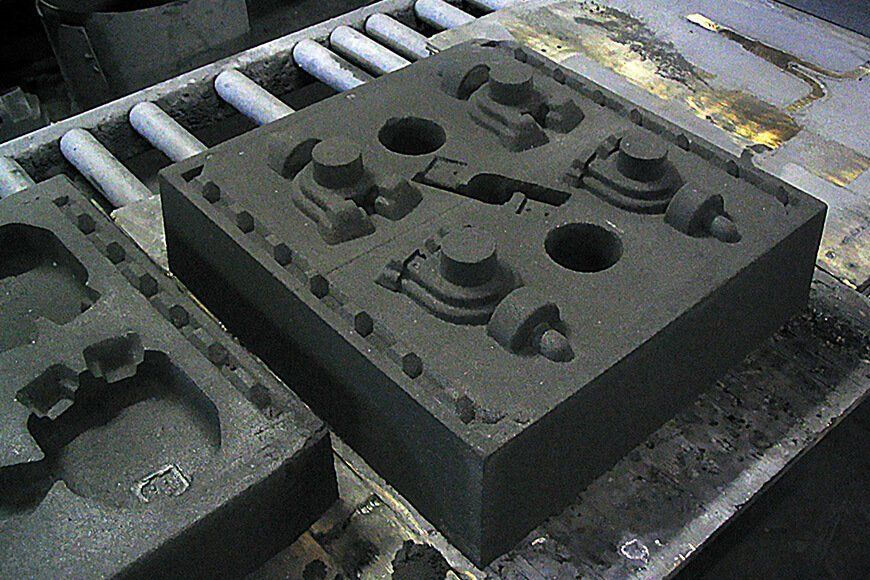
قالبهای سدیم سیلیکاتی (CO2)
برای چسبندگی مورد نیاز ساخت قالبها و یا ماهیچهها میتوان از 3 تا 6 درصد سدیم سیلیکات استفاده کرد. این متریال نوعی چسب غیرآلی مایع و شفاف است که پس از مخلوط شدن با ماسه داخل میکسرهای مول معمولی قرار گرفته و سپس قالب گیری میشوند. پس از آن نیز در معرض گاز CO2 قرار میگیرند. در این صورت، در طی چند ثانیه واکنشی شیمیایی شکل گرفته و قالب کاملا سفت میشود. گاز CO2 یک گاز غیر سمی، غیر اشتعال پذیر و بی بو است که برای شروع فرایند استفاده از آن نیازی به حرارت وجود ندارد.
برخلاف سایر روشهای ریخته گری، در ریخته گری با استفاده از قالبهای سدیم سیلیکاتی، پس از اینکه مذاب ریخته شده و قالب داغ میشود، ماسه سخت تر شده و در نتیجه آن، جدا کردن قطعه و خرد کردن قالب دشوار میشود. برای بهبود این مسئله نیز غالبا به قالب یک سری افزودنی اضافه میکنند.
قالبهای جعبه سرد، هوا-خشک و چسب شیمیایی
در فرایند ریخته گری با قالب جعبه سرد، برای پیوند شیمیایی دانههای ماسه و تامین استحکام بیشتر قالب، چسبهای گوناگون آلی و غیرآلی با ماسه ترکیب میشوند. این قالبها از قالبهای ماسه تر دقت ابعادی بالاتری دارند، ولی از این قالبها گران تر میباشند. در فرایند این روش، پس از ترکیب رزین مصنوعی مایع با ماسه، این ترکیب در دمای اتاق سخت میشود. زیرا پیووند قالب در این فرایند و فرایند جعبه سرد بدون گرم کردن انجام میشود.
کاربرد ریخته گری ماسه ای
ریخته گری ماسه ای یکی از بهترین و متداول ترین روشهای ریخته گری است که کاربردهای متنوعی در صنایع مختلف دارد. از این روش غالبا در صنایع هواپیما و هوافضا، نفت و گاز، راهسازی، تجهیزات غذایی، تجهیزات ساختمانی و تولید براق برای تولید و ساخت قطعات فلزی و غیرفلزی مختلف بسیار استفاده میشود. از جمله قطعاتی که با استفاده از این روش ساخته میشوند نیز میتوان به پایه ماشین، پروانههای توربین، بدنه موتورهای الکتریکی، قطعات اکسل، چرخ دندهها، سرسیلندر و… اشاره کرد.
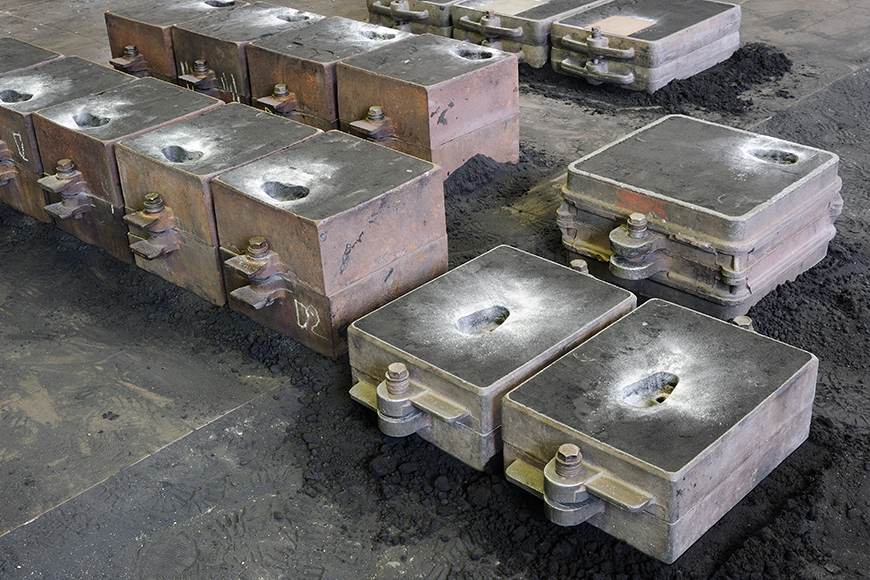
مراحل ریخته گری ماسه ای
همانطور که گفته شد، برای تولید و ساخت قطعات فلزی مختلف میتوان از روش ریخته گری ماسه ای استفاده کرد؛ اما درجه دشواری فلزات مورد استفاده یکسان نیست. به طور کلی، برای ریخته گری ماسه ای، غالبا مراحل زیر دنبال میشوند:
- در این مرحله، الگوی ریخته گری که همان شکل قطعه نهایی را دارد، برای ساخت قالب طراحی و تولید میشود. این الگوها غالبا از موادی مانند چوب یا پلاستیک ساخته میشوند. این الگوها به حدی بزرگ هستند که هنگام خنک شدن، فلز ریخته شده کوچک شود. در برخی موارد، اگر مدل یا همان الگو پیچیده باشد، میتوان آن را با استفاده از پرینت سه بعدی تولید کرد. نو الگو و مواد آن علاوه بر اینکه به ابعاد قطعه بستگی دارد، به تعداد ریخته گری مورد نیاز از هر اندازه قالب نیز وابسته است.
- پس از تعین الگو، از آن برای ساخت قالب استفاده میشود. در فرایند ساخت قالب مهمترین نکته انتخاب نوع ماسه است. همانطور که خواندید، ماسههایی که در ریخته گری مورد استفاده قرار میگیرند، بسته به ویژگیهایشان انواع مختلفی دارند. ماسههایی که برای ساخت قالب استفاده میشوند باید به یکدیگر بچسبند که برای خاصیت چسبندگی انها غالبا از مواد اضافی مانند چسبهای مصنوعی در ترکیب با ماسهها استفاده میشود.
- در این مرحله، ساخت قالب تکیمل میشود. برای این منظور نیاز به استفاده از ابزارهای ریخته گری ماسه ای و انجام فرایندهای تکمیلی وجود دارد. به عنوان مثال، برخی از قطعات دارای حفره یا سوراخ میباشند که برای ریخته آنها غالبا از یک ابزار جانبی به نام ماهیچه یا Core استفاده میشود. این ابزار جانبی در قالب نصب شده و مذاب ورودی دور آن را چر میکند. در این صورت در محل قرار گرفتن آنها فضای خالی موردنظر ایجاد میشود.
- پس از ساخت قالب، نوبت به ورود مواد مذاب است. برای این منظور فلز حرارت داده شده و ذوب میشود. پس از آن نیز این مذاب به داخل حفرههای موجود در قالب ماسه ای ریخته میشود. انتقال مذاب از کوره و بارریزی آن با استفاده از ظرفهای مخصوصی به اسم بوته انجام میشود و بسته به ابعاد قطعه در اندازههای مختلف موجود هستند.
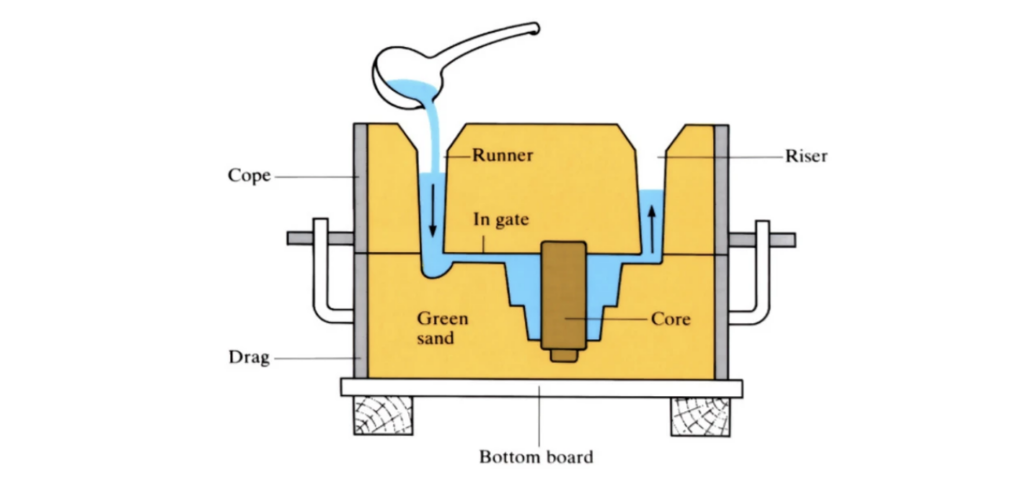
- پس از ریختن مواد مذاب به داخل قالب، نوبت به انجماد قالب است. در این مرحله، سرعت انجام کار بسیار اهمیت دارد؛ به همین دلیل در برخی مواقع برای تنظیم این سرعت از هیتر و یا خنک کنندههایی در اطراف قالب استفاده میشود. با این کار علاوه بر اینکه سرعت انجماد کنترل میشود، ساختار قطعه نهایی و خواص آن نیز بهبود پیدا میکند.
- در نهایت، پس از انجماد قالب با استفاده از ابزار ریخته گری ماسه ای مخصوص، قالب شکسته میشود. غالبا در این مرحله از ویبراتور برای به ارتعاش درآوردن قالب و خروج قطعه استفاده میشود.
در فرایند ریخته گری ماسه ای توجه به نکات زیر برای بالا بردن کیفیت قطعه نهایی اهمیت دارد:
- در طراحی و ساخت مدل در ریخته گری ماسه ای باید به مواردی مانند تغییرات ابعادی مذاب در حین انجماد، گازهای آزاد شده در اثر سوختن مدل و واکنش آن با ماسه و طراحی صحیح و اصولی اجزاء قالب توجه شود.
- رفتار انجمادی فلز مورد نظر باید به درستی بررسی شده و اجزاء قالب سیستم ماسه متناسب با آن طراحی شود.
- در تهیه سیستم ماسه باید به استانداردهای مربوطه توجه شده و کیفیت این سیستم نیز باید به دقت کنترل شود.
- در تهیه قالب ماسه مورد استفاده باید در تمامینقاط به طور همگن توزیع شده و میزان فشرده سازی ماسه نیز کنترل شود.
- رطوبت ماسهها در قالب نیز دارای اهمیت است و باید دیوارههای قالب دارای استحکام کافی باشند.
- قبل از ذوب ریزی بهتر از قالب با قرار گرفتن در کوره و یا با مشعل، پیشگرم شود.
- در تعبیه هواکش تعداد و قطر هواکشها اهمیت دارد تا خروج گازها و بخارات به آسانی انجام شود.
- روش ذوب فلز و مذاب ریزی باید متناسب با جنس فلز انتخاب شود.
- میزان، شکل و توزیع مک و تخلخل در قطعات ریخته گری باید بررسی شد و با استانداردهای مربوطه مقایسه شود.
مزایا و معایب ریخته گری ماسه ای
فرایند ریخته گری ماسه ای به دلیل ویژگی ها و مزایایی که دارد، دارای کاربردهای مختلفی است. از جمله مهمترین مزایای این روش میتوان به موارد زیر اشاره کرد:
- در این روش ساخت قطعات هزینه کمتری به همراه دارد.
- برای استفاده از این روش، در اندازههای قالب محدودیتی وجود نداشته و میتوان انواع قطعات را با اندازههای مختلف تولید کرد.
- امکان تولید قطعات با شکلهای پیچیده نیز در این روش وجود دارد.
- تولید قطعات با استفاده از این روش، به خصوص در خطوط نیمه اتوماتیک سرعت بالایی دارد.
- در این روش میتوان برای ساخت قطعات از مواد غیرفلزی نیز استفاده کرد.
- مواد اولیه و تجهیزاتی که در این روش مورد استفاده قرار میگیردند، در دسترس و ساده هستند. همچنین شن و ماسه ریخته گری شده در این روش غالبا قابل استفاده مجدد میباشد.
- برای دورههای تولید کوتاه، این روش بسیار ایده آل است.
- تولید قطعات با استفاده از این روش در مقیاسهای کلان نسبت به سایر روشهای نوین بسیار مقرون به صرفه است.
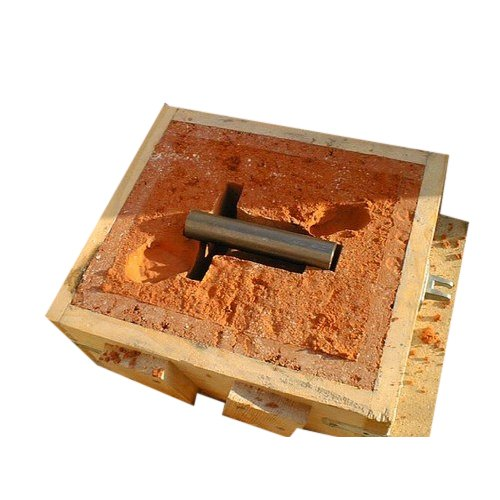
اما در کنار تمامیاین مزایا، ریخته گری ماسه ای یک سری معایب را نیز شامل میشود؛ که عبارتند از:
- قطعات ساخته شده با این روش دقت ابعادی بالایی ندارند.
- معمولا پس از تولید قطعه در این روش نیاز به ماشینکاری قطعه وجود خواهد داشت.
- ماده و انرژی زیادی در این روش هدر میرود.
- در این روش امکان آزاد شدن گازهای سمیوجود دارد و به محیط زیست آسیب میرسد.
- ریخته گری برخی فلزات با استفاده از این روش، توجیه اقتصادی ندارد.
- این روش موجب تخلخل بسیار در قطعه شده و مقاومت نهایی قطعه نیز کم میشود.
سوالات متداول
ریخته گری ماسه ای چه تفاوتی با ریخته گری دقیق دارد؟
ریخته گری ماسه ای در برخی عوامل مانند هزینه، وزن، صافی سطح و سهولت طراحی با ریخته گری دقیق تفاوت دارد. ریخته گری دقیق از ریخته گری ماسه ای پرهزینه تر است اما با استفاده از ریخته گری دقیق امکان تولید قطعات با ابعاد کوچک و در وزن کم وجود دارد؛ در صورتی که در ریخته گری ماسه ای غالبا نمیتوان قطعات کوچک و پیچیده تولید کرد.
ریخته گری دقیق قطعاتی با صافی سطح بیشتر و تلرانس پایین تر ایجاد میکند. همچنین در ریخته گری دقیق امکان تولید قطعات با هر شکلی وجود دارد.
انواع چسبهای مورد استفاده در ریخته گری ماسه ای کدامند؟
انواع چسبها و بایندرهایی که برای ریخته گری ماسه ای استفاده میشوند غالبا شامل، آب و خاک رس، روغنها، رزینها و سدیم سیلیکات هستند. در این روش میتوان از روغنهایی مانند بذر کتان و روغنهای گیاهی برای قالبها استفاده کرد. همچنین امکان استفاده از انواع طبیعی و مصنوعی رزینها برای بالا بردن کیفیت سطح و تخریب آسان قالب وجود دارد. سدیم سیلیکات نیز غالبا برای استحکام بیشتر قالبهای ماسه ای مورد استفاده قرار میگیرد اما جداکردن قطعه از قالبهایی که در آنها از سدیم سیلیکات استفاده شده است، کمیدشوار است.
جمع بندی
ریخته گری ماسه ای، روش متداول برای ریخته گری فلزات است که در آن از ماسه برای ساخت قالبها استفاده میشود. ماسههایی که در این روش مورد استفاده قرار میگیرند، بسته به ویژگیها و کاربردهایشان انواع مختلفی دارند. همچنین ممکن است بسته به نیاز و یا برای بالا بردن استحکام قالب از یک سری مواد افزودنی نیز در ساخت قالب استفاده شود. ریخته گری ماسه ای در صنایع مختلف بسیار کاربرد دارد و با مزایایی که دارد در تولید انواع قطعات به طور متعدد مورد استفاده قرار میگیرد.
با فبرینو بهترین ایده ها، از طراحی تا اجرا را تجربه کنید. ساخت انواع ابزارآلات و قطعات صنعتی با بهترین کیفیت و زیر نظر بهترین متخصصین و مهندسین مجموعه فبرینو. با ما بهترین ها را تجربه کنید.