برای برش فلزات در صنایع مختلف از فرایندهای متفاوتی استفاده میشود که هرکدام ویژگیهای خاص خود را داشته و بسته به عوامل مختلف در کاربردهای متنوع مورد استفاده قرار میگیرند. یکی از این فرایندها، فرایند برش کاری پلاسما است که یک روش بسیار دقیق برای برش انواع فلزات و مواد غیرفلزی محسوب میشود؛ به طوری که با استفاده از این روش میتوان انواع فلزات مختلف و متنوع را مانند فلزات نرم، فلزات نازک، فلزات ضخیم، فلزات رسانا و… را برش داد.
اگر میخواهید با روش برش کاری پلاسما، ویژگیها، مزایا و معایب این روش بیشتر آشنا شوید، مطالعه این مقاله را از دست ندهید.
برش پلاسما چیست؟
پلاسما یکی از حالتهای ماده است که دارای ذرات باردار مثبت یا همان یونها و ذرات باردار منفی یعنی الکترونها میباشد. این ماده بسیار داغ است؛ به صورتی که الکترونها از اتمها جدا شده و منجر به ایجاد یک گاز یونیزه میشوند.
برش پلاسما (Plasma Cutting)، فرایندی است که در آن از پلاسمای داغ برای برش مواد رسانا استفاده میشود. در این فرایند، یک گاز موثر (گازهای یونیزه شده که تا دمای 20000 درجه سانتیگراد حرارت داده شدهاند) مورد استفاده قرار میگیرد و این گاز با سرعت بالایی از درون نازل به بیرون دمیده میشود. در اینصورت، بین گاز و سطح برش یک قوس الکتریکی به وجود آمده و گاز در حالت پلاسما ایجاد میشود. در نتیجه آن، فلز یا قطعه مورد استفاده ذوب شده و برش داده میشود.
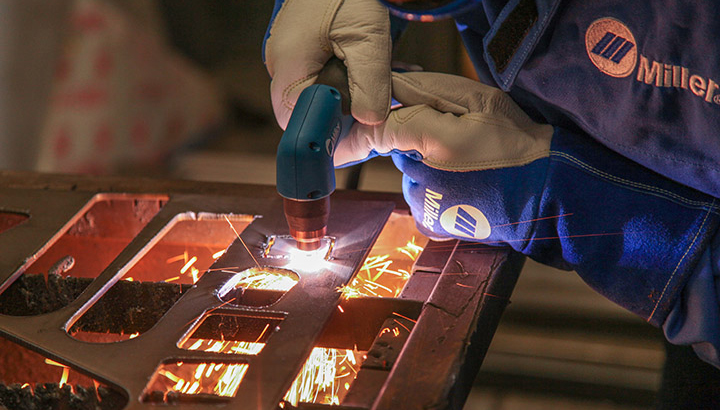
خروج گاز تحت فشار بالا علاوه بر اینکه باعث ذوب ماده فلزی میشود، مواد باقیمانده را نیز از مسیر برش دور میکند. موادی که در این فرایند مورد استفاده قرار میگیرند، غالبا مواد رسانای الکتریکی مانند مس، فولاد، آلومینیوم، برنج، فولاد ضد زنگ و… هستند. در نتیجه از این فرایند نمیتوان برای برش موادی مانند سنگ، شیشه و یا سایر موادی که خاصیت الکتریسیته ضعیفی دارند، استفاده کرد.
برش پلاسما، به دلیل دقت بالا و قابلیت تکرار پذیری و همچنین به دلیل طیف گسترده کاربرد آن روی فلزات و مقرون به صرفه بودن، در صنایع مختلفی مورد استفاده قرار میگیرد.
تاریخچه برش پلاسما
تاریخچه برش کاری پلاسما به سال 1957 بر میگردد. در ابتدای ابداع برش پلاسما، این فرایند با نام جوشکاری قوس تنگستن (Gas Tungsten Arc Welding) شناخته میشد. در آن دوران، از برش پلاسما غالبا برای برش مواد فولادی و آلومینیومی با ضخامتهای نیم تا شیش اینچ استفاده میشد و کاربرد اصلی این فرایند برای برش این فلزات بود. در آن زمان همچنین به دلیل گرمای ناشی از فرایند، الکترودها و نازلهای مورد استفاده به سرعت دچار شکستگی میشدند که تعویض آنها هزینههای زیادی را در پی داشت.
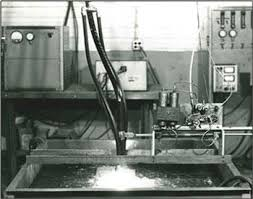
در اواخر دهه 60، ساخت مشعل با جریان دوگانه انجام شد که در بهبود طول عمر الکترود و نازلها و همچنین در افزایش کیفیت و دقت برش موثر بود.
در دهه 1970، کنترل میزان دود فرایند مورد بررسی قرار گرفت که در ابتدا یک صدا خفه کن و میز آب برای این فرایند طراحی شد. همچنین نازلهای بهتری طراحی شدند که استفاده از آنها بهبود دقت قوس و تنظیم دقیق ماشینها را فراهم میکرد.
در دهه 1980، تجربه علمی مهندسان افزایش یافت و برشدهندههای پلاسمایی با پایه اکسیژن طراحی و ابداع شدند. در این برشدهندهها کنترل برش در سطوح مختلف ارتقاء یافته و قابلیت حمل واحد برش پلاسما ارگونومیکتر شد.
در دهه 1990، برشدهندههای پایدار با پایه اکسیژن همراه با سیستم نازل جدید مورد استفاده قرار گرفتند. این سیستم جدید منجر به ارتقاء چهار برابری شدت انرژی نسبت به دورههای گذشته شد.
از دهه 1990 تا به امروز، مهندسان روی گزینههای قدرت، کنترلها و بهبود کارایی فرایند تمرکز کردند. همچنین دقت برشهای پلاسما را تا حد زیادی بهبود بخشیدند؛ به صورتی که امروزه با برش پلاسما میتوان لبههای تیزتر و برشهای دقیقتری ایجاد کرد. از دیگر جنبههای این فرایند که به طور قابل توجهی بهبود یافته است، قابلیت حمل و اتوماسیون میباشد که امروزه این روش با قابلیت حمل بالا و به صورت کاملا اتوماتیک انجام میشود.
انواع دستگاه برش پلاسما برای انواع برش پلاسما
دستگاههای برش پلاسما، دستگاههای برش کاملا اتوماتیک هستند که با هد کنترل کار میکنند. این هد روی میز نصب شده و پس از آن دستگاه مورد استفاده قرار میگیرد. دستگاههای برش پلاسما، انواع متفاوتی دارند که براساس اندازه و ضخامت صفحه و همچنین برای اساس تعداد ورقهای مورد استفاده در برشکاری و میزان فضای کار مورد استفاده قرار میگیرند.
رایجترین انواع دستگاه برش کاری پلاسما عبارتند از:
- دستگاه برش کاری پلاسما دستی
این دستگاهها بسیار متداول هستند و بیشتر برای برش کاریهای سبک مانند تراش یا برش قطعات کوچکتر فلزات مورد استفاده قرار میگیرند. دستگاههای برش کاری پلاسما دستی، قدرت آمپراژ بالایی دارند و یکی از مهمترین کاربردهای آنها در گاراژها، تعمیرگاههای خودکار یا خانهها میباشد.
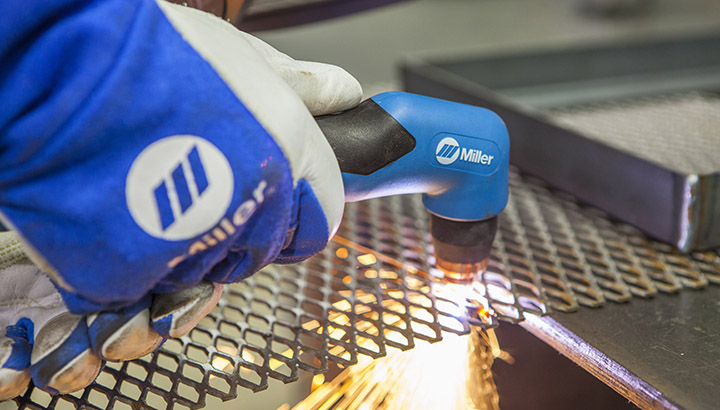
- دستگاه برش کاری پلاسما معمولی
در برخی کاربردها که اکثر کارها به صورت دستی انجام میشود، دستگاه برش کاری پلاسمای معمولی بیشتر کاربرد دارد. در این دستگاهها به جای گاز پلاسما، از هوا برای تعیین نوک نازک شکل قوس استفاده میشود. همچنین در این دستگاهها مقدار آمپر مورد استفاده در حدود 12 تا 20 کیلو آمپر در اینچ مربع است.
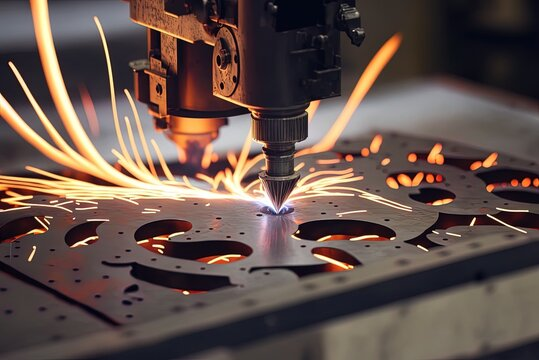
- دستگاه برش کاری پلاسما با کنترل عددی کامپیوتر (CNC)
این دستگاه از طریق نرم افزار کار میکند و کار با آن نیاز به مهارت دارد. در واقع، برای کار با این دستگاه نیاز به فردی وجود دارد که مهارت کار با دستگاه را داشته باشد و بتواند فایلهای CAD را در دستگاه CNC وارد کرده و این فایلها را در دستگاه، ایجاد و ویرایش کند.
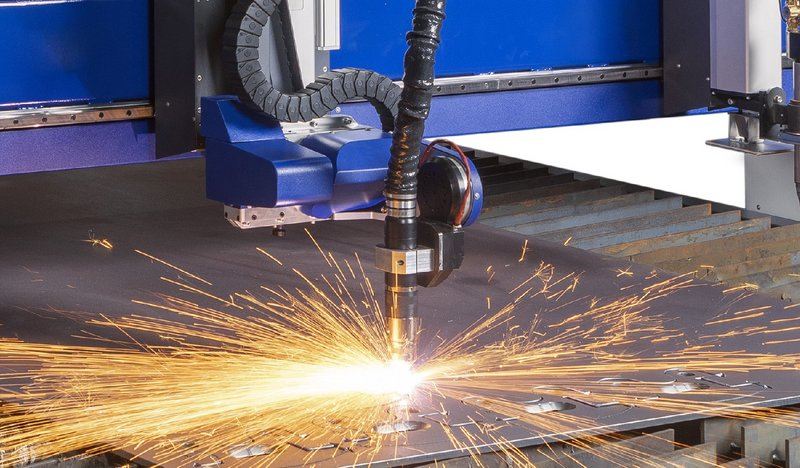
انواع فرایند برش پلاسما
سیستمهای مختلف برش پلاسما، نحوه عملکرد متفاوتی دارند و برای بهبود کیفیت برش، پایداری قوس، کاهش نویز و افزایش سرعت برش، با مکانیزمهای مختلفی طراحی شدهاند. در اینصورت انواع فرآیندهای برش پلاسما را میتوان در موارد زیر دستهبندی کرد:
- فرایند برش پلاسما با گاز دوگانه (Dual Gas)
در این فرایند، برش پلاسما، به همان روش سیستم مرسوم عمل میکند با این تفاوت که در این روش در اطراف نازل یک حفاظ گاز ثانویه قرار میگیرد. حضور این گاز ثانویه باعث افزایش انقباض قوس و دور شدن مواد ذوب شده از روی سطح برش میشود. در این روش از گازهای آرگون، آرگون-هیدروژن و یا نیتروژن برای تشکیل پلاسما استفاده شده و گاز ثانویه نیز با توجه به فلز مورد استفاده، انتخاب میشود.
از دیگر مزایای برش کاری پلاسما با گاز دوگانه میتوان به سرعت برش بالا، کاهش گرد شدن لبه بالایی سطح برش و کاهش خطر آتشسوزی ناشی از تشکیل قوس دوگانه اشاره کرد.
- فرایند برش پلاسما با تزریق آب (Water Injection)
در این فرایند آب به صورت شعاعی (تزریق گردابی) به قوس پلاسما برای افزایش انقباض تزریق میشود. دما نیز به طور قابل توجهی تا 30000 درجه سانتیگراد افزایش مییابد. در فرایند تزریق آب، گاز نیتروژن به عنوان گاز پلاسما مورد استفاده قرار میگیرد.
از جمله مزایای برش کاری پلاسما با تزریق آب میتوان به افزایش سرعت برش، کاهش خطر دوگانه شدن قوس، کاهش خوردگی نازل، بهبود کیفیت برش و عدم ایجاد ضایعات در سطح زیر برش اشاره کرد.
- فرایند برش کاری پلاسمای زیر آب (Water Shroud)
در برش کاری پلاسما، امکان برش کاری در محیطی با پوشش آب نیز وجود دارد که برای این کار قطعه مورد استفاده میتواند تا 75 میلیمتر زیر آب غوطهور شود. این فرایند با نام برش کاری پلاسمای زیر آب شناخته میشود. در این فرآیند سر و صدای ناشی از برش کاری تا حد قابل توجهی کاهش مییابد. همچنین این روش افزایش عمر نازل و کاهش دود را به همراه دارد. اما به دلیل عدم افزایش انقباض قوس در این روش، سرعت برش و لبه آن به طور موثری بهبود نمییابند.
- فرایند برش کاری پلاسمای هوا (Air Plasma)
در این روش، گاز تشکیلدهنده پلاسما با هوا جایگزین شده و از یک الکترود خاص با هافنیم و یا زیرکونیم نصب شده در یک نگهدارنده مسی استفاده میشود. همچنین در این روش میتوان از هوا به عنوان جایگزین آب نیز برای خنک کردن مشعل استفاده کرد.
مزایای برش پلاسمای هوا، شامل، استفاده از هوا به جای گازهای گران قیمت است که مزیت مهمی محسوب میشود. همچنین ذکر این نکته نیز ضروری است که الکترود و نازل در فرایند برش کاری پلاسمای هوا، بعد از اتمام طول عمر مفیدشان تعویض میشوند اما الکترودهای هافنیم در مقایسه با الکترودهای تنگستن قیمت بیشتری دارند.
- فرایند برش کاری پلاسما با توان بالا (High Tolerance Plasma)
سیستمهای برش قوس پلاسمایی با توان بالا، برای بهبود کیفیت برش در رقابت با سیستمهای برش لیزری هستند. در این روش، پلاسمای تولید شده، هنگام تزریق به روزنه ی نازل، دچار چرخش شده و برای حفظ این چرخش نیز، جریان گاز ثانویه در قسمت پایینی نازل تزریق میشود. همچنین، در برخی از این سیستمها، در اطراف قوس، میدان مغناطیسی جداگانهای قرار میگیرد.
از مزایای این روش میتوان به شیار برش کوچکتر، اعوجاج کم به دلیل ناحیه کوچک تحت تاثیر حرارت و همچنین کیفیت برش بهتر نسبت به برش پلاسمای مرسوم اشاره کرد. در واقع، کیفیت برش در این فرایند نزدیک به کیفیت برش در روش برش کاری لیزری است.
این روش، یک روش مکانیزه است که نیاز به تجهیزات دقیق و سرعت بالا دارد. اما از این روش تنها میتوان برای برش قطعات با حداکثر ضخامت 6 میلیمتر استفاده کرد و سرعت برش در آن نیز کمتر از فرایند برش پلاسمای مرسوم و روش برش کاری لیزری است.
مراحل انواع برش کاری پلاسما
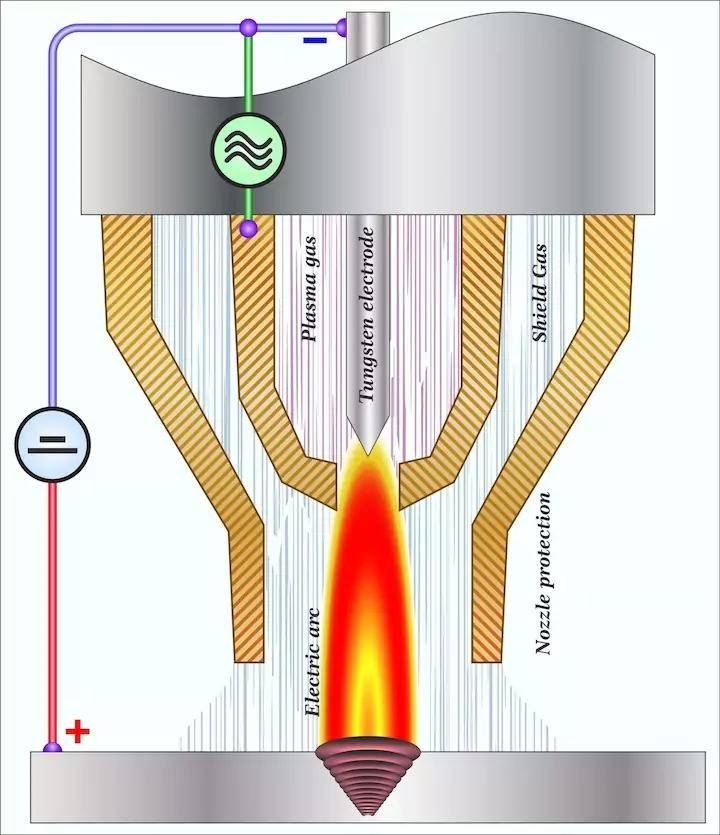
به طور کلی، در فرایند برش کاری پلاسما، مراحل زیر دنبال میشوند:
- در ابتدا در مشعل برش پلاسما، الکترود و نازل مورد استفاده به وسیله سوویرل رینگ یا حلقه چرخشی از یکدیگر جدا میشوند.
- حلقه چرخشی درون خود یکسری سوراخهای ریز دارد که جریان اولیه پلاسما به واسطه این سوراخها به صورت یک گرداب ایجاد میشود.
- پس از آن، منبع تغذیه شروع به کار کرده و جریان DC را تا 40 ولت ایجاد میکند. سپس گاز پلاسما تولید میشود.
- در ابتدا نازل به پتانسیل مثبت منبع تغذیه به صورت موقت متصل میشود و یک مدار قوس تشکیل میدهد. در این مرحله، الکترود نیز دارای پتانسیل منفی میشود.
- پس از آن، یک جرقه با فرکانس بالا تشکیل میشود که به یونیزه شدن گاز پلاسما کمک کرده و قدرت هدایت الکتریسیته به دست میآید. به این قدرت، قوس پایلوت یا هدایتگر گفته میشود. همچنین در این میان، دمای پلاسما بیشتر از 20000 درجه سانتیگراد است و سرعت آن نیز نزدیک به سرعت صوت میباشد.
- زمانی که این قوس با قطعه کار تماس پیدا میکند، مسیر جریان از نازل به قطعه کار منتقل میشود. در این فرایند، میز کار باید به زمین متصل باشد تا از حرکت جریان به مسیر دیگر جلوگیری شود. این جریان DC برای تولید آمپراژی که کاربر در تنظیمات دستگاه برش پلاسما انتخاب کرده، مورد استفاده قرار میگیرد.
- جریان و آمپر به مقداری که برای برش فلز قطعه کار لازم است، به جریان میافتد. سپس گاز ثانویه که نقش گاز محافظ را دارد، از طریق مسیر نازل وارد محیط میشود. این گاز محافظ منجر به حرکت صحیح پلاسما شده و در سطح برش زوایای اریب را کاهش داده و دقت برش را افزایش میدهد.
- هنگام برش، جریان پلاسما افزایش پیدا کرده و به واسطه آن جت پلاسما با عمق نفوذ بالا از ماده عبور میکند. در اینصورت، سرعت بالای این جریان منجر به دور شدن مواد مذاب خروجی پلاسما میشود.
این فرایند، فرایندی با سرعت بالا است که اگر با مهارت کامل انجام شود، میتواند دقت و کیفیت بالایی را ارائه دهد.
گازهای مورد استفاده در انواع برش پلاسما
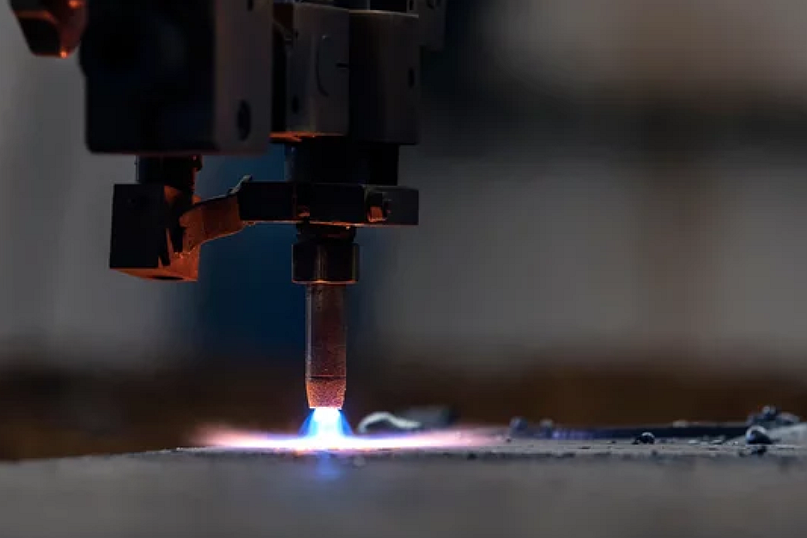
همانطور که در بالاتر نیز اشاره شد، در برش کاری پلاسما از انواع گازهای مختلفی برای فرایند برش کاری استفاده میشود. نوع گاز مورد استفاده در این فرایند به عواملی مانند ماده مورد استفاده، ضخامت برش و نوع روش برش کاری بستگی دارد. این گاز، پلاسمای مورد نیاز برای برش کاری را تولید کرده و در دور کردن مواد مذاب و اکسید از سطح برش موثر است.
رایجترین گازهایی که در برش پلاسما مورد استفاده قرار میگیرند، عبارتند از:
- گاز آرگون (Ar)
آرگون یک گاز خنثی و بیاثر است که دارای قوس پلاسمایی پایدار میباشد؛ به این معنا که این گاز به سختی با هر فلزی در دماهای بالا واکنش نشان میدهد. الکترودها و نازلهایی که برای برش آرگون استفاده میشوند، غالبا عمر مفید طولانیتری نسبت به سایر گازها دارند.
این گاز به دلیل قوس پلاسمایی کم و داشتن مقداری آنتالپی، هنگام برش یکسری محدودیتها را شامل میشود. از طرفی، به دلیل کشش سطحی فلز مذاب که حدود 30 درصد بیشتر از کشش سطحی موجود در محیط نیتروژن است، برش با این گاز در یک محیط محافظتی آرگون، غالبا مشکلات سربارهای را شامل میشود. به همین دلیل این گاز در برش پلاسما کمتر مورد استفاده قرار میگیرد.
- گاز نیتروژن (N2)
نیتروژن، نسبت به آرگون پایداری قوس پلاسما و جت انرژی بالاتری دارد؛ بخصوص در مواردی که منبع ولتاژ بالاتری وجود داشته باشد. استفاده از این گاز در برش پلاسما، حداقل سرباره را در لبههای پایینی برش ایجاد میکند؛ حتی این مورد برای برش فلزاتی مانند آلیاژ پایه نیکل و فولاد ضد زنگ که ویسکوزیته بالایی دارند هم صدق میکند.
گاز نیتروژن در فرایند برش پلاسما میتواند به عنوان یک گاز مستقل عمل کرده و یا در ترکیب با گازهای دیگر مورد استفاده قرار بگیرد. این گاز همچنین باعث بهبود و تسهیل برش فولاد کربنی با سرعت بالا میشود.
- هوا
هوا دارای 78 درصد نیتروژن و 21 درصد اکسیژن حجمی است که میتواند در برش کاری پلاسما مورد استفاده قرار بگیرد. به دلیل اکسیژن موجود در هوا، این گاز به عنوان یکی از سریعترین گازهای مورد استفاده در برش فولاد کم کربن شناخته میشود. همچنین از آنجایی که هوا در همه جا وجود دارد، استفاده از آن در برش کاری، میتواند بسیار مقرون به صرفه باشد.
اما الکترودها و نازلهایی که در فرایند برش پلاسما با هوا مورد استفاده قرار میگیرند، غالبا عمر مفید کوتاهی دارند که منجر به افزایش هزینه و کاهش کارایی و راندمان فرایند میشود. همچنین استفاده از هوا به عنوان گاز مستقل نیز غالبا مشکلاتی را ایجاد کرده و در طی فرایند غالبا مشکلاتی مانند آویزان شدن سرباره و اکسیداسیون برش ایجاد میشوند.
- اکسیژن (O2)
همانند برش پلاسما با هوا، برش کاری پلاسما با اکسیژن نیز منجر به افزایش سرعت فولاد کم کربن میشود. در واقع، استفاده از برش قوس پلاسما با انرژی بالا و دمای بالا برای اکسیژن روی افزایش سرعت فرایند تاثیرگذار خواهد بود. در اینصورت غالبا توصیه میشود که در فرایند برش کاری پلاسما با اکسیژن از الکترودهای مقاوم به اکسیداسیون و دمای بالا تحت گاز اکسیژن استفاده شود.
- هیدروژن (H2)
هیدروژن در برش کاری پلاسما غالبا در ترکیب با سایر گازهای پلاسمایی و به عنوان یک گاز کمکی مورد استفاده قرار میگیرد. یکی از رایجترین این ترکیبها، ترکیب گاز هیدروژن با آرگون است که منجر به تولید گازی قدرتمند در برش کاری پلاسما میشود. این ترکیب، ولتاژ قوس، آنتالپی و قدرت برش جریان پلاسمای آرگون را به طور قابل توجهی افزایش میدهد. راندمان برش این ترکیب نیز هنگام فشرده شدن توسط جت آب افزایش پیدا میکند.
هوای فشرده، نیتروژن، آرگون، هیدروژن و اکسیژن یا ترکیبی از دو یا سه مورد از این اجزا، محبوب ترین گازهای پلاسما برای برش پلاسما هستند.
چه گازی برای برش کاری پلاسما مناسب تر است؟
فلزات قابل برش با پلاسما
در برش کاری پلاسما مواد زیادی برای برش مورد استفاده قرار میگیرند و در واقع امکان برش هر ماده رسانایی با استفاده از این فرایند وجود دارد.
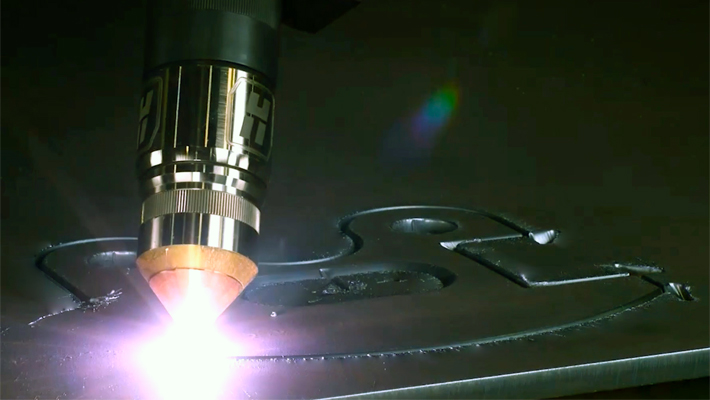
رایجترین فلزاتی که با فرایند برش پلاسما قابل برش هستند؛ عبارتند از:
- آلومینیوم
آلومینیوم یک فلز رسانا است که فرایند برش پلاسما یک فرایند کاربردی برای برش آن محسوب میشود. همچنین این فرایند با فلزات ضخیمتر، در مقایسه با سایر روشهای برش و ساخت آلومینیوم مانند برش کاری لیزر، مزایای بیشتری دارد و میتوان از آن برای برش آلومینیوم حتی با ضخامت 160 میلیمتر استفاده کرد.
- فولاد کم کربن
فولاد کم کربن که با نام فولاد ملایم نیز شناخته میشود، محتوای کربن کم شود، غالبا کمتر از 2.1 درصد دارد. از این فولاد میتوان در ساخت بسیاری از قطعات استفاده کرد و در واقع کاربرد زیادی در صنایع گوناگون دارد. همچنین، تهیه فولاد نرم هزینه بالایی نداشته و استفاده از آن مزایای زیادی اعم از استحکام ضربهای بالا، جوشپذیری و شکلپذیری بالا را شامل میشود.
- فولاد ضد زنگ
این نوع فولاد آلیاژی از آهن است که در برابر خوردگی و زنگزدگی بسیار مقاوم میباشد. برش کاری پلاسما یکی از رایجترین و موثرترین روشها برای برش و ساخت این نوع فولاد محسوب میشود و از این روش میتوان برای برش این نوع فولاد تا ضخامت 30 میلیمتر استفاده کرد.
- برنج
برنج خاصیت رسانایی دارد و به همین دلیل میتواند با استفاده برش پلاسما ساخته شود. برای استفاده از فرایند برش کاری پلاسما توسط فلز برنج، بهتر است تهویه مناسبی در فضا وجود داشته باشد؛ زیرا برنج حاوی مقداری روی است و استنشاق دودهای حاوی سوختن روی میتواند برای سلامتی مضر باشد.
- مس
مس رسانایی گرما و الکتریکی مطلوبی دارد. این فلز در برابر خوردگی مقاوم بوده و شامل قابلیتهای شکلپذیری و جوشپذیری بالایی میباشد. به همین دلیل فلز مس نیز برای برش کاری پلاسما بسیار کاربرد دارد. اما برای برش این فلز تحت فرایند برش کاری پلاسما، همانند برنج، باید تهویه خوبی در محل وجود داشته باشد.
- چدن
فلز چدن نسبت به اکثر فلزها قیمت پایینتری داشته و دارای خاصیت چکشخواری مطلوبی میباشد. این فلز در مقادیر کم، حاوی عناصری مانند منگنز، گوگرد، فسفر و سیلیکون است. فلز چدن یک فلز بسیار رسانا بوده و در کنار آن از مقاومت فشاری بالا و دمای ذوب پایینی برخوردار میباشد؛ به همین دلیل در برش کاری پلاسما بسیار کاربرد دارد.
کاربرد برشکاری پلاسما
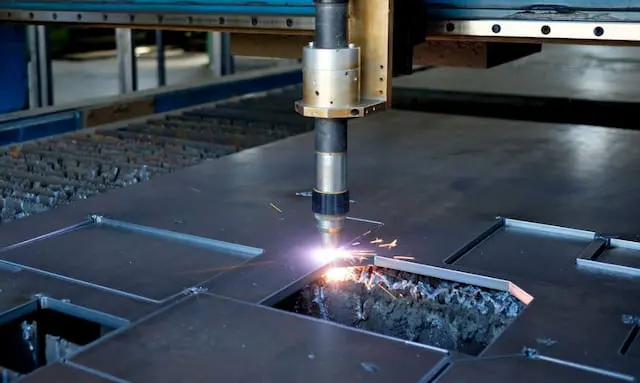
فناوری برش پلاسما، به دلیل ویژگیهایی که دارد، در صنایع مختلفی مورد استفاده قرار میگیرد. این فرایند در انواع پروژههای صنعتی اعم از صنایع دریایی، کشتیسازی، اتومبیلسازی، شرکتهای برودتی، ضایعات فلزات، ساخت و تعمیر وسایل نقلیه، عملیات نجات و سقوط تجهیزات و مصالح، تعمیر وسایل و تجهیزات کشاورزی، کارهای عمرانی و ساختمانسازی، عملیات برش فلزات درحوادثی مانند ریزش ساختمان، سیل و زلزله، تابلوهای نئونی، جوشکاری، نیروگاهها، کاربردهای مختلف CNC صنعتی و بسیاری دیگر از دستگاهها و پروژهها، کاربرد دارد.
به طور کلی، میتوان گفت این فرایند در اغلب صنایعی که نیاز به برش فولاد دارند، مورد استفاده قرار میگیرد و بسیار پرکاربرد است.
مزایا و معایب برش کاری پلاسما
همانند تمامی فرایندهای صنعتی، برش کاری پلاسما نیز ویژگیهای مختلفی دارد که باعث کاربرد آن در صنایع گوناگون شده است. از جمله مهمترین مزایای این فرایند، عبارتند از:
- امکان برش تمامیمواد رسانا با دستگاه برش پلاسما وجود دارد و این روش برای برش طیف وسیعی از مواد سازگاری دارد.
- برای فلزاتی که ضخامت بالایی ندارند، دقت این روش بسیار بالا میباشد.
- براش فلزات ضخیم تا 5 سانتیمتر نیز، غالبا برش کاری پلاسما به طور دقیق و با کیفیت بالا انجام میشود.
- هزینه استفاده از فرایند برش کاری پلاسما نسبتا پایینتر از سایر روشهای برش کاری است.
- سرعت این روش برای برش انواع مواد رسانای الکتریکی بسیار بالا است و در واقع این روش برش کاری در حدود یک چهارم زمان مورد نیاز برای برشزنی با بسیاری دیگر از تکنیکها را شامل میشود.
- در برش کاری پلاسما میتوان از دستگاههای CNC که دارای دقت بسیار زیاد و تکرار پذیری بالا در عملیات برش زنی هستند، استفاده کرد. در واقع، دستگاه برش پلاسما برای انجام برش به صورت اتوماتیک و برش قطعات با اشکال مختلف، قابلیت اتصال راحت به دستگاه CNC را دارد.
- با استفاده از این فرایند میتوان در آب و زیر آب نیز فلزات را برش داد که با این کار میزان تغییرات خواص مواد در اثر حرارت زیاد فرایند کاهش مییابد. همچنین با برش کاری زیر آب، سرو صدای بسیار کمتری ایجاد میشود.
- نگهداری از تجهیزات مورد استفاده در این فرایند بسیار ساده است و این تجهیزات به ندرت به تعمیر و تعویض نیاز خواهند داشت. در اینصورت هزینه نگهداری تجهیزات نیز کاهش مییابد.
- دستگاههای برش پلاسما در ابعاد مختلفی موجود هستند که میتوانند برای عملیات و کاربردهای مختلف مورد استفاده قرار بگیرند. حتی برخی از این دستگاهها، دستی، کوچک و قابل حمل میباشند.
- برش کاری پلاسما با استفاده از گازهای خنثی و بیاثر انجام میشود؛ به همین دلیل در مقایسه با برش با گاز اکسیژن که احتمال انفجار و یا آتش سوزی در آن وجود دارد، بسیار ایمنتر است.
- با استفاده از این فرایند امکان برش فولاد و آلومینیوم با آلیاژ بالا و ضخامت زیاد وجود دارد.
- این فرایند برای برشهای فولادی با استحکام بالا دارای یک عملکرد عالی بوده و ورودی گرمای کمتری را شامل میشود.
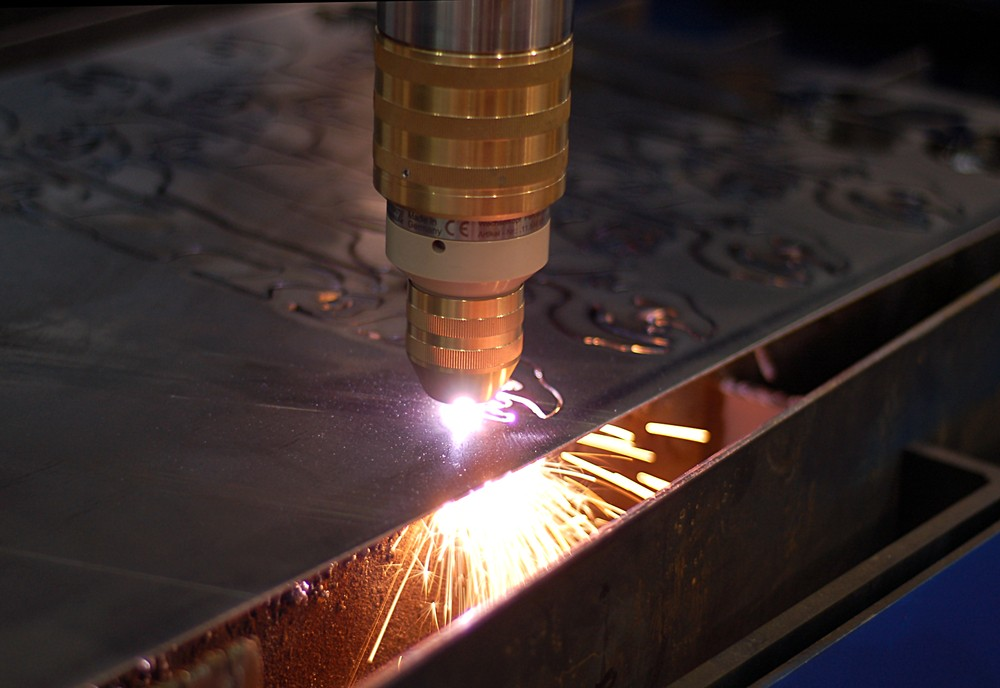
در کنار تمامی این مزایا، برش کاری پلاسما یکسری معایب را نیز شامل میشود؛ که عبارتند از:
- برش قطعات و مواد مختلف با استفاده از دستگاههای برش پلاسما نسبت به روش برش واترجت دقت پایینتری را شامل میشود.
- دقت برش کمتر این فرایند نیاز به پردازش قسمتهای برش خورده را افزایش میدهد.
- در مقایسه با برش لیزری، استفاده از این فرایند برای برش ورقها و صفحات نازکتر، کیفیت پایینتری را شامل میشود.
- برای انجام برش کاریهای مختلف نیاز به تغییر تنظیمات در دستگاه پلاسما وجود دارد.
- احتمال اکسیده شدن نازل دستگاه پلاسما در فرایند برش کاری وجود دارد و به همین دلیل بازدهی دستگاه کاهش مییابد.
- امکان برش مواد با ضخامتهای زیاد در این فرایند وجود ندارد.
- برش کاری پلاسما منجر به ایجاد دود و سر و صدای زیادی میشود؛ به همین دلیل باید از آن در فضای باز و در مکانی با تهویه مناسب استفاده کرد.
- در حین این فرایند نور شدید و زیادی نیز تولید میشود که در حین انجام آن نیاز به استفاده از محافظ چشم وجود دارد.
- در فرایند برش پلاسما، در صورت رعایت نکردن نکات ایمنی کار با دستگاه برش، احتمال برق گرفتگی نیز وجود دارد.
- تعمیر دستگاه برش پلاسما و تامین تجهیزات مورد نیاز آن، مانند گاز مورد نیاز و الکترود، هزینه بالایی را شامل میشود.
- این روش مصرف انرژی بسیار بالایی دارد.
- برش کاری پلاسما در عمق برش نیز شامل محدودیت است و برای برش خشک عمق برش حداکثر 160 میلیمتر و برای برش زیر آب عمق برش حداکثر 120 میلیمتر را شامل میشود.
سوالات متداول
برش کاری پلاسما با برش هوا گاز چه تفاوتی دارد؟
هر دوی این روشها برای برش فلزات مورد استفاده قرار میگیرند. برش پلاسما یک برش با قوس الکتریکی است که در مقایسه با سایر روشهای برشزنی از جمله برش هوا گاز، سرعت بالاتری دارد. همچنین این روش دقت بالاتر و فاصله برش کمتری را نسبت به برش هواگاز شامل میشود.
اما در برش هواگاز فرایند برش به صورت عمودی انجام میشود که از آن غالبا برای برش زدن آهن و شمشهای فولادی ضخیم در حد 2 و نیم متر، استفاده میشود. تهیه تجهیزات و لوازم مورد نیاز برای برش هوا گاز نسبت به روش برش کاری پلاسما نیاز به سرمایه کمتری داشته و روشهای نگهداری و تعمیرات تجهیزات مورد استفاده در این روش نیز آسانتر است.
فرایند قوس برش پلاسما چگونه انجام میشود؟
در فرایند برشکاری پلاسما، پس از ورود برق به الکترودهای دستگاه و ایجاد جرقه، یک قوس الکتریکی بین الکترود و فلز رسانا ایجاد میشود. در این فرایند الکترود به عنوان کاتد و فلز به عنوان آند عمل کرده و در نتیجه آن قوس برش شکل میگیرد. برای برش پلاسمای بهتر در این فرایند استفاده از دستگاههای برش پلاسما با امکان ایجاد قوسهای فشردهتر و متمرکزتر بسیار اهمیت دارد تا در نتیجه آن بتوان برشهای دقیقتر و قویتری ایجاد کرد.
دستگاه برش پلاسما چه کاربردهایی دارد؟
برش پلاسما برای برش فلزات غیرآهنی و فولادهایی با ضخامت کمتر از 2.54 سانتیمتر یک روش بسیار ایده آل محسوب میشود. در روش برش هواگاز، نیاز به کنترل دقت سرعت برش توسط اپراتور وجود دارد تا فرایند اکسید شدن به درستی انجام شود. اما در فرایند برش کاری با دستگاه برش پلاسما نیاز به دقت بالا وجود ندارد و انجام این فرایند به صورت اتوماتیک امکانپذیر است. استفاده از دستگاه برش پلاسما همچنین در مواردی که نیاز به سرعت بالای انجام فرایند وجود دارد، کاربرد بسیاری دارد و به راحتی در برشهای غیرخطی مورد استفاده قرار میگیرد.
برش کاری پلاسما چه محدودیتهایی را نسبت به روش هوا برش شامل میشود؟
استفاده از دستگاههای برش کاری پلاسما هزینه بیشتری را نسبت به روش هوابرش شامل میشود. همچنین در روش برش کاری هوابرش (هواگاز) نیاز به استفاده از انرژی الکتریکی و هوای فشرده وجود ندارد و به همین دلیل این روش کاربرد بیشتری در برخی صنایع دارد. سرعت انجام فرایند برش نیز در برش کاری پلاسما برای برشهای ضخیمتر غالبا کندتر از روش هواگاز میباشد.
جمع بندی
همانطور که خواندید، برش کاری پلاسما یکی از فرایندهای پرکاربرد در صنایع مختلف است که در آن از پلاسمای داغ برای برش مواد رسانا استفاده میشود. این روش برش کاری، سرعت و دقت بالاتری نسبت به اکثر روشهای برش کاری را شامل میشود و میتواند به عنوان یکی از بهترین روشها در این زمینه شناخته شود. همچنین به دلیل هزینه کمتر این فرایند، قابلیت تکرارپذیری و کاربرد گسترده این روش روی فلزات مختلف، امروزه از برش کاری پلاسما در صنایع گوناگون برای کاربردهای متنوع استفاده میشود.