در گذشته، زمانی که از روش ریخته گری برای ساخت ابزار مهندسی مختلف استفاده میشد، همیشه برای تولید قطعات با دقت ابعادی بالا چالشهایی وجود داشت؛ تا زمانی که روشهای ریخته گری دقیق اختراع شدند. روش ریخته گری دقیق یکی از معتبرترین روشهای ریخته گری است که برای ساخت و شکلدهی ابزارها و قطعات مختلف صنایع مورد استفاده قرار میگیرد.
در واقع، استفاده از روش ریخته گری دقیق منجر به تولید قطعاتی بسیار دقیق و با کیفیت میشود. در زمانهای قدیم نیز از این روش برای ساخت بتها، جواهرات و مقبرهها استفاده میشد تا امروز که این روش اهمیت بسیاری در تولیدات صنعتی دارد.
اگر میخواهید با ریخته گری دقیق، ویژگیها و کاربردهایش بیشتر آشنا شوید، مطالعه این مقاله جامع را از دست ندهید.
ریخته گری دقیق چیست؟
همانطور که احتمالا میدانید، ریخته گری روشی برای تولید قطعات و ابزارهای مختلف در حوزه مهندسی است. در این روش، فلز مذاب به داخل قالبهای نسوز ریخته شده و پس از گذشت مدت زمان مشخصی مواد داخل قالب سرد و منجمد شده و در نهایت نیز قطعه از قالب جدا میشود. ریخته گری دقیق (Investment Casting)، از انواع روشهای ریخته گری است که در آن یک مدل مومی یا پلاستیکی به درون دوغاب مواد نسوز فرو برده میشود.
در این روش، داشتن دقت بالا از نظر ابعادی بسیار دارای اهمیت است و هر چه این دقت بیشتر باشد، ریخته گری نیز دقیقتر انجام میشود.
در روش ریخته گری دقیق، قالبهای نسوز با پوشاندن مدلهای از بین رونده ساخته شده و فلز مذاب برای انجماد و شکلگیری قطعه نهایی به این قالب انتقال پیدا میکند. مهمترین مزیت این روش، ریخته گری فلزاتی با دمای ذوب بالا است که قابلیت قالبگیری در گچ یا فلز را ندارند. همچنین این روش، برای تولید قطعات فلزی دارای هندسه و ابعاد پیچیده بسیار مناسب است.
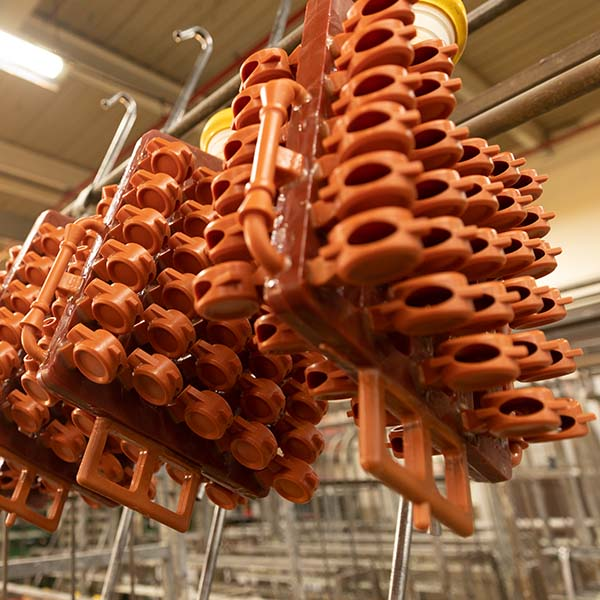
قالبهای ریخته گری دقیق از یک مدل موم با ابعاد قطعه موردنظر تولید میشوند. مدلهای به کار رفته نیز غالبا از جنس موم یا پلاستیک هستند که با سوزاندن یا ذوب از محفظه قالب خارج میشوند. امروزه بسیاری از آلیاژهای فلزی با این روش، ریخته گری میشوند. تولید قطعات به این روش، یک سری فرایندهای تکرارشونده را شامل میشود که منجر به افزایش هزینههای مربوطه و زمان تولید نسبت به سایر فرایندهای ریخته گری میشود؛ اما چون در این روش ساخت قطعات با ابعاد دقیق و پیچیده بسیار باکیفیت انجام میشود، در صنایع مختلف بسیار کاربرد دارد.
انواع مختلفی از بهترین انواع ریخته گری دقیق موجود است، از جمله ریخته گری سرمایه گذاری ، ریخته گری سرامیکی، ریخته گری فلز، ریخته گری تحت فشار و ریخته گری فوم از دست رفته. ریخته گری سرمایه گذاری رایج ترین نوع مورد استفاده برای تولید ریخته گری فلزات آهنی و غیرآهنی است. ریخته گری سرمایه گذاری که به عنوان ریخته گری موم گم شده نیز شناخته می شود، فرآیندی است که از موم برای ایجاد قالب برای قطعات فلزی استفاده می کند. این روش امکان دقت بیشتر و سطوح صاف تر را نسبت به ریخته گری شن و ماسه سنتی فراهم می کند.
انواع روشهای ریخته گری دقیق
در حال حاضر، ریخته گری دقیق یک مفهوم کلی در صنعت محسوب میشود و به همین دلیل روشهای مختلفی در این فرایند مورد استفاده قرار میگیرند. در حالت کلی، ریخته گری دقیق به دو نوع مختلف تقسیمبندی میشود:
ریخته گری دقیق واترگلس و ریخته گری دقیق سیلیکا سل (سیلیکای کلوئیدی)
در ادامه این روشها معرفی شده اند.
ریخته گری دقیق واترگلس (water glass Investment casting)
این روش برای اولین بار در کشور شوروی سابق انجام شده و سپس در کشور چین معرفی شد. ریخته گری دقیق واترگلس متداولترین روش ریخته گری در چین است و هزینه تولید قطعات در آن بسیار کمتر از ریخته گری سیلیکا سل میباشد. این روش غالبا برای ریخته گری فولاد مورد استفاده قرار میگیرد. در این روش از واترگلس یا چسب سدیم سیلیکات برای ادغام پوسته سرامیکی و مدل استفاده میشود. به همین دلیل این روش با نام ریخته گری سدیم سیلیکات نیز شناخته میشود.
ریخته گری دقیق سیلیکاسل (silica sol Investment casting)
در این روش از ترکیب سیلیکاسل زیرکون به عنوان قالب استفاده میشود. این ترکیب با اینکه هزینه زیادی را شامل میشود، اما میتوان قطعاتی بسیار دقیق و با کیفیتی را با استفاده از آن تولید کرد. در واقع، این روش منجر به تولید قطعه با تمیزترین سطح و کمترین عیوب، میشود. روش ریخته گری سیلیکاسل غالبا برای ریخته گری استنلس استیل (stainless steel) یا همان فولاد ضدزنگ مورد استفاده قرار میگیرد.
صافی قطعه تولید شده در این روش، بسیار بهتر از ریخته گری واترگلس است و قطعات تولید شده از نظر ابعادی با الگوی اصلی تطابق بیشتری دارند.
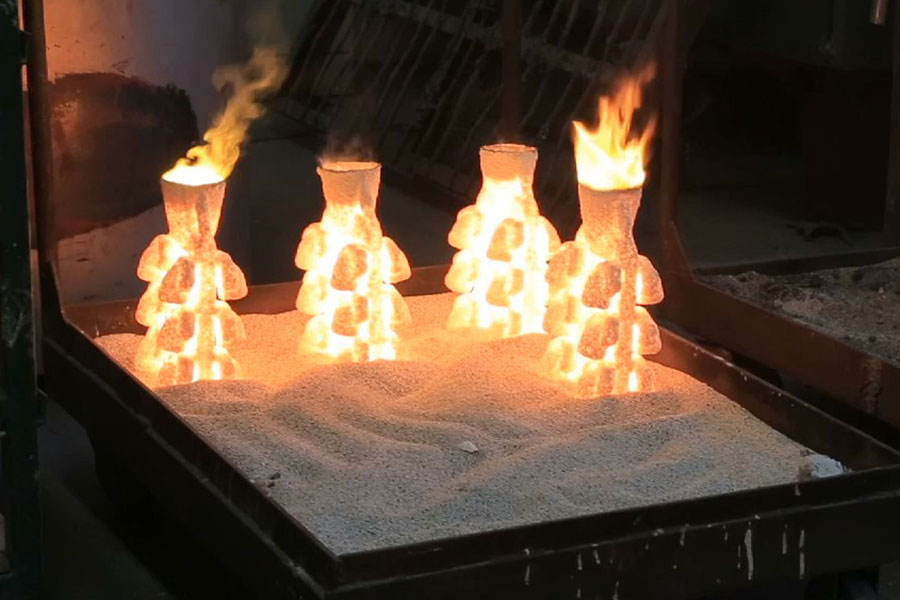
سایر روشهای ریخته گری دقیق که کاربرد کمتری دارند، عبارتند از:
ریخته گری دقیق فشاری در خلاء (VPC)
در این روش، ریخته گری دقیق با استفاده از خلاء انجام شده که استفاده از فشار گاز یا خلاء در این روش باعث عملکرد بهتر ریخته گری میشود. ریخته گری فشاری در خلاء بیشتر برای تولید جواهرات اعم از جواهرات نقره و طلا کاربرد دارد. همچنین امکان اجرای ریخته گری برای برخی از ابر آلیاژها نیز در این روش وجود دارد.
برای ایجاد خلاء در این روش از ماشینهای VPC استفاده میشود. این ماشینها دو محفظه بالایی و پایینی را شامل میشوند که در محفظه بالایی مواد مذاب قرار گرفته و در محفظه پایینی قالب ریخته گری دقیق قرار میگیرد. در اینصورت با وجود دو محفظه میتوان فشار لازم را روی آلیاژ ایجاد کرد.
ریخته گری دقیق جاذبه معکوس (CGC)
قالبهایی که در این روش مورد استفاده قرار میگیرند، یک مجرای دارند که وارد مواد مذاب میشود. با قرار دادن قالبها در ماده مذاب، به دلیل خلاء موجود، مواد مذاب به درون قالب کشیده میشوند. پس از آن، قالب خنک شده و زمانی که بخشهای مهم قطعه منجمد شد، خلاء برداشته شده و بخشهای اضافی قطعه نیز از قالب خارج میشوند.
در این روش، فلز مذاب از هرگونه سرباره کاملا خالی است. در روش ریخته گری جاذبه معکوس امکان ریخته گری فلزات با چگالی پایین و با بهترین بازده فراهم است. همچنین به دلیل قابلیت کار در دمای پایین، امکان مشاهده دانهبندی مطلوب نیز در این روش وجود دارد.
ریخته گری دقیق پوستهای (Shell Mold Casting)
در این روش، روی سطح درختچهها یک لایه نازک ایجاد میشود. این لایه از ذرههای ماسه نسوز تشکیل شده و برای پوشش مدل درختچهای مورد استفاده قرار میگیرد. روش ریخته گری دقیق پوستهای، برای آلیاژهایی مناسب است که نقطه ذوب آنها بیشتر از 100 درجه سانتیگراد باشد. در نتیجه از این روش برای تولید قطعات فولادهای ساده کربنی، فولادهای آلیاژی، آلیاژهای مقاوم در برابر حرارت، فولادهای ضدزنگ و سایر آلیاژها با نقطه ذوب بالای 100 درجه سانتیگراد استفاده میشود.
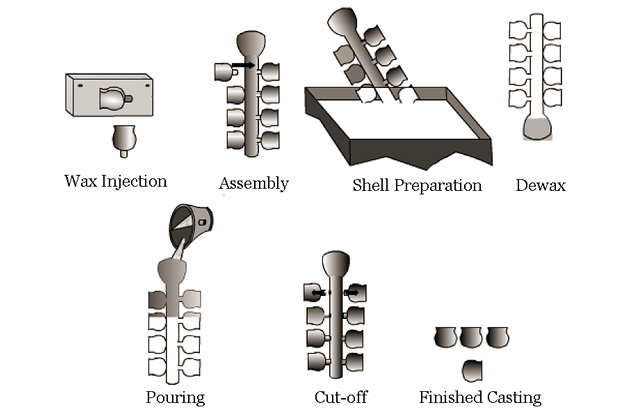
مراحل و فرایند ریخته گری دقیق
ریخته گری دقیق، در دو نوع روش مستقیم و روش غیر مستقیم انجام میشود. در روش مستقیم یا موم اصلی، به تولید قالبهای نسوز و خارج کردن موم نیازی نیست. اما در روش غیر مستقیم که ساخت آن ملزم به استفاده از موم میباشد، کپیهایی از الگوی اصلی ایجاد شده و نیاز به تولید قالبهای نسوز و خارج کردن موم وجود دارد.
در ادامه، فرایند انجام ریخته گری دقیق توسط روش غیر مستقیم شرح داده شده است.
برای انجام ریخته گری دقیق به روش غیرمستقیم مراحل زیر دنبال میشوند:
مرحله اول: الگوسازی
در ابتداییترین مرحله، الگوی اصلی ساخته میشود. در این مرحله، با تزریق موم به داخل قالب فلزی، الگوی اصلی شکل میگیرد. الگوی مومیدر واقع یک قطعه ریخته گری است که میتوان به صورت دستی آن را تهیه کرد؛ اما در صورتی که از پرینتر سه بعدی استفاده شود، نتیجه دقیقتری حاصل خواهد شد. همچنین با استفاده از پرینتر سه بعدی، هزینهها کاهش یافته و قطعات نیز با کمترین میزان خطا در ابعاد مختلف تولید میشوند.
هر تعداد الگوی مومی ساخته شود، همان تعداد نیز محصول نهایی تولید خواهد شد. در این مرحله برای درست کردن ساختارهای داخلی، امکان استفاده از ماهیچهها نیز وجود دارد. پس از تشکیل الگو، این الگو به راهگاه متصل میشود تا یک مونتاژ درختچه مانند ساخته شود. فلز مذاب از این راهگاهها وارد حفرههای قالب شده و در آن جریان مییابد.
مرحله دوم: ساخت قالب
پس از الگوسازی، با استفاده از ابعاد الگوی اصلی یک قالب مناسب ساخته میشود. در این مرحله، درختچه مونتاژ درون دوغاب سرامیکی فرو رفته و یک لایه پوشش بیرون آن ایجاد میشود. پس از مدت زمان مشخصی این دوغاب خشک شده و پوسته سرامیکی تشکیل میشود. این فرایند دائم تکرار میشود تا جایی که پوسته به قدری ضخیم شود که بتواند ذوبریزی یا همان ریخته گری را تحمل کند.
پس از آن، پوسته درون کوره قرار داده میشود. با قرار گرفتن پوسته درون کوره، موم ذوب شده و یک پوسته سرامیکی تو خالی که همان قالب قطعه است، باقی میماند. به همین دلیل روش ریخته گری دقیق با نام ریخته گری لاست وکس (Lost Wax) یا موم فداشونده نیز شناخته میشود.
در روش مستقیم ریخته گری دقیق، قالب مورد نظر با استفاده از مدل اصلی که غالبا فلزی است، ساخته میشود. در واقع الگو در روش مستقیم باید فلز بوده و نقطه ذوب بیشتری نسبت به قالب داشته باشد.
مرحله سوم: تشکیل قالب
پس از ذوب شدن موم درون قالب، رطوبت و موم موجود در این قالبها باید از بین بروند. برای این منظور، قالبها در دمای 1100 درجه سیلیسیوس قرار میگیرند. هرچه گرما بیشتر باشد، دقت کار نیز افزایش مییابد. همچنین با بیشتر شدن گرما زمان بیشتری نیز برای انجماد نیاز خواهد بود. در نهایت نیز قالب سرامیکی آماده استفاده است.
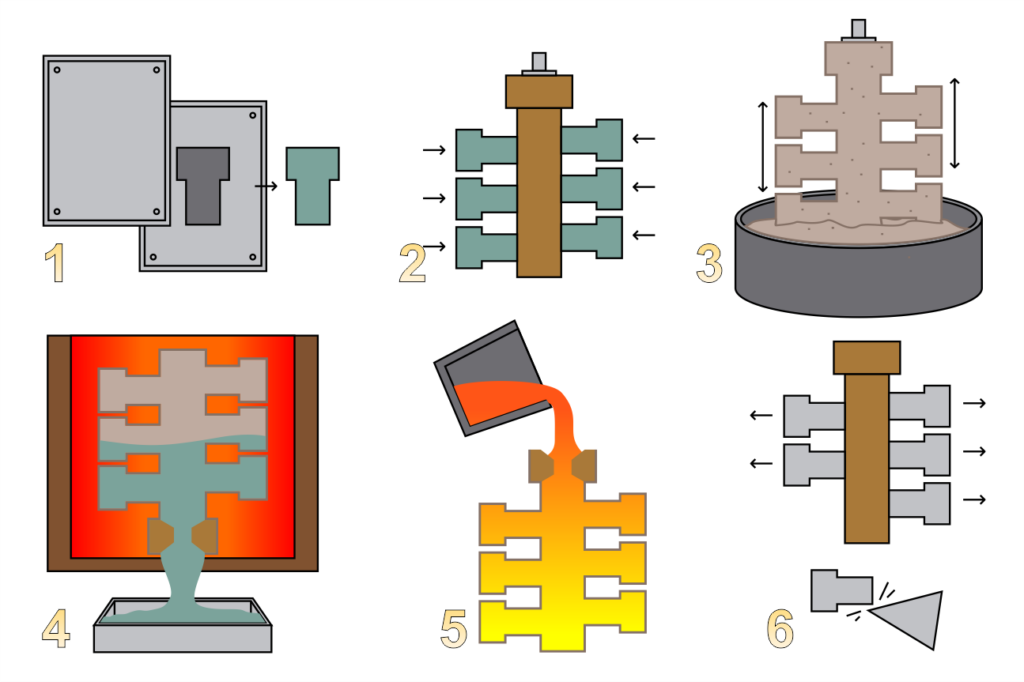
مرحله چهارم: ذوبریزی
در این مرحله ذوبریزی یا همان ریخته گری فلز انجام میشود. برای این کار شمش فلز ابتدا باید ذوب شده و به حالت مذاب در بیاید. همچنین برای انجام فرایند ذوبریزی باید ابعاد و مشخصات قالب به طور دقیق در نظر گرفته شوند. ذوب ریزی یا همان ریخته گری فلز درون قالب میتواند در خلاء، به کمک فشار، به کمک گرانش و یا با استفاده از نیروی گریز از مرکز انجام شود. در نهایت نیز فلز مذاب از طریق راهگاه به داخل حفره قالب ریخته میشود.
مرحله پنجم: خارج کردن قطعه
پس از اینکه فرایند ریخته گری یا ذوب ریزی انجام شد، قالب در دمای اتاق سرد میشود تا قطعه راحتتر خارج شود. هر چه قطعه ضخیمتر باشد، زمان خنکسازی نیز بیشتر خواهد بود. پس از منجمد شدن قطعه، میتوان آن را به کمک چکش جدا کرد. برای این کار غالبا با لرزش و شکستن پوسته سرامیکی، قطعه نهایی تولید شده از قالب جدا میشود.
در نهایت، برای حذف فلز اضافی قطعات از راهگاه جدا میشوند. برای اینکه قطعه سطحی صاف و یکنواخت داشته باشد، غالبا از شات بلاست در این مرحله استفاده میشود. همچنین ممکن است برای بهبود خواص مکانیکی محصولات، یکسری عملیات حرارتی نیز انجام شوند.
مواد مورد استفاده در ریخته گری دقیق
همانطور که احتمالا میدانید، مواد مورد استفاده در فرایندهای ریخته گری ویژگیهای شیمیایی یا فیزیکی متفاوتی دارند و بسته به این ویژگیها در حین فرایند واکنشهای مختلفی از خود نشان میدهند. در واقع برخی مواد هستند که با توجه به خواص شیمیایی یا فیزیکی فوقالعادهای که دارند، در صنایع مختلف کاربرد بیشتری داشته و رایجتر هستند.
براساس ماده مورد استفاده در فرایند ریخته گری، میتوان این فرایند را به چند دسته مختلف تقسیم بندی کرد:
- ریخته گری فولاد: ریخته گری با استفاده از فلز فولاد در محیطهای دارای رطوبت و محیطهایی که دمای زیادی دارند، بهتر انجام میشود. فلز فولاد معمولا با خوردگی مواجه میشود. به همین دلیل عناصر دیگری به آن اضافه میشوند. در اینصورت ترکیب فولاد با موادی مانند نیکل و یا کروم میتواند باعث جلوگیری از تشدید خوردگی فولاد شود.
- ریخته گری مس: در فلز مس، امکان هدایت جریان الکتریکی یا حتی هدایت حرارت به سادگی امکانپذیر است. همچنین چکشخواری فلز مس نیز بسیار مناسب بوده و دارای قابلیت شکلپذیری بالایی میباشد. به همین دلیل این فلز نیز غالبا در ریخته گری دقیق مورد استفاده قرار میگیرد.
- ریخته گری روی: اگر نیاز به انجام ریخته گری با سرعت بالا وجود داشته باشد، از فلز روی استفاده میشود. ریخته گری روی علاوه بر اینکه سرعت بالایی دارد، از نظر اقتصادی نیز بسیار بهصرفه است. در این روش، قطعات بسیار سریعتر خنک شده و تکمیل حفرهها نیز در این روش، در کمترین زمان ممکن انجام میشود.
- ریخته گری چدن: ریخته گری فلز چدن، مقاومت و استحکام زیادی دارد. در ریخته گری چدن غالبا وزن چدن کم است و از نظر پرداخت هزینه نیز این روش بسیار مقرون بهصرفه میباشد. از دیگر ویژگیهای چدن میتوان به قابلیت انعطافپذیری بالای آن اشاره کرد که با داشتن این قابلیت، شکلپذیری مطلوبی را نیز شامل میشود.
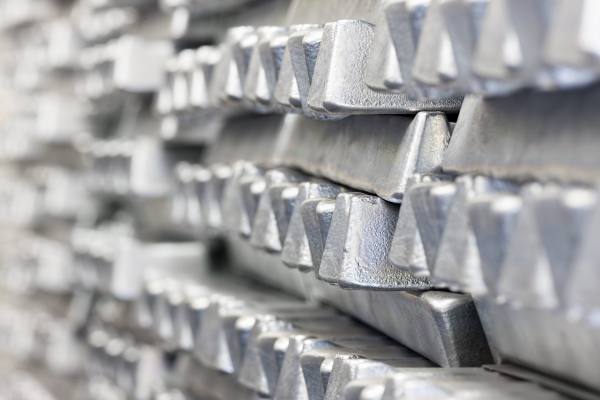
ابزارهای مورد استفاده در ریخته گری دقیق
همانطور که خواندید، استفاده از فرایندهای مختلف ریخته گری دقیق باعث تولید قطعات با کیفیت میشود. ابزارهایی که در تمامی فرایندهای مختلف ریخته گری دقیق مورد استفاده قرار میگیرند، با یکدیگر مشابه هستند. در واقع، تنها پارامترهای ریخته گری یا برخی از آلیاژهای خاص است که در این فرایندها با یکدیگر تفاوت دارند.
در نتیجه میتوان گفت دستگاههای مورد نیاز در فرآیندهای مختلف ریخته گری عبارتند از:
- دستگاههای برش
- دریلهای صنعتی
- کوره قوس خلاء
- کوره مقاومت الکتریکی
- کوره حرارتی
- کوره بوتهای گازسوز
- کوره مخصوص پخت قالبهای سرامیکی
- کوره ذوب القایی
- سیستم پیشگرم
- دستگاههای تراش
- آلیاژهای دارای ضریب انبساط بالا
- آلیاژهای غیرفلزی مانند مس و نیکل
با استفاده از این تجهیزات، فرایند ریخته گری دقیق به روشهای مختلفی انجام میشود که انتخاب روش نیز به نوع قطعه نهایی بستگی دارد. به همین دلیل، بهتر است ابتدا خواص شیمیایی و مکانیکی محصول به طور دقیق مشخص شده و سپس روش ریخته گری دقیق انتخاب شود.
کاربرد ریخته گری دقیق
ریخته گری دقیق یکی از فرایندهای مهم در صنایع مختلف است که برای شکل دادن مواد و تولید قطعات با کیفیت و دقت بالا مورد استفاده قرار میگیرد. در واقع، امکان تولید پیچیدهترین قطعات فلزی با استفاده از آلیاژهای متفاوت در این روش وجود دارد. قطعاتی مانند چرخ دنده، جواهرات و برخی از وسایل دندانپزشکی با استفاده از فرایند ریخته گری تولید میشوند.
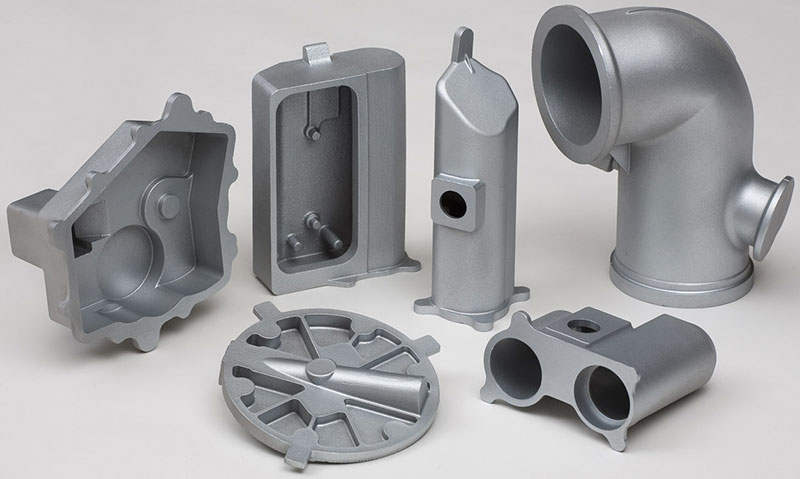
در ادامه به برخی از مهمترین و متداولترین کاربردهای ریخته گری دقیق اشاره شده است:
- صنایع خودروسازی و یا ساخت وسایل نقلیه: در این صنایع از فرایند ریخته گری برای تولید پیستونهای وسایل نقلیه یا سرسیلندرها استفاده میشود. همچنین در برخی موارد برای تولید تجهیزات راهآهن یا کشتیسازی نیز از فرایند ریخته گری استفاده میشود.
- صنایع نظامی: غالبا در صنایع نظامی نیاز است که تسلیحات با دقت و ظرافت بالا ساخته شوند. به همین دلیل در این صنایع نیز غالبا از روش ریخته گری دقیق برای تولید برخی از قطعات خودروهای جنگی، اسلحهها یا سایر مهمات استفاده میشود.
- صنایع الکتریکی: در این صنایع نیز از ریخته گری دقیق برای بهبود تولید پمپ، ژنراتور و موتورهای احتراق استفاده میشود.
- صنایع لوازم خانگی یا تاسیسات: در تاسیسات از فرایند ریخته گری برای ساخت تاسیسات سرمایشی و لولههای مختلف استفاده میشود. در صنایع لوازم خانگی نیز فرایند ریخته گری غالبا در تولید بسیاری از لوازم خانگی استفاد میشود.
- صنایع ماشین آلات سنگین: فرایند ریخته گری غالبا برای قطعات بسیار سنگین یک محدودیت وزنی را شامل میشود. اما این فرایند در تولید ماشین آلات سنگین مخصوص کشاورزی یا ماشین آلات راهسازی نیز کاربرد دارد.
- صنایع تولید وسایل تزئینی: از فرایند ریخته گری همچنین در صنایع تزئینی و حوزههای مختلف هنری نیز استفاده میشود. به عنوان مثال این فرایند در ساخت مجسمه، جواهرات یا وسایل دکوری بسیار کاربرد دارد.
مزایا و معایب ریخته گری دقیق
همانند تمامی فرایندهای صنعتی، ریخته گری دقیق نیز یکسری مزایا و معایب را شامل میشود. از مهمترین مزایای این روش میتوان به موارد زیر اشاره کرد:
- مومهایی که در فرایند ریخته گری دقیق مورد استفاده قرار میگیرند، قابلیت استفاده مجدد دارند و میتوان در ریخته گری بعدی از آنها استفاده کرد. زیرا این مومها قابل بازیافت هستند و این قابلیتشان باعث میشود که در مصرف مواد مورد نیاز صرفهجویی شود.
- از برترین ویژگیهای این فرایند این است که در آن ویژگیهای ماده به صورت دقیق تنظیم میشود. با این کار میتوان به خوبی خواص مکانیکی و شیمیایی ماده مانند اندازه دانهها را کنترل کرد.
- با استفاده از ریخته گری دقیق میتوان قطعاتی که دارای اشکال هندسی پیچیده هستند را نیز به طور دقیق تولید کرد. با این قابلیت نیز خطای ابعادی قطعات تا حد زیادی کاهش پیدا میکند.
- غالبا پس از تولید قطعه با روش ریخته گری دقیق نیاز به پردازش سطح قطعه وجود ندارد.
- همچنین غالبا اکثر قطعات پس از ریخته گری دقیق نیاز به جوشکاری ندارند و ممکن است بسته به نوع فلز، عملیات جوشکاری به میزان کمی انجام شود. این قابلیت نیز باعث صرفهجویی در هزینه و زمان انجام فرایند ریخته گری میشود.
- از این روش میتوان در ساخت قطعات مختلف با استفاده از آلیاژهای متنوع استفاده کرد. از جمله رایجترین آلیاژهایی که در این فرایند مورد استفاده قرار میگیرند، میتوان به آلیاژهای آلومینیوم و چدن اشاره کرد.
- از فرایند ریخته گری میتوان برای فلزات دارای دمای ذوب بسیار بالا نیز استفاده کرد.
- در این روش، بدون اینکه به قطعه آسیبی وارد شود، میتوان بخشهای نازک آن را تراش داده و این بخشها را از بین برد.
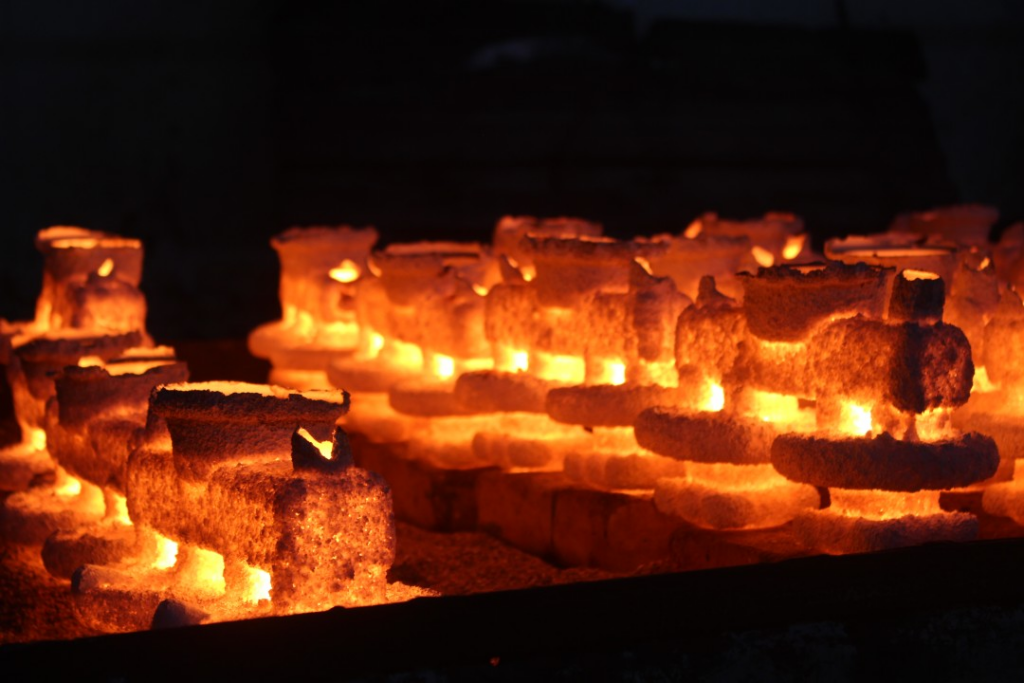
اما در کنار این مزایا، ریخته گری دقیق یکسری معایب را نیز شامل میشود؛ محدودیت های روش ریخته گری دقیق عبارتند از:
- در روش ریخته گری دقیق به دلیل استفاده از تجهیزات خاص، تولید قالبهای مورد نیاز، استفاده از مواد نسوز و همچنین با بهکارگیری نیروهای ماهر و متخصص، هزینه نهایی کمی بالاتر است. همچنین هرچه قطعه پیچیدهتر باشد، هزینه تولید آن با این روش بیشتر خواهد بود.
- در روش ریخته گری دقیق ممکن است هنگام منجمد شدن، قطعه دچار تغییر شکل شده یا حتی سوراخهای کوچکی در سطح خارجی آن ایجاد شود. همچنین در صورتی که در محیط ذرههای اضافی وجود داشته باشند، سطح قطعه دچار ناهمواری میشود. به همین دلیل ریخته گری دقیق باید با دقت بالا و مهارت کافی انجام شود تا این مشکلات به وجود نیاید.
- در برخی موارد، در ریخته گری دقیق امکان به وجود آمدن حفرههایی با قطر کمتر از 1.6 میلی متر و یا عمق بیشتر 1.5 برابر قطر وجود ندارد. به همین دلیل، تولید این دسته از قطعات با ریخته گری دقیق کمی مشکل است. حتی ممکن است نتیجه مورد نظر حاصل نشود.
- با این روش، امکان تولید قطعات مورد نظر با ابعاد متفاوت وجود دارد؛ اما این روش نسبت به ریخته گری ماسهای در خصوص تعیین ابعاد محدودیت بیشتری را شامل میشود.
- همچنین در ریخته گری دقیق وزن قطعه بسیار اهمیت دارد و ممکن است ساخت ابزار و قطعات سنگین در این روش با محدودیت همراه باشد.
- روش ریخته گری دقیق طولانیتر است و با استفاده از این روش، قطعه زمان بیشتری برای آمادهسازی نیاز دارد.
تقریبا اکثر معایب گفته شده به دلیل انجام نادرست فرایند ریخته گری دقیق ایجاد میشوند. در واقع اگر تولید قطعات با روش ریخته گری دقیق با مهارت و دقت بالا انجام شود، قطعه نهایی نیز بسیار دقیق و باکیفیت خواهد بود.
نکاتی در رابطه با فرایند ریخته گری دقیق
همانطور که در طول این مقاله بارها به آن اشاره شد، ریخته گری دقیق فرایندی بسیار حساس است که باید با دقت بالا و توسط یک فرد ماهر انجام شود. در این میان، رعایت یکسری نکات نیز میتواند در انجام بهتر فرایند و کیفیت قطعه نهایی تولید شده با استفاده از این روش، موثر باشد. برخی از مهمترین نکات حین فرایند ریخته گری دقیق عبارتند از:
- میزان کربن مورد استفاده در قطعات، در این فرایند بسیار اهمیت دارد. زیرا اگر مقدار کربن بیشتر شود، ممکن است قطعه آب شود. در نتیجه بهتر است برای جلوگیری از آب شدن یا منقبض شدن قطعه، کربن کمتری در آن به کار رود.
- برای جلوگیری از آبرفتگی قطعه، ضخامت جداره آن نیز در هنگام ریخته گری دارای اهمیت است.
- همچنین در حین این فرایند بالا رفتن فشار در قطعه نیز باعث کاهش آب رفتگی آن میشود.
- در ریخته گری دقیق طراحی سطح عمومی قطعات به صورت مایل نیز بسیار اهمیت دارد؛ زیرا باعث میشود که قطعه هنگام خارج کردن مدل دچار آسیب نشود.
- در انتخاب روش انجام فرایند ریخته گری عوامل متعددی اعم از اندازه و وزن قطعه مورد بررسی قرار میگیرند. در اینصورت، محدودیت وزنی قطعه اهمیت داشته و پیچیده بودن یا ساده بودن طراحی و شکل هندسی قطعه نیز باید در نظر گرفته شود. همچنین بهتر است استهلاک قطعه و آلیاژهای به کار رفته در آن نیز از نظر خواص مکانیکی به صورت کاملا دقیق بررسی شوند.
سوالات متداول
مزایای ریخته گری دقیق نسبت به ریخته گری ماسهای چیست؟
در فرایند ریخته گری ماسهای از ماده پایه سیلیکا مانند ماسه برای ایجاد یک سطح از قالبگیری استفاده میشود. همچنین ممکن است در این فرایند از مقداری رس استفاده شود تا ذرات ماسه بیشتر به یکدیگر نزدیک شوند. قالبهایی که با استفاده از ماسه ساخته میشوند، انعطافپذیری بیشتری دارند اما دقت عملکرد ریخته گری ماسهای از ریخته گری دقیق کمتر است.
در واقع مزیت ریخته گری دقیق نسبت به ریخته گری ماسهای در عملکرد آن است. با استفاده از روش ریخته گری ماسهای میتوان قطعاتی را تولید کرد که سطح صافتری داشته و به ماشینکاری کمتری نیاز دارند. همچنین با ریخته گری دقیق میتوان از بسیاری از معایبی که در ریخته گری ماسهای وجود دارد، جلوگیری کرد.
از ریخته گری دقیق در چه مواردی استفاده میشود؟
ریخته گری دقیق امروزه در صنایع مختلف کاربردهای بسیاری دارد؛ زیرا با استفاده از این روش میتوان انواع قطعات صنایع مختلف اعم از پزشکی، دندانپزشکی، تجهیزات نظامی، هوافضا و… را با کیفیت و دقت بالایی تولید کرد.
هزینه ساخت قالب فلزی در ریخته گری دقیق چقدر است؟
معمولا هزینه تهیه قالب فلزی، بخش مهمی از هزینه فرایند ریخته گری دقیق را تشکیل میدهد. در صورتی که بخواهید تعداد قطعات کمیتولید کنید، ریخته گری دقیق ممکن است نسبت به سایر روشها هزینه بیشتری را شامل شود و ساخت قالب و استفاده از این فرایند در این شرایط مقرون بهصرفه نخواهد بود.
چگونه ریخته گری دقیق با سایر انواع ریخته گری متفاوت است؟
فرایند ریخته گری دقیق غالبا با استفاده از موم فداشونده انجام شده و از این طریق قالب قطعه ساخته میشود. با استفاده از ریخته گری دقیق میتوان قطعاتی با پیچییدهترین اشکال را تولید کرد و هیچ محدودیت طراحی در این روش برای ساخت قطعه وجود ندارد. همچنین در ریخته گری دقیق میزان تلورانس ریخته گری از سایر روشها دقیقتر بوده و غالبا نیاز به انجام عملیات ثانویه در این روش وجود ندارد.
در فرایند ریخته گری دقیق از چه آلیاژهایی استفاده میشود؟
در فرایند ریخته گری غالبا میتوان از کلیه آلیاژها اعم از فولاد زنگ نزن، آلومینیوم، چدن و… استفاده کرد. در واقع، استفاده از هر ماده یا آلیاژی که توانایی ریخته گری داشته باشد در این فرایند امکانپذیر است.
جمع بندی
یکی از متداولترین روشهای ریخته گری، ریخته گری دقیق است که با نام ریخته گری ظریف نیز شناخته میشود. از این فرایند برای تولید قطعات در طرحها و اندازههای گوناگون با ابعاد مختلف استفاده میشود. در واقع امکان تولید پیچیدهترین قطعات نیز با استفاده از این فرایند وجود دارد. در فرایند ریخته گری دقیق غالبا از موم فداشونده که نقش الگوی اصلی قطعه را ایفا میکند، برای تولید قالب استفاده میشود.
در نهایت نیز مواد مذاب درون قالب ریخته شده و پس از انجماد، قطعه نهایی تولید میشود. این روش نسبت به سایر روشهای ریخته گری مزایای زیادی را شامل میشود. مهمترین مزیت این روش که منجر به کاربرد فوقالعاده آن در صنایع گوناگون شده است؛ قابلیت تولید قطعات با دقت ابعادی بالا است. همچنین در این روش قطعات تولید شده، سطحی کاملا صاف و یکنواخت خواهند داشت.
در فبرینو، ما با افتخار پیشگامی در عرصهی ساخت و طراحی را بر عهده داریم. تعهد ما به استانداردهای برتر کیفی و خدمات ممتاز پس از فروش، با استفاده از دانش فنی پیشرفته و تجربیات ارزشمند، موجب شده تا اطمینان و رضایت مشتریان را به دست آوریم. برای کسب اطلاعات بیشتر و دریافت مشاوره، با ما تماس بگیرید و از خدمات ما بهره مند شوید.