امروزه، تولید قطعات یا نمونههای اولیه آنها، در یک محیط پیچیده از چالشهای مختلفی برخوردار است. برای این منظور، اغلب تولیدکنندگان از روشهای پیشرفته ماشین کاری استفاده میکنند تا بتوانند تمامی استاندردهای موردنیاز و نیازمندیهای مشتریان را برآورده کنند. سنگ زنی یکی از فرایندهای مهم تولید و ماشینکاری است که با حذف دقیق برادههای اضافی و صافکاری سطوح، نقش مهمی در صنایع مختلف دارد.
اگر میخواهید با فرایند سنگ زنی قطعات صنعتی، ویژگیها و کاربردها و انواع دستگاه سنگ زنی و حتی اصول سنگ زنی بیشتر آشنا شوید، مطالعه این مقاله از فبرینو را از دست ندهید. فبرینو برترین مشاوره، ایده پرداز و سازنده انواع قطعات صنعتی برای انواع پروژه های بزرگ و کوچک است. با مشاورین ما در فبرینو تماس بگیرید و از خدمات ما بهره مند شوید. در ادامه این مقاله همراه ما باشید.
سنگ زنی چیست؟
سنگ زنی (Grinding) یکی از مهارتهای بسیار مهم در حوزه ماشینکاری و تولید است. در این فرایند، قطعات با تلرانس بسیار کوچک تولید میشوند. فرایند سنگ زنی زیر شاخهای از عملیات ماشینکاری فلزات در صنعت تولید و ابزارسازی است. از ماشینها و آسیابهای مخصوص برای ماشینکاری مواد مختلف و برای ایجاد سطوح، شکلها و تولید قطعات در ابعاد مورد نیاز بسیار استفاده میشود. اما در برخی موارد، تولید قطعات صنعتی نیازمند دقت و کیفیت بالایی است که در این موارد، فرایند سنگ زنی غالبا به عنوان یکی از راهحلهای مناسب برای مواجهه با این چالشها مورد استفاده قرار میگیرد.
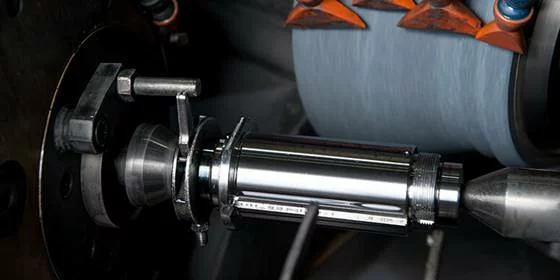
در فرایند سنگ زنی، ابزارهای بخصوصی مورد استفاده قرار میگیرند که این ابزارها از دانههای ریز و مواد ساینده (چرخ سنگ) تشکیل شده و توسط فرایند سایش، از قطعه کار که باید نرمتر از مواد باشد، برادهبرداری میکنند. در واقع، این دانهها مانند لبههای برنده عمل کرده و تعداد زیاد آنها در کنار سایشی بودن فرایند منجر به ایجاد سطوح صاف و پرداخت شده در قطعه میشوند.
هدف اصلی از استفاده از فرایند سنگ زنی ایجاد یک پرداخت سطحی بالا در مراحل نهایی ساخت قطعه یا ایجاد سطوح مبنا در شروع فرایند است. همچنین با این فرایند میتوان از سطوح سختی که سایر فرایندهای ماشینکاری در پرداخت آنها ناتوان هستند، براده برداری کرد.
استفاده از فرایند سنگ زنی مزایای بسیار دیگری نیز دارد. در این فرایند امکان تولید قطعات با دقت بسیار بالا فراهم شده و تلرانسهایی با مقدار بسیار کمتر از یک میکرومتر، برای قطر و گردی مورد نیاز، قابل دستیابی هستند. همچنین این فرایند به عنوان یک راهحل مقرون به صرفه برای تولید قطعات بادقت و با کیفیت محسوب میشود؛ که غالبا هزینه زیادی را به همراه ندارد.
فرایند سنگ زنی
سنگ زنی یک فرایند فرسایشی است که با استفاده از آن میتوان مواد اضافه موجود روی قطعه کار را با عملیات سایش برداشت. ابزارهایی که در این فرایند مورد استفاده قرار میگیرند، انواع مختلفی دارند اما در حالت کلی، تمامی این ابزارها روی خود شامل یکسری دانههای ساینده هستند که هر یک از این دانهها منجر به تغییر شکل بخش کوچکی از قطعه کار میشوند. در واقع، فرایند سنگ زنی، نهاییترین مرحله کار روی قطعه است که پس از انجام این فرایند کیفیت سطح کار افزایش یافته و به نوعی پرداخت با کیفیتی روی سطوح قطعه انجام خواهد شد.
در این فرایند، حرکت برشی میتواند توسط قطعه کار و یا توسط حرکت ابزار انجام شود که این مسئله کاملا به هندسه قطعه کار بستگی دارد. ابزارهای مورد استفاده در این روش نیز از ذرات مختلفی اعم از کاربید، سیلیسیم یا آلومین تشکیل شده و در یک ماتریس غوطهور شدهاند که با استفاده از آنها عملیات پرداخت و سنگ زنی انجام میشود. با توجه به اینکه، در یک محدوده از ابزار، اندازه ذرات سخت دارای تغییر است، به همین دلیل این ذرات با جهتهای تصادفی در داخل ماتریس قرار میگیرند.
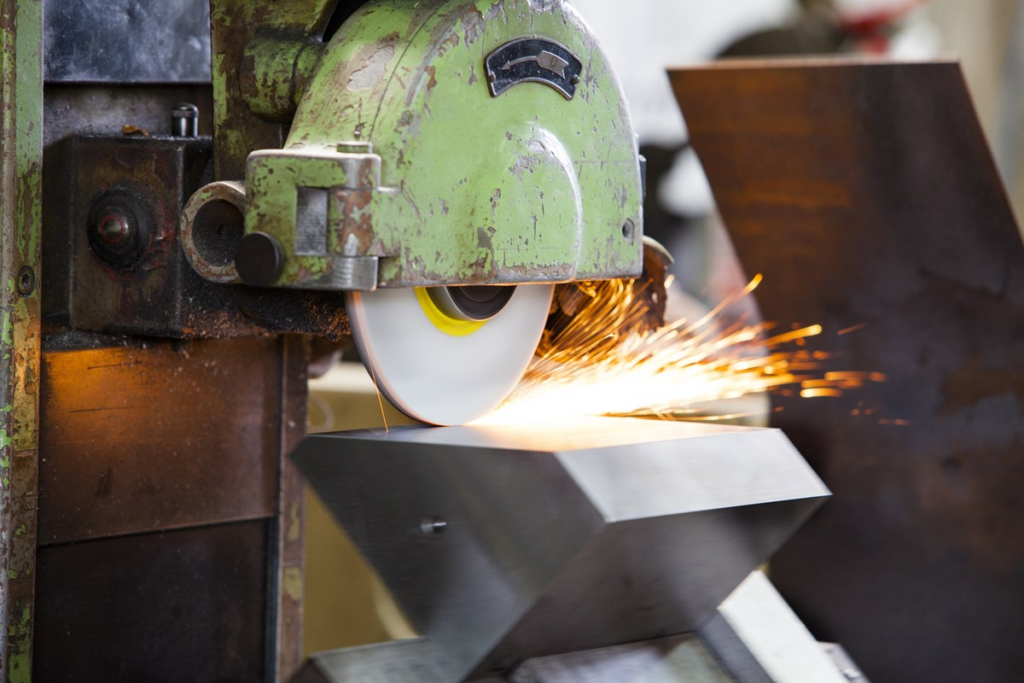
در فرایند سنگ زنی از دستگاه مخصوص این کار استفاده میشود. دستگاه سنگ زنی نیز از دو قسمت ابزار و قطعه کار تشکیل شده که شامل یک موتور گرداننده است و با سرعت مورد نیاز ابزار مورد استفاده و یا سنگ را میچرخاند. همچنین برای نگهداری قطعه کار درون فیکسچر دارای یک بستر است. در این دستگاه سر سنگ نیز برای قطعه کارهای ثابت و متحرک قابل تنظیم میباشد.
در حین انجام فرایند سنگ زنی، در انواع دستگاه سنگ زنی حرارت قابل توجهی ایجاد میشود؛ به همین دلیل این دستگاه دارای سیستم خنک کننده است تا گرما بیش از حد تحمل قطعه بالا نرود. اما در سنگهای با دقت بالا، در حدود 200 نانومتر، حرارت کمی تولید میشود که نیاز به خنککاری در این فرایند وجود ندارد.
فرایندهای صنعتی با روشها و ماشینهای مختلفی انجام میشوند که انتخاب آنها به نوع ماده قطعه کار و شکل آن بستگی دارد. سنگهای مورد استفاده نیز دارای دانهبندیهای مختلف، در قطرها و اشکال متنوع میباشند.
انواع سنگ زنی
همانطور که گفته شد، این فرایند با اشکال مختلفی از سنگ و قطعه کار انجام میشود. انتخاب فرایند مورد نیاز برای سنگ زنی به شکل قطعه، اندازه آن، سهولت فیکسچربندی و آهنگ تولید مورد نیاز بستگی دارد. در این فرایندها، حرکت نسبی سنگ سنباده ممکن است در راستای سطح قطعه کار یا به طور شعاعی، رو به قطعه کار باشد.
در بین فرایندها، فرایند سطحی بیشترین درصد کاربرد را دارد و بعد از آن نیز فرایندهای سنگ زنی رومیزی، استوانهای، تیغچه و ابزار قرار میگیرند. کم کاربردترین فرایند نیز، سنگ زنی داخلی میباشد. در هر یک از این فرایندها از ماشینهای مخصوص استفاده شد که برای انواع طرحها و اندازههای مختلف قطعه کار موجود میباشند.
ماشین های سنگ زنی به پنج دسته تقسیم می شوند : آسیاب های سطحی، آسیاب های استوانه ای، آسیاب های بدون مرکز، آسیاب های داخلی و مخصوص.
انواع دستگاه سنگ زنی
انواع سنگ زنی عبارتند از:
- سنگ زنی تخت
یکی از متداولترین فرایندها، سنگ زنی تخت است که همانطور که از نامش پیداست، برای سنگ زنی سطوح تخت مورد استفاده قرار میگیرد. در این فرایند، نظام مغناطیسی به میز ماشین سنگ زنی تخت چسبیده و قطعه کار روی یک سر این نظام بسته میشود. مواد غیر مغناطیسی نیز غالبا با فیکسچر مخصوص، نوار چسبهای دو رویه، گیره و یا با استفاده از نظام به میز بسته میشوند.
در این فرایند از ماشینهای سنگ تخت استفاده میشود که میز کار در این دستگاهها میتواند چهار وجهی باشد. در اینصورت، این فرایند میتواند یک حرکت رفت و برگشتی داشته باشد، دایرهای باشد و بدون داشتن حرکات رفت و برگشتی حول محور خود دوران کند. ابزار براده برداری یا همان چرخ سنگ نیز در این دستگاه روی یک محور افقی یا عمودی (اسپیندل) میچرخد.
یک سنگ سنباده گرد تخت نیز به محور دوران افقی دستگاه نصب میشود. سنگ زنی عرضی با رفت و برگشت طول میز و پیشروی قطعه، بعد از هر رفت و برگشت انجام میشود. در این فرایند، برای انجام عملیات رو به داخل، سنگ سنباده به شکل شعاعی (همانند یک شیار) به طرف قطعه کار حرکت میکند. اندازه یک دستگاه تخت نیز، با ابعاد سطحی که میتوان روی آن فرایند سنگ زنی را انجام داد، مشخص میشود.
- سنگ زنی استوانهای (سنگ زنی محور) (Cylindrical Grinding Machines)
در فرایند استوانهای، که با نام سنگ زنی مرغکی نیز شناخته میشود، سطح استوانهای خارجی و شانههای قطعه کار سنگ زنی میشوند. قطعه استوانهای مورد استفاده در این فرایند در حال دوران بوده و در امتداد محور خود حرکت رفت و برگشتی دارد.
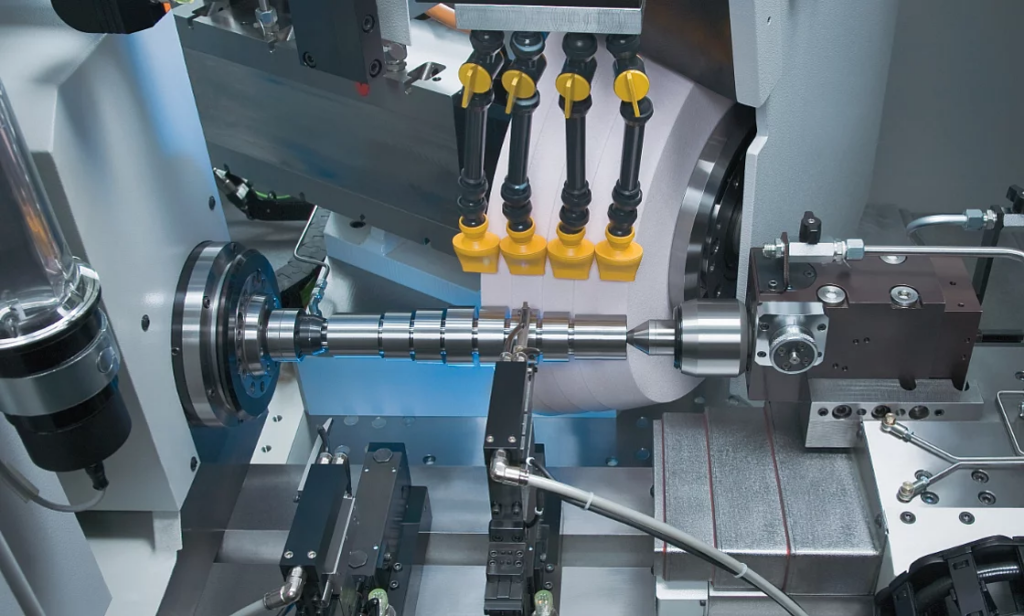
اصلیترین روش نگهداری قطعه کار در دستگاههای استوانهای، استفاده از مرغک است. در این فرایند، قطعه کار بین دو مرغک قرار گرفته، توسط یک نظام گرفته شده و یا در کلهگی ماشین سنگ زنی، یه یک صفحه نظام بسته میشود. برای سطوح استوانهای راست، در این فرایند، محورهای دورانهای سنگ و قطعه کار موازی هم هستند. موتورهای جداگانهای محور دورانهای سنگ و قطعه را با سرعتهای مختلف حرکت میدهند. قطعه کارهای با طول زیاد (دراز) یا قطعه کارهای دارای دو یا چند قطر مختلف نیز با دستگاه سنگ محور، سنگ زنی میشوند.
انواع دستگاه سنگ زنی استوانهای، همانند ماشینهای تراش، با حداکثر قطر و طول رفت قطعه کاری که میتوانند سنگ زنی کنند، شناخته میشوند و بر این اساس مورد استفاده قرار میگیرند. در این فرایند با استفاده از این دستگاهها، از سنگهای فرم استفاده میشود که در آنها سنگ به شکل قطعه تیز شده و با استفاده از آن میتوان اشکال مورد نظر را سنگ زنی فرم کرد.
در فرایند سنگ زنی استوانهای، محدوده جابجایی میز، تعیین کننده طولی از سطح قطعه کار میباشد که قابلیت سنگ زنی آن وجود دارد. در مواردی که از این دستگاه برای سنگزنی قطعات بسیار بزرگ و سنگین استفاده میشود، با توجه به اینکه حرکت میز ناشی از وزن بالای قطعه کار در این موارد دشوار است، میز و قطعه کار ثابت در نظر گرفته شده و ابزار که همان چرخ سنگ است، حرکت رفت و برگشتی انجام میدهد.
- سنگ زنی داخلی (Internal Grinding Machines)
در این نوع از انواع سنگ زنی از یک سنباده کوچک برای سنگ زنی سطوح داخلی قطعاتی مانند بوش و پوسته یاتاقانها استفاده میشود. در واقع در این فرایند، از ماشینهای مخصوص برای سایز کردن قطر انواع سوراخهای بسته، مخروطی، پله دار و… و همچنین برای افزایش صافی سطوح داخلی سوراخها یا افزایش عمق آنها استفاده میشود. به اینصورت که قطعه کار در یک نظام دوار نگه داشته شده و سنگ با سرعت بالایی در حدود 30000 rpm یا بیشتر دوران میکند.
امکان عملیات برای اشکال داخلی با سنگهای فرم که به صورت شعاعی رو به قطعه کار حرکت میکنند نیز، در این فرایند وجود دارد. همچنین امکان سنگ زنی سوراخهای مخروطی نیز در این فرایند وجود داشته و برای این منظور میتوان کله گی ماشینهای سنگ زنی داخلی را در یک صفحه افقی گرداند.
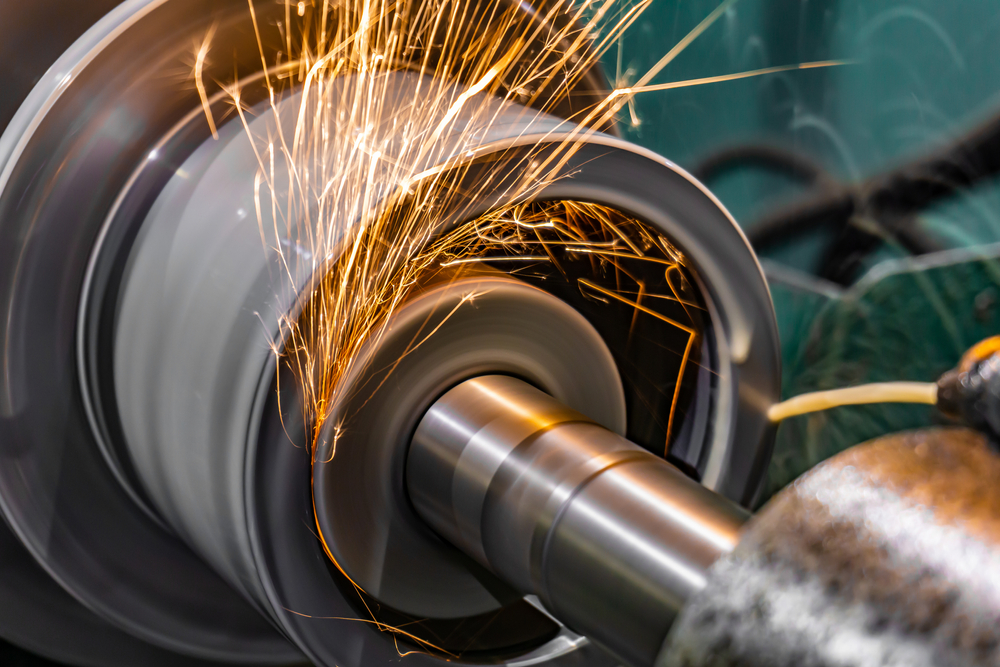
فرایند سنگ زنی داخلی به پنج نوع مختلف انجام میشود:
- در برخی موارد در این فرایند قطعه کار دورانی بدون حرکات خطی مورد استفاده قرار گرفته و چرخ سنگ شامل حرکات دورانی و خطی خواهد بود.
- در برخی موارد قطعه کار دورانی بدون حرکات خطی خواهد بود و چرخ سنگ شامل حرکات دورانی، خطی و شعاعی است. در واقع در این فرایند قطر نهایی سوراخ نیز با تنظیم موقعیت مداری چرخ سنگ تنظیم میشود.
- در برخی موارد، قطعه کار شامل حرکات دورانی و رفت و برگشتی بوده و چرخ سنگ شامل حرکات دورانی و بدون حرکات خطی است. در واقع در این فرایند چرخ سنگ روی یک اسپیندل یا موقعیت ثابت قرار گرفته و دوران میکند و قطعه کار نیز حرکات چرخشی و رفت و برگشتی خواهد داشت.
- در نوع چهارم این فرایند، قطعه بدون دوران و حرکت خواهد بود و چرخ سنگ شامل حرکات دورانی، خطی و شعاعی است. در واقع در این فرایند، برخلاف فرایندهای قبلی، قطعه در موقعیت خود کاملا ثابت بوده و تمامی حرکات رفت و برگشتی، چرخشی و شعاعی به چرخ سنگ محدود میشوند.
- در نوع پنجم این فرایند نیز از ماشینهای داخل سنگ زنی سنترلس (سنترلس داخلی) استفاده میشود که برای سایز کردن قطر و افزایش صافی سطح انواع سوراخهای ساده، پلهدار و مخروطی به روش خارج از مرکز استفاده میشود. با استفاده از این ماشینها قطعه کار میان دو غلتک تکیهگاهی و فشاری و یک چرخ تنظیم قرار میگیرد و از اسپیندل نگهدارنده قطعه کار استفاده نخواهد شد.
- سنگ زنی بدون مرغک یا سنگ زنی سنترلس (Centerless Grinding Machines) برای سطوح خارجی
این فرایند سنگ زنی یک فرایند تولید انبوه است که در آن قطعه کار به وسیله یک تیغه نگه داشته میشود و برای سنگ زنی سطوح استوانهای مورد استفاده قرار میگیرد. همچنین در این فرایند تولید پیوسته اپراتوری با مهارت کم نیز کافی است. در این فرایند از دستگاههایی استفاده میشود که این دستگاهها هیچگونه اسپیندل یا محوری برای چرخاندن قطعه کار ندارند و قطعه در تماس با چرخ سنگ قرار میگیرد.
چرخ تنظیم نیز به صورت خودکار در موقعیت صحیح خود قرار گرفته و میچرخد. قطعه کار میان چرخ سنگ و چرخ تنظیم قرار میگیرد. این دو چرخ هر دو در جهت عقربههای ساعت میچرخند و تحت تاثیر آنها نیز قطعه کار جهت خلاف عقربههای ساعت دوران میکند. از طرفی، ناحیه زیرین قطعه کار توسط یک تیغه پشتیبانی شده که از خروج احتمالی و ناگهانی قطعه کار جلوگیری میکند.
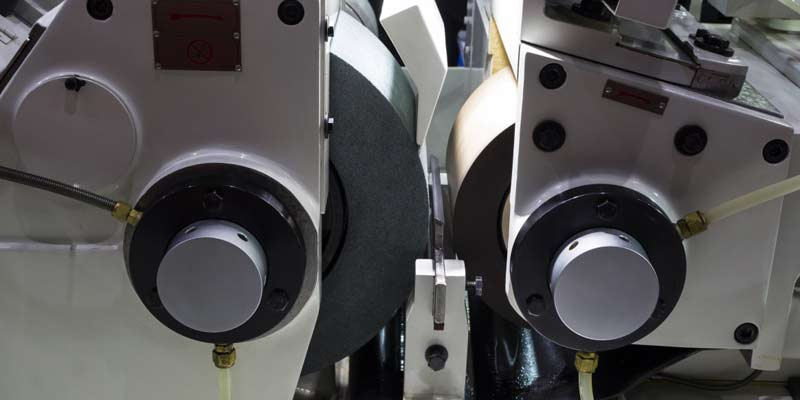
با استفاده از این فرایند نیازی به ایجاد سوراخ مرغک در قطعه وجود ندارد و نصب قطعه و انجام فرایند سنگ زنی آسانتر و سریعتر انجام میشود. قطعات نازک و بلند نیز با کمترین میزان ریسک در این فرایند قابل سنگ زدن هستند. هنگام انجام فرایند سنگ زنی خارج از مرکز در این فرایند، قطعه موقعیت صحیح خود را پیدا کرده و به درستی سنگ میخورد. همچنین در این فرایند، به جای کنترل کردن شعاع قطعه، میتوان قطر آن را کنترل کرد که باعث کاهش خطا و افزایش دقت فرایند و قطعه سنگ زنی شده، میشود.
با استفاده از فرایند سنگ زنی بدون مرغک، قطعاتی با قطرهایی به کوچکی یک دهم میلیمتر سنگ زنی میشوند. همچنین در این فرایند امکان استفاده از سنگ چرخهای بزرگ وجود داشته که استفاده از آنها در کاربردهای صنعتی باعث افزایش بهرهوری و کاهش هزینههای نگهداری دستگاه میشود. فشار ناشی از سنگ زنی در این فرایند نیز قطعه کار را محکمتر در جای خود نگه داشته و در اینصورت استفاده از مقادیر بیشتر باردهی امکانپذیر خواهد بود.
- سنگ زنی خزشی
در این فرایند، عمق برش سنگ زنی شش میلیمتر و سرعت قطعه کار پایینتر است و از آن برای برادهبرداری با آهنگهای کم و پرداخت کاریهای ظریف استفاده میشود. سنگ سنبادههای مورد استفاده در فرایند سنگ زنی خزشی غالبا از درجه نرم با چسب رزینی و با ساختاری باز استفاده میشوند تا به این ترتیب دما پایین نگه داشته شده و صافی سطح بهبود پیدا کند.
دستگاه سنگ زنی خزشی، قابلیتهای مختلفی اعم از قدرت زیاد، ظرفیت لرزهگیری بالا، سرعتهای متغیر محور دوران میز کار و ظرفیت بالای مایعات سنگ زنی را شامل میشود. در حال حاضر در این فرایند از سنگهایی استفاده میشود که قابلیت تیز شدن پیوسته سنگ سنباده با غلتکهایی از الماس را دارند.
به طور کلی، میتوان گفت که سنگ زنی خزشی از لحاظ اقتصادی نسبت به دیگر فرایندهای براده برداری به صرفهتر است و میتواند برای کاربردهای خاص دیگر مانند فرایندهای ماشین کاری نیز مقرون به صرفه باشد. از جمله کاربردهای این فرایند میتوان سنگ زنی سنبهها، جا خارها، شیارهای مته پیچی، ریشه پره توربین و انواع قطعات پیچیده سوپر آلیاژی اشاره کرد.
از آنجایی که در این فرایند سنگ سنباده به شکل قطعه کار تولیدی تیز میشود، نیازی به فرزکاری، ماشین کاری یا خانکشی قطعه کار وجود نخواهد داشت. در نتیجه از این فرایند میتوان برای قطعات ریخته گری و فورجی با اشکالی نزدیک به شکل خالص اشاره کرد. همچنین در این فرایند امکان به دست آوردن سطح مطلوب با یک پاس سنگ زدن وجود دارد اما برای صافی بهتر سطح ممکن است نیاز به انجام پاس سنگ دوم باشد.
تکنیک مورد استفاده در فرایند سنگ زنی
همانطور که خواندید، در عملیات انواع دستگاه سنگ زنی از ابزار سمباده و ساینده برای حذف مواد اضافی و پرداخت سطوح قطعههای کار استفاده میشو تا فرم و سطح دلخواه قطعه کار ایجاد شود. اصلیترین ابزار مورد استفاده در این فرایند، ماشینهایی هستند که با سرعت زیاد منجر به چرخاندن صفحهها و تسمههای سمباده و ساینده میشوند تا پرداخت و براده برداری قطعه کار سریعتر و بهتر انجام شود.
در این فرایند از تکنیکهای مختلفی استفاده میشود که از جمله مهمترین آنها میتوان به موارد زیر اشاره کرد:
- براده برداری: این تکنیک در این فرایند بسیار ضروری است و باعث شکلدهی دقیق و دستیابی قطعه کار به ابعاد مورد نیاز میشود.
- صاف کاری و پرداخت سطوح: تکنیکهای مورد استفاده برای صاف کاری و پرداخت سطوح در فرایند سنگ زنی باعث ایجاد سطوحی صاف و دقیق شده و منجر به افزایش زیبایی و عملکرد قطعه کار میشوند.
- کنترل تلورانس: تکنیکهای مورد استفاده در این فرایند به تلورانس کمتر در قطعه کار کمک کرده و در اینصورت میتوان قطعه کار را با توجه به نیازهای موجود تولید کرد.
- تیز کردن و ترمیم ابزار: در این فرایند همچنین از تکنیکهایی برای تیز کردن و ترمیم ابزارهای برش مانند فرز، متهها و قلاویزها استفاده میشود تا تیزی آنها حفظ شده و دوام و طول عمر بیشتری داشته باشند.
چرخ سنگ زنی
یکی از ابزارهای مهم و موثر ، سنگ چرخ است. روی این سنگ از مواد ساینده تشکیل شده است که به طور طبیعی روی آن قرار نگرفتهاند. در واقع برای چسباندن مواد ساینده در کنار یکدیگر، روی سنگ چرخ از ماده چسبنده استفاده میشود، که زمینه اصلی ساخت سنگ چرخ را ایجاد میکنند. مواد چسبندهای که بری این منظور مورد استفاده قرار میگیرند، باید بسیار قدرتمند باشند؛ زیرا برداشتن براده از روی قطعات سنگین نیاز به استفاده از چسبهای قوی دارد.
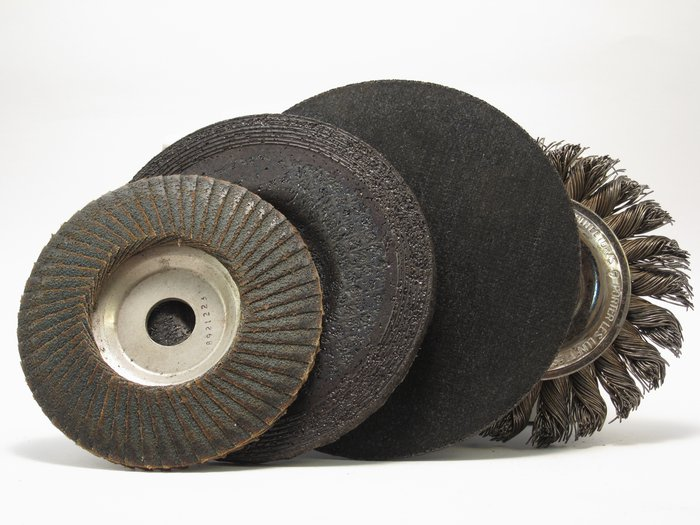
در سنگ چرخ، مواد سایشی مورد استفاده دارای خلل و فرجی هستند که طراحی آنها برای براده برداری بهتر و راحت است. در نتیجه، آن چه که به برادهبرداری در ماشین کاری سایشی یا همان سنگ زنی کمک میکند، سنگ چرخ مورد استفاده است. در ساخت سنگ چرخ عوامل متعددی اعم از ویژگیهای ساختاری ماده ساینده، جنس مواد سایشی، اندازه دانههای سایشی، مواد چسبنده و خلل و فرج موجود در ساختار سنگ چرخ اهمیت دارند.
سایندههایی که در سنگ چرخ مورد استفاده قرار میگیرند، سختی بالایی داشته و خاصیت گردشوندگی دارند؛ به عبارتی دانههای ساینده قابلیت شکستن به صورت قطعات کوچکتر را دارند. این خاصیت قابلیت تیز شدن خود به خودی را به مواد ساینده اضافه میکند. گردشوندگی زیاد در واقع نشاندهنده استحکام کم و یا مقاومت کم ساینده نسبت به شکست است؛ در نتیجه دانههایی که گردشوندگی زیادی دارند، در مواجهه با نیروهای سنگ زنی، سریعتر از دانههایی که گردشوندگی کمی دارند، خرد میشوند.
انواع مواد سایندههای چرخ سنگ زنی
در چرخ سنگ زنی از سایندههای طبیعی مانند سنباده، یاقوت، کوارتز و الماس استفاده نمیشود؛ زیرا این سایندهها اغلب حاوی مقادیر شناختهشدهای از ناخالصیها میباشند. همچنین خواص غیر یکنواختی داشته و عملکرد آنها با ثبات و قابل اعتماد نخواهد بود. سایندههایی که در فرایند سنگ زنی و فرایند تولید مورد استفاده قرار میگیرند، سایندههای معمولی مانند اکسید آلومینیوم، سیلیکون کارباید و ابرسایندهها مانند برن نیتراید مکعبی و الماس هستند. این سایندهها، بخصوص ابرسایندهها، از مواد ابزار برشکاری معمولی بسیار سختتر هستند.
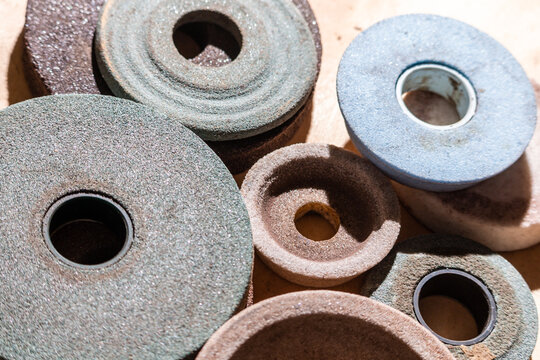
از ماده اکسید آلومینیوم برای اکثر آلیاژهای فولادی در فرایند سنگ زنی استفاده میشود. سیلیکون کارباید نیز غالبا برای سنگ زنی مواد برنجی، آلومینیوم و مس استفاده میشود و نسبت به اکسید آلومینیومها قابلیت گردشوندگی بیشتری دارد؛ بنابراین شکنندگی بیشتری داشته و تیز میماند. برن نیتراید مکعبی نیز از دیگر مواد ساینده است که تنها برای مواد سخت در فرایند سنگ زنی مورد استفاده قرار میگیرد. در برخی موارد نیز الماس در فرایند سنگ زنی به کار میرود؛ اما به دلیل هزینه بالای این ماده، تنها در موارد خاص از آن استفاده میشود.
سایندههایی که در فرایندهای تولید استفاده میشوند،، غالبا در مقایسه با اندازه ابزارهای برش و الماسها، اندازه کوچکتری دارند. سایندهها همچنین دارای لبههای تیزی هستند و به این وسیله مقادیر بسیار کمی بار را از سطح قطعه کار، بر میدارند.
انواع چسب مورد استفاده برای مواد ساینده
چسبهایی که در فرایند سنگ زنی برای چسباندن مواد ساینده مورد استفاده قرار میگیرند غالبا شامل چسبهای شیشهای، رزینی، لاستیکی و فلزی هستند. اغلب این چسبها هم در سنگهای سنتی و هم در ابر سایندهها استفاده میشوند. چسب شیشهای که با نام چسب سرامیکی نیز شناخته میشود، در اصل یک شیشه است و کاربرد بیشتری دارد.
چسبهای رزینی نیز غالبا از رزینهای ترموستینگ ساخته شده و دامنه بسیار وسیعی از ترکیبات و خواص موجود را شامل میشوند. این چسبها یک ترکیب آلی هستند و سنگهایی که در آنها از چسبهای رزینی استفاده میشود، با نام سنگ سنبادههای آلی نیز شناخته میشوند.
چسبهای لاستیکی نسبت به سایر چسبها انعطافپذیری بسیار بیشتری دارند و از آنها میتوان در سنگ سنبادهها استفاده کرد. در چسبهای فلزی نیز از فنون متالوژی پودر استفاده شده و در عمقهای 6 میلیمتر یا کمتر به محیط یک چرخ فلزی چسبانده میشوند.
نحوه سنگ زنی و برداشت براده با استفاده از دانههای ساینده
همانطور که خواندید، در چسبهای ذرات ساینده از انواع مختلف مواد آلی مانند چسب لاستیکی، رزین و مواد غیرآلی مانند خاک رس استفاده میشود. چسبهای معدنی ساختار شیشهای یا متبلور داشته و در کارگاههای خانگی استفاده میشوند؛ در صورتی که چسبهای رزینی غالبا در برش فولاد مورد استفاده قرار میگیرند و در استفاده از آنها نیاز به دقت کار بالا وجود دارد. از چسبهای رزینی نیز برای خشنکاری یا برداشت ماده زیاد مانند ریخته گری استفاده میشود.
چرخهای سنگ زنی، علاوه بر سایندهها و مواد چسباننده، غالبا شامل یکسری عناصر اضافی هستند که منجر به ایجاد حفرههای ریز در چرخ میشوند یا به طور شیمیایی به تیز شدن دانهها کمک میکنند. یکی از ویژگیهای مهم چرخهای سنگ زنی این است که با استفاده از آنها میتوان خلل و فرجهای مختلف و گوناگونی را ایجاد کرد که در ویژگیهای برش چرخ سنگ زنی موثر هستند.
خلل و فرج، فضای آزاد داخل چسب را نشان میدهد که اتاقی برای تراشههای کوچک فلز تراشیده شده و ساینده که در طول فرایند سنگ زنی تولید میشوند، میباشد. این خلل و فرجها همچنین برای حمل مایعاتی که جهت کنترل گرما و بهبود ویژگیهای برش در دانههای ساینده میباشند، مسیر مناسبی محسوب میشوند. بدون تخلخل (خلل و فرج) کافی بین ذرات ساینده، امکان پر شدن چرخ سنگ زنی به وسیله تراشهها وجود داشته و برش درست متوقف میشود.
کاربرد
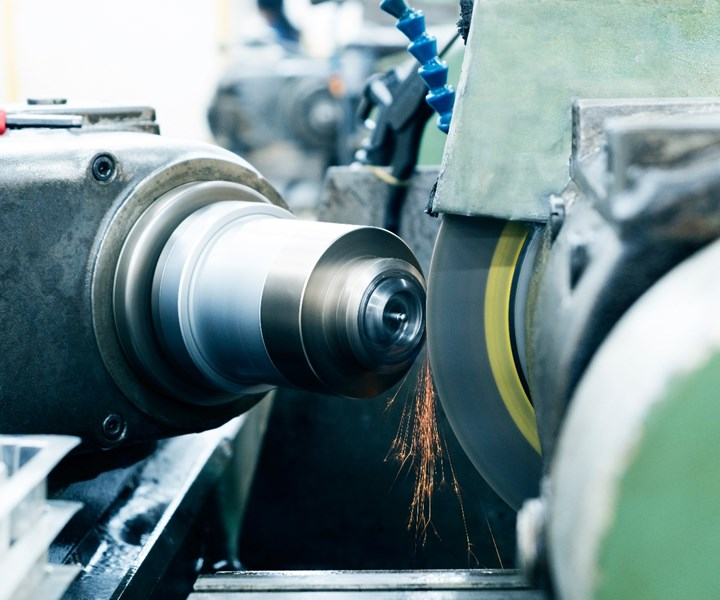
فرایند سنگ زنی به عنوان بخشی از عملیات ماشین کاری مورد استفاده قرار گرفته و به طور موثری فرایند براده برداری قطعه کار را انجام میدهد. در فرایند سنگ زنی با استفاده از سایش مواد و چرخ سنگ زنی میتوان مواد اضافه را از روی قطعه کار برداشت. در دستگاههای سنگ زنی برای ایجاد سطوح صاف از عملیات لایهبرداری روی سطح قطعه کار استفاده میشود. این دستگاهها قابلیت انجام کارهای متفاوت در صنایع مختلف را دارند که از جمله رایجترین کاربردهای آنها میتوان به موارد زیر اشاره کرد:
- صنایع تولیدی: تولید قطعات کار با کیفیت، با ابعاد مورد نیاز و تلورانسهای ضعیف بخصوص در صنایعی مانند خودروسازی، هوا فضا و ماشین ابزار
- صنعت فلزکاری: فرمدهی و تولید قطعات با ابعاد دقیق و سطوح صیقلی و آماده کردن سطوح قطعههای کار برای فرایندهای جوشکاری و پولیش
- ماشین کاریهای دقیق: پرداخت بالا و دقیق قطعات کار برای استحکام بالا و تلورانس بالای قطعات کار به خصوص در صنایعی مانند هوافضا، پزشکی و الکترونیک
- صنعت خودروسازی: تولید قطعاتی مانند میللنگها، چفها، چرخدندهها، روتورهای ترمز، اجزای انتقال و قطعات تزریق سوخت برای رسیدن به عملکرد مناسب، اندازه دقیق و سطوح صیقلی بالا
- صنایع ابزارسازی و قالب سازی: تیزکردن، ترمیم و بازسازی ابزارهای برش مانند متهها، فرزها و قلاویزها برای افزایش عمر ابزارها و داشتن عملکرد بهینه
- صنعت انرژی: تولید قطعاتی مانند توربینها و روتورها و فرمدهی و ساخت دقیق اجزای پیچیده برای تولید بیشترین انرژی و به حداقل رسیدن استهلاکها و هدر رفتهای انرژی
مزایای سنگ زنی
برای براده برداری با ابزارهای فلز تراشی روشهای مختلفی وجود دارد؛ اما غالبا روش سنگ زنی بهترین فرایند برای براده برداری محسوب میشود. این فرایند نسبت به سایر فرایندها مزایای برتری دارد که این مزایا عبارتند از:
- ذراتی که در این فرایند برای ساخت ابزارها مورد استفاده قرار میگیرند، سختی بالایی دارند.
- دستگاه سنگ زنی در اغلب شرایطی که سایر ابزارهای براده برداری قادر به براده برداری قطعات نیستند، بهترین عملکرد را دارند و در این شرایط نیز قابل استفاده میباشند.
- به دلیل کمتر بودن فشار ابزارهای دستگاه سنگ زنی نسبت به سایر ابزارهای فلز تراشی، این سنگها و چرخهای سنباده میتوانند برادههای بسیار ظریفی را از روی سطوح کار حذف کنند. در اینصورت، تغییر فرم زیادی در قطعه کار ایجاد نشده و تاب خوردگیهای ناشی از عملیات آبکاری نیز برطرف خواهند شد.
- به دلیل ابعاد براده برداری بسیار کوچک در ماشینهای این روش، استفاده از این ماشینها دقت بسیار زیادی را به همراه دارد.
- عملیات سنگ زنی به عنوان یک عملیات پرداخت کاری و صیقل کاری نهایی مورد استفاده قرار میگیرد و منجر به ایجاد صافی بسیار با کیفیتی روی قطعه کار میشود.
سوالات متداول
مواد ساینده سنگ زنی چه اثری روی قطعه دارند؟
تاثیر سنباده زنی روی قطعه کار در عملیات سنگ زنی کاملا به شکل مواد ساینده بستگی دارد. اگر در این فرایند از سنگ چرخ با لبههای تیز استفاده شود، سطح قطعه براده برداری خواهد شد. زمانی که دانههای ساینده چرخ سنگ فرسوده شده و یا از بین میروند، شکل ظاهری آنها گرد مانند خواهد بود.
به همین دلیل، در استفاده از آنها، قطعه شخم زده شده و لبههای برنده در قطعه فرو میرود و عمل براده برداری انجام نخواهد شد. همچنین در صورتی که لبههای ماده ساینده به طور کامل از بین رفته باشد، براده برداری انجام نمیشود. استفاده از دانههای ساینده تنها منجر به سایش سطح قطعه خواهد شد.
اندازه دانههای سایشی در چرخ سنگ چقدر است؟
دانههای ساینده مورد استفاده در فرایند سنگ زنی در ابعاد متفاوتی ساخته میشوند. یکی از مهمترین ویژگیها برای انتخاب این دانهها، توجه به اندازه آنها در کنار توجه به میزان صافی سطح است. در واقع، هرچه سطح صافتر باشد، باید از دانههای کوچکتری استفاده کرد. در صورتی که دانههایی با ابعاد بزرگتر استفاده شوند، میزان صافی سطح کمتر خواهد بود و در کنار آن حجم برادههای ایجاد شده نیز بیشتر میشود. این دانهها، زمانی مورد استفاده قرار میگیرند که کاهش ضخامت سطح اهمیت داشته باشد.
سنگ زنی چه تفاوتی با ماشین کاری دارد؟
این روش غالبا به عنوان یکی از مراحل ماشین کاری قطعات شناخته می شود. دانههای ساینده مورد استفاده در فرایند سنگ زنی، شکلهای غیز منظم دارند و به طور نامنظمی در اطراف سنگ قرار میگیرند. زاویه شیب متوسط این دانهها نیز منفی است و برادههای سنگ زنی، نسبت به سایر فرایندهای براده برداری ماشین کاری، تغییر شکل بیشتری را غالبا شامل میشوند. همچنین در آن سرعت برشکاری بسیار بالاتر از سایر فرایندهای ماشین کاری بوده و غالبا در حدود 30 میلیمتر بر ثانیه است.
چگونه میتوان سنگ سنباده را برای فرایند سنگ زنی انتخاب کرد؟
نوع سنگ سنباده مورد استفاده در فرایند سنگ زنی، روی کیفیت سطوح ایجاد شده و اقتصادی بودن عملیات، بسیار تاثیرگذار است. انتخاب این سنگ علاوه بر اینکه به شکل سنگ بستگی دارد، به شکل قطعه تولیدی و خواص ماده نیز وابسته است. در نتیجه خواص فیزیکی و مکانیکی جنس قطعه کار روی انتخاب نوع ساینده موثر هستند.
جمع بندی
همانطور که خواندید، روش سنگ زنی یکی از فرایندهای اساسی براده برداری و پرداخت قطعات کار است که غالبا به افزایش استقامت آنها نیز کمک میکند. در ماشینهای سنگ زنی، از چرخهای ساینده و سمباده برای شکلدهی و صیقل کاری سطوح و همچنین برای ترمیم ابزارها استفاده میشود تا کیفیت قطعات افزایش یابد.
انواع دستگاه سنگ زنی اجزای مختلفی دارند که استفاده صحیح از آنها باعث میشود که بهرهوری این ماشینها افزایش پیدا کرده و در کنار آن، ایمنی دستگاه نیز هنگام عملیات سنگ زنی افزایش مییابد. در نتیجه، با استفاده از ماشینهای سنگ زنی میتوان بهرهوری و کیفیت محصولات را افزایش داد.