ریخته گری یکی از روشهای متداول برای ساخت قطعات فلزی است که با استفاده از فرآیندهای مختلفی انجام میشود. یکی از این فرایندها، فرایند ریخته گری ریژه یا ریخته گری ثقلی است که با استفاده از قالب ریژه انجام میشود.
اگر میخواهید با ریخته گری ثقلی، ویژگیها، نحوه عملکرد و کاربردش بیشتر آشنا شوید، مطالعه این مقاله را از دست ندهید.
ریخته گری ثقلی چیست؟
ریخته گری ثقلی یا ریخته گری ریژه (Gravity Casting) یکی از روشهای متداول ریخته گری است که برای تولید قطعات مختلف فلزی و غیرفلزی در صنایع متفاوت مورد استفاده قرار میگیرد. این روش یکی از قدیمیترین فرایندهای شناخته شده ریخته گری میباشد که برای ساخت فلزات و آلیاژهای فلز به کار گرفته میشود.
در فرایند ریخته گری ثقلی فلز مذاب به وسیله وزن خود و نیروی گرانش زمین به درون قالب هدایت میشود. در واقع در این روش گازهای تحت فشار، وکیوم یا نیروی گریز از مرکز برای هدایت فلز مذاب به درون قالب به کار نمیروند. فرایند این روش تقریبا مشابه با روش ریخته گری ماسهای و ریخته گری دایکاست است؛ با این تفاوت که قالبهایی ک در این روش مورد استفاده قرار میگیرند، دائمی و از جنس فلز هستند و به عبارتی قابل استفاده مجدد میباشند.
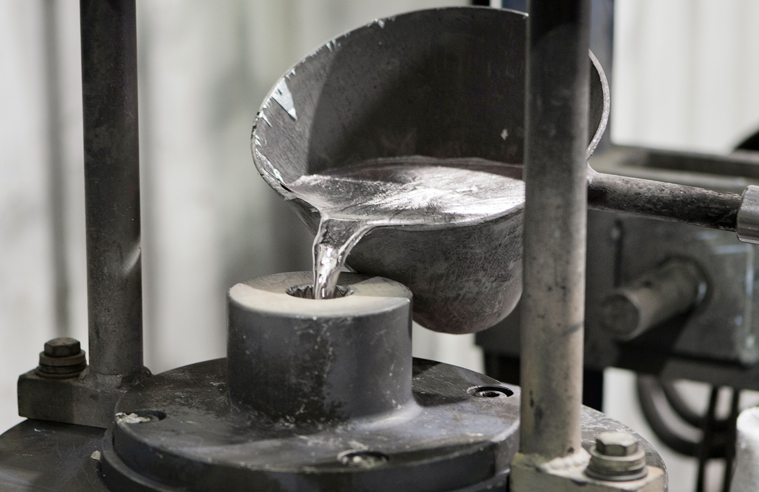
این قالبها در دمای بالا خراب نمیشوند، به سادگی تغییر شکل نمیدهند و کاملا در دسترس هستند. برای ریخته گری ریژه غالبا از قالبهایی با مقیاس کوچک استفاده میشود.
ریخته گری ریژهای غالبا برای تولید قطعات آلیاژی غیر آهنی اعم از آلیاژهای پایه مانند آلومینیوم، روی و مس مورد استفاده قرار میگیرد. این فرایند انجماد سریعتری داشته و به همین دلیل قطعات تولید شده با این روش سطح بهتر و خواص مکانیکی بهتری نسبت به اغلب روشهای ریخته گری بخصوص روش ریخته گری ماسهای دارند. همچنین فرایند ریخته گری ریژه ای سرعت بیشتری دارد. گرچه در این روش هزینه نهایی تولید محصول به دلیل استفاده از قالبهای فلزی، نسبت به ریخته گری شن و ماسه بالاتر است.
از ویژگیهای مهم این روش میتوان به ساده بودن فرایند آن، تخلخل کم گاز و اندازههای ریز دانه اشاره کرد.
انواع روشهای ریخته گری ثقلی
براساس نوع تجهیزات مورد استفاده، قطعه مورد نیاز، در ریخته گری ثقلی با استفاده از روشهای مختلفی تولید میشود؛ که این روشها عبارتند از:
- روش دستی
در این روش، تمامی مراحل ریخته گری به صورت دستی و بدون استفاده از دستگاه انجام میشوند. این روش بیشتر برای تولید قطعات ساده و با ضخامت کم یا ضخامت خیلی زیاد و قطعات با شکل هندسی ساده کاربرد دارد. با استفاده از این روش میتوان قطعات ضخیم با برآمدگیهای زیاد را به سادگی تولید کرد.
- روش نیمه اتوماتیک
در این روش، فرایند باز و بسته کردن قالب با استفاده از سیستمهای هیدرولیکی انجام میشود و این مرحله از فرایند ریخته گری نیاز به نیروی انسانی نخواهد داشت. اما پر کردن قالب و خروج قطعات از قالب ریژه توسط نیروی انسانی انجام خواهد شد. از روش نیمه اتوماتیک میتوان برای تولید قطعات در تعداد انبوه استفاده کرد.
- روش اتوماتیک
در این روش، تمامی مراحل ریخته گری اعم از ریختن مواد مذاب به درون قالب، بستن قالب، انجماد و خروج قطعه به صورت خودکار و توسط دستگاه انجام میشود. سرعت و دقت انجام مراحل در این روش بیشتر است. همچنین در روش اتوماتیک امکان تولید قطعات بیشتر با ابعاد مختلف به سادگی فراهم است و به دلیل استفاده از دستگاه احتمال بروز خطا کاهش پیدا میکند.
انواع مواد قالب ریخته گری ثقلی یا ریژه
ریخته گری در قالبهای ریژه غالبا به وسیله آلیاژهای غیر آهنی انجام میشود. هر فلزی که در این قالبها مورد استفاده قرار میگیرد، مزایا و معایب خاص خود را داشته و بسته به ویژگیهای قطعه مورد نظر، کاربرد خود را دارند.
Everything You Need to Know About Gravity Die Casting Mould Material
مواد قالب ریخته گری گرانشی یک آلیاژ فلزی است که برای فرآیندهای تولید صنعتی استفاده می شود. برای تشکیل اجزا و قطعات با اشکال پیچیده و دقت بالا استفاده می شود. انواع مختلفی از مواد قالب ریخته گری گرانشی وجود دارد، مانند آلیاژهای آلومینیوم، روی، منیزیم و مس. هر نوع ماده مزایا و معایب خاص خود را دارد و باید با توجه به کاربرد انتخاب شود.
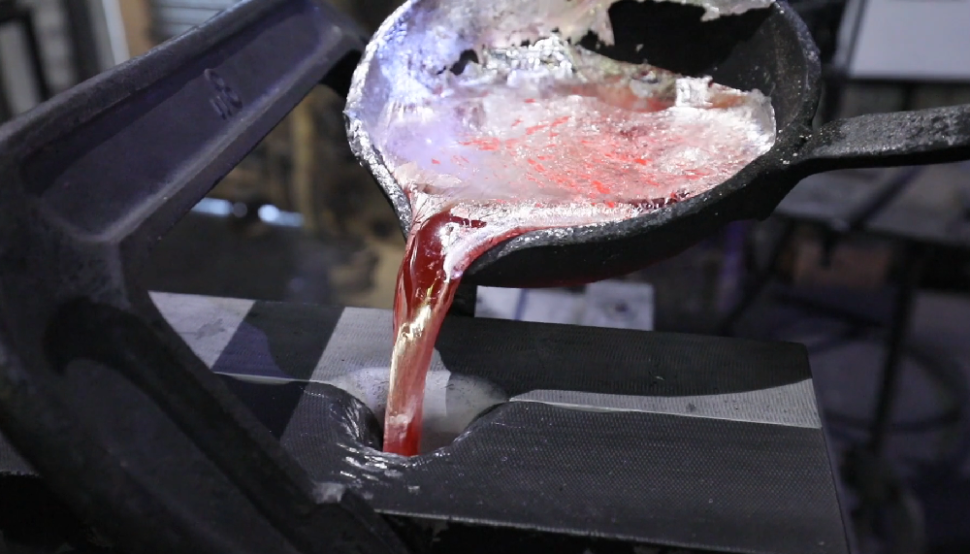
انواع مواد پرکاربرد و مورد استفاده در قالب ریخته گری ثقلی یا ریژه عبارتند از:
- آلیاژهای آلومینیوم: این آلیاژها نقطه ذوب بالایی دارند و در برابر خوردگی بسیار مقاوم میباشند. همچنین از رسانایی حرارتی و الکتریکی مطلوبی برخوردار هستند. قطعاتی که توسط آلیاژهای آلومینیوم تولید میشوند میتوانند تا 70 کیلوگرم وزن داشته باشند. از جمله قطعاتی که با استفاده از این آلیاژها در فرایند ریخته گری ریژهای تولید میشوند میتوان به بدنه موتور با ضخامت کم اشاره کرد.
- آلیاژهای منیزیم: این آلیاژها سبک وزن هستند اما نسبت به وزنی که دارند، دارای استحکام خوبی میباشند. از آلیاژهای منیزیم در مواردی استفاده میشود که نیاز به تولید قطعات و ابزارهایی با وزن سبکتر وجود دارد. میانگین وزن قطعات تولید شده با استفاده از این آلیاژها در قالبهای ریژه، حدودا 10 کیلوگرم است.
- آلیاژهای مس: این آلیاژها دامنه گستردهای آلیاژهای مختلف اعم از آلیاژهای برنج دارند که برای ریخته گری در قالبهای ریژهای مناسب میباشند. قطعاتی که با استفاده از آلیاژهای مس در قالبهای ریژه ساخته میشوند رسانایی حرارتی و الکتریکی مطلوبی داشته و در برابر خوردگی مقاوم میباشند. تنها نکته مورد توجه در استفاده از مس توجه به سرعت انجماد بالای آن است که پس از ریخته گری باید به سرعت از قالب جدا شوند. قطعاتی که با استفاده از این آلیاژ در ریخته گری ریژهای ساخته میشوند، غالبا وزنی کمتر از 10 کیلوگرم دارند.
- آلیاژهای روی: این آلیاژها شکلپذیری و انعطافپذیری بسیار خوبی دارند و به همین دلیل استفاده از آنها در تولید قطعات با اشکال پیچیده بسیار کاربرد دارد. آلیاژهای روی همچنین در برابر خوردگی بسیار مقاومت داشته و نسبت به سایر فلزات، غالبا کم هزینهتر هستند.
- چدن خاکستری: از چدن خاکستری هیپویوتکتیک نیز در برخی موارد برای تولید قطعه در قالب ریژه استفاده میشود. اما هزینه طراحی با استفاده از این چدنها بالا بوده و سرعت انجماد بخصوص برای قطعات بزرگ بسیار کمتر است.
فاکتورهای مهم در انتخاب مواد قالب ریخته گری ثقلی
انتخاب مواد بی کیفیت در ریخته گری ریژه میتواند منجر به تولید محصولات و قطعات بیکیفیت شود. به همین دلیل در انتخاب مواد مورد استفاده، توجه به موارد زیر اهمیت دارد:
- حفظ دمای قالب: در ریخته گری ریژه اگر قالب در دمای مناسب نگهداری نشود، محصول تولید شده کیفیت لازم را نخواهد داشت.
- تمیز کردن قالب: در صورتی که قالب به درستی و با دقت تمیز نشود، محصول نهایی تولید شده دارای نقص بوده و همچنین عمر و دوام قالب نیز کاهش پیدا میکند.
- بازرسی قالب: قالب باید به طور منظم بررسی شده و عیوب احتمالی آن برطرف شود؛ در غیر اینصورت قطعه تولید شده در این قالب، دارای کیفیت مطلوب و دوام طولانی مدت نخواهد بود.
مراحل و فرایند ریخته گری ثقلی
همانطور که خواندید، ریخته گری در قالبهای ریژه، به روشهای مختلفی انجام میشود. در اغلب موارد، این فرایند به صورت دستی انجام شده و فلز مذاب با استفاده از ملاقه به قالب افزوده میشود. در این فرایند، میتوان با کج کردن قالب سرعت و جهت پر شدن آن را کنترل کرد. گرچه در برخی از کاربردهایی که نیاز به تولید قطعات در حجم بالا وجود دارد، میتوان از فرایند اتوماتیک یا نیمه اتوماتیک نیز برای ریخته گری استفاده کرد.
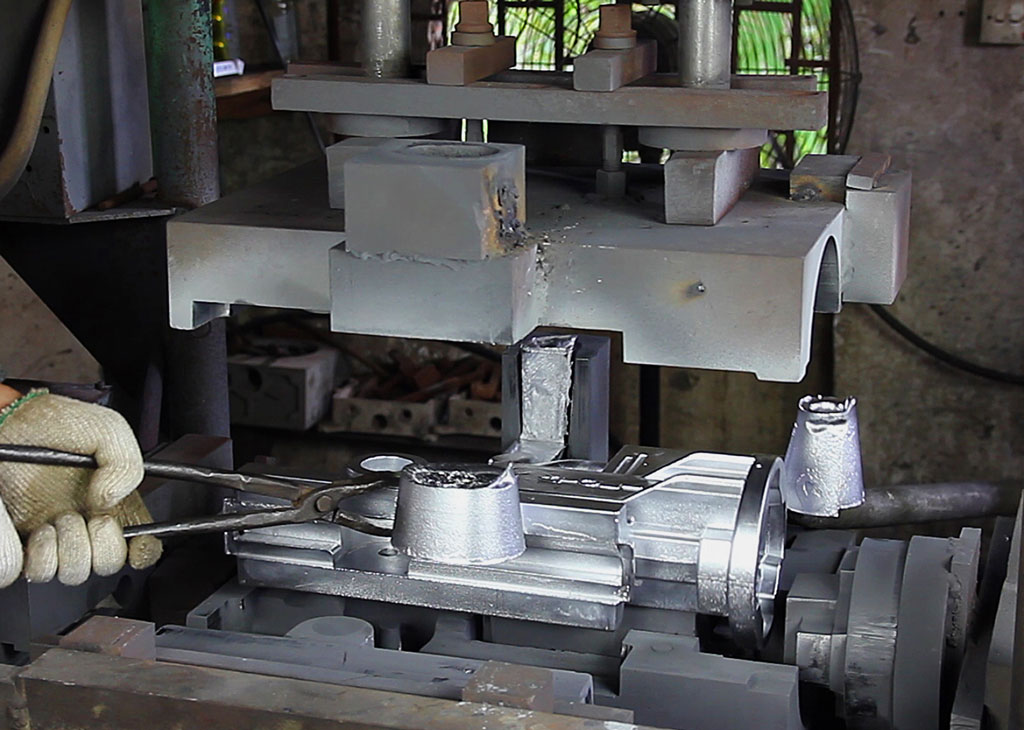
در فرایند ریخته گری، فلز مذاب درون حفره قالب ریخته شده و مواد توسط نیروی جاذبه به قالب وارد میشوند. فرایند اصلی ریخته گری در قالبهای ریژه شامل مراحل اصلی زیر میباشد:
- آماده سازی قالب
همانند تمامی فرایندهای ریخته گری، قبل از شروع فرایند و در ابتداییترین مرحله، قالب ریخته گری آماده میشود. برای این منظور پس از طراحی و ساخت قالب، قالب داغ شده و با پوشش نسوز پوشیده و بسته میشود. پوشش مورد استفاده در قالب به کنترل دمای قالب هم در هنگام ریخته گری و هم در زمان خروج قطعه پس از ساخت کمک میکند.
سیستم راهگاهی که میتواند در بالا، کنار و یا پایین قالب باشد، باید با دقت طراحی شود؛ زیرا به صورت مستقیم روی تلاطم و عملکرد فلز تاثیرگذار است. همچنین اندازه قالب باید به اندازه کافی بزرگ باشد تا راهگاه و رایزر به خوبی درون آن جای گرفته و حتی در حدود 75 تا 200 میلیمتر از بالای قالب فاصله داشته باشند. قالب ریخته گری ریژه غالبا از 2 یا تعدادی قطعه فلزی ساخته میشود که به وسیله گیره، پیچ و… به یکدیگر متصل میشوند. این قالب دائمی بوده و برای تولید قطعات با تعداد زیاد و به صورت مستمر مورد استفاده قرار میگیرد.
- ریخته گری فلز مذاب
پس از آماده شدن قالب، فلز مذاب به صورت دستی و یا با استفاده از دستگاه در قالب ریخته میشود. در ریخته گری ثقلی، فلز آهستهتر از ریخته گری تحت فشار به درون قالب ریخته میشود، به همین دلیل تلاطم فرایند کمتر شده و قطعه ریخته گری شده متراکمتر خواهد بود.
ریخته گری در قالب ریژه براساس وزن یا نیروی ثقل مذاب انجام میشود و برای ورود مواد مذاب به درون قالب هیچگونه نیروی خارجی مورد استفاده قرار نمیگیرد. در واقع، عامل موثر در پر شدن قالب، فشار حاصل از اختلاف ارتفاع دهانه بارریزی و محفظه قالب میباشد و به همین دلیل این روش با نام ریخته گری ثقلی نیز شناخته میشود.
قالب مورد استفاده، قبل از فرایند گرم شده و درجه حرارت آن کنترل میشود تا در ویسکوزیته مذاب تاثیر مخرب نداشته باشد. در این مرحله، پس از ریختن فلز مذاب باید مدت زمانی صبر کرد تا فلز کاملا سرد شده و حالت جامد به خود بگیرد.
معمولا برای ریخته گری قطعات کوچک از فرایند خودکار ریخته گری ثقلی استفاده میشود، تا در طول ریختن مذاب، قالب کنترل شده و تلاطم به حداقل برسد.
- خارج کردن قطعه از درون قالب
پس از انجماد کامل قطعه، قالب باز شده و قطعه ریخته گری شده از درون قالب خارج میشود. خارج کردن قطعه ممکن است توسط دست یا در برخی مواد توسط پینهای اجکتور در دستگاههای مکانیزه انجام شود. معمولا قالبهای بزرگی که برای آلیاژهای آلومینیوم و منیزیم مورد استفاده قرار میگیرند، با استفاده از دست مونتاژ و جدا میشوند؛ اما خارج کردن قالبهای کوچک به ویژه قالبهای آهنی به صورت خودکار انجام میشود.
- پرداخت نهایی قطعه
در مرحله نهایی، قسمتهای اضافی قطعه ریخته گری شده در قالبهای ریژه، حذف میشوند. پس از آن قطعه تولید شده پرداخت میشود تا لبههای تیز و مواد اضافی احتمالی از بین بروند. بسته به طراحی سیستم راهگاهی فرایند این نوع ریخته گری بین 40 تا 60 درصد بازده دارد.
در فرایند ریخته گری ریژه ، نرخ تولید کاملا به طراحی و اندازه قطعه و همچنین مواد مورد استفاده بستگی دارد. معمولا برای سرسیلندرهای آلومینیومی نرخ تولید یک در هر 5 دقیقه است. در صورت استفاده از روش اتوماتیک، اغلب ریخته گریهای آهنی ک طراحی ساده و کوچکی دارند، نرخ تولید بالایی را در روش ریخته گری ثقلی شامل میشوند.
کاربرد ریخته گری ثقلی
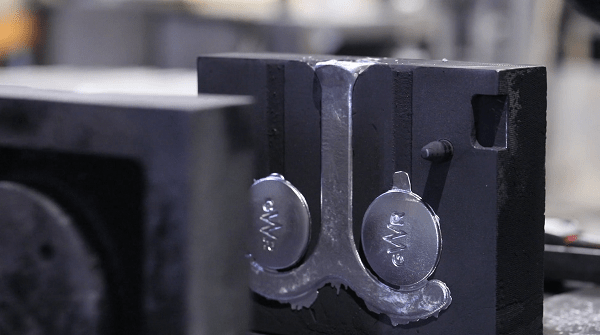
ریخته گری ثقلی یا ریخته گری ریژه برای تولید قطعات گوناگون در صنایع مختلف مورد استفاده قرار میگیرد؛ که برخی از مهمترین آنها عبارتند از:
- صنعت خودروسازی برای تولید قطعات خودرو مانند پیستون، سرسیلندر، کالیپر ترمز، توربو، بلوک موتور
- موتورهای دیزلی با اسب بخار بالا
- توربینهای گازی
- کمپرسورها
- پمپها
- تجهیزات پزشکی
- چاپ عکس و تصویر برداری
- تجهیزات روشنایی
- وسایل آشپزخانه و شیرآلات
- تجهیزات سازههای ساختمانی
- صنایع دفاعی
- کامیونهای مفصلی
قطعات و ابزارهایی که توسط این روش ساخته میشوند بسیار باکیفیت هستند و اگر به درستی و با مهارت بالا ریخته گری شوند، دوام طولانی مدتی خواهند داشت.
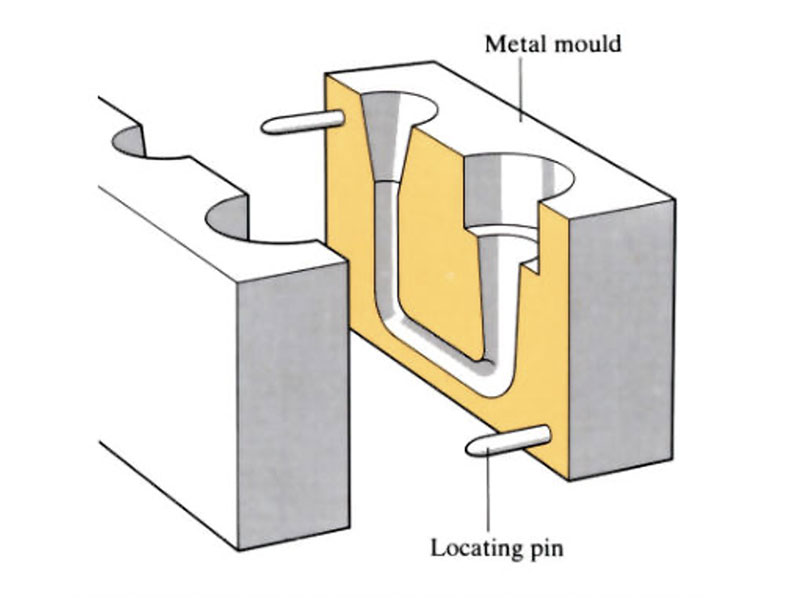
مزایا و معایب ریخته گری ثقلی
ریخته گری ریژه مزایا و ویژگیهای زیادی دارد که برخی از مهمترین آنها عبارتند از:
- این روش سرعت تولید قطعه را بخصوص با استفاده از فرایند اتوماتیک افزایش میدهد.
- در این روش میتوان قطعات را در تیراژ بالا با استفاده از قالب دائمی ریژه تولید کرد.
- قطعاتی که با استفاده از این روش ساخته میشوند، دقت ابعادی خوبی دارند.
- سطح قطعه تولید شده نیز دارای کیفیت بالایی خواهد بود.
- قطعاتی که با استفاده از این روش تولید میشوند، از کیفیت متالورژیکی بالایی برخوردار میباشند.
- قطعه تولید شده استحکام و مقاومت بالایی داشته و خواص فیزیکی و مکانیکی مطلوبی نیز دارد.
- هزینه تولید قطعات در این روش نسبت به اغلب سایر روشها مناسبتر است.
- به دلیل ثابت بودن ابعاد و زوایای قالب مورد استفاده، این روش از دقت بالایی برخوردار است.
- این روش شرایط زیست محیطی مطلوبی داشته و هیچگونه آسیبی برای محیط زیست ندارد.
- قطعات تولید شده در این روش تخلخل کمتری داشته و نسبت به ریخته گری ماسهای ساختار دانهای بهتری دارند.
- امکان تولید قطعات با ابعاد کوچک و نازک در این روش به سادگی فراهم است.
در کنار تمامی این مزایا، ریخته گری ثقلی یکسری معایب را نیز شامل میشود؛ که این معایب عبارتند از:
- هزینه طراحی و ساخت قالب ریژه بالا است و به همین دلیل برای تولید قطعات در تعداد کم این روش صرفه اقتصادی ندارد.
- با استفاده از این روش نمیتوان تمامی فلزات و آلیاژها را ریخته گری کرد.
- در این روش برای افزایش عمر قالب باید از پوششهایی مانند سیلیکات سدیم، گل نسوز، اکسید فلزی و… استفاده کرد.
- امکان تولید قطعات با اشکال پیچیده در این روش وجود ندارد؛ زیرا این روش بر اساس نیروی ثقل و ویسکوزیته مذاب عمل میکند.
- تولید قطعات با ابعاد بزرگ در این روش غیر ممکن است؛ زیرا ساخت قالب این قطعات هزینه زیادی به همراه دارد.
سوالات متداول
چه عواملی در کیفیت قطعه تولید شده در فرایند ریخته گری ثقلی تاثیرگذار هستند؟
در این روش، عوامل مهمی اعم از دمای قالب، دمای مذاب، ضخامت پوشش قالب و ضخامت دیواره قالب روی کیفیت نهایی قطعه تولید شده تاثیر قابل توجهی دارند.
آیا ریخته گری ثقلی برای تولید انبوه مناسب است؟
این روش ریخته گری نسبت به اغلب سایر روشهای ریخته گری کم هزینه تر است و برای انجام آن نیاز به ابزار و روشهای سادهتری وجود دارد. در نتیجه، این روش از مناسبترین روشها برای تولید قطعات در تعداد انبوه محسوب میشود. همچنین به دلیل اینکه در این روش از قالبهای دائمی استفاده میشود، استفاده از آن برای تولید قطعات در تعداد کم به صرفه نمیباشد؛ زیرا هزینه ساخت قالب هزینه قابل توجهی است.
چه عواملی در افزایش طول عمر قالبهای ریژه تاثیرگذار هستند؟
روی دوام قالبهای ریژه عوامل زیادی تاثیر میگذارند. از جمله مهمترین آنها میتوان به جنس قالب و تعداد دفعات ریخته گری در آن قالب اشاره کرد. همچنین درجه حرارت مواد مذاب در حین بارریزی، وزن قطعه فلزی، ضخامت قطعه، روش خنک کردن قطعه و قالب، پوششدهی قالب ریژه، روش محافظت از قالب و روش تمیزکاری قالب از دیگر عوامل تاثیرگذار در دوام قالبهای ریژه هستند.
چگونه میتوان جنس مناسبی برای قالب ریژه انتخاب کرد؟
جنس قالب در کیفیت قطعه ریخته گری شده بسیار تاثیرگذار است. در انتخاب جنس قالب عوامل مهمی اعم از درجه حرارت مذاب، ابعاد قطعه مورد نیاز، ظرفیت حدودی تولید و هزینه تولید باید مورد بررسی قرار بگیرند.
ریخته گری ثقلی چه تفاوتی با سایر ریخته گریها دارد؟
در این روش، ریخته گری در قالب مورد استفاده بر اساس وزن یا نیروی ثقل انجام میشود و نیروی خارجی برای ورود مذاب به درون قالب وجود ندارد. در نتیجه، تنها تفاوت این روش با سایر ریخته گریها اعم از ریخته گری قالبهای ماسهای و موقت این است که در آنها از فشار خارجی استفاده شده و از وزن یا فشار مواد مذاب برای ریخته گری استفاده نمیشود.
جمع بندی
یکی از فرایندهای ریخته گری، ریخته گری ثقلی است که با نام ریخته گری ریژه نیز شناخته میشود. در این روش، مواد مذاب تحت نیروی جاذبه و بدون استفاده از هیچگونه نیروی خارجی به درون قالب وارد میشوند. قالبهایی که در این فرایند مورد استفاده قرار میگیرند، از نوع قالبهای دائمی هستند که قابلیت استفاده مجدد دارند. استفاده از این قالبها همچنین باعث افزایش سرعت و کاهش زمان تولید میشوند. قطعاتی که با استفاده ریخته گری ریژه تولید میشوند دارای دقت ابعادی بالا، پرداخت سطحی مطلوب و هزینه ی کم هستند و به همین دلیل این روش در تولید قطعات در صنایع مختلف بسیار کاربرد دارد.
برای دریافت اطلاعات بیشتر و دریافت خدمات ایده تا اجرا ساخت انواع قطعات با گروه فبرینو تماس بگیرید و از تخصص این گروه برای ساخت انواع قطعات بهره مند شوید.