فرایند تغییر شکل از مهمترین فرایندهایی است روی مواد مختلف انجام شده و در هر ماده روشهای مخصوص به خود را دارد. تغییر شکل ماده میتواند به صورت شیمیایی یا فیزیکی انجام شود. به عنوان مثال، ورق روغنی از سنگ آهن ساخته میشود. برای این منظور سنگ آهن طی یکسری مراحل شیمیایی و فیزیکی مختلف و با اعمال حرارت و اعمال فشار، تغییر شکل میدهد. اعمال فشار یا حرارت نیز در فرایندهای تغییر شکل مواد به شکلهای مختلفی انجام میشود. اکستروژن یکی از فرایندهایی است که با استفاده از آن، فلزات از طریق دهانه قالب و تحت فشار سیلان مییابد تا بدین وسیله شکل مقطع مورد نظر ایجاد شود. اکستروژن از فرایندهای بسیار بهینه است که باعث کاهش هزینهها میشود.
اگر میخواهید با فرایند اکستروژن، ویژگیها و کاربردهای دستگاه اکستروژن و روش اکستروژن مستقیم و اکستروژن معکوس بیشتر آشنا شوید، مطالعه این مقاله از فبرینو را از دست ندهید. فبرینو یکی از برترین اجرا کننده های پروژه های صنعتی است که از طراحی تا اجرا همراه شما است و در انجام یک پروژه عالی به شما کمک خواهد کرد. از نمونه کارهای ما دیدن کنید و در صورت تمایل با متخصصین ما برای مشاوره بیشتر تماس بگیرید.
اکستروژن چیست؟
اکستروژن (Extrusion) یا روزن رانی، یکی از فرایندهای جدید تغییر شکل مواد است که به طور گسترده، برای فلزات مورد استفاده قرار میگیرد. در این فرایند شمش فلزی از طریق اعمال فشار از قالب مخصوصی عبور داده شده، فرم داده میشود و دچار تغییر شکل خواهد شد. نیروی مورد نیاز برای انجام فرایند اکستروژن به صورت هیدرولیکی یا مکانیکی تامین میشود. امروزه برای انجام این فرایند از روشهای مختلفی در کارخانههای تولیدی استفاده میشود که از رایجترین این روشها میتوان اکستروژن مستقیم و اکستروژن معکوس اشاره کرد.
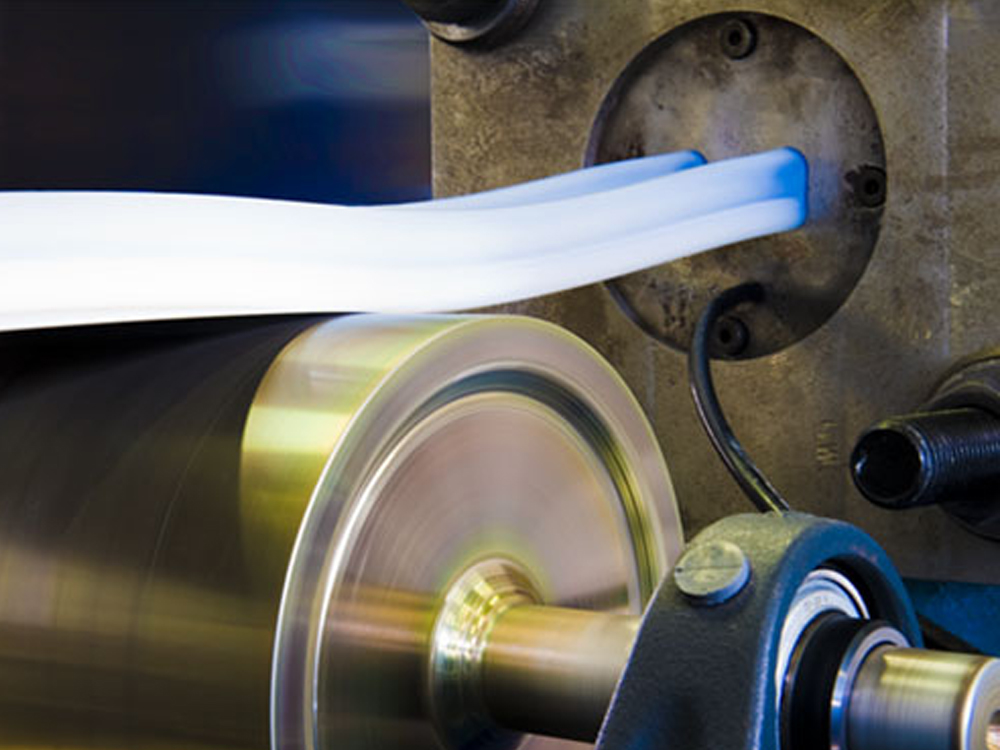
از جمله مزیتهای برتر این فرایند نسبت به سایر فرایندهای شکلدهی مواد، قابلیت تولید قطعات با سطح مقطع پیچیده و همچنین صرفهجویی در زمان و هزینه فرایند است. قطعاتی که با استفاده از این فرایند شکل میگیرند دارای سطح مقطع با کیفیت و صافی هستند و همچنین استحکام بالایی را شامل میشوند. این مزیتها غالبا به این دلیل است که در فرایند اکستروژن، ماده مورد استفاده تحت فشار و تنش برشی قرار گرفته و تحت عملیاتهای مخرب قرار نمیگیرد.
فرایند اکستروژن در طول زمان، پیشرفتهای زیادی داشته است و امروزه یکی از فرایندهای مهم و کاربردی شکلدهی مواد و بخصوص مواد فلزی محسوب میشود؛ تا جایی که امروزه اغلب صنایع بسته به نیازهای خود از این فرایند برای تولید قطعات مختلف استفاده میکنند. حتی امکان تولید اشکال پیچیدهتر نیز توسط این فرایند فراهم است. اکستروژن فلزات میتواند برای فلزات، عناصر غیر فلزی و آلیاژهایی مانند آلومینیوم، مس، سرب، منیزیم، کربن، فولاد و استنلس استیل استفاده شود.
فرایند انواع اکستروژن
همانطور که در بالاتر نیز اشاره شد، کاربرد غالب این روش برای شکلدهی فلزات است. فرایند شکلدهی فلزات با این روش انواع مختلفی داشته و با روشهای مختلفی انجام میشود که در ادامه به آنها اشاره شده است. اما در حالت کلی یکسری تکنیکها و مراحل مهم در تمامیروشهای این فرایند مورد استفاده قرار میگیرند؛ که عبارتند از:
- آمادهسازی بیلت: در این مرحله که مرحله ابتدایی اکستروژن است یک بیلت فلزی انتخاب و آمادهسازی میشود. این بیلت فلزی نیز غالبا بلوکی استوانهای از فلز است. در این مرحله همچنین تعیین دما، اندازه و ترکیب آلیاژ بیلت نیز عوامل بسیار مهمی هستند که باید با دقت تعیین شده و روی نتیجه اکستروژن تاثیرگذار میباشند.
- طراحی قالب: شکل نهایی فلز اکسترود شده در این مرحله تعیین میشود. برای این منظور یک قالب طراحی شده و غالبا توسط فولاد ابزار ساخته میشود تا بتواند در برابر فشار و دمای بالا مقاومت داشته باشد. قالب طراحی شده بسته به خروجی مورد نیاز میتواند دارای شکلی ساده یا پیچیده باشد و در طرحهای مختلفی ساخته شود.
- پرس اکستروژن: مهمترین مرحله در فرایند اکستروژن، انجام پرس اکستروژن است. در این مرحله، بیلت یا شمش فلز درون یک محفظه قرار گرفته و با استفاده از یک پیستون به آن فشار وارد میشود. با این کار، بیلت به قالب فشرده شده و از آن عبور میکند. در اینصورت شکل قالب را به خود گرفته و مشابه با قطعه مورد نیاز تولید میشود.
- کنترل دما: دمای فرایند اکستروژن بسته به نوع اکستروژن مورد استفاده تنظیم میشود. در صورتی که دما به صورت مناسب کنترل نشود احتمال بروز مشکلاتی مانند ترک خوردن قطعه یا تغییر شکل اضافی آن در طول فرایند وجود دارد.
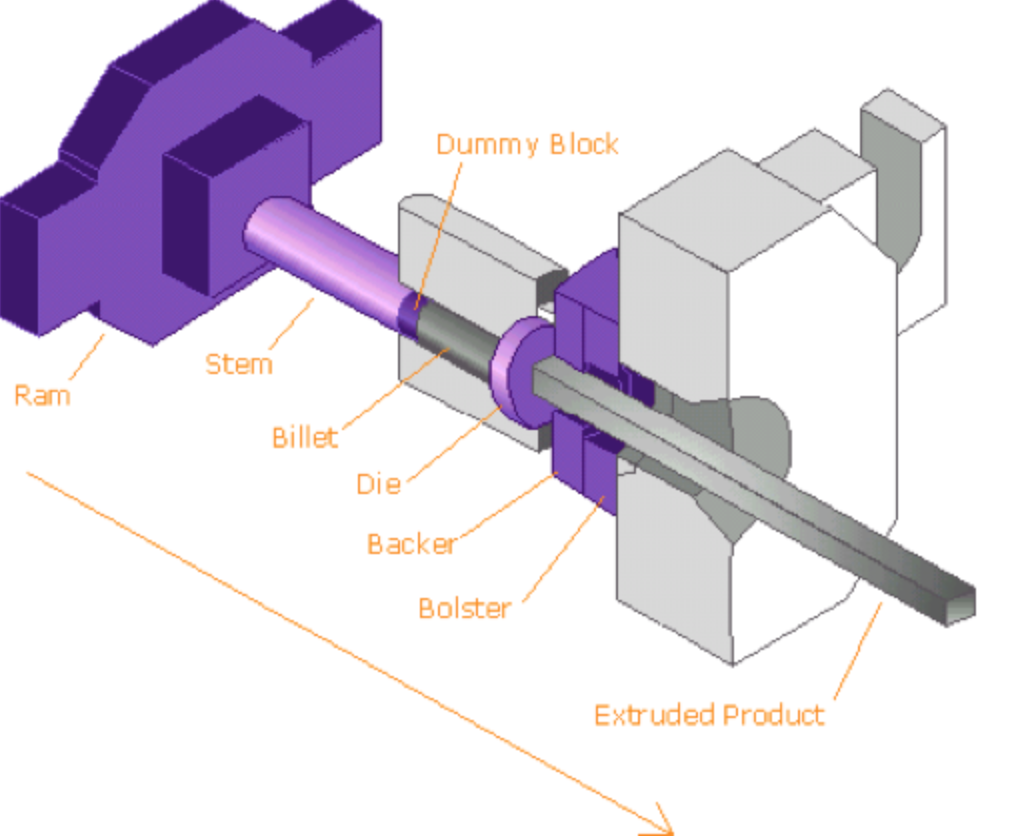
انواع روشهای اکستروژن
به طور کلی، اکستروژن فلزات در دو حالت سرد و گرم انجام میشود. برای این حالتها نیز انواع روشهای مختلفی وجود دارند؛ که عبارتند از:
- اکستروژن مستقیم (Direct Extrusion)
- اکستروژن معکوس (Indirect Extrusion)
- اکستروژن ضربه ای (Impact Extrusion)
- اکستروژن هیدرواستاتیک (Hydrostatic Extrusion)
- اکستروژن عمودی یا جانبی (Lateral Extrusion)
در میان این روشها، روشهای اکستروژن مستقیم و اکستروژن معکوس هم در حالت گرم و هم در حالت سرد کاربرد دارند. روشهای اکستروژن ضربهای و هیدرواستاتیک غالبا تنها در حالت سرد اکستروژن و روش اکستروژن جانبی نیز تنها در حالت گرم اکستروژن انجام میشوند. در ادامه، هر یک از این فرایندهای اکستروژن با جزئیات بیشتری معرفی شدهاند.
- اکستروژن گرم
در این روش اکستروژن، قبل از انجام عملیات برش، بیلت یا شمش مورد استفاده گرم میشود تا قابلیت شکلپذیری آن افزایش پیدا کند. پس از آن، توسط پیستون دستگاه پرس، به بیلت فشار وارد میشود تا از قالب عبور کرده و شکل مورد نیاز را به خود بگیرد. از نظر علمی، از طریق اکستروژن گرم میتوان شکلهای خاصی را با استفاده از مقاطع مختلف فولاد در قالبهای مخصوص ایجاد کرد.
روش اکستروژن گرم بیشتر برای تولید محصولات فلزی با طول زیاد و مقطعی با اشکال پیچیده و ثابت مناسب است. همچنین از آن برای ساخت پروفیلهای توپر و تو خالی نیز استفاده میشود. در این میان، توجه به این نکته نیز ضرورت دارد که در این فرایند برای استفاده از مواد مختلف، نیاز به کنترل دماهای متفاوتی وجود دارد و نمیتوان تمامی مواد مختلف را با یک دمای یکسان اکسترود کرد؛
به عنوان مثال، برای آلیاژهای فولاد دمای مناسب بین 1200 تا 1300 درجه، برای سرب دمای مناسب بین 200 الی 250 درجه، برای آلیاژهای نسوز دمای مناسب بین 220 تا 975 درجه، برای منیزیم دمای مناسب بین 350 تا 425 درجه و همچنین برای آلیاژهای مس دمای مناسب اکستروژن گرم بین 650 تا 1300 درجه سانتیگراد میباشد.
از مزایای این روش اکستروژن میتوان به امکان تولید قطعات با مقاطع پیچیده و مقاطعی که امکان تولید آنها با فرایندهای دیگر وجود ندارد اشاره کرد. همچنین هزینه کمتر این فرایند، حداقل زمان ممکن جهت انجام فرایند، عدم ایجاد کرنش سختی در قطعه و حفظ تلورانس ابعادی عالی از دیگر مزایای این روش میباشند.
معایب این روش نیز شامل سایش بالا، نگهداری بالای این روش، سطح پایین و احتمال ایجاد ترک گرم در دمای 510 درجه به بالا میباشد.
دمای مناسب فلزات در روش گرم
مواد دما [°C (°F)] منیزیم 350–450 (650–850) آلومینیوم 350–500 (650–900) فلز مس 600–1100 (1200–2000) فولاد 1200–1300 (2200–2400) تیتانیوم 700–1200 (1300–2100) نیکل 1000–1200 (1900–2200) آلیاژهای نسوز تا 2000 (4000)
- اکستروژن سرد
در روش اکستروژن سرد، فرایند اکستروژن در دمای اتاق و بدون ایجاد حرارت انجام میشود؛ اما در طول انجام تغییر شکل قطعه، امکان افزایش دمای آن وجود دارد. این روش برخلاف اکستروژن گرم، عدم اکسیداسیون را به همراه دارد. از جمله موادی که غالبا در این روش مورد استفاده قرار میگیرند میتوان به مس، قلع، سرب و آلومینیوم اشاره کرد.
این روش اکستروژن براساس نوع پانچ، طراحی قالب و سیالیت مواد میتواند به صورت مستقیم، غیر مستقیم و یا جانبی انجام شود. فشار پانچ در این روش نیز به تنش ناشی از سیلان قطعه، میزان تغییر شکل یا کرنش قطعه، هندسه بیلت، اصطکاک بین بیلت و قالب و همچنین طراحی قالب بستگی دارد.
از مزایای اکستروژن سرد میتوان به استحکام بالاتر این روش نسبت به اکستروژن گرم، پرداخت سطح بهتر، داشتن فرایند سریعتر، خواص مکانیکی قطعه ایجاد شده و کیفیت سطح بالای قطعه اشاره کرد. اما در این روش نسبت به اکستروژن گرم نیاز به نیروی بیشتری وجود داشته و محصول نهایی کرنش نیز سخت شده خواهد بود.
- اکستروژن مستقیم
این روش یکی از رایجترین انواع روش های اکستروژن است که با نام اکستروژن رو به جلو نیز شناخته میشود و برای هر دو حالت گرم و سرد قابل استفاده است. در این روش، شمش به صورت مستقیم تزریق شده و به آن نیرو وارد میشود. قالب مورد استفاده نیز ثابت میباشد و شمش یا بیلت فلزی توسط حرکت پیستون به سمت قالب هدایت میشود. بنابراین جهت حرکت پیستون و قطعه یکسان خواهد بود که منجر به کنترل دقیق قطعات متحرک و انتقال بهینه قدرت میشود.
از این روش میتوان برای اکسترود موادی مانند مس، آلومینیوم، منیزیم و آلیاژهای آنها و همچنین برای اکسترود فولادهای کربنی و فولادهای زنگ نزن، به دلیل قابلیت انعطافی بالایی که دارند، در شکلهای مختلف استفاده کرد.
در این روش از انواع اکستروژن برای انجام اکستروژن از پرسهای مستقیم برای تولید مقاطع توپر، میلگردها، تسمهها و سایر مقاطع استفاده میشود. همچنین با توجه به هم راستا بودن جهت در این روش، امکان استفاده از بیلتهایی با شکل گرد و چهار گوش نیز در آن وجود دارد. در اکستروژن مستقیم همچنین میتوان از ابزارهای بسیار بزرگ برای تولید ایمن و مطمئن مقاطع بزرگ و عریض با حداقل تلرانس و کیفیت بالا استفاده کرد.
در این روش از پرسهای پیشرفتهای استفاده میشود که معمولا به ابزارهای خاصی مانند گیره قالب، محورهای فشاری با قابلیت باز و بسته شدن آسان، کنترل اتوماتیک هم راستایی، بالشتک برشی، فشار دهنده بیلت تلسکوپی، سیستم جاگذاری ضربهای و نرم افزارهای کامپیوتری برای بازدهی و کیفیت بالاتر، مجهز هستند.
از مزایای این روش میتوان به قابلیت کنترل قطعه، سادگی اجرای فرایند و قابلیت کنترل و خنک کاری قطعه اکسترود شده بعد از خروج از قالب اشاره کرد. اما این روش دارای اصطکاک زیادی در سطح تماس بین شمش و محفظه است و باعث ایجاد حرارت و احتمال تشکیل عیوب داخلی میشود. همچنین انجام عملیات این روش نیاز به نیروی بالایی خواهد داشت.
- اکستروژن معکوس (اکستروژن غیر مستقیم)
در این روش اکستروژن، برخلاف روش اکستروژن مستقیم، جهت حرکت پیستون و قطعه در خلاف جهت یکدیگر است. در واقع در این روش، به جای حرکت شمش فلزی به سمت قالب، قالب به سمت بیلت حرکت کرده و آن را از خود عبور میدهد. انرژی مورد نیاز برای این نوع از اکستروژن کمتر است و به همین اصطکاک کمتری ایجاد میشود.
روش اکستروژن معکوس غالبا برای اکسترود آلیاژهای سخت مناسب است و در هر دو حالت گرم و سرد قابل اجرا میباشد. همچنین در این روش امکان ایجاد قطعات با ضخامت کمتر وجود داشته و از آن میتوان برای کاربردهای مختلف اعم از ساخت میلهها، مقاطع و لولههای آلومینیومی استفاده کرد.
به دلیل کاهش اصطکاک در این روش، نیروی مورد نیاز برای انجام فرایند نیز در حدود 20 تا 30 درصد کمتر از روش مستقیم میباشد و دمای سطح شمش نیز به شکل ناخواسته افزایش پیدا نمیکند. همچنین با استفاده از این روش میتوان قطعات نازکتری را تولید کرد. اما در فرایند اکستروژن معکوس امکان خنککاری محصول پس از خارج شدن از قالب با محدودیت بیشتری همراه است. همچنین احتمال کیفیت پایینتر سطح خارجی محصول نسبت به روش اکستروژن مستقیم نیز وجود دارد.
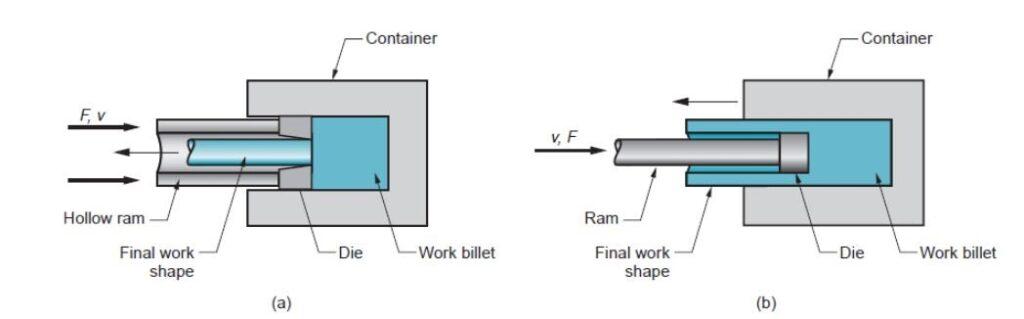
- اکستروژن هیدرواستاتیک
در این روش اکستروژن، به جای نیروی پرس، برای اعمال فشار روی شمش فلزی از یک سیال استفاده میشود. به عبارتی، فاصله میان پیستون و بیلت با مایعی مانند روغن پر میشود تا فشار از طریق آن به بیلت وارد شود. با این کار، نیروی اصطکاک به شدت کاهش پیدا میکند. محفظه یا حفره نیز کوچکتر از بیلت ساخته شده و نیرو را از سنبه به بیلت انتقال میدهد. مهمترین مزیت این روش، نیاز به اعمال نیروی کمتر به دلیل اصطکاک ناچیز در آن است.
در این روش اکستروژن، نیروهای سه محور توسط سیال منتقل شده و فشار حاصل از آن به شکلپذیری و بهبود بیلت کمک میکند. همچنین در روش اکستروژن هیدرواستاتیک، از بیلتهای بزرگ در دستگاه اکستروژن استفاده شده و در نتیجه با استفاده از آن میتوان مقاطع فلزی بزرگ را تولید کرد.
از دیگر مزایای این روش میتوان به کاهش مصرف نیرو و انرژی، به دلیل عدم ایجاد اصطکاک در این روش، جلوگیری از بالا رفتن دمای بیلت، عدم ایجاد پرتی و توزیع متعادل نیرو به دلیل جریان یکنواخت مواد اشاره کرد. اما به دلیل وجود سیالی مانند روغن، امکان استفاده از حالت گرم در این روش وجود ندارد و نگهداری از مایعات پرفشار نیز دشوار و پرهزینه خواهد بود. همچنین غالبا لازم است تا یک انتهای بیلت باریک شود تا اندازه آن با زاویه ورودی قالب تطبیق پیدا کند.
- اکستروژن ضربهای
این روش از انواع اکستروژن که بسیار مشابه با روش اکستروژن مستقیم است، در حالت سرد قابل انجام بوده و با استفاده از آن میتوان فلزات نرمی مانند مس، آلومینیوم و سرب را اکسترود کرد. در فرایند این روش، پیستون با سرعت بالایی به سمت پایین فشرده شده و باعث ورود نیروی زیادی به شمش میشود. با اعمال این نیرو شمش یا همان بیلت از دو طرف به سمت عقب پیستون اکسترود شده و با استفاده از استریپر از قالب خارج میشود.
نیروی وارد شده بر پانچ در این روش بسیار زیاد است و به همین دلیل ابزار مورد استفاده باید مقاومت کافی را داشته باشد.
ضخامت مقاطع اکسترود شده در این روش، تابعی از فاصله بین پانچ و حفره قالب است. همچنین در این روش غالبا از پرس مکانیکی استفاده شده و قطعه با سرعت بالا و با یک ضربه نسبتا کوتاه شکل داده میشود.
این روش اکستروژن براساس حرکت مواد سه نوع رو به جلو، معکوس و ترکیبی را شامل میشود. در اکستروژن ضربهای رو به جلو، فلز در همان جهت ورود نیرو، جریان پیدا میکند؛ در صورتی که در اکستروژن ضربهای معکوس، فلز در خلاف جهت جریان مییابد. در نوع ترکیبی نیز امکان حرکت مقطع فلزی در هر دو جهت وجود دارد.
از مزایای این روش میتوان به صرفهجویی در مصرف مواد اولیه تا 90 درصد، کاهش زمان ماشین کاری تا 75 درصد، حذف عملیات ماشین کاری ثانویه، بهبود خواص مکانیکی و استحکام مواد، بهبود قابلیت ماشین کاری و صرفهجویی در هزینههای کل تا 50 درصد، اشاره کرد. اما در برابر، اغلب قطعاتی که به این روش اکسترود میشوند، قبل از تکمیل نیاز به انجام فرایندهای جانبی بیشتری مانند فورج کاری و… دارند.
- اکستروژن جانبی یا عمودی
در این روش اکستروژن، محفظه دستگاه پرس به صورت عمودی قرار گرفته و قالب نیز در کناره دستگاه قرار دارد و باید به صورت افقی درون دستگاه قرار داده شود. در این دستگاه رام یا همان پانچ دستگاه از بالا به سمت پایین حرکت کرده و منجر به فرستادن به بیلت به درون قالب میشود. این روش از اکستروژن فلزات، غالبا برای شکلدهی به فلزاتی با نقطه ذوب پایین استفاده میشود.
- اکستروژن لوله ای
در این روش اکستروژن، از قالبهای مخصوصی استفاده میشود که در قسمت وسطی آنها حفرهای وجود دارد. شمش جامد از طریق حفره روی قالب، عبور داده شده و باعث ایجاد لولههای توخالی و بدون درز میشود. این روش در واقع یکی از بهترین و رایجترین روشها برای تولید لوله محسوب میشود و با استفاده از آن میتوان قطعاتی یکنواخت و بدون درز را با دستگاه اکستروژن ایجاد کرد.
ایرادات ناشی از فرایند اکستروژن
همانطور که خواندید، اکستروژن یکی از فرایندهای تغییر شکل مواد است. به همین دلیل، در حین تغییر شکل مواد، ممکن است ایرادات احتمالی مختلفی در محصولات اکسترود شده ایجاد شوند. رایجترین این ایرادات احتمالی عبارتند از:
- انفجار مرکزی (center burst): این ایراد احتمالی جزء عیوب داخلی است که بر اثر تنش کششی در طول عملیات اکستروژن رخ میدهد و احتمال وقوع آن حین اکستروژن فشاری بسیار کم است. وجود ناخالصی در مواد میتواند باعث شروع ایجاد ترک در داخل قطعه کار شود.
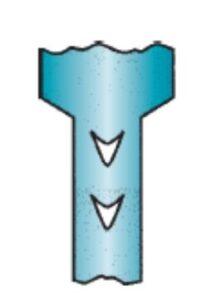
لولهای شدن: این مسئله مربوط به روش انجام اکستروژن مستقیم است که با ایجاد آن، انتهای شمش تغییر شکل داده و داخل آن فرو میرود.
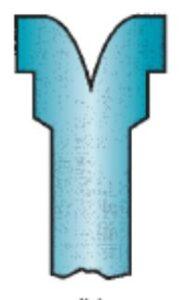
ترکهای سطحی: در دماهای بالا و یا زمانی که سرعت فرایند اکسترود بسیار بالا باشد، احتمال ایجاد ترکهای سطحی روی قطعه وجود دارد. در واقع این مسئله به دلیل نرخ کرنش بالا و تولید گرما ایجاد میشود. گرچه سایش بالا و سرعت سرد کردن از دمای بالای اکستروژن گرم میتوانند روی ایجاد ترکهای سطحی موثر باشند.
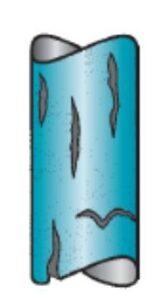
دستگاه اکستروژن
فرایندهای اکستروژن غالبا توسط دستگاهی به نام اکسترودر انجام میشوند. اکسترودر یک دستگاه صنعتی است که شکلی محفظی و ماردون مانند دارد. این دستگاه مواد گرانولی را با نیروی حرکتی و حرارتی به داخل هدایت میکند تا هنگام خروج با فشار از انتهای دستگاه، محصولی به صورت خمیری یا نواری شکل ایجاد شود. این دستگاه غالبا برای اکستروژن در کاربردهای صنایع لاستیک و پلاستیک استفاده میشود.
دستگاه پرس اکستروژن
اکستروژن یکی از روشهای تولید ناپیوسته است و قطعات تولید شده با آن به صورت جداگانه در خروجی دستگاه اکستروژن قرار میگیرند. دستگاه اصلی مورد استفاده در اکستروژن، دستگاه پرس اکستروژن است که دارای مکانیزم سادهای میباشد. این دستگاه از اجزای مختلفی تشکیل شده است که مهمترین و اصلیترین اجزای آن عبارتند از:
- قالب اکستروژن (Die): این قالب اکستروژن برای شکلدهی مواد مورد استفاده قرار گرفته و مواد اولیه با فشار درون آن وارد میشوند. این قالبها غالبا از جنس صفحات فولادی هستند.
- رام (Ram): این جزء دستگاه، میلهای فولادی متصل به سیلندر است که مواد اولیه را به سمت قالب هدایت میکند.
- دامی(Dummy): این جزء از دستگاه، قطعهای است که بین رام و بیلت قرار گرفته و مانع از بازگشت مواد اولیه به بیرون از کانتینر میشود.
- بیلت (Billet): این جزء همان مقدار مورد نیاز از مواد اولیه است که برای تولید هر قطعه مورد استفاده قرار میگیرد.
- کانتینر (Container): بیلت درون این محفظه قرار گرفته و در اثر فشار به سمت قالب هدایت میشود.
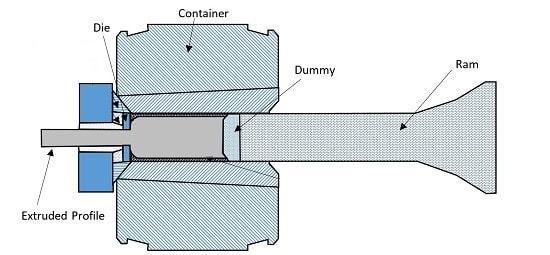
کاربرد دستگاه اکستروژن
ویژگیهای متعدد فرایندهای مختلف اکستروژن باعث شدهاند که از آن در صنایع مختلف به طور گسترده استفاده شود. برخی از رایجترین کاربردهای اکستروژن در صنایع مختلف عبارتند از:
- صنعت خودروسازی: برای ساخت اجزایی مانند قاب پنجرهها، مبدلهای حرارتی و قطعات موتور
- صنعت هوافضا: برای ساخت بال و اجزای بدنه هواپیما به دلیل وزن کم و استحکام بالای اکستروژن
- صنایع ساخت و ساز: برای ساخت قاب در و پنجره، عناصر تزئینی و پروفیلهای سازهای
- کالاهای مصرفی: ساخت طیف وسیعی از کالاها اعم از مبلمان و لوازم خانگی به دلیل انعطاف در طراحی و مقرون به صرفه بودن این روش
- انرژیهای تجدیدپذیر: برای تولید قابهای پانل خورشیدی، اجزای توربین بادی و مبدلهای حرارتی
- محصولات پلیمری: برای ساخت کامپاندها یا سایر آمیزههای پلیمری، فیلمها، لولهها و شیلنگهای پلاستیکی، تولید سیم و کابل، کاغذها یا فلزات پوشش داده شده با پلاستیک
- تولید محصولات و قطعاتی مانند پروفیلها، ورقههای بسیار نازک و قطعات گرانولی شکل
در نتیجه میتوان گفت این فرایند از فرایندهای پرکاربرد در صنایع مختلف است که مزایای بسیاری را در تولید محصولات و قطعات مختلف ارائه میدهد.
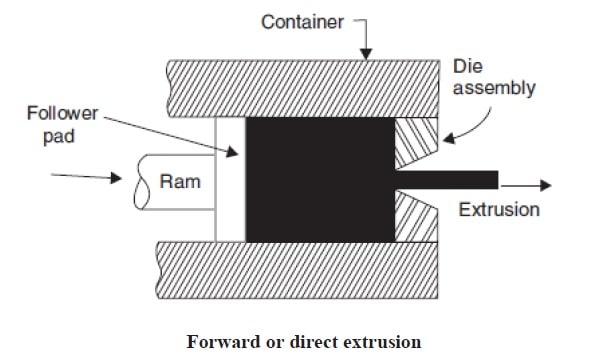
مزایا و معایب اکستروژن
همانطور که گفته شد، اکستروژن یکی از پرکاربردترین روشهای تغییر شکل فلزات است که برای تولید انواع مقاطع و بخصوص مقاطع دارای اشکال پیچیده استفاده میشود. این روش همانند تمامی فرایندهای صنعتی ویژگیهای بخصوصی دارد که از مهمترین مزایای آن میتوان به موارد زیر اشاره کرد:
- با استفاده از فرایند اکستروژن میتوان شکلهای پیچیده مقاطع را به سادگی تولید کرد.
- فرایندهای اکستروژن و بخصوص اکستروژن سرد، تلورانس ابعادی نسبتا پایینی را شامل میشوند.
- با استفاده از این فرایند ضایعات مواد اولیه مورد استفاده به حداقل میزان ممکن میرسد و دور ریز مواد در این روش بسیار کم است.
- فرایند اکستروژن منجر به بهبود خواص مکانیکی فلزات اکسترود شده اعم از استحکام و انعطافپذیری آنها میشود.
- قطعاتی که به وسیله این فرایند تولید میشوند، دارای کیفیت، عملکرد و دوام بالایی هستند.
- این روش با سرعت بالایی انجام شده و کاهش ضایعات را به همراه دارد؛ در نتیجه با استفاده از آن در زمان و هزینه صرفهجویی میشود.
در کنار این مزایا، اکستروژن فلزات یکسری معایب و محدودیتها را نیز شامل میشود؛ که رایجترین آنهاعبارتند از:
- در صورت عدم انتخاب صحیح متغیرهای مختلف در این فرایند، احتمال ایجاد ترک در قطعه یا شمش وجود دارد.
- در این فرایند، سطح مقطع قطعه اکسترود شده باید در تمام طول آن یکنواخت باشد.
- تغییر شکل برای تمامی فلزات توسط این روش توصیه نمیشود و امکان ایجاد مشکلاتی اعم از ترکخوردگی یا پارگی در برخی از مواد توسط این روش وجود دارد. در واقع رایجترین فلزاتی که امکان تغییر شکل آنها با این روش وجود دارد، شامل آلومینیوم، سرب، مس و موادی مشابه این موارد میباشند.
- تهیه تجهیزات اولیه دستگاه اکستروژن نیاز به سرمایهگذاری زیادی دارد و این روش برای تولید در مقیاس کوچک توجیه اقتصادی ندارد.
سوالات متداول
اصول فرایند اکستروژن چیست؟
در روشهای مختلف اکستروژن برخی فرایندها اهمیت بسیاری دارند و از اصول مهم این روشها محسوب میشوند. در نتیجه میتوان گفت اصولی مانند آمادهسازی شمش، طراحی قالب، پرس و کنترل دما از اصول مهم و اساسی فرایند اکستروژن محسوب میشوند.
انواع روشهای اکستروژن چیست؟
به طور کلی، اکستروژن در دو حالت گرم و سرد انجام میشود که از تکنیکهای مورد استفاده در این حالتها میتوان به روشهای اکستروژن مستقیم، اکستروژن معکوس، هیدرواستاتیک، لولهای و ضربهای اشاره کرد.
روشهای اکستروژن چه مزایایی به همراه دارند؟
فرایند تغییر شکل با روش اکستروژن مزایای مهمی شامل امکان تولید قطعات با سطح مقطع پیچیده، کارایی مواد، بهبود خواص مکانیکی و صرفهجویی در زمان و هزینه را شامل میشود.
اکستروژن پلاستیک به چه صورت انجام میشود؟
در این روش اکستروژن، یک ماده ترموپلاستیک مورد استفاده قرار گرفته و با استفاده از حرارت نرم میشود تا آماده شکلدهی شود. پس از آن، دستگاه اکسترودر برای فرمدهی این مواد مورد استفاده قرار میگیرد.
جمع بندی
شکلدهی فلزات به روشهای مختلفی انجام میشود که هر کدام ویژگیهای خاص خود را دارند. یکی از روشهای رایج و پرکاربرد برای این منظور، روش اکستروژن است. در این روش با آمادهسازی بیلت، طراحی قالب، پرس و کنترل دما و انجام یکسری تکنیکها، فرایند اکستروژن انجام میشود. این فرایند مزایای زیادی را به همراه داشته و قطعهای که با استفاده از آن تولید میشود غالبا دارای کیفیت و استحکام بالایی است. از روش های انواع اکستروژن با دستگاه اکستروژن در کاربردهای مختلف و گستردهای استفاده میشود و میتواند در تولید قطعات مختلفی مورد استفاده قرار بگیرد.