ریخته گری یکی از متداولترین روشهای تولید قطعات فلزی و غیرفلزی است. ریخته گری تحت فشار یکی از رایجترین روشهای ریخته گری است که غالبا برای تولید قطعات نازک با استحکام بالا مورد استفاده قرار میگیرد. این روش برای تولید قطعات با استفاده از اغلب فلزات مورد استفاده قرار میگیرد اما نمیتوان از آن برای تولید قطعات فلزی از جنس چدن یا فولاد یا فلزاتی که دارای نقطه ذوب بالا هستند، استفاده کرد.
اگر میخواهید با ریخته گری تحت فشار، ویژگیها و کاربردهایش بیشتر آشنا شوید، مطالعه این مقاله را از دست ندهید.
ریخته گری تحت فشار (die casting) چیست ؟
ریخته گری تحت فشار یا ریخته گری دایکاست (die casting) یکی از شناخته شدهترین روشهای ریخته گری است که طی فرایند آن مواد مذاب، تحت فشار به داخل قالب تزریق میشوند. برخلاف سیستمهایی که در آنها مواد مذاب تحت نیروی وزن خود به داخل قالب ریخته میشوند، سیستم ریخته گری تحت فشار، قابلیت تولید قطعات محکم و بدون حفرههای درونی را دارد. در واقع اعمال فشار باعث حذف حفرهها و تخلخلها شده و منجر به افزایش استحکام قطعات میشود.
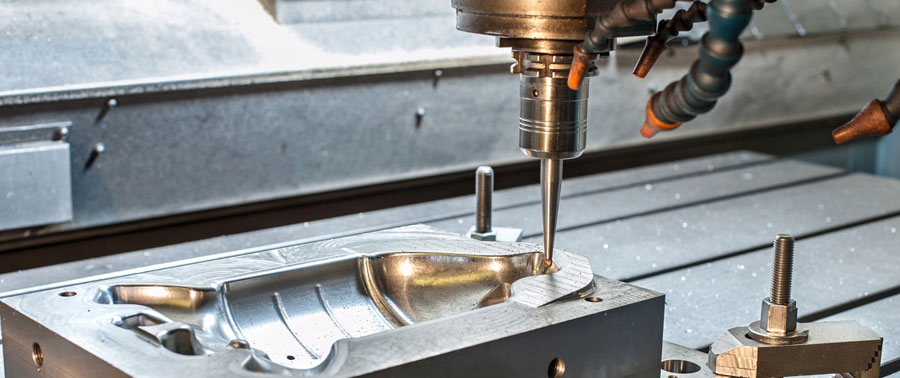
این روش به عنوان سریعترین و اقتصادیترین روش تولید قطعات و محصولات فلزی شناخته میشود؛ به همین دلیل کاربرد آن در صنایع مختلف بسیار گسترده است. امروزه، ریخته گری تحت فشار به عنوان یکی از مهمترین روشهای تولید قطعات صنعتی شناخته میشود. محصولات و قطعاتی که توسط این روش تولید میشوند، غالبا دارای کیفیت بیشتری نسبت به قطعات تولید شده توسط روشهای دیگر میباشند.
از ریخته گری دایکاست یا تحت فشار برای تولید قطعات با وزن 90 گرم تا حدود 25 کیلوگرم استفاده میشود.
ریخته گری دایکاست با ریخته گری قطعات چاپگر مانند چرخ دنده ها و میل لنگ زنگ در اوایل / اواسط قرن 19 آغاز شد. قطعات ساده بودند: ابزارها آهنی و درشت ساخته شده بودند و مواد پر شده با دست از ملاقه ریخته می شد. این فرآیند در قرن بیستم توسعه یافت تا به یک پایه اصلی در تولید قطعات فلزی با حجم بالا تبدیل شود. خطوط تولید کاملاً خودکار و پیچیده در حال حاضر رایج شدهاند، اگرچه بسیاری از منشأهای ابتداییتر این فرآیند هنوز در استفاده تجاری معنادار هستند.
تاریخچه ریخته گری دایکاست
لیست فلزات مورد استفاده در ریخته گری تحت فشار
در گذشته، انسانها به استخراج و استفاده از فلزات دسترسی نداشتند؛ اما به مرور زمان فلزات کشف شده و روشهای متنوعی برای تولید قطعات فلزی ابداع شدند. روش ریخته گری تحت فشار غالبا با استفاده از آلیاژهای غیرآهنی انجام میشود. انتخاب مواد اولیه برای انجام ریخته گری تحت فشار کاملا به عواملی مانند نقطه ذوب، استحکام، دانسیته، مقاومت به خوردگی و حتی هزینه بستگی دارد.
رایجترین و پرطرفدارترین آلیاژهایی که در ریخته گری تحت فشار مورد استفاده قرار میگیرند، عبارتند از:
- آلیاژهای آلومینیوم: این آلیاژها وزن سبکی داشته، در برابر خوردگی مقاومت بالایی دارند و خواص مکانیکی مطلوبی را ارائه میدهند. سازگار بودن با محیط زیست، هدایت حرارتی مطلوب و هدایت الکتریکی بالا نیز از دیگر ویژگیهای آلیاژهای آلومینیوم در ریخته گری دایکاست است.
امکان تولید قطعات با دیوارههای نازک و هندسههای پیچیده با استفاده از آلومینیوم و ریخته گری آلومینیوم وجود دارد و این آلیاژها در صنایع مختلفی اعم از هوافضا، خودروسازی و الکترونیک بسیار کاربرد دارند.
- آلیاژهای مس: این آلیاژها در برابر خوردگی و سایش مقاومت بالایی از خود نشان میدهند و در بین آلیاژهای مورد استفاده در ریخته گری تحت فشار، بهترین خواص مکانیکی را دارند. اغلب محصولات و قطعاتی که با استفاده از مس ساخته میشوند، بادوام هستند. از این آلیاژ غالبا برای تولید قطعات صنایع لولهکشی و برق استفاده میشود.
- آلیاژهای منیزیوم: این آلیاژها سبکترین آلیاژهایی هستند که در ریخته گری تحت فشار مورد استفاده قرار میگیرند. نسبت استحکام این آلیاژها نسبت به وزنشان بالا است و به همین دلیل در ریخته گری دایکاست بسیار کاربرد دارند. از جمله کاربردهای این آلیاژ در صنایع میتوان به کاربرد گسترده آنها در صنعت هوافضا اشاره کرد.
- آلیاژهای روی: این آلیاژها آسانترین فلزاتی هستند که به سادگی ریخته گری میشوند. آلیاژهای روی انعطافپذیری و شکلپذیری بالایی دارند و بسیار مستحکم هستند. دقت بالا، تحمل در برابر سختیها و ویژگیهای حرارتی برجسته از دیگر ویژگیهای آلیاژ روی است.این آلیاژ نیز برای تولید چرخدندهها و اتصالدهندهها در فرایند ریخته گری تحت فشار به طور متداول مورد استفاده قرار میگیرد.
- آلیاژهای برنز و برنج: این آلیاژها نیز تقریبا به همان سرعت آلیاژهای روی ریخته گری میشوند. قطعاتی که با استفاده از این آلیاژها ساخته میشوند بسیار مستحکم و بادوام هستند.
- آلیاژهای سرب: مهمترین ویزگی این آلیاژها مقاومت آنها در برابر خوردگی است. استفاده از آلیاژهای سرب در صنایعی که با مواد غذایی در تماس هستند، توصیه نمیشود. از این آلیاژها غالبا در تولید وسایل ایمنی آتشنشانی، وسایل فلزی زینتی و یاتاقانها استفاده میشود.
انواع دستگاه (ماشین) ریخته گری تحت فشار
در ریخته گری تحت فشار، دو دستگاه مختلف بر اساس کاربرد و اندازه قطعه، مورد استفاده قرار میگیرند: دستگاه دایکاست با محفظه گرم و دستگاه دایکاست با محفظه سرد.
در ادامه هر یک از این دستگاهها همراه با ویژگیهایشان معرفی شدهاند.
دستگاه دایکاست با محفظه گرم چیست؟ (Hot chamber die casting machine)
در ساختار این دستگاهها یک محفظه فشار قرار گرفته است که به حفره قالب متصل میباشد. فلز مذاب به طور مداوم و توسط فشار به داخل این محفظه نفوذ میکند. زمانی که سیلندر محفظه به حالت بدون فشار بازگردد، فلز مذاب به داخل قالب، ریخته گری میشود. برای این منظور، ظرف مخصوص قالب برای ذوب کردن فلز به دستگاه متصل شده و مکانیزم پیستونی برای تزریق هیدرولیک فلز به داخل قالب ظرف نصب میشود.
پس از بسته شدن قالب، پیستون خارج شده و دریچه محفظه برای جریان یافتن فلز مذاب به داخل محفظه باز میشود. پس از آن، فلز مذاب از طریق گردن غاز و نازل به داخل حفره قالب فشار میدهد و پیستون درگاه را مسدود میکند. زمانی که فلز مذاب به حفره قالب وارد شد، این فلز تحت فشار قرار میگیرد تا زمانی که در داخل قالب منجمد شده و شکل جامد به خود بگیرد.
در برخی از دستگاههای ریخته گری محفظه داغ، برای فشار مستقیم فلز به داخل قالب، از هوای فشرده استفاده میشود. فرایند ریخته گری با دستگاه محفظه گرم فشار بالایی داشته و به همین دلیل نسبت به فرایند محفظه سرد نرخ تولید بسیار بالاتری دارد.
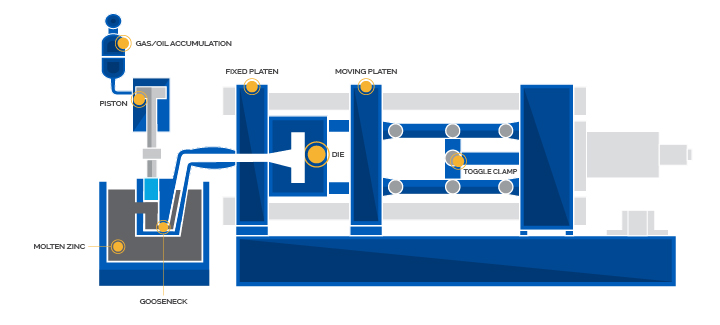
از مزایای فرایند ریخته گری با دستگاه دایکاست محفظه گرم میتوان به بهرهوری بالا، بهبود سطح پرداخت، امکان تولید قطعات پیچیده، سرعت تولید سریعتر، امکان ذوب شدن فلز درون دستگاه ریخته گری، کاهش تخلخل قطعات، ایجاد حداقل ضایعات، داشتن نقطه ذوب پایین و عمر طولانیتر اشاره کرد.
این دستگاه بیشتر برای آلیاژهایی که دمای ذوب پایینی دارند اعم از روی، قطع و سرب مورد استفاده قرار میگیرد. دماهای بالاتر برای ذوب سایر آلیاژها میتواند باعث آسیب به پمپ شود؛ زیرا پمپ در تماس مستقیم با فلز مذاب قرار دارد. در این فرایند، نیاز به استفاده از مکانیزم پیستون وجود ندارد؛ زیرا مکانیزم تزریق در فلز مذاب غوطهور میشود. در اینصورت لازم است از فرسایش یا آسیبهای شیمیایی به سیستم تزریق غوطهور جلوگیری شود.
روش ریخته گری دایکاست با دستگاه محفظه داغ یکسری معایب را نیز شامل میشود. به عنوان مثال، این روش تنها برای تولید قطعات در تیراژ بالا مناسب است و از آن نمیتوان برای فلزات با نقطه ذوب بالا استفاده کرد. همچنین در این روش سیالیت کم فلز باعث محدود شدن پیچیدگی محصول میشود. محدوده فشار بالایی نیز در این روش مورد نیاز است.
دستگاه دایکاست با محفظه سرد چیست؟ (Cold Chamber Die Casting Machine)
در این دستگاه، فلز مذاب در یک کوره نگهدارنده جداگانه نگهداری شده و پس از اینکه قالب بسته میشود، این فلز به داخل محفظه سرد ریخته شده و پس از آن با فشار وارد قالب میشود. فرایند دستگاه دایکاست با محفظه سرد به گونهای است که فلز در خارج از دستگاه ذوب شده و سپس به محفظه فشردهسازی اضافه میشود. این دستگاه دو نوع مختلف دستگاه دایکاست محفظه سرد عمودی و دستگاه محفظه سرد افقی را شامل میشود که هریک از آنها در جهت حرکت پیستون فشردهسازی با یکدیگر تفاوت دارند.
در دستگاه محفظه سرد عمودی، فلز مذاب از کوره خارج شده و به داخل محفظه فشردهسازی ریخته میشود. پس از آن فلز توسط پیستون تراکمی به درون قالبهاب مخصوص وارد شده و فلز اضافی توسط یک پیستون دیگر به بیرون رانده میشود. دستگاه محفظه سرد افقی نیز همانند دستگاه عمودی است اما جهت حرکت پیستون افقی خواهد بود. امروزه غالبا از دستگاه ریخته گری دایکاست محفظه سرد افقی استفاده میشود.
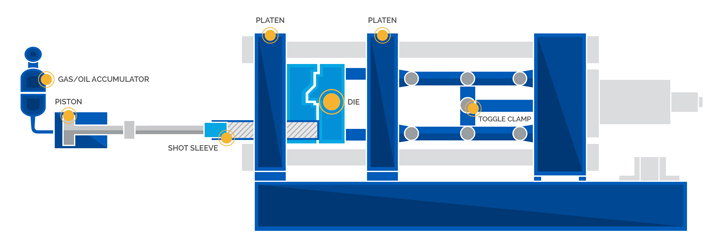
فرایند محفظه سرد پس از انتقال مواد مذاب از طریق سوراخ از کوره به محفظه شات، آغاز میشود. پس از آن، درگاه محفظه سرد توسط یک پیستون بسته شده و فلز با فشار وارد حفره قالب میشود. پس از تزریق فلز به داخل حفره، پیستون به سمت جلو باقی مانده و در حالی که فلز منجمر میشود، پیستون فشار را نگه میدارد. پس از منجمد شدن مواد نیز، سیستم هیدرولیک پیستون را جمع کرده و قطعه توسط واحد گیره خارج میشود.
واحد گیره و نصب قالبها در این دستگاه مشابه دستگاه محفظه گرم است. اما این دستگاه برخلاف دستگاه محفظه گرم برای فلزات با نقطه ذوب زیادی اعم از فلز مس و آلومینیوم نیز مناسب است.
از مزایای این دستگاه میتوان به کاهش احتمال خوردگی، امکان ریخته گری فلزات با نقطه ذوب بالا، امکان ساخت قطعات بزرگ، امکان ساخت قطعات با مقاومت بالاتر، ریخته گری متراکمتر به دلیل افزایش فشار حین تزریق، هزینه نگهداری کمتر، دقت ابعادی بالا، امکان تولید با سرعت بالا و فرآیند ساده برای انجام ریخته گری اشاره کرد.
اما ریخته گری با این دستگاه معایبی را نیز شامل میشود. به عنوان مثال، در این روش زمان فرایند کندتر از روش ریخته گری در دستگاه محفظه گرم است. همچنین فرایند ریخته گری با فشار پایینتری انجام میشود و کیفیت قطعه نهایی به دلیل آلایندههای بیشتر پایینتر خواهد بود.
انواع روش های ریخته گری تحت فشار
فرایند ریخته گری دایکاست یا تحت فشار انواع مختلفی دارد که قالب گیری در آنها با استفاده از فلز مذاب تزریقی به نوع فلز ذوب شده، نوع هندسه قطعات و اندازه قطعه بستگی دارد. در اینصورت انواع فرایندهای این روش را میتوان در موارد زیر دسته بندی کرد:
ریخته گری فشار بالا به کمک خلاء (Vacuum Die Casting)
این فرایند بیشتر با دستگاه دایکاست محفظه سرد انجام میشود. در این روش، گازهای محبوس شده در داخل حفره قالب، توسط یک منبع خلاء هوا، قبل از ورود فلز مذاب به قالب حذف میشوند. ریخته گری فشار بالا به کمک خلاء، باعث به حداقل رسیدن تلاطم گاز شده و برای مواقعی که عملیات حرارتی پس از ریختگی در نظر گرفته میشوند، بسیار کاربرد دارد. فلز مذاب شده در این روش، توسط فشار خلاء و با سرعت بالا به درون قالبهای اصلی ریخته میشود. این کار روی چرخه زمانی کوتاهتر و دقت ریخته گری بالاتر بسیار موثر است.
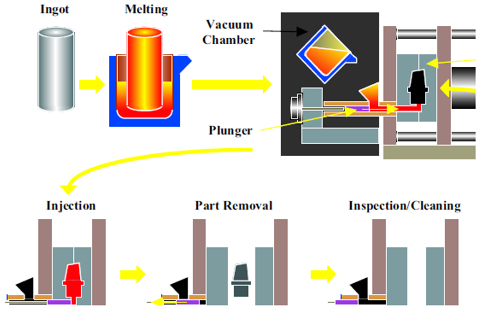
از مزایای فرایند ریخته گری فشار بالا به کمک خلاء میتوان به بهبود خواص مکانیکی قطعه، پرداخت سطح بهتر، پایداری ابعادی، کوتاهتر شدن زمان فرایند و کاهش عیبهای احتمالی ناشی از گازهای به دام افتاده اشاره کرد.
ریخته گری فشار پایین (low-pressure die casting)
ریخته تحت فشار با فشار پایین برای تولید قطعات آلومینیومیکه حول برخی از محورهای چرخش متقارن هستند، بسیار کاربرد دارد و به طور متداول برای تولید این دسته از قطعات مورد استفاده قرار میگیرد. از جمله قطعاتی که با ریخته گری فشار پایین تولید میشوند میتوان به چرخهای خودرو اشاره کرد. در فرایند این ریخته گری، قالب به صورت عمودی بالای حمام فلز مذاب باقی مانده و با لوله رایز به آن متصل میماند. پس از آن فلز گرم شده، در محفظه تحت فشار با فشار معینی قرار گرفته و فلز مذاب را به سمت بالا به داخل قالب میکشد.
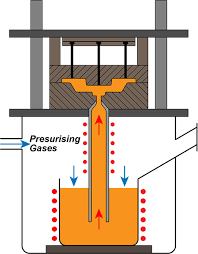
ریخته گری فشرده (Squeeze casting process)
ریخته گری فشرده یا ریخته گری فشاری همان آهنگری فلز مایع است که ویژگیهایی از ریخته گری و آهنگری را برای ساخت اجزای خودرو و بدنههای ملات ارائه میدهد. در ابتدای این فرایند، فلز مذاب درون قالب فشرده میشود. پس از آن، زمانی که فلز مذاب شد، نواحی فرو رفته درون قالب توسط این فلز پر شده و محصولات به صورت متراکم شده تولید میشوند. از این روش با نفوذ آلومینیوم مذاب به ساختار تقویت کننده الیاف برای ساخت کامپوزیتهای زمینه فلزی نیز استفاده میشود.
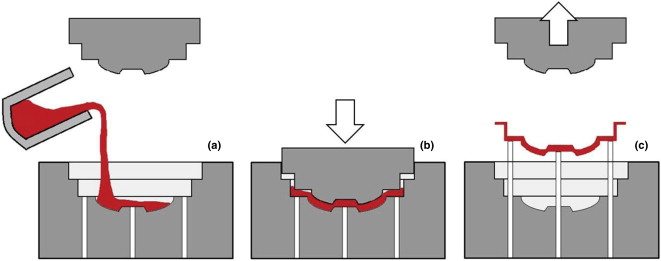
از مزایای این فرایند میتوان به کاهش انقباض و تخلخل گاز، بهبود کیفیت مکانیکی قطعه به دلیل ساختار دانههای کوچک ناشی از انجماد سریع و کیفیت سطح برتر قطعه اشاره کرد. در این روش، غالبا از آلیاژهای آلومینیوم و منیزیم برای ریخته گری استفاده میشود.
شکل دهی فلز نیمه جامد (Semi-solid metal forming)
شکل دهی فلز نیمه جامد یا ریخته گری نیمه جامد که با نام پردازش حالت مخلوط نیز شناخته میشود، نوعی فرایند ریخته گری دایکاست با قالب است که در آن از مواد نیمه مذاب استفاده شده و شامل برخی ویژگیهای ریخته گری در کنار ویژگیهای آهنگری میباشد. از این روش بیشتر برای ساخت قطعات فلز آلومینیوم در صنایع هوافضا، برای ساخت پایهها و بلوکهای موتور و محفظههای فیلتر پمپ روغن استفاده میشود.
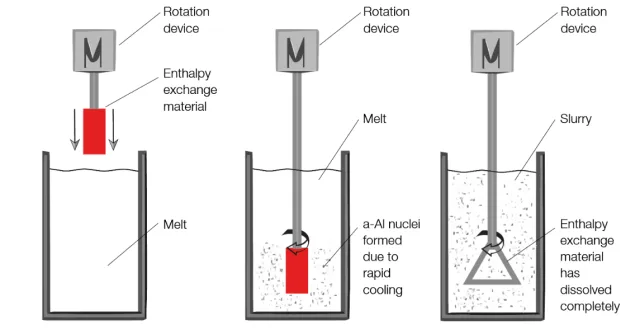
امکان تولید قطعات پیچیده با دیوارههای نازک، امکان تولید قطعات با خواص مکانیکی و سطح عالی و امکان کاهش تخلخل از مزایای ریخته گری تحت فشار نیمه جامد است. اما این روش به شدت در برابر عوامل محیطی مانند دما حساس است. در اینصورت، تجهیزات تولیدی و محیطی مورد استفاده به کنترل بیشتری نیاز داشته و حتی در اکثر موارد نیاز به استفاده از تجهیزات گران قیمت وجود خواهد داشت.
قالب ریخته گری تحت فشار
یکی از مهمترین اجزا برای ساخت قطعات با استفاده از فرایند ریخته گری تحت فشار، قالب است. قالب ریخته گری تحت فشار از دو قسمت ثابت یا قالب پوششی (Cover Die) و قسمت متحرک یا قالب پران (Ejector Die) تشکیل میشود. هر یک از این قسمتها در دستگاه دایکاست روی صفحه مخصوص به خود قرار میگیرند. طراحی دو قسمتی این قالبها، باعث شده است که امکان باز و بسته کردن آنها در راستای یک خط جدایش مشخص فراهم شود. پس از اینکه دو قسمت قالب بسته میشوند، حفره قالب گیری قطعه تشکیل خواهد شد.
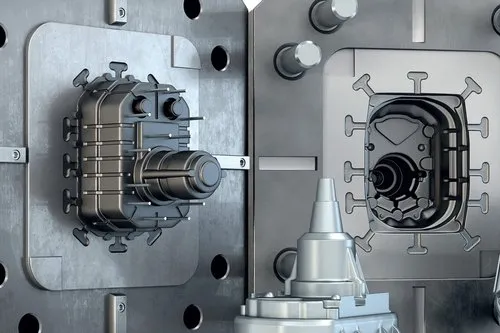
قالبهایی که در دو دستگاه ریخته گری محفظه سرد و ریخته گری محفظه گرم مورد استفاده قرار میگیرند، تقریبا مشابه یکدیگر هستند اما کمیبایکدیگر تفاوت دارند. اجزای قالب ریخته گری دایکاست در دستگاه محفظه گرم و محفظه سرد عبارتند از:
- قالب ثابت
- بوش اسپرو یا راهنما
- مغزی حفره
- حفره قالب
- مجراهای قالب
- دریچه
- قالب متحرک
- جعبه پران
- مغزی ماهیچه
- جداکننده
- راهگاه
- سیستم خنک کننده
- پین پران
- صفحه نگهدارنده
- صفحه حایل
- صفحه پران
- خط جدایش
- اسپرو
- قطعه
در قالبهایی که در دستگاه ریخته گری دایکاست محفظه سرد استفاده میشوند، به جای بوش اسپرو، یک غلاف تزریق تعبیه میشود. در این میان، ذکر این نکته نیز اهمیت دارد که قالبهای مورد استفاده در ریخته گری تحت فشار دارای اجزای مشترک و متفاوت زیادی هستند. در اینصورت، برای قطعاتی که ابعاد و خصوصیات مشابهی دارند، غالبا بخشهای قالب بدون تغییر باقی میماند. اما تفاوت اصلی در ماهیچه و مغزیهای حفرههای قالب است. در نهایت این قسمتها هستن که شکل قطعه نهایی قالب گیری شده را تعیین میکنند.
مراحل و فرایند ریخته گری دایکاست
در فرایند ریخته گری دایکاست با استفاده از دستگاههای محفظه گرم و محفظه سرد، به طور کلی مراحل زیر دنبال میشوند:
آماده سازی قالب (Mold Design)
اولین مرحله در ریخته گری تحت فشار، آماده سازی قالب است. آماده سازی قالب باید به طور دقیق و مطابق با ابعاد قطعات انجام شود. قالب ریخته گری دایکاست غالبا از فولاد یا آلومینیوم ساخته شده و به صورتی طراحی میشود که در برابر دما و فشارهای بالا در فرایند دایکاست مقاومت داشته باشد. برای این منظور قالب با ماشین کاری تولید میشود.
در این مرحله همچنین در دیوارههای داخلی قالب یک روانکننده اعمال میشود. اعمال روانکننده در قالب بسیار اهمیت دارد؛ زیرا باعث تنظیم دمای قالب شده و همچنین یک لایه بین فلز مذاب و قالب ایجاد میکند که باعث جداسازی راحتتر قطعه ریخته گری شده میشود.
هرچه ابعاد قالب و دستگاه بزرگتر باشد، تمیزکاری و روانکاری قالب بیشتر طول میکشد. همچنین در دستگاههای بزرگ باز و بسته کردن قالبها در زمان طولانیتری انجام میشود. همانطور که گفته شد، قالبهای دایکاست دو قسمت متحرک و ثابت دارند که در این مرحله، قسمت متحرک قالب روی صفحه متحرک و قسمت ثابت آن روی صفحه ثابت نصب میشود.
در مرحله آماده سازی قالب تمیز کردن قالب، روانکاری و بستن آن بسیار اهمیت دارد و باید با دقت و مهارت بالا انجام شود.
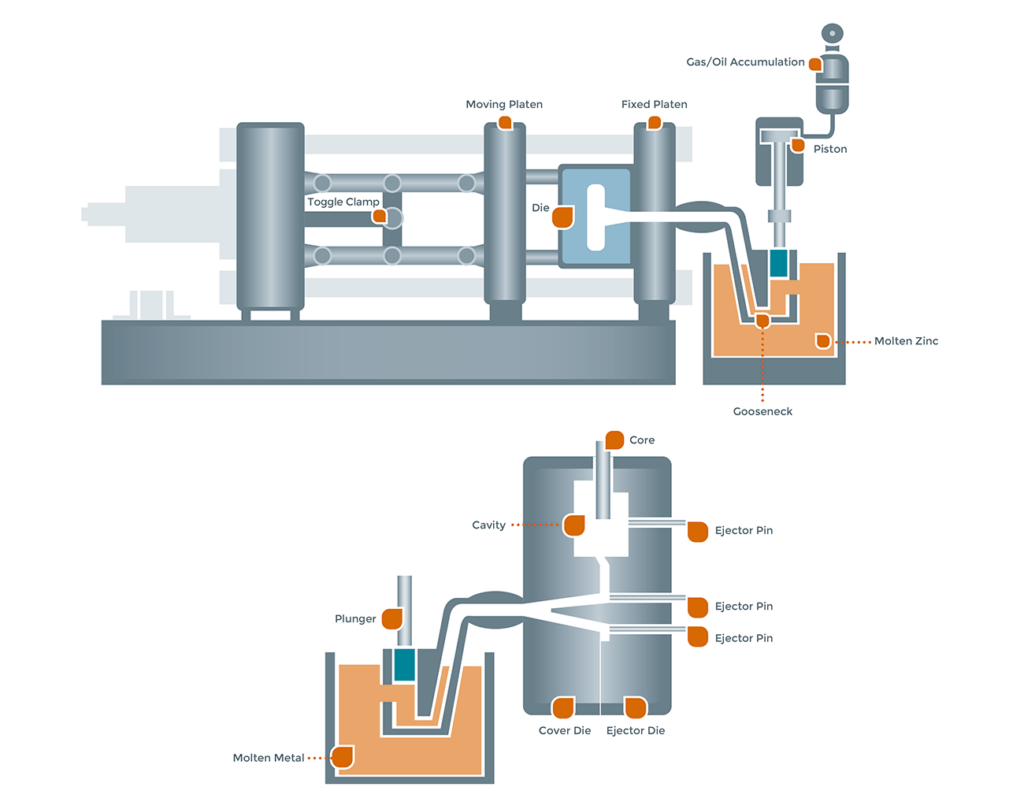
آماده سازی مواد اولیه فلزی (Metal Preparation)
در این مرحله، مواد اولیه فلزی برای تزریق آماده میشوند. آلیاژهایی که در ریخته گری دایکاست مورد استفاده قرار میگیرند، غالبا فولاد، آلومینیوم، منیزیم یا روی میباشند. این فلزات یا آلیاژها در کوره ذوب شده و پس از ذوب شدن در ملاقه (ladle) ریخته میشوند. با این کار برای قرار گرفتن در قسمت تزریق دایکاست آماده میشوند.
فرآیند تزریق (Injection process)
پس از اینکه قالب و مواد اولیه مورد نیاز آماده شدند، فلز مذاب به درون قالب تزریق میشود. در این مرحله، قالب مورد استفاده باید کاملا بسته باشد؛ در غیر اینصورت قالب نمیتواند فلز مذاب با فشار بالا را پذیرش کند. با توجه به عوامل متعدد و کاربردهای مختلف، فلز مذاب با فشاری بین 1500 تا 25000 پوند بر اینچ مربع (PSI) به درون قالب تزریق خواهد شد. این فشار تا زمانی که فلز سرد و منجمد شود، در قالب حفظ میشود.
تخلیه حفره (Ejection)
در این مرحله، حفره تازه تولید شده از درون قالب بیرون کشیده میشود. غالبا اکثر قالبها دارای یکسری پینهای اجکتوری هستند و زمانی که درگیر میشوند، حفره را آزاد میکنند. در صورتی که فلز خام هنوز مایع باشد، باید مدت زمان دیگری صبر کرد تا فلز خنک شده و بتواند حفره را از قالب خارج کند. پس از اینکه فلز کاملا سرد و سفت شود، قالب باز شده و قطعه از درون قالب خارج میشود.
پرداخت نهایی قطعه (Finishing process)
در آخرین مرحله از ریخته گری دایکاست، پرداخت، تکان دادن یا برش کاری قطعه انجام میشود. در این مرحله، تمام ضایعات فلزی احتمالی از حفره تازه ایجاد شده جدا میشوند. به عبارتی، در ریخته گری دایکاست تمام مواد فلزی مذاب شده برای فرایند ریخته گری استفاده نشده و مقداری از آن داخل قالب گیر میکند. در نتیجه، قبل از استفاده مجدد از قالب، این ضایعات فلزی باید برداشته شوند.
پرداخت نهایی قطعه نقش مهمیدر کیفیت آن و در فرایند ریخته گری دایکاست دارد؛ زیرا روی عملکرد و دوام قطعه بسیار تاثیرگذار است. برخی فرایندهای مکمل استاندارد نیز مانند آنودایز، پوشش پودری، آبکاری، سخت کاری سطحی و… نیز غالبا روی قطعه تولید شده انجام میشوند.
کاربرد ریخته گری تحت فشار
ریخته گری دایکاست یا ریخته گری تحت فشار یکی از کاربردیترین روشها برای ساخت قطعاتی با شکلهای پیچیده، ابعاد دقیق، ساختار یکپارچه، قطعاتی با سطح باکیفیت، مقاومت بالا و سختی مطلوب است. به دلیل همین ویژگیها و مزایا این روش کاربرد گستردهای در تولید قطعات و تجهیزات صنعتی بخصوص قطعات صنعت خودروسازی دارد؛ تا جایی که میتوان گفت در حدود 60 درصد از قطعات ریخته گری شده در صنعت اتومبیل سازی با استفاده از فرایندهای ریخته گری دایکاست یا تحت فشار ساخته میشوند.
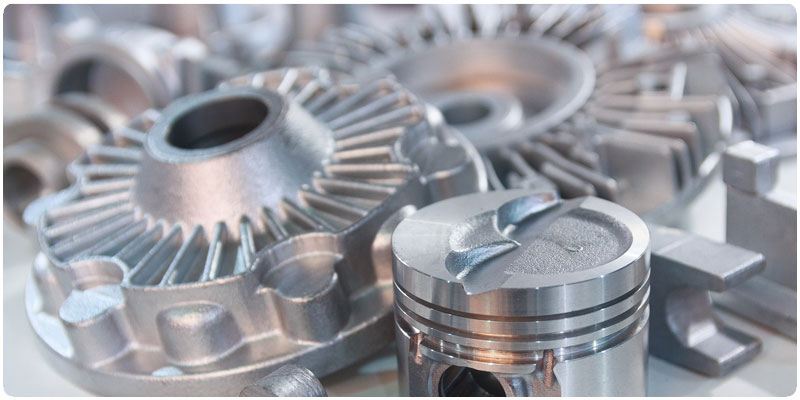
علاوه بر صنعت خودروسازی، این فرایند در تولید قطعات صنایعی مانند هوافضا، تجهیزات الکترونیکی، ساخت لوازم خانگی و جواهرسازی نیز کاربرد دارد. چراغ دایکاست مانند چراغهای شهری و لوسترهای دایکاست، ظروف دایکاست مانند قابلمههای چدنی دایکاست، رادیاتور اتومبیل دایکاست و چرخ دایکاست از جمله شناخته شده ترین لوازم و قطعات ساخته شده توسط ریخته گری دایکاست هستند. در کنار این لوازم، لوازم و قطعات صنعتی و غیر صنعتی بسیاری وجود دارند که با استفاده از ریخته گری تحت فشار تولید میشوند.
مزایا ریخته گری تحت فشار
ریخته گری قطعات فلزی و غیرفلزی با استفاده از فرایند دایکاست مزایای زیادی را به همراه دارد که از جمله مهمترین این مزایا میتوان به موارد زیر اشاره کرد:
- قطعاتی که با استفاده از دایکستینگ تولید میشوند، کیفیت بالایی دارند و نسبتا ارزانتر هستند.
- از این روش میتوان برای تولید قطعات در تعداد بالا و حجم زیاد نیز استفاده کرد.
- به دلیل فرایندهای نیمه خودکار یا خودکار دستگاههای دایکاست، هزینه نیروی کار در این روش کمتر است.
- امکان تولید قطعات با اشکال پیچیده و تلرانسهای محدود در این روش وجود دارد.
- فرایند دایکاست یک فرایند نسبتا سریع است.
- به دلیل فشار زیاد مورد استفاده در طول فرایند دایکستینگ، امکان تولید قطعات با دیوارههایی به نازکی 0.38 میلیمتر فراهم است.
- قطعات تولید شده در این فرایند سطوح بسیار صافی دارند.
- این روش دقت ابعادی عالی و کیفیت سطح مطلوبی را ارائه میدهد.
- در این روش امکان تولید قطعات کوچکتر با استفاده از قالبهای چند حفره وجود دارد.
- از این روش میتوان برای ریخته گری انواع فلزات اعم از آلومینیوم، روی و منیزیوم استفاده کرد.
- ضایعات مواد در این روش به میزان حداقل است.
- در این روش فلز مذاب به سرعت در دیوارههای قالب خنک میشود و همچنین قالب ریخته گری دارای ریزدانه سخت با استحکام عالی است. به همین دلیل در این روش ضخامت دیواره کاهش پیدا میکند اما نسبت مقاومت به وزن اجزای دایکاست افزایش خواهد یافت.
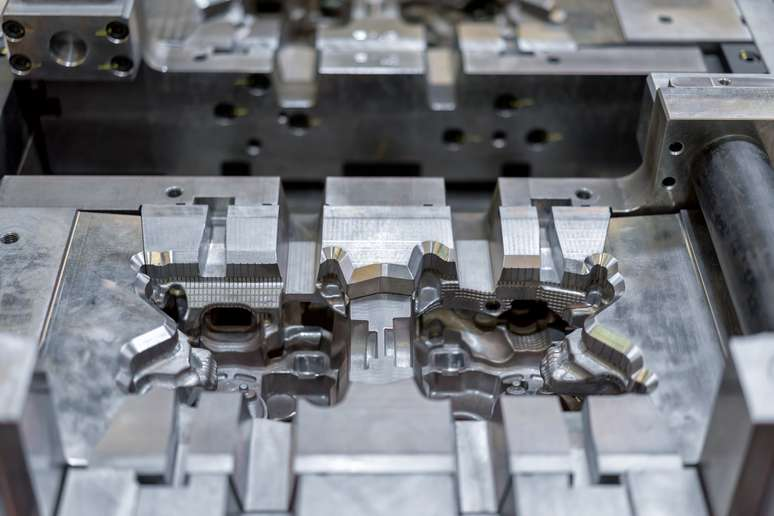
معایب ریخته گری تحت فشار
در کنار تمامیاین مزایا، ریخته گری تحت فشار یکسری معایب را نیز شامل میشود که عبارتند از:
- استفاده از تجهیزات ریخته گری تحت فشار تنها برای تولید قطعات در حجم بالا و تعداد زیاد مقرون به صرفه است.
- این روش برای ریخته گری فلزات و آلیاژهایی با نقطه ذوب بالا مناسب نیست.
- به دلیل محدودیت، امکان طراحی قالب و فرایند ریخته گری برای قطعات بزرگ در این روش فراهم نمیباشد.
- طراحی و ساخت قالب در این روش زمان و هزینه بالایی را شامل میشود.
- تغییرات احتمالی مورد نیاز در طراحی قطعه زمانبر و پرهزینه است.
- تخلخل ناشی از هوا و گازهای محبوس شده در این روش روی یکپارچگی قطعه تاثیرگذار هستند. (گرچه روش ریخته گری دایکاست تحت خلاء این تخلخل را کاهش میدهد)
سوالات متداول
ریخته گری دایکاست و قالب گیری تزریقی چه تفاوتی با یکدیگر دارند؟
تفاوت این دو روش، در ماده مورد استفاده برای ساخت قطعات است. ریخته گری دایکاست یا تحت فشار برای تولید قطعات فلزی بخصوص قطعات آلومینیومی در ابعاد کوچک تا متوسط و در تعداد انبوه است. در صورتی که قالب گیری تزریقی برای ساخت قطعات پلاستیکی مورد استفاده قرار میگیرد.
چگونه میتوان روش ریخته گری دایکاست مناسبی را انتخاب کرد؟
نوع فرایند و نوع دستگاه ریخته گری دایکاست، بر اساس فلزات مورد استفاده انتخاب میشود. غالبا در صورتی که ریخته گری روی، قلع و یا سرب موردنیاز باشد، از دستگاه ریخته گری دایکاست با محفظه داغ استفاد میشود. از طرفی، در صورتی که به ریخته گری فلزات با نقطه ذوب بالا مانند آلومینیوم یا آلیاژهایی با محتوای آلومینیوم و یا مس نیاز باشد، از دستگاه ریخته گری محفظه سرد استفاده میشود.
جمع بندی
ریخته گری دایکاست یکی از روشهای متداول ریخته گری فلزات است که فرایند ریخته گری در انواع روش های ریخته گری تحت فشار انجام میشود. این فرایند با استفاده از دو نوع دستگاه محفظه سرد و محفظه گرم انجام میشود که هر کدام بسته به کاربردها و ویژگیهایی که دارند در فرایندهای مختلف ریخته گری تحت فشار مورد استفاده قرار میگیرند.
روش ریخته گری تحت فشار به عنوان یکی از سریعترین روشهای تولید قطعات و محصولات فلزی شناخته میشود که غالبا مقرون به صرفه میباشد؛ به همین دلیل کاربرد بسیاری در صنایع مختلف دارد. در حال حاضر این روش به عنوان یکی از متداولترین روشهای تولید قطعات صنعتی شناخته میشود.