یکی از روشهای متداول قالب گیری، روش قالب گیری فشاری (Compression Molding) است. در این روش، مواد اولیه مورد استفاده در ابتدا تحت حرارت قرار گرفته و در یک حفره قالب گیری گرم و باز قرار داده میشوند. پس از آن، قالب توسط یک نیروی فوقانی و با یک درپوش بسته شده و تحت فشار زیاد، مواد درون آن شکل قالب را به خود میگیرند. در طی این فرایند فشار تا زمان قرار گرفتن ماده در تمامی بخشهای قالب ادامه دارد و گرما و حرارت فرایند نیز حفظ میشوند.
در مرحله نیمه فرآوری شده فرایند قالب گیری فشاری غالبا از رزینهای ترموست استفاده میشود که ممکن است به شکل ذرات، مواد پیش ساخته و یا بتونه مانند باشند. ترموستها همچنین به صورت پیش گرم شده مورد استفاده قرار گرفته و ایجاد اضافات را به طور موثری کاهش میدهند. به صورتی که در قالب خروجی سطوح اضافه وجود نداشته و دوام محصول نهایی با این قابلیت افزایش مییابد. این فرایند با فشار بسیار بالایی عمل میکند و برای تشکیل مواد تقویت شده به کمک فایبرگلاس با استحکام بالا بسیار کاربرد دارد.
همچنین امکان ایجاد ترموپلاستیکهای ترکیبی پیشرفته به شکل نوارهای تک جهت، پارچههای بافته شده، الیاف جهت دار متناوب و یا رشتههای خرد شده وجود دارد.
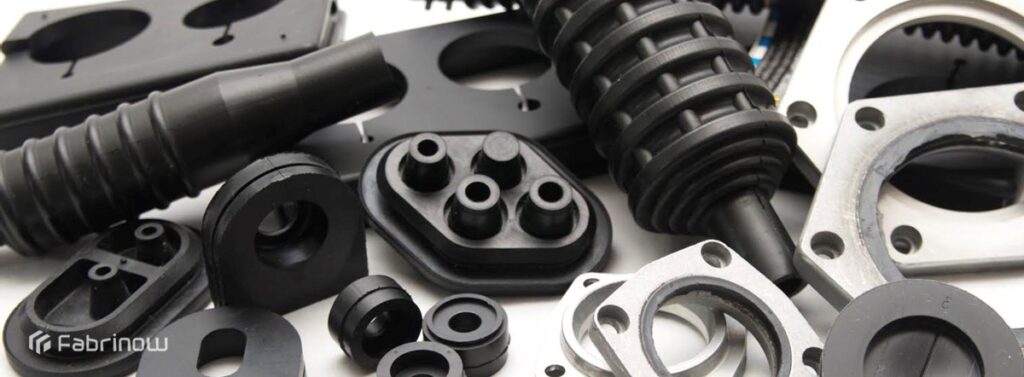
فرایند قالب گیری فشاری نسبت به روشهای قالب گیری دیگر مانند روش انتقالی و یا تزریقی هزینه کمتری دارد و هدر رفت مواد اولیه نیز در این روش کمتر است. اولین بار این فرایند برای تولید قطعاتی استفاده میشد که در بسیاری از محصولات جایگزین فلزات میشدند اما امروزه این فرایند برای ساخت محصولات مسطح و منحنی با جنسهای مختلف پلاستیک، لاستیک و کامپوزیت بسیار کاربرد دارد. در این فرایند هرچه مواد اولیه صاف تر و هموار تر روی سطح قالب پخش شوند، برون ریز (شارش) به وجود آمده در طی مرحله فشرده سازی کمتر خواهد بود.
مراحل و فرایند قالب گیری فشاری
همانطور که گفته شد، قالب گیری فشاری یکی از روشهای شکل دهی مواد پلاستیکی و یا کامپوزیتها است. فرایند این روش در تولید محصولات گوناگون، شامل یک سری مراحل مختلف است؛ که عبارتند از:
- قبل از شروع فرایند قالب گیری فشاری، ابتدا قالبهای مورد نیاز طراحی و تولید میشوند. قالبهای فشاری معمولا از جنس فولاد و یا آلومینیوم هستند که در طراحی و تولید آنها الزامات ابعادی مورد نیاز قطعه نهایی با دقت بالا در نظر گرفته میشوند. همچنین این قالبهای دارای یک قالب بالا، یک قالب پایین و یک حفره (فاصله میان قالب بالا و پایین) میباشند.
- پس از تولید، قالبها آماده و راه اندازی میشوند. برای این منظور قالب تمیز شده و گرمایش آن، بسته به نوع ماشین آلات مورد استفاده، روشن میشود. همچنین نوعی از مواد قالب گیری مانند ورقهای SMC (Sheet Molding Compound) در قالب داغ قرار گرفته و به اصطلاح پیش شارژ میشوند. ابعاد پیش شارژ قالب به صورتی است که بتواند حدود 50 درصد از سطح قالب را پوشش داده و وزن پیش شارژ نیز غالبا قبل از قرار گرفتن در قالب اندازهگیری میشود.
در قالبهای فشاری، موقعیت پیش شارژ یا کنترل دما، به خصوص برای مواد ترموست، بسیار اهمیت دارد؛ زیرا به طور مستقیم روی کیفیت قطعه، جهتگیری الیاف، تشکیل خط کشباف و فضای خالی تاثیرگذار است.
- پس از آن، مواد اولیه مورد نیاز برای فرایند انتخاب میشوند. این مواد اولیه غالبا دو نوع اصلی ترموستها و ترموپلاستیکها را شامل میشوند.
ترموستها که معمولا رزین تقویتشده با الیاف، لاستیک یا سیلیکون را شامل میشوند، در حفره گرم شده قالب قرار گرفته و پس از بسته شدن قالب با سرعت و فشار برنامهریزی شده، این مواد با واکنش شیمیایی اتصال عرضی تحت فشار و دما قرار گرفته و پخته میشوند. پس از پخته شدن نیز فشار، آزاد شده، قطعه از قالب خارج میشود و رزینهای اضافی نیز به صورت دستی بریده میشوند.
اما در فرایند ترموپلاستیکها از قالبهای خنککننده با کنترل دما استفاده شده و پس از سفت شدن ماده ترموپلاستیک در قالب، میتوان آن را خارج کرد. در قالب گیری فشاری، ترموپلاستیکها قبل از ورود به حفره قالب ذوب میشوند. فرایند پر کردن قالب و اطمینان از پوشش کامل حفره با مواد ذوب شده نیز به واسطه طراحی و اجرای فرایند قالبگیری مدیریت میشود.
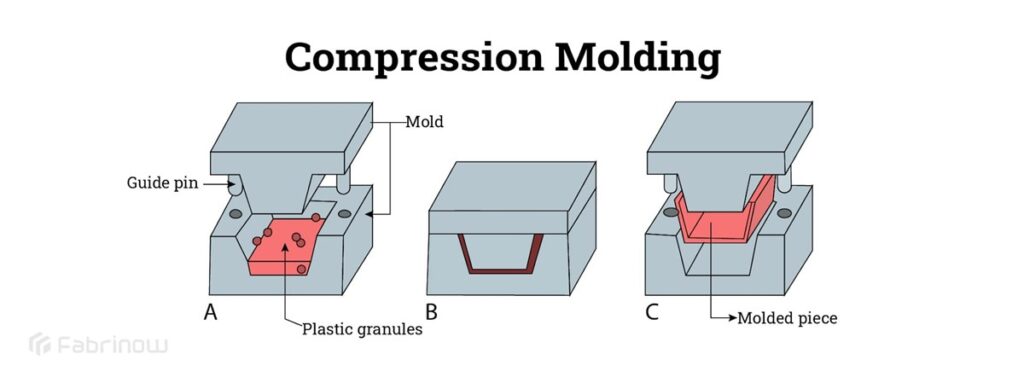
- زمانی که پیش شارژ در قالب قرار میگیرد، قالب بالایی با سرعت بالا به سمت پایین حرکت میکند تا سطح بالایی در معرض مواد پیش شارژ قرار بگیرد. پس از آن، قالب با سرعت پایینی در حدود 5 تا 10 میلیمتر بر ثانیه به سمت پایین حرکت میکند تا مواد پیش شارژ فشرده شوند.
همزمان با بسته شدن قالب و افزایش فشار قالب گیری، مواد پیش شارژ برای پر کردن حفره قالب جریان مییابد و با این کار هوا از طریق لبههای برشی یا دریچههای هوای قالب خارج میشود. در این مرحله، مهمترین عواملی که روی عملکرد فرایند و کیفیت محصول تاثیرگذار هستند، سرعت بسته شدن قالب و دمای قالب است.
- در این مرحله، پخت مواد انجام میشود. پس از اینکه حفره قالب به طور کامل با مواد پیش شارژ پر شد، قالب در حالت بسته میماند و فشار قالب نیز برای مدت زمان مشخصی حفظ میشود. در این مدت، مواد، پخته شده و قطعه به صورت یکپارچه ایجاد میشود. در این مرحله، زمان مورد نیاز برای پخت کاملا به فرمولاسیون مخلوط رزین، ضخامت قطعه و دمای قالب بستگی دارد.
- پس از پختن رزین و جامد شدن قطعه، با کمک پینهای اجکتور، قطعه از قالب خارج شده و خنک میشود. در برخی موارد ممکن است نیاز به صاف کردن سطح قطعه و بریدن مواد اضافه در آن، وجود داشته باشد. همچنین در این مرحله، سطح قالب نیز تمیز شده و برای چرخه قالب گیری بعدی، یک عامل آزادکننده قالب خارجی یا همان رهاساز روی سطح قالب اعمال میشود.
برای فرایند قالب گیری فشاری، اندازهگیری صحیح مواد بکار رفته، استفاده از روش مناسب برای گرم کردن مواد، مصرف بهینه انرژی در زمان گرم کردن مواد و بهینهسازی زمان اجرای فرایند بسیار اهمیت دارند. همچنین پیشبینی کامل نیروهای مورد نیاز برای پخش مواد و طراحی سیستم خنک کننده سریع پس از اتمام فرایند نیز از عوامل مهم و موثر در فرایند قالب گیری فشاری و کیفیت قطعات تولید شده در این فرایند میباشند.
تجهیزات مورد استفاده در قالب گیری فشاری
در طی فرایند قالب گیری فشاری، علاوه بر قالب، از لوازم و تجهیزات متعددی استفاده میشود؛ که عبارتند از:
- پرس با تناژ بالایی بین 150 تا 2500 تن
- قالبی مطابق با قطعه مورد نیاز با دو نیمه بالایی و پایینی داشته که با دقت ماشین کاری شده و قبل از شروع فرایند پیش گرم میشود.
- حفرههای قالب که باید طراحی دقیقی برای قرارگیری مواد و توزیع مناسب آنها در طول فرایند قالب گیری داشته باشند.
- اتاق گرمایش یا فر جداگانه برای گرم کردن مواد تا دمای ذوب
- عناصر گرمایش اولیه شامل مقاومتهای الکتریکی استوانهای بلند
- سیستم هوای فشرده برای تمیز کردن قالب، حذف مواد اضافی از حفره قالب و سطح قطعه
- سیستمهای اتوماسیون شامل نوار نقاله، بازوهای رباتیک و قیف
- دستگاههای کنترل و نظارت دما
- سیستمهای تخلیه مکانیکی
انواع قالب فشاری
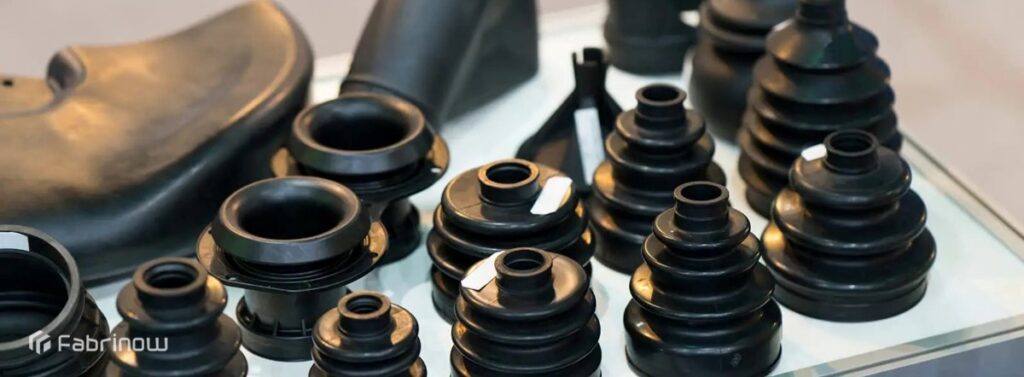
ساختمان قالبهای فشاری با یکدیگر متفاوت است. به عبارتی این قالبها بسته به مبنای اجازه ورود مواد به کانال فلاش، انواع مختلفی دارند؛ که عبارتند از:
- قالب فشاری فلاش دار (flash die)
در این نوع از قالبهای فشاری، فشار ایجاد شده روی قالب، به واسطه پرس، باعث میشود که مواد اضافی به سادگی به کانال فلاش راه داشته باشند. در این قالبها، فلاش معمولا به صورت افقی است.
در استفاده از قالبهای فشاری فلاشدار، معمولا علاوه بر هزینه طراحی و ساخت، باید هزینهای برای سنگ زدن پلیسه ایجاد شده در اطراف قطعه در نظر گرفته شود. در واقع، این هزینه اضافی از معایب این قالبها محسوب میشود. اما به طور کلی این قالبها ارزانتر و سادهتر هستند.
از این قالبها برای تولید قطعات با استفاده از مواد پلاستیکی با ضریب بالک پایین استفاده میشود. ضریب بالک حاصل تقسیم حجم مواد فرم نگرفته به مواد فرم گرفته است که در فرایند تولید بسیار اهمیت دارد. همچنین قالبهای فشاری فلاشدار در تولید قطعاتی که رعایت ضخامت دیوارههای آنها اهمیتی ندارد نیز کاربرد دارند. گرچه یکنواختی ضخامت دیوارهها غالبا به دقت میلههای راهنما بستگی دارد.
- قالب فشاری سنبهای کفی یا پلهای (flat die)
این قالبها همانند قالبهای فلاشدار هستند با این تفاوت که در قالبهای سنبهای، یک محفظه بار به قالب اضافه شده است. این قالبها، نسبت به قالبهای فلاشدار، قطعات را با دانسیته یا چگالی بیشتری تولید میکنند. همچنین غالبا دارای 3.16 اینچ عرض هستند تا از خروج مواد اضافی که از بین سنبه و محفظه نشت میکنند، محافظت کنند.
از این قالبها، برای تولید قطعات با پینهای کوچک و مقاطع ظریف استفاده میشود. همچنین در این قالبها، مانند قالبهای فلاشدار، نسبت به قبل، سنگزنی فلاش یا پلیسه با مقدار کمتری لازم است.
- قالب فشاری مثبت (positive die)
در این قالبها، نسبت به دو نوع قبلی، فضای کمتری برای خروج مواد اضافی به داخل کانال فلاش تعبیه شده است. سنبه قالبهای مثبت، در محفظه قالب دارای انطباق کاملا جذب بوده و ترانس نیز در هر طرف 0.003 اینچ است.
از این قالبها برای قالب گیری مواد با فیلر پارچهای و قطعات عمیق مانند محفظه رادیو استفاده میشود و در این زمینهها، بسیار کاربردی بوده و نسبت به سایر قالبها بهتر عمل میکنند.
در این قالبها، پلیسه یا فلاش به صورت عمودی است و به سادگی برطرف میشود. اما سنبه این قالبها باعث خراشیدگی محفظه قالب شده که این موضوع میتواند به طور مستقیم روی قطعه تاثیرگذار باشد. این مورد از مهمترین معایب قالبهای فشاری مثبت محسوب میشود.
- قالب فشاری نیمه مثبت (semi-positive die)
این قالبها، از یک قالب سنبهای پلهدار و یک قالب مثبت تشکیل میشوند. پلیسه یا فلاش ایجاد شده توسط این قالبها به سادگی توسط سنگ برطرف میشود و لقی بین سنبه ماتریس نیز 0.001 اینچ در هر طرف خواهد بود.
از قالبهای نیمه مثبت برای ساخت قطعات با عمق زیاد و قطعاتی که در ته آنها مقاطع بزرگی قرار دارد، استفاده میشود. همچنین این قالبها در تولید قطعاتی که در برخی از مقاطعشان اختلاف ضخامت وجود دارد نیز، کاربرد دارند و از آنها میتوان برای فرم دادن ملامینها و ترکیبات اورهای نیز استفاده کرد.
قالبهای نیمه مثبت با نام قالبهای ویژه نیز شناخته میشوند و معمولا به صورت چند محفظهای و با محفظه باردهی مشترک ساخته میشوند؛ تا جایی که در برخی موارد ممکن است بیشتر از 100 محفظه در آنها تعبیه شود.
مواد مورد استفاده در قالب گیری فشاری
همانطور که گفته شد، در روش قالب گیری فشاری به طور کلی از ترموستها و یا ترموپلاستیکها استفاده میشود. قالب گیری فشاری همچنین طیف وسیعی از ترموستها و ترموپلاستیکها را شامل میشود که رایجترین و اصلیترین آنها عبارتند از:
- اپوکسی (Epoxy)
رزینهای اپوکسی با داشتن خواص بینظیر مانند خواص مکانیکی عالی، پایداری ابعادی و مقاومت حرارتی بالا، در قالب گیری فشاری کاربرد زیادی دارند. این رزینها در زمان ذوب به سادگی جریان پیدا کرده و تمام حفرههای قالب را در طول فرایند فشردهسازی به طور کامل پر میکنند.
قطعاتی که با استفاده از این رزینها ساخته میشوند، استحکام و دوام بالایی داشته و برای صنایعی که نیاز به قالب گیری با استحکام بالا دارند مانند صنعت ساخت قطعات هوافضا و صنعت ساخت عایقهای الکتریکی بسیار کاربرد دارند.
- سیلیکون (Silicone)
سیلیکونها مقاومت حرارتی بالا و خواص الکتریکی مطلوبی دارند و میتوانند خواص فیزیکی خود را در یک گستره دمایی وسیع نیز حفظ کنند. این مواد همچنین دارای انعطافپذیری مطلوبی هستند. مواد سیلیکونی همانند رزینهای اپوکسی به سادگی جریان مییابند و با حفرههای پیچیدهترین قالبها نیز انطباق پیدا میکنند. از این مواد اولیه غالبا برای تولید آببندهای دقیق، واشرها، تجهیزات پزشکی و قطعات خودرو استفاده میشود.
- ملامین (Melamine)
رزینهای ملامین نیز مقاومت حرارتی بالایی دارند و مقاومت شیمیایی و سختی آنها بسیار مناسب است. این مواد اولیه به سادگی قالب گیری میشوند و با استفاده از آنها میتوان قطعاتی با پرداخت سطح عالی و پایداری ابعادی تولید کرد.
از رزینهای ملامین غالبا در قالب گیری فشاری برای تولید ظروف آشپزخانه، لمینتهای تزئینی، قطعات الکتریکی و ظروف مقاوم در برابر حرارت استفاده میشود.
- اورتان (Urethane)
مواد اورتان که با نام پلی اورتان نیز شناخته میشوند، دارای خواصی مانند چقرمگی بالا، مقاومت در برابر سایش و استحکام ضربهای هستند. از اورتانها میتوان به صورتی استفاده کرد که طیف گستردهای از خواص فیزیکی را ارائه دهند و با کاربردهای مختلف تطبیق داشته باشند. این مواد همچنین در طول فرایند قالب گیری فشاری به خوبی جریان پیدا میکنند و به همین دلیل از آنها میتوان برای طراحیهای پیچیده قالب و تولید قطعاتی مانند چرخها، غلتکها، قطعات خودرو و آببندهای صنعتی استفاده کرد.
- پلی اتیلن با چگالی بالا یا HDPE (High-density Polyethylene)
این مواد اولیه یک نوع ترموپلاستیک هستند که استحکام، مقاومت شیمیایی و سختی بالایی داشته و به همین دلیل در قالب گیری فشاری بسیار پرکاربرد هستند. این مواد نیز در طول فرایند قالب گیری فشاری به راحتی ذوب شده و در قالب جریان مییابند. در اینصورت با دقت میتوانند حفرههای قالب را کاملا پر کنند.
قطعاتی که با استفاده از این پلی اتیلنها در قالب گیری فشاری ساخته میشوند دارای مقاومت ضربهای و پایداری ابعادی بالایی هستند. از این مواد غالبا برای ساخت قطعات خودرو و سایر قطعات صنعتی استفاده میشود.
- سولفید پلی فنیلن یا PPS (Polyphenylene Sulfide)
این مواد نیز از انواع ترموپلاستیکها هستند که دارای خواصی مانند مقاومت شیمیایی بالا، عدم اشتعالپذیری و پایداری ابعادی میباشند. سولفیدهای پلی فنیلن همچنین خواص جریانی مطلوبی دارند و در طول فرایند قالب گیری فشاری کلیه حفرههای قالب را به طور کامل پر میکنند. قطعاتی که با استفاده از این مواد ساخته میشوند دارای استحکام و سفتی بالایی هستند و برای تولید قطعات الکتریکی، قطعات خودرو و تجهیزات صنعتی بسیار کاربرد دارند.
- پلی تترافلوئورواتیلن یا PTFE (Polytetrafluoroethylene)
این مواد نوعی فلوئور و پلیمر ضد چسبندگی هستند که دارای خواص مقاومت شیمیایی مطلوب و پایداری دمایی بالایی میباشند. این مواد همچنین خواص الکتریکی بالایی ارائه میدهند و ضریب اصطکاک پایینی دارند. پلی تترافلوئورواتیلن در قالب گیری فشاری بسیار کاربرد دارد و در طی فرایند این قالب گیری به سادگی جریان مییابد. به همین دلیل میتوان از آن برای تولید قطعات پیچیده و دقیقی مانند واشرها، یاتاقانها، آببندها و اجزای عایق الکتریکی استفاده کرد.
کاربردهای قالب گیری فشاری
فرایند قالب گیری فشاری، ویژگیهای متعددی را ارائه میدهند. این نوع قالب گیری در تولید قطعات با مقاطع پیچیده و قطعات دقیق بسیار کاربرد دارد. در واقع از این فرایند قالب گیری میتوان برای تولید قطعات با مقاطع پیچیده، قطعات دارای سوراخهای کوچک و عمیق، قطعات با پلیسه کمتر و قطعات با وزن سنگینتر و… استفاده کرد. به همین دلیل، میتوان گفت که قالب گیری فشاری طیف وسیعی از کاربردها را شامل میشود.
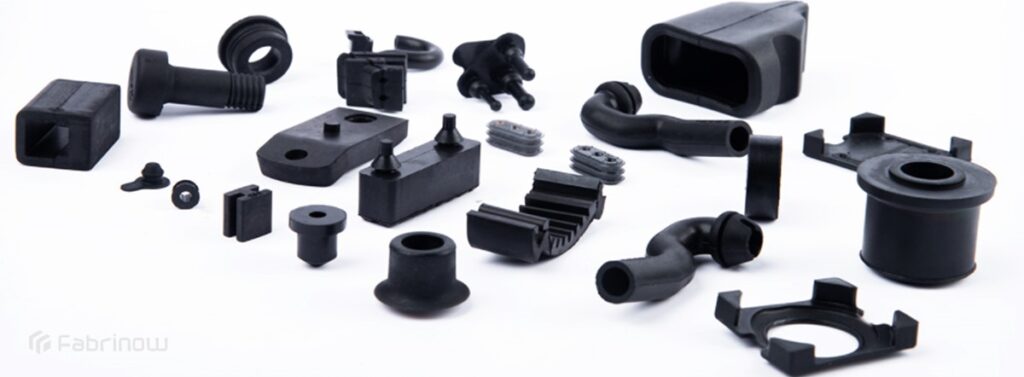
از جمله مهمترین کاربردهای این فرایند در صنایع مختلف میتوان به موارد زیر اشاره کرد:
- ساخت لوازم آشپزخانه
از فرایند قالب گیری فشاری میتوان برای ساخت لوازم آشپزخانه مانند کاسهها، فنجانها، بشقابها و بخصوص لوازمی که از جنس ملامین هستند در اشکال متنوع استفاده کرد. در اینصورت قالب گیری فشاری منجر به تولید این محصولات و لوازم با دوام بالا و استحکام عالی شده و امکان تولید انبوه و کارآمد آنها را به سادگی فراهم میکند.
- ساخت قطعات خودرو
از فرایند قالب گیری فشاری برای تولید قطعات و پنلهای بزرگ برای خودروها و سایر وسایل نقلیه مانند تراکتورها بسیار استفاده میشود. همچنین از این فرایند میتوان برای تولید قطعات پلاستیکی به کار رفته در اجزای داخلی وسایل نقلیه مانند پنل جلوی ماشین، دربها، قطعات موتور و سایر اجزایی مانند کیسه هوا، کمربند ایمنی و داشبورد با دقت و کارآمدی بالا استفاده کرد.
- ساخت تجهیزات هوافضا
فرایند قالب گیری فشاری در صنعت هوافضا نیز بسیار پرکاربرد است. در صنعت هوافضا از این فرایند میتوان برای ساخت اجزای ساختاری هواپیما مانند بالهای هواپیما، بدنه و اجزای موتور هواپیما مانند پرههای توربین و تیغههای فن استفاده کرد.
- ساخت قطعات الکتریکی
در صنایع الکتریکی، از قالب گیری فشاری میتوان برای تولید سوکتهای الکتریکی، صفحه کلیدها، کنتورها، سوئیچها و … استفاده کرد. همچنین این فرایند در تولید بردهای مدار یا سایر شکلهای که به ابعاد دقیق و دقت بالایی نیاز دارند، بسیار کاربرد دارد. در واقع، این فرایند در تولید قطعات الکتریکی منجر به تولید قطعات و لوازم با شکلهای دقیق شده و عملکرد آن برای این محصولات کاملا کاربردی و قابل اعتماد خواهد بود.
- ساخت تجهیزات کامپیوتری
یکی از کاربردهای رایج قالب گیری فشاری، تولید اجزای مورد نیاز برای کنترلرهای بازیهای ویدئویی، صفحه کلیدها و سایر تجهیزات مشابه است. در این روش از مواد با خواصی مانند مقاومت ضربهای، پایداری ابعادی و عایق الکتریکی میتوان برای تولید این تجهیزات استفاده کرد. همچنین با توجه به امکان پرداختهای سطحی دلخواه و تولید انبوه، فرایند قالب گیری فشاری یکی از روشهای پرکاربرد برای تولید قطعاتی با دقت بالا، راحت برای کاربر و قطعاتی دارای دوام بالا در تولید بازیهای ویدئویی و تجهیزات کامپیوتری است.
- ساخت تجهیزات پزشکی و دندانپزشکی
از فرایند قالب گیری فشاری در صنعت پزشکی میتوان برای تولید قطعات پلاستیکی و سیلیکونی مانند ماسکهای تنفسی و درپوش سرنگها استفاده کرد. همچنین در این صنایع از این فرایند برای تولید ایمپلنتهای ارتوپدی و پروتزها نیز استفاده میشود. در واقع، این فرایند به دلیل امکان تولید اجزای دقیق و با کیفیت بالا، در تولید تجهیزات و لوازم پزشکی و دندانپزشکی بسیار کاربرد دارد.
ویژگیها، مزایا و معایب قالب گیری فشاری
قالب گیری فشاری ویژگیهای متعددی را ارائه میدهد. در واقع ویژگیهای متنوع این فرایند منجر به کاربرد گسترده آن در صنایع مختلف شده است. از جمله مهمترین مزایای فرایند قالب گیری فشاری میتوان به موارد زیر اشاره کرد:
- در طی این فرایند فشار زیادی به مواد وارد شده و انباشتگی متراکم مواد به واسطه این فشار، منجر به تولید محصولات و قطعاتی مستحکم و پایدار از لحاظ ساختاری میشود.
- این فرایند با ضخامتهای مختلف کاملا سازگار است و با استفاده از قالبهای سفارشی در این فرایند امکان تولید قطعاتی با هندسهها، بافتها و ساختارهای یکپارچه وجود دارد.
- این فرایند با طیف وسیعی از مواد نیز سازگار است و هم از مواد ترموست و هم از مواد ترموپلاستیک در این فرایند میتوان برای کاربردهای مختلف استفاده کرد.
- در فرایند قالب گیری فشاری از مواد به صورت کارآمد استفاده شده و غالبا منجر به کاهش هزینههای تولید اعم از هزینههای استفاده از مواد خام و هزینه کلی تولید میشود.
- اعمال فشار بالا در این روش قالب گیری منجر به ایجاد سطوحی صاف و یکدست میشود و به همین دلیل از این فرایند میتوان برای تولید قطعات با کیفیت سطح عالی استفاده کرد.
- با استفاده از فرایند قالب گیری فشاری امکان تولید انبوه و به عبارتی امکان قالب گیری همزمان چندین قطعه در یک سیکل فراهم میشود.
- استفاده از سیستمهای خودکار و پیشرفته در این فرایند منجر به افزایش بهرهوری، کاهش زمان تولید و افزایش خروجی تولید میشود.
- در این فرایند امکان استفاده از مواد بازیافتی یا رزینهای زیست پایه وجود دارد و در اینصورت وابستگی به مواد اولیه کاهش مییابد.
- در این فرایند ضایعات مواد نیز کم است و غالبا در قالبهای فشاری لوله راهگاه و کانال هدایت مواد وجود ندارد.
- فرایند قالب گیری فشاری میتواند به صورت خودکار یا دستی نیز انجام شود و به همین دلیل هزینه تجهیزاتی نسبتا اندکی را شامل میشود.
- در این فرایند جریان مواد در مدت زمان کوتاهی انجام میشود و به همین دلیل تنش در قطعه تولید شده و ساییدگی در قالب کمتر است.
- به طور کلی فرایند قالب گیری فشاری هزینه پایینی را نسبت به سایر روشهای قالب گیری مانند قالب گیری تزریقی شامل میشود.
در کنار تمامی این مزایا، قالب گیری فشاری یکسری معایب و محدودیتها را نیز شامل میشود؛ که عبارتند از:
- این روش در تولید قطعات پیچیده دارای محدودیت است. به عبارتی، به دلیل استفاده از مواد اولیه از پیش شکل گرفته، قالب باز و بازه فشار، در طراحی قطعات محدودیت وجود داشته و غالبا امکان استفاده از این فرایند برای تولید قطعات با هندسههای داخلی پیچیده و یا دیوارههای نازک وجود ندارد.
- این فرایند، نسبت به سایر روشهای قالب گیری مانند قالب گیری انتقالی و تزریقی، به دلیل اعمال فشار، اعمال حرارت و داشتن چرخههای خنک کاری، غالبا چرخه زمان طولانیتری نیز دارد.
- در این فرایند، امکان ایجاد لبههای اضافه یا فلاش وجود دارد و در صورت عدم مدیریت و نظارت میتواند باعث نیاز به انجام فرایندهای اضافی مانند برش دستی و یا لبهزدایی با نیتروژن مایع شود. این فرایندها هزینههای تولید را افزایش میدهند.
- در قالبهای فشاری، قسمتهای داخلی قالب به سادگی دچار آسیب میشوند.
- معمولا محصولات معیوبی که در این فرایند تولید میشوند مجددا قابل بازیابی نیستند.
تفاوت بین قالب گیری فشاری و تزریقی
قالب گیری فشاری و قالب گیری تزریقی از روشهای مهم و پرکاربرد صنعت برای تولید قطعات پلاستیکی محسوب میشوند. در هر دوی این فرایندها مواد پلاستیکی با گرم شدن تغییر شکل میدهند. اما این دو روش تفاوتهای مهمی وجود دارد که باعث تمایز این دو روش از یکدیگر شدهاند. این تفاوتها عبارتند از:
- طراحی فرایند این دو روش با یکدیگر متفاوت است. در قالب گیری فشاری مواد پلاستیکی حرارت داده شده با قرار گرفتن در یک حفره قالب تحت فشار قرار میگیرند تا شکل مورد نظر ایجاد شود. با این کار، پلاستیک در ابتدا ذوب شده و در قالب سرد میشود. در صورتی که در فرایند قالب گیری تزریقی، گلولههای، پلاستیکی ذوب شده و سپس تحت فشار بالا به قالب تزریق میشوند. با این کار پلاستیک مذاب حفره قالب را پر کرده و پس از سرد شدن، جامد میشود.
- قالب گیری تزریقی به دلیل فراهم نمودن امکان تولید همزمان چند قطعه بسیار سریعتر و کارآمدتر است و برای دورههای تولید با حجم بالا بسیار کاربرد دارد. در صورتی که از قالب گیری فشاری در یک زمان تنها میتوان برای تولید یک قطعه استفاده کرد.
- برای تولید قطعات پیچیده با طرحها و جزئیات پیچیده استفاده از قالب گیری تزریقی مناسبتر است. زیرا در این فرایند فشار بالا و کنترل دقیق فرایند امکان قالب گیری با جزئیات و اشکال پیچیدهتر را فراهم میکند. در صورتی که قالب گیری فشاری برای طرحها و اشکال سادهتر مناسبتر است.
- هزینه استفاده از قالبهای فرایند قالب گیری فشاری کمتر از قالبهای فرایند قالب گیری تزریقی است.
- قالب گیری فشاری برای استفاده از پلاستیکهای ترموست به دلیل عدم امکان ذوب مجدد، کاربرد بیشتری دارد و مناسبتر است. در صورتی که قالب گیری تزریقی برای مواد ترموپلاستیک به دلیل امکان ذوبهای متعدد، مناسبتر بوده و کاربرد بیشتری برای این مواد دارد.
- قالب گیری فشاری برای تولید قطعات بزرگ بسیار به صرفه است و برای موادی که ویسکوزیته بالایی دارند یا پردازش آنها دشوار است، مناسبتر میباشد و کنترل بهتری روی توزیع مواد و بهبود پایداری ابعادی ارائه میدهد. در صورتی که قالب گیری تزریقی برای تولید مقادیر انبوه قطعات کوچک تا متوسط با هندسههای پیچیده مناسب میباشد و ابزار و ماشین آلات مورد استفاده در فرایند آن هزینههای بالاتری را نیز شامل میشوند.
در واقع، هر دو روش قالب گیری فشاری و قالب گیری تزریقی در صنایع مختلف بسیار پرکاربرد هستند و هر کدام ویژگیهای خاص خود را ارائه میدهند. در اینصورت بسته به نیازهای خاص پروژه اعم از شکل مورد نیاز، مواد اولیه مورد استفاده، پیچیدگی، حجم و هزینه میتوان از هر کدام از این روشهای قالب گیری استفاده کرد.
دوام محصولات تولید شده با فرایند قالب گیری فشاری
همانطور که گفته شد، از فرایند قالب گیری فشاری برای تولید محصولات و قطعات مختلفی استفاده میشود. دوام و عمر مفید این محصولات و قطعات به عوامل مختلفی بستگی دارد که این عوامل عبارتند از:
- نوع ماده استفاده شده در فرایند: بدیهی است که مواد اولیه مختلف طول عمرهای متفاوتی نیز دارند. به عنوان مثال پلاستیکهای مهندسی مانند PPS، نسبت به پلاستیکهای رایج مانند پروپلینها عمر طولانیتر و دوام بالاتری دارند. به همین دلیل استفاده از آنها در تولید محصولات قالب گیری فشاری میتواند منجر به افزایش عمر مفید این محصولات شود.
- عمر مفید محصولات به کاربرد مورد نظر آنها نیز بستگی دارد. در واقع، محصولات و قطعاتی که در محیطهای سخت و خشن استفاده میشوند، نسبت به محصولاتی که در محیطهای داخلی و محافظتشده استفاده میشوند، دوام و عمر مفید کوتاهتری دارند.
- میزان نگهداری و مراقبت از محصولات تولید شده در فرایند قالب گیری فشاری نیز با دوام آنها مرتبط است و با مراقبت و نگهداری صحیح از این محصولات میتوان دوام و عمر مفید آنها را افزایش داد.
اما به طور کلی میتوان گفت که محصولات قالب گیری فشاری دوام و طول عمر بالایی دارند و در صورت استفاده از محصول در شرایط مناسب و مطابق با دستورالعملهای سازنده، نگهداری و تمیز کردن به موقع آنها و همچنین محافظت از آنها در برابر آسیبهای فیزیکی و شیمیایی میتوان از آنها در مدت طولانیتری استفاده کرد.
سوالات متداول
فرایند تولید قطعات با قالب گیری فشاری چگونه است؟
برای تولید قطعات در این فرایند ابتدا باید قالب تمیز شده و شارژ شود. پس از آن، قالب از طریق پرس هیدرولیک بسته شده و مقداری از قالب برای خارج شدن گازهای جمع شده، باز میماند. پس از بسته شدن قالب، مقداری حرارت و فشار به قالب اعمال شده و مواد دقیقا شکل قالب را به خود میگیرند. در نهایت نیز مواد سرد شده و فرم میگیرند.
در پایان نیز باید قطعات را از قالب جدا کرده و آن را در فیکسچر سرد کرد تا در همان فرم باقی بماند. تمامیاضافهها و پلیسهها نیز باید از روی قطعه جدا شوند.
آیا فرایند قالب گیری فشاری یک فرایند ایمن است؟
در صورت استفاده از دستورالعملهای مناسب و رعایت اقدامات احتیاطی در حین کار، فرایند قالب گیری فشاری غالبا به عنوان یک فرایند تولیدی ایمن شناخته میشود. برای این منظور، استفاده از تجهیزات محافظتی مناسب مانند عینک ایمنی و لباس مقاوم در برابر حرارت، انجام تعمیر، نگهداری و بازرسی منظم تجهیزات و دستگاه فرایند و فراهم کردن تهویه مناسب در محل کار، میتواند باعث افزایش ایمنی فرایند قالب گیری فشاری شوند.
کیفیت قطعات تولید شده در فرایند قالب گیری فشاری چگونه است؟
قالب گیری فشاری غالبا منجر به تولید قطعات با کیفیت بالا میشود. در واقع، از این فرایند میتوان برای تولید قطعات با استحکام بالا، پایداری و دقت ابعادی بالا، مقاومت حرارتی و کیفیت سطحی مطلوب استفاده کرد. این فرایند غالبا نسبتا به سایر فرایندهای قالب گیری مانند قالب گیری تزریقی، قطعاتی با سطوح با کیفیتتر تولید میکند.
در فرایند قالب گیری فشاری، علاوه بر مواد اولیه از چه موادی استفاده میشود؟
برای تولید برخی محصولات در این فرایند، علاوه بر مواد اولیه از یک سری محصولات میانی نیز استفاده میشود. به عنوان مثال، قبل از استفاده در کامپوزیتها، الیاف مورد استفاده قرار میگیرد. پری پرگ نیز لایهای از الیاف است که با رزین آغشتهشده و به عنوان محصول میانی در فرایند قالب گیری فشاری برای تولید کامپوزیتهای الیافی استفاده میشود.
از دیگر محصولات میانی مورد استفاده در این فرایند میتوان به پارچههای پیش آغشته و گرانولهای پلیمری اشاره کرد. پارچههای پیش آغشته پارچههایی هستند که به رزین یا مواد دیگر آغشته میشوند و در ساخت کامپوزیتهای پارچهای به عنوان محصول میانی مورد استفاده قرار میگیرند. گرانولهای پلیمری نیز دانههای ریز پلیمری هستند که غالبا در این فرایند به عنوان محصول میانی در ساخت برخی قطعات مورد استفاده قرار میگیرند.
جمع بندی
یکی از فرایندهای پرکاربرد در ساخت طیف وسیعی از قطعات پلاستیکی یا کامپوزیتی قالب گیری فشاری است. در این فرایند، یک ماده مانند پلیمر ترموست یا ترکیب ترموپلاستیک از پیش اندازهگیری شده، پیش گرم میشود و در یک حفره باز قالب قرار میگیرد. سپس قالب بسته شده و برای فشرده شدن و شکلگیری مواد، فشار بالایی به قالب اعمال میشود. همچنین برای ذوب و پخت مواد نیز حرارت مشخصی اعمال شده و پس از پخته شدن، قطعه سرد شده و از قالب جدا میشود.
این فرایند باعث تولید قطعاتی با دقت، استحکام و پایداری ابعادی بالا میشود و کیفیت مطلوبی را در ساخت قطعات ارائه میدهد. در واقع فرایند قالب گیری فشاری دارای ویژگیها و مزایای متعددی است که باعث کاربرد گسترده آن در صنایع مختلف شده است.