یکی از متداول ترین روشها برای ساخت قطعات فلزی، روش ریخته گری است. ریخته گری خود شامل انواع روشهای مختلفی است که ریخته گری گریز از مرکز (Centrifugal Casting) یکی از انواع روشهای ریخته گری میباشد. این روش غالبا برای تولید لولههای فلزی مورد استفاده قرار میگیرد. این روش به عنوان یک تکنیک ریخته گری تخصصی و کاملا منحصر به فرد شناخته میشود که ویژگیهای زیادی دارد.
اگر میخواهید با ریخته گری گریز از مرکز، روشها، مزایا و کاربردهایش بیشتر آشنا شوید، این مقاله را مطالعه کنید.
ریخته گری گریز از مرکز چیست ؟
ریخته گری گریز از مرکز یا ریخته گری سانتریفیوژ یکی از روشهای ریخته گری است که در طی آن، قالب تحت تاثیر نیروی گریز از مرکز پر میشود. در سایر روشهای ریخته گری، قطعه در قالب ثابت منجمد میشود؛ در صورتی که در این روش قالب در حال چرخش برای شکل گیری قطعه نهایی به کار میرود.
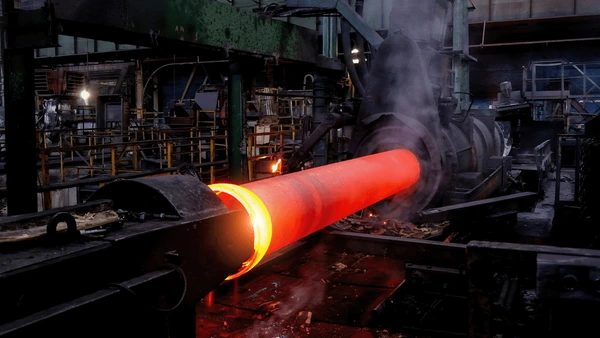
این روش برای تولید قطعات دقیق با استحکام بالا، به ویژه قطعاتی که دارای شکل استوانهای هستند، مورد استفاده قرار میگیرد. امروزه از این روش با اعمال خلاء، برای جلوگیری از اکسیداسیون و آلودگی مذاب و همچنین برای کمک به پر شدن سریعتر قالب، استفاده میشود.
در این روش، نیاز به سیستم راهگاه وجود نداشته و از هیچگونه ماهیچه داخلی نیز برای شکلدهی به مذاب استفاده نمیشود. ضخامت نهایی دیواره تولید شده، به حجم مواد مذاب اولیه ورودی بستگی دارد. همچنین در این روش به دلیل عمل چرخش و وجود اختلاف چگالی بین ناخالصیها و مذاب فلز، ناخالصیها روی سطح لوله جمع شده اما به سادگی با عملیات ماشینکاری حذف خواهند شد.
قطعاتی که با استفاده از این روش تولید میشوند، غالبا بین 2.5 میلیمتر تا 12.5 سانتیمتر ضخامت داشته و معمولا بین 3 تا 15 متر قطر دارند. در این روش میتوان از تمامی فلزاتی که قابلیت ریخته گری دارند، استفاده کرد؛ اما استفاده از انواع چدن، انواع فولاد و بخصوص فولادهای ضدزنگ، انواع آلیاژهای آلومینیوم، مس، منیزیوم و نیکل، در این روش بیشتر کاربرد دارد. گرچه این روش برای تولید انواع قطعات شیشهای و بتن نیز به کار برده میشود.
تاریخچه ریخته گری گریز از مرکز
حق اختراع اولیه برای ریخته گری گریز از مرکز در سال 1809 به آنتونی اخارت، انگلیسی، اعطا شد. در عرض چند سال، پتنت های دیگری در آلمان و آمریکا صادر شد. با این حال، پیشرفت در تکمیل این تکنیک برای بیش از یک قرن آهسته و ناسازگار باقی ماند. نقطه عطف قابل توجهی در تکامل این روش پس از جنگ جهانی اول، به ویژه در ریختهگری لولهها اتفاق افتاد. در این دوره، ریختهگری گریز از مرکز لولهها به یک رویکرد تولیدی قابل دوام و رقابتی تبدیل شد.
https://www.xometry.com/resources/casting/centrifugal-casting/
مراحل و فرآیند ریخته گری گریز از مرکز
در ریخته گری گریز از مرکز، یک قالب میچرخد و همزمان فلز مذاب درون آن ریخته میشود. در این روش، نیروی گریز از مرکز باعث توزیع فلز مذاب در قالب، در فشارهایی نزدیک به 100 برابر نیروی گرانش، میشود. به طور کلی، فرآیند ریخته گری گریز از مرکز شامل مراحل زیر است:
- مرحله اول ریخته گری سانتریفیوژ : آماده سازی قالب
برای انجام ریخته گری گریز از مرکز، در ابتدا سطح داخلی قالب با استفاده از مواد نسوز با ضخامت بین 1 تا 1.5 میلیمتر پوشانده میشود. در روش واقعی ریخته گری گریز از مرکز، برای این فرایند ابتدا قالب پیش گرم شده و در حین چرخش قالب از دوغاب سرامیکی استفاده میشود.
پس از آن، قالب خشک شده و تحت یک فرایند پخته میشود. در این مرحله باید از چسبیدن پوشش نسوز به سطح قالب به طور کاملا ایمن اطمینان حاصل کرد. همچنین بهتر است سطح قالب قبل از اعمال پوشش نسوز، کاملا از هرگونه آلودگی تمیز شود. این کار روی سطح و یکپارچگی قطعه ریخته گری بسیار تاثیرگذار است.
- مرحله دوم ریخته گری سانتریفیوژ: ریختن فلز مذاب درون قالب
پس از آمادهسازی قالب ریخته گری، فلز مذاب به درون آن ریخته میشود. برای این کار، در ابتدا فلز ریخته گری تا نقطهای بالاتر از نقطه ذوب خود گرم شده و سپس به طور مستقیم از طریق یک دهانه به داخل قالب ریخته میشود. برای این کار نیاز به استفاده از دروازه یا گیت وجود ندارد. همچنین حین این کار، قالب چرخانده میشود. امکان چرخاندن قالب پس از اتمام ریخته گری فلز یا مواد نیز وجود دارد.
سرعت چرخش قالب نیز به مشخصات مورد نیاز بستگی دارد اما غالبا بین 300 تا 3000 دور در دقیقه است.
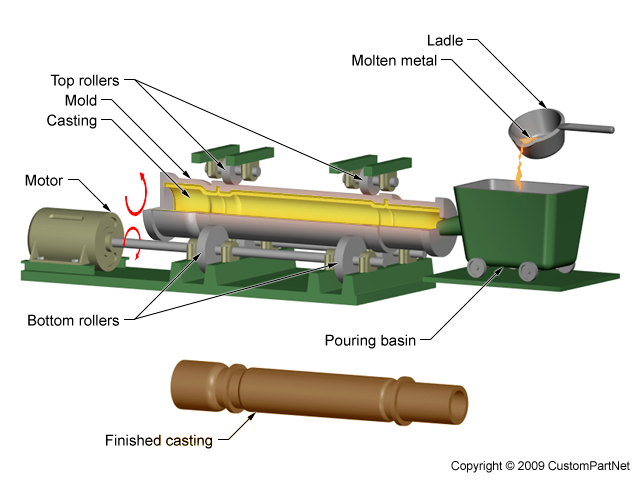
- مرحله سوم ریخته گری سانتریفیوژ : توزیع فلز مذاب توسط نیروی گریز از مرکز
فلز مذاب ریخته شده، به واسطه نیروی گریز از مرکز ایجاد شده از طریق چرخش قالب، به سمت دیواره بیرونی حفره قالب متمایل میشود. پس از ریختن مواد، چرخش قالب حفظ شده و همچنان به چرخش ادامه میدهد تا به مرور زمان ماده خنک و کاملا سفت شود. در این میان، چرخش قالب در حفظ توزیع یکنواخت مواد در اطراف محیط داخلی قالب بسیار موثر است.
در حقیقت این نیروی گریز از مرکز است که با راندن مذاب به سمت دیواره قالب، باعث شکلدهی فلز به صورت حلقوی میشود.
- مرحله چهارم ریخته گری سانتریفیوژ : خارج کردن قطعه از قالب
پس از اینکه ماده ریخته گری شده کاملا سفت و منجمد شد، قالب برداشته شده و باز میشود. در اینصورت قطعه تولید شده استخراج خواهد شد. قطعه تولید شده اگر با مهارت کافی ریخته گری شده باشد و سطح قالب نیز قبل از ریخته گری کاملا تمیز شده باشد، سطح قطعه نیاز به پرداخت نخواهد داشت.
اما به دلیل عمل چرخش و اختلاف چگالی موجود بین ناخالصیها و مذاب فلز اصلی مورد نظر، غالبا ناخالصیها روی سطح لوله جمع میشوند و میتوان آنها را با عملیات ماشینکاری حذف کرد.
عوامل موثر در ریخته گری گریز از مرکز
در بهبود فرایند ریخته گری گریز از مرکز عوامل زیادی تاثیرگذار هستند که مهمترین آنها عبارتند از:
- سرعت بارریزی: در فرایند ریخته گری گریز از مرکز، سرعت بارریزی مذاب باید بهینه باشد. به عبارتی طبق تجربه باید حداقل سرعت مورد نیاز برای تولید قطعات سالم اعمال شود. در صورتی که سرعت بارریزی از حالت بهینه کمتر باشد، عیوبی مانند پر نشدن و یا سرد جوشی ایجاد میشوند. همچنین در صورت زیاد بودن سرعت بارریزی، زمان انجماد افزایش مییابد. بالا رفتن زمان انجماد نیز باعث ایجاد ترکهای طولی خواهد شد.
- دمای بارریزی: دمایی که برای فرایند ریخته گری گریز از مرکز اعمال میشود، کاملا به شکل، ابعاد و جنس محصول بستگی دارد. اگر دما بیش از حد افزایش پیدا کند، قدرت تبریدی قالب کاهش پیدا کرده و زمان انجماد افزایش مییابد. در نتیجه آن پدیده جدایش و درشت دانه گی ایجاد میشود. همچنین در اثر سرد نشدن مذاب، این مذاب در سطح قالب ریزش پیدا کرده و در هنگام رسیدن به یکدیگر دچار لغزش خواهند شد.
- دمای قالب: اگر در این فرایند دمای قالب افزایش پیدا کند، قالب دچار انبساط حرارتی میشود. این انبساط، فاصله هوایی و زمان انجماد را افزایش میدهد. کاهش دمای قالب نیز باعث کاهش میزان انبساط شده و باعث میشود نیروهای انقباضی به قطعه وارد شوند. نیروهای انقباضی باعث ایجاد ترک در قطعه خواهند شد.
انواع ریخته گری گریز از مرکز
ریخته گری گریز از مرکز به روشهای مختلفی انجام میشود که این روشها عبارتند از:
- ریخته گری گریز از مرکز واقعی (True Centrifugal Casting)
این روش از ریخته گری گریز از مرکز، همان نوع معمولی این فرایند است. در این روش، قالب چرخانده شده و در نتیجه آن فلز با فشار قابل توجهی به دیواره قالب فشرده میشود. قطعهای که از این فرایند حاصل میشود، دانهبندی فشردهای داشته و دارای استحکام بالایی است. تمام ناخالصیهای سبک وزن احتمالی که در مذاب وجود دارند، به دلیل اختلاف چگالی، به سطح قطعه منتقل میشوند اما با یک تراشکاری ساده میتوان این ناخالصیها را از قطعه جدا کرد.
قطعاتی که با استفاده از روش ریخته گری گریز از مرکز واقعی تولید میشوند، بسیار با کیفیت بوده و دارای دقت ابعادی بالایی میباشند. همچنین غالبا سطح بیرونی بسیار صافی دارند. از این روش برای تولید قطعاتی اعم از بوش، آستر، سیلندر موتور و رینگهای یاتاقان به طور متداول استفاده میشود.
- ریخته گری نیمه گریز از مرکز (Semi Centrifugal Casting)
این روش غالبا برای تولید قطعاتی استفاده میشود که تقارن دورانی تقریبی دارند. همچنین این روش برای تولید قطعاتی که قسمت داخلی آنها پس از ریخته گری قابلیت ماشینکاری دارند، بسیار مناسب است؛ زیرا در این روش ناخالصیهای سبک وزن در مرکز قطعه جمع میشوند.
در این روش، در دیواره قالب یکسری حفره قرار گرفته است که مذاب درون این حفرات نفوذ کرده و قطعه شکل پیچیدهتری خواهد داشت. ریخته گری نیمه گریز از مرکز میتواند برای تولید قطعات با پیچیده ترین اشکال مورد استفاده قرار بگیرد که برای این منظور در این روش از ماهیچه استفاده میشود.
فرآیند این روش همانند روش گریز از مرکز واقعی است؛ اما سرعت چرخش در این روش کمتر از سرعت چرخش در روش گریز از مرکز واقعی میباشد. همچنین محور چرخش قالب در این روش همواره با موقعیت عمودی است.
از جمله قطعاتی که به طور متداول با استفاده از این روش تولید میشوند میتوان به چرخ، قرقره، چرخ دنده، چرخ تسمه شیاردار، پروانه و روتور موتورهای الکتریکی اشاره کرد.
- ریخته گری گریز از مرکز اسمی(Centrifugal Spin Casting)
در روش اسمی ریخته گری گریز از مرکز، برای رساندن فلز مذاب از یک مخزن مرکزی به قالبهای جداگانه، از نیروی گریز از مرکز استفاده میشود. در این روش اگر فاصله حفره قالب تا محور دوران تغییر کند، خواص قطعه نهایی نیز دچار تغییر خواهد شد. همچنین در این روش، محفظههای قالب به شکل متقارن در اطراف محور مانند پرههایی اطراف چرخ تعبیه میشوند. در اینصورت، در هر بار ذوبریزی، میتوان چندین قطعه تولید کرد.
روش ریخته گری گریز از مرکز اسمی در تولید بدنه شیرآلات، بستها و قطعات کوچک مانند طلا و جواهرات بسیار کاربرد دارد. برای تولید قطعات ظریف با دیوارههای نازک با کیفیت بالا، این فرایند با سرعتهای چرخش نسبتا پایین استفاده خواهد شد.
انواع دستگاه ریخته گری گریز از مرکز
براساس محور چرخش دستگاه، فرایند ریخته گری گریز از مرکز به دو صورت و با استفاده از دو دستگاه متفاوت انجام میشود:
- دستگاه ریخته گری گریز از مرکز افقی (Horizontal Centrifugal Casting)
در این روش، قالب چرخنده به دور محور افقی میچرخد. روش گریز از مرکز افقی برای تولید اجزای لولهای شکل بسیار کاربرد دارد و میتواند این اجزا را با کیفیت بسیار بالایی تولید کند. همچنین این روش برای قطعاتی که استوانهای شکل بوده و ارتفاع زیادی دارند بسیار متداول است. طول این قطعات به طور قابل توجهی بلندتر از قطر خارجی آن بوده و به صورت بسیار باکیفیت ساخته خواهند شد.
در روش ریخته گری گریز از مرکز افقی، پس از شکل گیری نهایی، قطعه باید به سرعت از قالب خارج شود و این مورد مهم ترین نکته در تولید قطعات با استفاده از این روش است. برای تولید قطعاتی مانند خطوط لوله مستقیم، سیلندرهای طولانی با فلج انتهایی و… از این روش استفاده میشود.
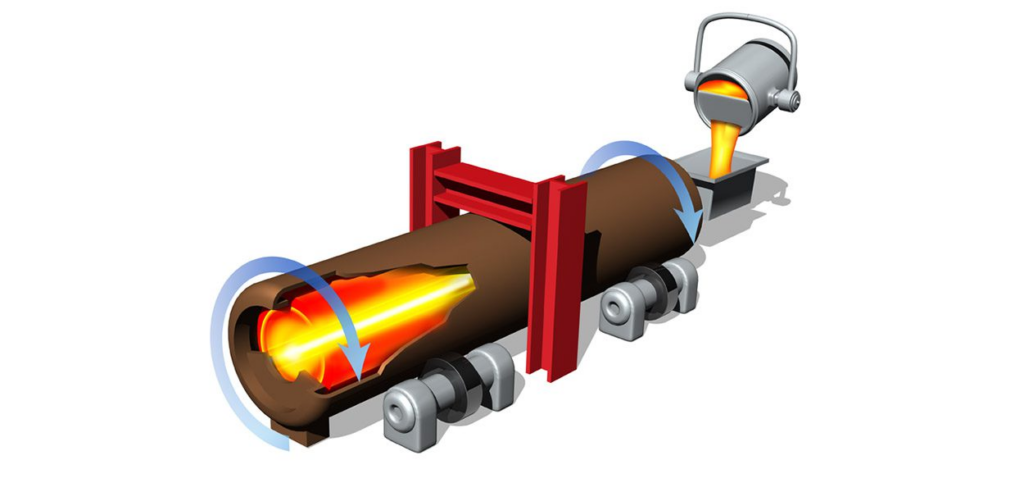
- دستگاه ریخته گری گریز از مرکز عمودی (Vertical Centrifugal Casting)
در این دستگاه، قالب چرخنده به دور محور عمودی میچرخد. از این روش برای تولید قطعات استوانهای شکلی استفاده میشود که در انتهایشان برآمدگی یا فرورفتگی داشته باشد. این قطعات که به اصلاح با نام OD شناخته میشوند، با استفاده از دستگاه ریخته گری گریز از مرکز عمودی با کیفیت بسیار بالایی تولید میشوند. در اینصورت، با قرار گرفتن ماهیچههایی از جنس گرافیت، ماسه یا سرامیک در انتهای قالب، قطعه نهایی به صورت فرورفته یا برآمده خواهد بود.
نکته قابل توجه در این روش این است که بخش نهایی قالبهای مورد استفاده در آن، باید کاملا متفاوت باشد تا به حفظ تعادل در هنگام چرخش کمک کند. در این روش، غالبا ارتفاع قطعه ریخته گری کمتر از دو برابر عرض قطعه است. همچنین قطعاتی که با استفاده از این روش تولید میشوند، غالبا به پردازش بعدی اعم از ماشینکاری ثانویه نیازی ندارند.
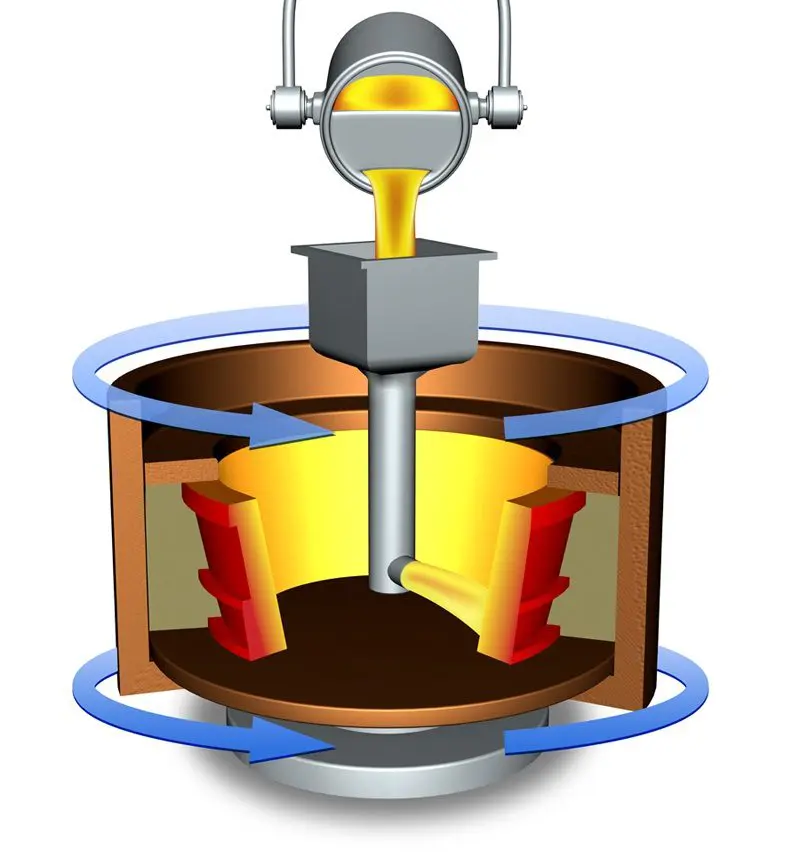
مزایا و معایب ریخته گری سانتریفیوژ
استفاده از انواع روشهای ریخته گری گریز از مرکز، ویژگیها و مزایای زیادی دارد؛ که مهمترین این مزایا عبارتند از:
- در این روش، امکان تولید تعداد بسیار زیادی اجزای استوانهای شکل با سرعت مطلوب فراهم است.
- این روش دقت ابعادی بالایی دارد.
- با استفاده از این روش غالبا نیاز به ماهیچهگذاری و یا ایجاد راهگاه برای ریخته گری وجود ندارد.
- قطعه نهایی تولید شده با استفاده از این روش خواص مکانیکی مطلوبی خواهد داشت.
- به دلیل شکلگیری خوب دانهبندی در سطح خارجی قطعه، با استفاده از این روش میتوان قطعاتی با مقاومت بالا در برابر خوردگی را تولید کرد.
- امکان ریخته گری فلزات با وزن بالا در این روش وجود دارد.
- به دلیل وجود بخش کنترل کامل الکترونیک در دستگاههای مورد استفاده در این روش، نیاز به عملیات اپراتوری بسیار ساده وجود دارد.
- نسبت به اغلب سایر روشها، سرعت انجماد در این روش بالاتر است.
- این روش برای محیط زیست خطری نداشته و آلودگی ایجاد نمیکند.
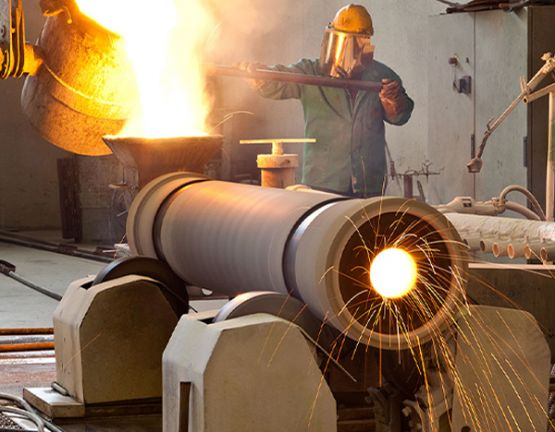
در کنار تمامی این مزایا، ریخته گری گریز از مرکز یکسری معایب را نیز شامل میشود؛ که این معایب عبارتند از:
- با استفاده از این روش غالبا نمیتوان اشکال هندسی پیچیده را به سادگی تولید کرد.
- امکان ایجاد تفکیک و جدایش در مناطق مختلف قطعه وجود دارد.
- اجزای دستگاه به صورت روزانه نیاز به روغنکاری خواهند داشت.
- برای تولید قطعات حجیم و سنگین در این روش غالبا انرژی بالایی مصرف میشود.
کاربرد ریخته گری گریز از مرکز
ریخته گری گریز از مرکز به دلیل ویژگیها و مزایای متعددی که دارد، در تولید قطعات مختلفی مورد استفاده قرار میگیرد. برخی از رایجترین کاربردهای این این روش عبارتند از:
- تولید قطعاتی که بخشهای متقارن دارند و میتوانند حول یک محور بچرخند.
- تولید قطعاتی که به روشهای ریخته گری ایستا قابلیت تولید ندارند و خواص آنها با استفاده از این روشها نامطلوب است.
- تولید قطعاتی که ابعاد طویل دارند.
- تولید قطعات با استفاده از آلیاژهایی که امکان ریخته گری آنها در سایر روشها امکان پذیر نبوده و یا هزینه زیادی داشته باشد.
- تولید قطعاتی که در ساخت آنها نیاز به دانهبندی یکنواخت وجود داشته باشد.
- تولید قطعاتی که نیاز به انسجام و یکنواختی ابعادی دارند.
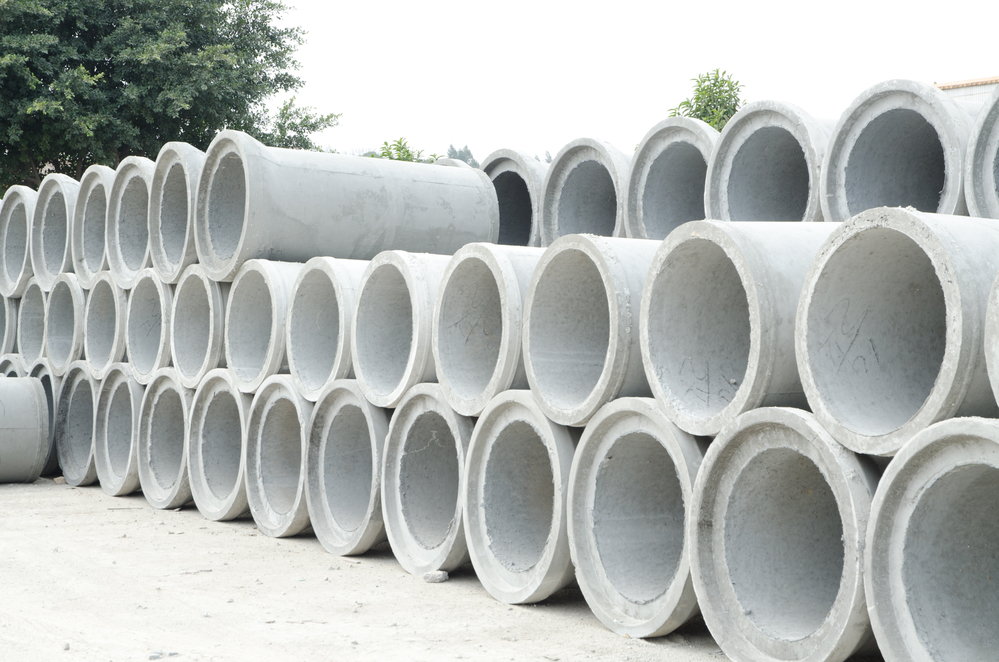
برخز از متداولترین صنایعی که در آنها از دستگاه ریخته گری گریز از مرکز برای تولید قطعات مختلف استفادف میشود نیز، عبارتند از:
- صنعت خودروسازی: برای تولید قطعات موتور، انواع سیلندرها، سیستم ترمز، دیسکهای ترمز و…
- صنعت هوافضا: برای تولید قطعات مهم و حساس هواپیما مانند توربینهای گازی، کمپرسورها، توربین هواپیما و قطعات سیستمهای هواپیما
- صنعت ساختمان: برای تولید قطعات ساختمانی مانند ستونها، تیرهها و قطعات سازههای بتنی
- صنعت نفت و گاز: برای تولید قطعاتی مانند راکتورها، شیرها، فلنجها و لولههای پرسوری
- صنعت معدنی: برای تولید قطعات معدنی مانند پروانههای تراکمی و روتورها
سوالات متداول
تفاوت بین ریخته گری گریز از مرکز و ریخته گری شن و ماسه چیست؟
ریخته گری شن و ماسه یک روش ایستا یا ثابت ریخته گری است که در آن از قالبهای ماسهای برای تولید قطعات فلزی و یا غیر فلزی استفاده میشود. اما در روش ریخته گری گریز از مرکز از قالبهای چرخنده که به دور یک محور مشخص میچرخند، برای تولید قطعات فلزی و یا غیرفلزی استفاده میشود.
آیا ریخته گری سانتریفیوژ مانند ریخته گری دقیق است؟
این دو روش ریخته گری در نحوه اجرا و فرایند انجام ریخته گری با یکدیگر تفاوت دارند. در ریخته گری گریز از مرکز، قالب تحت تاثیر نیروی گریز از مرکز پر میشود و قالب در حال چرخش است. اما در روش ریخته گری دقیق، قطعه در قالب ثابت منجمد میشود.
چه زمانی باید از ریخته گری گریز از مرکز استفاده کرد؟
همانطور که خواندید در کاربردهای متنوعی میتوان از روش ریخته گری گریز از مرکز استفاده کرد؛ اما این روش غالبا در تولید قطعاتی به کار میرود که بخشهای متقارن داشته، طویل هستند و دور یک محور میچرخند.
چه فلزاتی را میتوان به صورت گریز از مرکز ریخته گری کرد؟
آلیاژ اصلی و متداولی که در ریخته گری گریز از مرکز مورد استفاده قرار میگیرد، فولاد ضد زنگ است که در برابر خوردگی بسیار مقاوم بوده و از استحکام و دوام بالایی برخوردار میباشد. این آلیاژ هم برای ریخته گری گریز از مرکز واقعی و هم برای ریخته گری نیمه گریز از مرکز مناسب است و بسته به پیچیدگی قطعه و الزامات کاربردی خاص مورد استفاده قرار میگیرد. اما از سایر آلیاژها نیز مانند آلیاژهای نیکل، مس، چدن و آلومینیوم نیز در ریخته گری گریز از مرکز فلزات استفاده میشود.
جمع بندی
همانطور که خواندید، ریخته گری گریز از مرکز یکی از روشهای ریخته گری فلزات است که قالبهای مورد استفاده در آن، تحت تاثیر نیروی گریز از مرکز پر میشوند. در این روش، برخلاف سایر روشهای ریخته گری، از قالب در حال چرخش برای شکلگیری قطعه نهایی استفاده میشود. ریخته گری گریز از مرکز یک روش کارآمد است که قطعه تولید شده به وسیله آن دارای خواص مکانیکی مطلوبی میباشد. این روش برخلاف معایب اندکی که دارد، مزایای قابل توجهی ارائه میدهد و به همین دلیل در تولید قطعات در صنایع مختلف به طور متداول از آن استفاده میشود.
با فبرینو از ایده تا اجرا را با خیال آسوده طی کنید. اگر نیاز به تولید قطعات خاص دارید بدون تردید فبرینو می تواند یک گام موثر در انجام پروژه شما باشد. با متخصصین ما تماس بگیرید و از خدمات ما بهره مند شوید.