یکی از تکنیکهای ریخته گری دایکاست یا تحت فشار، ریخته گری تحت فشار در خلا یا vacuum casting است. در ریخته گری تحت فشار، در اغلب موارد، وجود عیوبی مانند مک در قطعات تولیدی، منجر به ایجاد مشکل در تولید شده و همچنین در صورت وجود حبابهای محبوس پراکنده، ریسک بیشتری را به وجود خواهد آورد. به همین دلیل، به دلیل سرعت بالای پرشدن در این فرایند، تسریع در تخلیه محفظه قالب از هوای درونی بسیار اهمیت داشته و باعث حذف مکهای گازی که به دلیل نامناسب بودن تخلیه هوای قالب در قطعات به وجود میآیند، میشود.
در حال حاضر، فرایندهای تولیدی بسیار پیشرفت کرده و در ریخته گری تحت فشار از فناوری تخلیه هوای داخل قالب استفاده میشود که مزیتهای بیشتری نسبت به طراحی مرسوم خروجی هوا در قالبهای دایکاست دارد.
در شرایط خلاء، گازهایی که داخل قالب حبس شدهاند، منبع اصلی وجود روزنه در ریخته گری هستند. در ریخته گری تحت فشار در خلا، میتوان توسط سیستم رونده و لوله پرتان، خلاء را در طول فرایند شکل داد. در این فرایند ریخته گری، بین اجزاء یکپارچگی و تعامل خاصی وجود داشته که بهتر از ریخته گری نوع سنتی میباشند. در واقع، فرایند ریخته گری خلا در کنار ویژگیها و مزایای ریخته گری سنتی، ویژگیهای دیگری را نیز اعم از قابلیت اعتماد و اتکای بالای این فناوری در افزایش کیفیت قطعات تولیدی، با حفظ منافع اقتصادی فرایند شامل میشود.
اگر میخواهید با فرایند ریخته گری تحت فشار در خلا، ویژگیها و کاربردهای آن بیشتر آشنا شوید، مطالعه این مقاله از فبرینو را از دست ندهید.
ریخته گری تحت فشار در خلا چیست و چه کاربردهایی دارد؟
ریخته گری تحت فشار در خلا یا همان ریخته گری در خلا، یک فرایند بسیار کاربردی است که در طی آن مواد ذوب شده تحت فشار در شرایط خلا به داخل قالب تزریق میشوند. در این صورت برخلاف روشهای سنتی که در آنها مواد مذاب به طور طبیعی به داخل قالب ریخته میشوند، در این روش، امکان تولید قطعات محکم و قطعاتی با سختی بالا فراهم میشود. در واقع این فرایند علاوه بر حذف فضاهای خالی منجر به افزایش استحکام قطعات نیز میشود.
در این فرایند قطعات دایکاست با دوام بالا تولید شده و غالبا تلرانسهای دقیقی دارند. همچنین قطعات تولید شده با این فرایند در برابر گرما، UV و امواج الکترومغناطیسی مقاومت دارند. با استفاده از ریخته گری خلا امکان تولید قطعات پیچیده با سرعت و دقت بالایی فراهم میشود و در واقع امکان تولید انبوه قطعات با این فرایند وجود دارد.
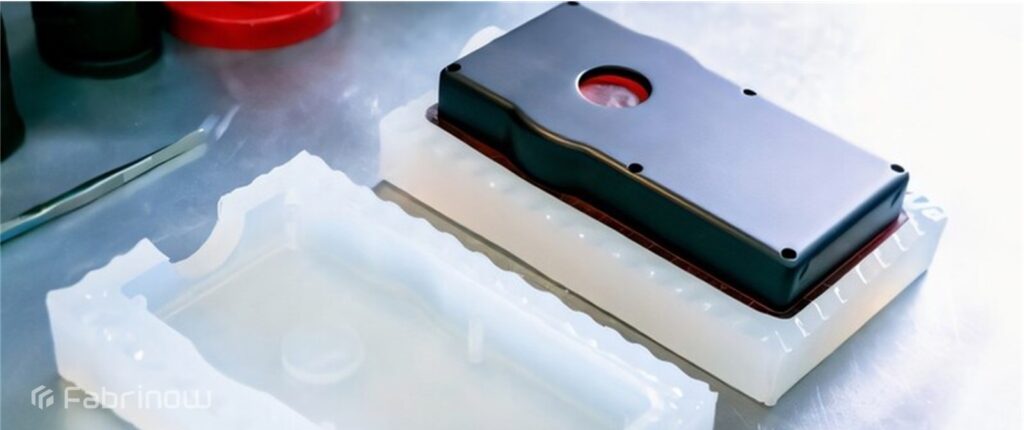
ریخته گری خلا غالبا تنها روش تولید مقادیر خاصی از فولاد و آلیاژهای آن محسوب میشود که منجر به تولید آلیاژ با کیفیت فولادی شده و در صنایع خودروسازی، هوافضا و راه آهن مورد استفاده قرار میگیرند. در طی فرایند تولید این قطعات، مقادیری هیدروژن و کربن از فولاد مذاب حذف میشوند. در گذشته، حذف این مقادیر هیدروژن در مدت زمان بیشتری انجام میشد که امروزه خارج کردن هیدروژن با روش پیشرفته و تحت خلا انجام شده و برخی از نواقص احتمالی که روی عملکرد فولاد نیز تاثیرگذار هستند، برطرف میشوند.
حذف گاز هیدروژن و یا کربن تحت شرایط خلاء علاوه بر کاهش نقصهای احتمالی منجر به ایجاد فولاد کم کربن شده که این فولاد خاصیت انعطاف پذیری بیشتری داشته و در این صورت شکل پذیری بهتری خواهد شد.
از کاربردهای این فرایند میتوان به ساخت قطعات پیچیده با ساختار یکپارچه، ابعاد دقیق، سطح با کیفیت، قطعاتی با مقاومت و سختی بالا اشاره کرد؛ به همین دلیل در صنایع مختلفی به طور گسترده مورد استفاده قرار میگیرد. به عنوان مثال از این فرایند در صنعت خودروسازی برای تولید 60 درصد از قطعات اتومبیل استفاده میشود. در کنار آن در تولید قطعات صنایعی مانند هوافضا، صنایع الکترونیک، لوازم خانگی و جواهرات نیز کاربرد دارد.
نحوه انجام ریخته گری تحت فشار در خلا
برای ساخت قطعه با روش ریخته گری تحت فشار در خلا، ابتدا قطعات ریخته گری آماده میشوند. قالبهای دایکاست از دو قسمت متحرک و ثابت ساخته میشود که قسمت متحرک روی صفحه متحرک و قسمت ثابت نیز روی صفحه ثابت نصب میشود. در این میان، تمیزکاری، روانکاری و بستن قالب از مهم ترین عوامل در فرایند آماده کردن قالبهای ریخته گری در خلا محسوب میشوند.
برای انجام فرایند ریخته گری تحت فشار در خلا سایر مراحل زیر دنبال میشوند:
- آماده سازی قالب
همانطور که در بالاتر اشاره شد، اولین مرحله برای انجام ریخته گری در خلا، آماده سازی قالبها است. قالبهای مورد استفاده در این فرایند معمولا از فولاد و یا سایر مواد مقاوم تولید میشوند زیرا این قالبها شکل دقیق داخلی اشیا را تعیین میکنند و در کنار آن باید در برابر دما و فشارهای بالا در فرایند ریخته گری در خلا مقاومت داشته باشند.
همچنین در دیوارههای داخلی قالب مقداری روان کننده اعمال میشود. استفاده از روان کنندهها در دیوارههای قالب منجر به تنظیم دمای قالب شده و در کنار آن یک لایه بین فلز مذاب و قالب ایجاد میکند. با این کار، امکان حذف راحت تر ریخته گری فراهم خواهد شد.
- آماده سازی مواد ریخته گری
مواد ریخته گری خلا غالبا فلزات مذاب هستند که میتوانند به صورت تک فلزی یا آلیاژی باشند. این مواد مذاب در یک کوره یا محفظه خاص در دمای بالا ذوب شده، در ملاقه ریخته شده و در ظرفی نگهداری میشوند. فلزات مورد استفاده در فرایند ریخته گری خلا معمولا آلیاژی مانند فولاد، آلومینیوم، منیزیم یا روی میباشند.
- ایجاد خلا در دستگاه
قبل از ورود مواد مذاب به قالب ریخته گری، فضای دستگاه با استفاده از یک سری پمپهای خاص و سیستممهای خلا تحت فشار، تحت فشار پایین و خلا قرار میگیرد. هدف از ایجاد خلا در فضای دستگاه در این مرحله، از بین بردن هوا و رطوبت است تا از ایجاد اکسیداسیون و سایر عوامل مخرب در فرایند ریخته گری جلوگیری شود.
- پر کردن قالبها
در این مرحله، مواد مذاب به وسیله یک سیستم پمپاژ و با استفاده از یک سری لولههای خاص به قالبها منتقل میشوند. فشار محیط در این مرحله منجر به ریخته شدن مواد مذاب با دقت و با سرعت مناسب در داخل قالبها خواهد شد. در این مرحله همچنین قالب باید کاملا بسته شود؛ در غیر اینصورت امکان ریخته گری فلز مذاب با فشار بالا وجود ندارد.
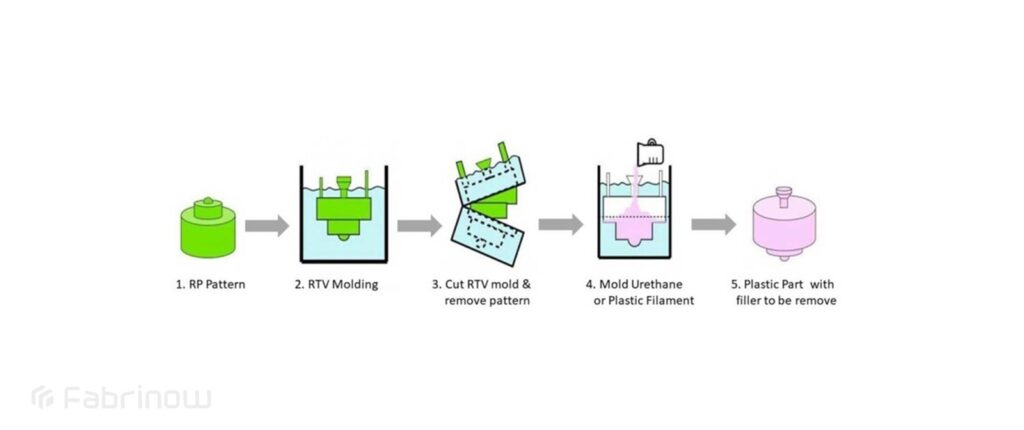
- سرد شدن و جامد شدن مواد
پس از اینکه قالبهای ریخته گری پر شدند، مواد مذاب داخل قالبها به تدریج خنک و جامد میشوند. معمولا این فرایند نیاز به زمان مشخصی داشته و میتوان برای تسریع فرایند خنک شدن از سیستمهای خنک کننده، هوا یا آب استفاده شود.
- باز کردن قالب و خروج قطعه
پس از اینکه مواد داخل قالب به طور کامل سرد و جامد شدند، قالب باز شده و قطعه جامد شده از داخل آن خارج میشود. در این صورت، قطعه به صورت نهایی شکل داده شده و آماده استفاده است.
- عملیات پس پردازش
در برخی مواقع، پس از خروج قطعه از قالب، ممکن است نیاز به حذف و یا برش مواد اضافی و یا اصلاح جزئیات نهایی روی قطعه وجود داشته و نقاط ضعف قطعه برطرف شود. برای این منظور عملیات پس پردازش اعم از پرداخت، تمیزکاری، ماشین کاری و یا سایر فرایندهای نهایی روی قطعه انجام خواهند شد.
پرداخت نهایی قطعه در فرایند ریخته گری تحت فشار در خلا، یک مرحله مکمل است که میتواند روی کیفیت سطح قطعه بسیار تاثیرگذار باشد. همچنین انجام فرایندهای مختلف پرداخت کاری قطعه روی دوام و عملکرد قطعه نیز موثر است.
صنایع پرکاربرد ریخته گری تحت فشار در خلا
ریخته گری تحت فشار در خلا به دلیل ویژگیها و کاربردهای مختلفی که ارائه میدهد در صنایع مختلفی به طور گسترده مورد استفاده قرار میگیرند. از جمله مهمترین و رایجترین این صنایع میتوان به موارد زیر اشاره کرد:
- صنعت هوافضا: برای تولید قطعات پیچیده و حساس اعم از توربینها، موتورها، قطعات مکانیکی، قطعات سوختی و قطعات ساختاری
- صنعت خودروسازی: برای تولید انواع قطعات خودرو اعم از صفحههای ترمز، موتورها، دیسکها، قطعات سیستم سوسپانسیون و سایر قطعات درونی خودرو
- صنعت الکترونیک: برای تولید قطعات الکترونیکی پیچیده اعم از مدارهای مجتمع (IC)، قطعات سنسور، کانکتورها و الکترودها
- صنایع طبی: برای تولید ایمپلنتهای پزشکی، ابزارهای جراحی، ابزارهای تشخیصی و قطعات پروتزهای داخلی
- صنایع دقیق: برای تولید ساعت، جواهرات، ابزارهای دقیق و قطعات فلزی با دقت بالا
علاوه بر این صنایع، ریخته گری خلا، در صنایعی مانند صنعت نیروگاهها، صنعت ماشین آلات، صنایع ساختمانی و صنایع شیمیایی نیز بسیار کاربرد دارد. همچنین به دلیل امکان استفاده از آلیاژها و فلزات با دمای بالا و خواص مکانیکی و فیزیکی ویژه، از روش ریخته گری خلا غالبا در صنایع پیشرفته و پیشرو نیز استفاده میشود.
تفاوت ریخته گری تحت فشار و قالب گیری تزریقی
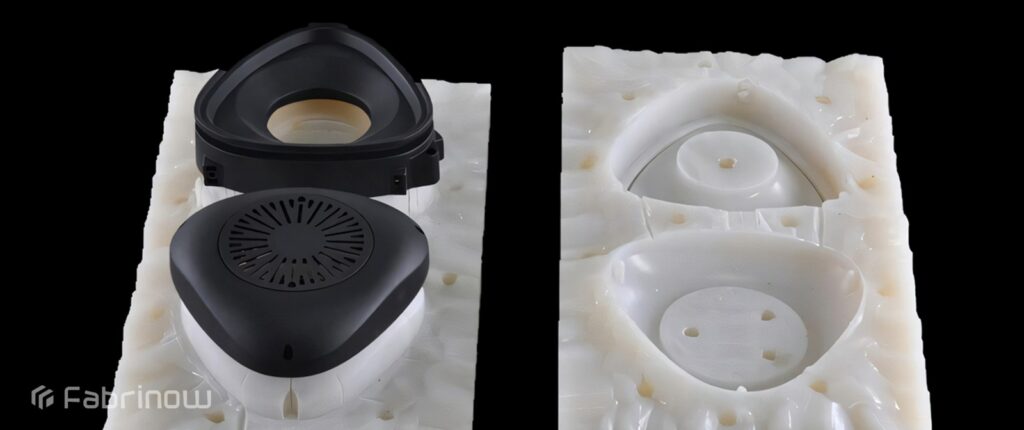
فرایند و نحوه انجام روشهای قالب گیری تزریقی و ریخته گری تحت فشار در خلا مشابه است و تفاوت آنها در نوع و مقدار مواد استفاده میشود. همچنین این فرایند ویژگیها، مزایا و معایب خاص خود را دارند. در فرایند ریخته گری تحت فشار از مواد خام فلزی استفاده شده و در قالب گیری تزریقی غالبا از پلیمر یا پلاستیک به عنوان مواد اولیه استفاده میشود.
از جمله مزایای ریخته گری تحت فشار در خلا میتوان به دقت بالاتر و تحمل سخت تر اشاره کرد و با استفاده از آن امکان ریخته گری طرحهای پیچیده نیز فراهم میشود. همچنین قالبهای دایکاست قویتر، پایدارتر و مقاومتر از قالبهای تزریق پلاستیک هستند و قطعات تولید شده در این قالبها در برابر اشعه ماوراء بنفش، هوازدگی و ترک خوردگی کاملا مقاوم میباشند.
در برابر، قطعات تولید شده در قالبهای تزریق پلاستیک براساس حجم واحد ارزانتر میباشند و عایقهای الکتریکی خوبی محسوب میشوند. در فرایند قالب گیری تزریقی همچنین انعطافپذیری بیشتری وجود داشته و در آن میتوان از مواد مختلف پلاستیکی یا پلیمری استفاده کرد. در کنار آن امکان استفاده از پرکنندهها در قالبهای پلاستیکی برای افزایش استحکام نیز وجود دارد.
مزایا، معایب و محدودیتهای ریخته گری تحت فشار در خلا
ریخته گری تحت فشار در خلا یا همان ریخته گری خلا، ویژگیهای مختلفی را شامل میشود که از جمله ترین مهم ترین مزایای این فرایند میتوان به موارد زیر اشاره کرد:
- این فرایند سرعت و دقت بالایی را شامل میشود و با استفاده از آن میتوان قطعات پیچیده با تلرانسهای نزدیک را تولید کرد.
- با استفاده از فرایند ریخته گری خلا امکان تولید انبوه قطعات یکسان بدون نیاز به ابزارهای اضافی فراهم میشود.
- قطعات تولید شده با این فرایند دقت و استحکام بالایی داشته و تلرانسهای دقیق را حفظ میکنند.
- قطعات تولید شده با این فرایند در برابر عوامل خارجی اعم از گرما، اشعه UV و امواج الکترومغناطیسی نیز کاملا مقاوم هستند.
- قطعات دایکاست نسبت به قطعات تولید شده با سایر روشهای ریخته گری قویتر و سبکتر هستند و کارایی بیشتری دارند.
- در فضای خلا، تماس مواد ریخته گری با هوا کاهش مییابد، به همین دلیل احتمال ایجاد ترک و ناهمواری در سطح قطعات ریخته گری شده در این فرایند نیز کاهش مییابد. در این صورت، استحکام و مقاومت قطعات بیشتر خواهد بود.
- در فرایند ریخته گری خلا، هوا از فضای داخلی قالبها و مواد ریخته گری شده حذف شده که این مورد نیز باعث کاهش پوروزی و نفوذ پذیری قطعات میشود. همچنین این مورد روی خواص مکانیکی و فیزیکی قطعات نیز تاثیر مثبتی داشته و کیفیت آنها را افزایش میدهد.
- در فشار بالا و شرایط خلا، مواد ریخته گری یکنواخت تر و با دقت بالاتری خنثی میشوند؛ به همین دلیل خواص مکانیکی اعم از مقاومت، سختی و اندازه دانه بندی بهبود مییابد.
- در فضای خلا و در شرایطی با دمای بالا و فشار کنترل شده، امکان استفاده از آلیاژهای ویژه و مواد با خواص منحصر به فرد و سختی بالا فراهم میشود که این موضوع روی تولید قطعات با خواص خاص و استحکام بالا تاثیرگذار است.
- در دستگاه ریخته گری تحت فشار در خلا، فشار و دمای فضای خلا قابل کنترل است که این موضوع روی تولید قطعات با دقت بالا و تکرارپذیری بهتر موثر است.
- در فضای خلا، هوا و آلایندههای موجود در آن حذف شده و با این موضوع خطر آلودگی قطعات کاهش مییابد. در این صورت کیفیت نهایی محصول نیز افزایش خواهد یافت.
به دلیل این همه مزایا میتوان گفت که فرایند ریخته گری خلا در صنایع پیچیده و حساس مانند هوافضا، خودروسازی، صنایع الکترونیکی و صنایع پیشرفته بسیار کاربرد دارد.
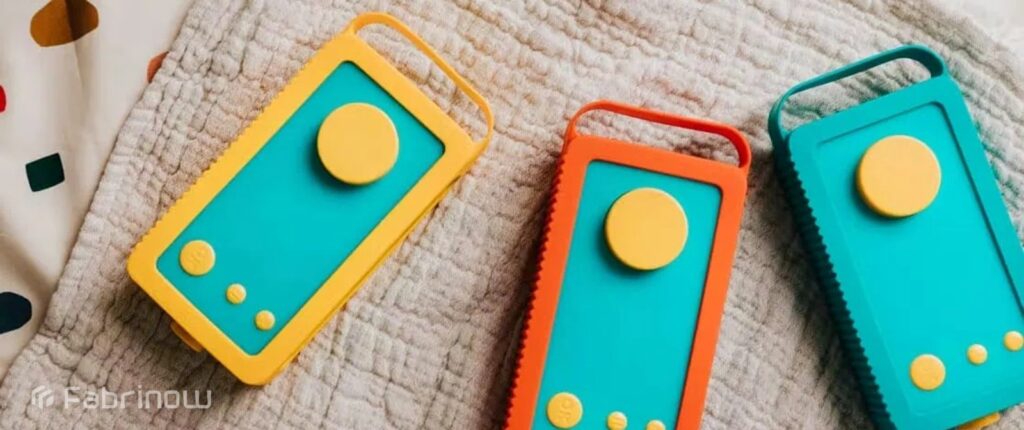
در کنار تمامیاین مزایا، ریخته گری در خلا یک سری معایب را نیز شامل میشود. به عنوان مثال امکان ایجاد یک سری عیوب و نقصهای احتمالی در طی فرایند مانند ایجاد زائدههای ناخواسته، حباب، ترکهای گرم و… وجود دارد که غالبا به دلیل فشار نامناسب تزریق، حجم شات، دمای نامناسب و نرخ نامناسب خنک شدن مواد ایجاد میشوند. در این صورت، نظارت دقیق بر فرایند ریخته گری و اجرای صحیح آن میتواند روی کاهش احتمال بروز این عیوب بسیار موثر باشد.
در کنار آن، سیلندرهای مورد استفاده در ریخته گری تحت فشار در خلا نیز یک سری معایبی را شامل میشود. در برخی مواقع، نوع خاصی از سیلندرهای ثابت در این فرایند مورد استفاده قرار میگیرند که عرض آنها در حدود 5 تا 10 سانتی متر بوده و شکافی به اندازه 0.5 میلی متر دارند. با وجود اینکه یک سیستم تخلیه میتواند قدرت مکش بالایی داشته باشد، این سیلندر ثابت خروجی نازکی مانند دهانه شیشه دارد که منجر به خروج خفقان آور گاز از قالب میشود.
همچنین معمولا هنگام استفاده از سیلندر ثابت و خنک کننده سیلندرها، بین پمپ تخلیه و قالب ریخته گری یک تاخیر 0.5 ثانیه ای وجود دارد. سیلندرهای متحرک نیز در برابر خروج هوا مقاومت کمتری از سیلندرهای ثابت دارند.
سایر روشهای ریخته گری تحت فشار
همانطور که خواندید، در ریخته گری تحت فشار در خلا از منبع خلا هوا استفاده میشود که منجر به حذف گازهای محبوس شده در داخل حفره قالب و کاهش عیوب ناشی از این گازها میشود. در کنار آن این فرایند بهبود خواص مکانیکی، پرداخت سطح بهتر و کیفیت و پایداری ابعادی قطعات را شامل میشود که با سرعت و دقت بالایی انجام میشود. در کنار این فرایند، ریخته گری تحت فشار انواع روشهای دیگری را نیز شامل میشود که عبارتند از:
- ریخته گری تحت فشار پایین: در این روش، قالب مورد استفاده به طور عمودی روی حوضچه فلز مذاب قرار گرفته و به وسیله لوله رایزر به آن متصل میشود. پس از آن فلز گرم شده و تحت فشاری بین 2 تا 100 کیلوپاسکال قرار میگیرد. در این صورت فلز مذاب به سمت بالا و به داخل قالب کشیده میشود.
- ریخته گری تحت فشار کوبشی: در این روش ریخته گری دایکاست فلز مذاب به داخل یک قالب باز ریخته شده و با اعمال فشار، مواد به درون حفره هدایت میشوند. این فرایند امکان ساخت فلزات با جریان پذیری پایین را فراهم کرده و روانی و جریان پذیری فلزات و آلیاژهای مذاب از عوامل مهم و اساسی در این فرایند محسوب میشوند.
- ریخته گری تحت فشار نیمه جامد: شکل دهی فلز نیمه جامد نیز با فرایند ریخته گری دایکاست انجام میشود که غالبا این فرایند برای تولید قطعات آلومینیومی مورد استفاده قرار میگیرد. این فرایند برای تولید قطعات پیچیده با خواص مکانیکی عالی و سطح مناسب بسیار کاربرد دارد اما غالبا در برابر عوامل محیطی حساس بوده و نیازمند تجهیزات گران قیمتی برای کنترل دما میباشد.
سوالات متداول
ریخته گری تحت فشار در خلا، روی رفع سوراخها و تخللهای موجود در فولاد چگونه عمل میکند؟
در گذشته، در صنعت فولادسازی به دلیل وجود گازهای نیتروژن و هیدروژن در فولاد مذاب در طول فرایند، فولادهای بی کیفیتی تولید میشدند. هیدروژن محلول منجر به ایجاد سوراخ و تخلخل در محصول نهایی شده و نیتروژن نیز دارای حلالیت کمی در فولاد است که میتواند منجر به ایجاد نقصهایی مانند شکنندگی و کاهش شکل پذیری شود.
به همین دلیل از ریخته گری خلا برای حذف گازهای محلول از فولاد مذاب، استفاده میشود. در این فرایند، عملیات ریخته گری در شرایط خلا و با حذف گازهای نیتروژن و هیدروژن انجام شده و منجر به رفع این نقصهای احتمالی میشوند.
دستگاه ریخته گری تحت فشار در خلا چیست؟
فرایند ریخته گری خلا با استفاده از دستگاه مخصوص برای تولید قطعات فلزی در شرایط خلا فشار بالا انجام میشود. این دستگاه یک فضای خلا را شامل شده که در آن فشار محیط به طور قابل توجهی کاهش یافته و محیط داخلی دستگاه نیز تقریبا خالی از هوا است. استفاده از این دستگاه برای انجام ریخته گری تحت فشار منجر به کاهش عیوبی مانند ترک خوردگی و پوروزی در قطعات تولید شده میشود. همچنین مقاومت و سایر خواص مکانیکی قطعه را افزایش میدهد.
استفاده از سیلندرها در فرایند ریخته گری خلا چه مزایایی دارد؟
سیلندرهای ثابت مورد استفاده در این فرایند هزینه کمتری دارند و از آنجایی که قطعات ثابتی دارند، حفظ و نگهداری آنها نیز ساده است. از طرفی، پمپ تخلیه غالبا در طول قالب گیری برای به حداکثر رساندن تخلیه گازها تا لحظات آخر فرایند درگیر خواهد بود؛ به همین دلیل استفاده از سیلندرها نیز در طول فرایند بسیار موثر خواهد بود.
جمع بندی
فرایند ریخته گری تحت فشار در خلا یکی از تکنیکهای ریخته گری تحت فشار یا دایکستینگ است که ویژگیهای مختلفی را ارائه میدهد. در این فرایند، از یک منبع خلا هوا استفاده میشود که این منبع گازهای محبوس شده در داخل حفره قالب را قبل از ورود فلز مذاب به قالب حذف میکند. این روش ریخته گری، منجر به کاهش حداقلی تلاطم گاز شده و در کنار آن مزایایی مانند بهبود خواص مکانیکی قطعه تولید شده، پرداخت سطح بهتر، پایداری ابعادی، زمان چرخه کوتاه تر و کاهش عیوب ناشی از گازهای به دام افتاده را ارائه میدهد.
در فرایند ریخته گری خلا همچنین فلز مذاب شده با سرعت بالا به درون قالبهای مادر ریخته میشود. در این صورت نیز چرخه زمانی کوتاه و دقت بالای ریخته گری در این فرایند از دیگر مزایای آن محسوب میشوند. به دلیل ویژگیها و مزایای متعدد فرایند ریخته گری خلا امروزه از این فرایند در کاربردهای صنایع مختلف به خصوص صنایع پیشرفته بسیار استفاده میشود.