یکی از فرایندهای مهم و رایج صنعت، فرایند جوشکاری است که در آن با استفاده از تکنیکهای مختلف، بین مواد و اجسام متنوع، یک اتصال مستحکم برقرار میشود. جوشکاری زیرپودری یکی از انواع روشها و تکنیکهای جوشکاری است که در آن از قوس الکتریکی استفاده شده و این قوس الکتریکی زیر پوششی از پودر روانساز مخفی شده است. در این صورت گرمای لازم برای جوشکاری بین الکترود مصرفی و قطعه کار توسط قوس الکتریکی تامین میشود.
اگر میخواهید با فرایند جوشکاری زیر پودری، ویژگیها و کاربردهای آن بیشتر آشنا شوید، مطالعه این مقاله از فبرینو را از دست ندهید.
جوشکاری زیر پودری چیست؟
جوشکاری زیر پودری Submerged arc welding یا به اختصار جوشکاری (SAW) یک فرایند رایج جوشکاری قوس الکتریکی است که در آن الکترود از مواد روانساز یا همان پودر جوش جدا است. در این فرایند، گرمای لازم برای جوشکاری توسط یک یا چند قوس بین یک فلز پوشش نشده، یک یا چند الکترود مصرفی و یک قطعه کار تامین میشود. همچنین در این فرایند قوس الکتریکی زیر پوشش پودری قرار گرفته و مخفی میباشد؛ به همین دلیل در آن میتوان از شدن جریانهای بالا، حتی تا 2500 آمپر، استفاده کرد.
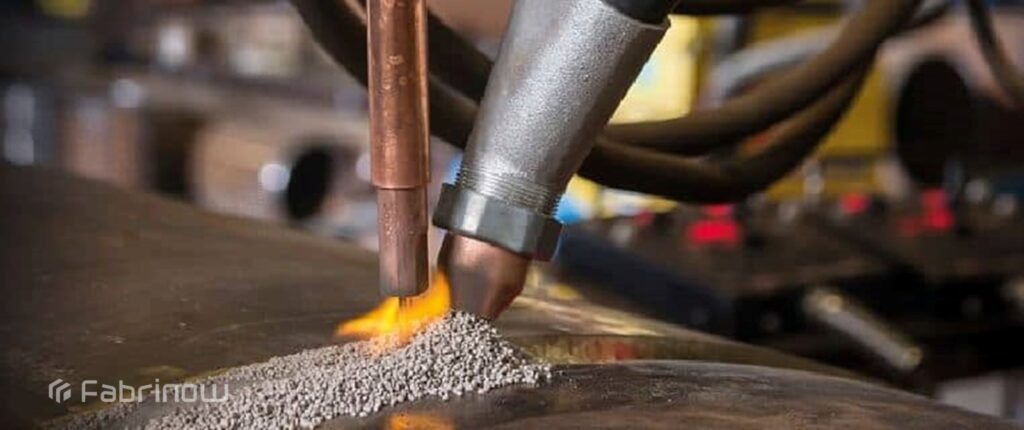
در فرایند جوشکاری زیر پودری، نوک الکترود داخل پودری از مواد معدنی قرار گرفته و در زیر این پودر، قوس مورد نیاز در امتداد مسیر جوشکاری تشکیل میشود. در این صورت، قوس قابل مشاهده نخواهد بود. در این عملیات از سیم بدون روکش استفاده شده و این سیم به طور متوالی از قرقره مخصوص رها میشود. با این کار ضمن تشکیل قوس، واسطه اتصال نیز ایجاد میشود. قوس توسط لایه ای از پودر قابل ذوب (فلاکس پودری) پوشیده میشود که این پودر همزمان فلز جوش مذاب و فلز پایه نزدیک اتصال را نیز پوشانده و از فلز جوش مذاب در برابر آلودگیهای اتمسفر محافظت میکند.
کاربرد جوشکاری زیر پودری چیست؟
همانطور که گفته شد، فرایند جوشکاری زیرپودری یکی از فرایند مهم و رایج صنعتی است. این فرایند به دلیل ارائه نتیجه با کیفیت بالا و همچنین اجرا و استفاده آسان، کاربرد بسیاری در صنایع مختلف دارد. از جمله مهمترین و رایجترین کاربردهای این فرایند در صنایع مختلف عبارتند از:
- جوشکاری مخازن تحت فشار در صنایع نفت و گاز، نیروگاهها، صنایع شیمیایی و سایر صنایعی که از مخازن تحت فشار استفاده میکنند، برای اتصال قطعات و جوشهای بزرگ
- جوشکاری خطوط لوله در صنایع نفت و گاز، صنایع فاضلاب و حمل و نقل سیالات و صنایع آب برای ایجاد اتصالات محکم و مقاوم در خطوط لولههای بلند و با فشارهای مختلف
- جوشکاری مخازن ذخیره در صنایع نفت، آب و فاضلاب و صنایع شیمیایی برای ساخت و تعمیر مخازن ذخیره مایعات اعم از نفت، گاز، آب و مواد شیمیایی
- جوشکاری سازههای سنگین در صنایع ساخت و ساز برای ساخت و تعمیر سازههای سنگین اعم از پلها، ساختمانهای فلزی، تراکمپلرها و سایر سازههای صنعتی
- جوشکاری ساخت کشتی در صنایع کشتی سازی برای ایجاد اتصالات دائمیو مقاوم بین قطعات فلزی بزرگ کشتیها با قابلیت انجام در شرایط آبی و محیطهای مرطوب
- جوشکاری ساخت واگنهای راه آهن در صنعت راه آهن برای ساخت و تعمیر واگنها و قطارهای ریلی برای ایجاد اتصالات قوی و مقاوم بین قطعات فلزی
فرایند جوشکاری زیرپودری چگونه است؟
در فرایند جوشکاری زیرپودری، ابتدا جریان الکتریکی مورد نیاز از طریق یک ژنراتور که غالبا ترانسفور ماتور یا رکتی فایر است، تامین میشود. با این جریان، بین الکترود و فلز پایه یک قوس برقرار شده و به این واسطه حوضچه مذاب برای پر کردن اتصال تشکیل میشود. در جوشکاری زیرپودری، این حوضچه مذاب جوش، ترکیبی از پودر (فلاکس) مذاب و فلز جوش است. پس از اعمال قوس، جریان الکتریکی از این منطقه عبور میکند.
برخلاف فلاکسهای سرد که رسانا نیستند، فلاکسهای مذاب غالبا رسانای خوب جریان الکتریسیته محسوب میشوند. برای اینکه جوشکاری به طور مداوم ادامه داشته باشد نیز، در این فرایند غلتکهای هدایت با استفاده از نیروی مکانیکی، سیم الکترود مصرفی فلزی را از میان لوله تماس یا همان نازل و توده فلاکس به اتصال موردنظر برای جوش، به طور پیوسته، هدایت میکنند. پس از آن، الکترود یا همان سیم جوش در منطقه جوش ذوب شده و در طول اتصال رسوب میکند.
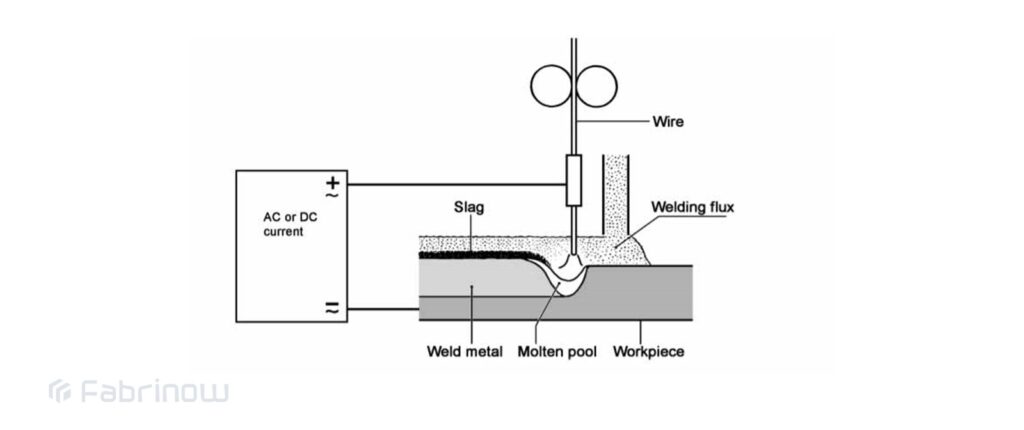
پس از رسوب سیم جوش، فلاکس پودری در جلوی قوس ریخته شده و سرد و منجمد میشود. پس از انجماد فلز جوش نیز، فلاکس ذوب نشده توسط سیستم مکش جمع کننده برای استفاده مجدد جمع آوری میشود.
در برخی موارد خاص، دو یا چند الکترود به صورت متوالی در یک اتصال تغذیه میشوند. این الکترودها هم میتوانند کنار یکدیگر قرار گرفته و به یک حوضچه تغذیه شوند و هم میتوانند به انداز کافی فاصله داشته باشند تا پس از انجماد یکی از آنها، حوضچه دیگر تشکیل شده و به شکل مستقل منجمد شود.
در فرایند جوشکاری زیرپودری، انتهای سیم جوش به داخل مواد روانساز فرو میرود و این مواد منطقه جوش را نیز پوشش میدهند. قبل از شروع جوشکاری، یک لایه نازک از پودر فلاکس روی سطح قطعه کار قرار میگیرد و قوس جوش در امتداد خط اتصال حرکت میکند. پس از انجام جوشکاری نیز، پودر اضافی بازگردانده میشود.
انواع روشهای جوشکاری زیرپودری چیست؟
جوشکاری زیرپودری با استفاده از روشهای مختلفی انجام میشود که هر کدام از این روشها، ویژگیها و مزایای خاص خود را داشته و برای شرایط کاری مختلف مناسب هستند. انواع روشهای جوشکاری زیرپودری عبارتند از:
- جوشکاری زیر پودری نیمه خودکار
در این روش، برای انجام جوشکاری زیرپودری از تفنگ جوشکاری دستی استفاده میشود. با استفاده از این تفنگ، انتقال الکترود و پودر محافظ انجام میشود. جوشکاری زیر پودری نیمه خودکار غالبا در شرایطی که نیاز به سرعت متوسط و استفاده از الکترودهای با قطر کم وجود دارد، استفاده میشود. همچنین با استفاده از تفنگ جوشکاری دستی در این روش، امکان کنترل دقیقتر فرایند جوشکاری فراهم میشود.
تغذیه خودکار سیم جوش و انتقال پودر محافظ از مخزن نیز، روی بهبود سرعت و کارایی فرایند بسیار موثر خواهد بود.
- جوشکاری زیر پودری خودکار
در این روش، همانطور که از نامش پیداست، فرایند جوشکاری توسط دستگاه و کنترل کنندههای خودکار انجام میشود؛ بدون اینکه نیاز به دخالت مستقیم کاربر وجود داشته باشد. در واقع، از ابتدا تا انتهای فرایند جوشکاری زیرپودری کاملا خودکار و اتوماتیک انجام شده و تنها در انتهای فرایند، کیفیت جوش و نتیجه نهایی توسط یک مهندس بررسی و ارزیابی میشود.
- جوشکاری زیر پودری ماشینی
در این روش نیز، فرایند جوشکاری زیرپودری توسط ماشین انجام میشود اما شروع فرایند و پایان آن و همچنین نظارت بر فرایند جوشکاری، کنترل سرعت و تنظیم متغیرهای جوشکاری در حین فرایند توسط کاربر انجام میشود. در جوشکاری زیرپودری ماشینی نیز برای کنترل کیفیت جوش و دقت بیشتر در کنترل جوشکاری، یک مهندس یا متخصص کنترل کیفیت حضور دارد تا عملیات تحت نظر قرار گرفته و نتیجه نهایی جوش کیفیت لازم را داشته باشد.
انواع پودر در جوشکاری زیر پودری
در جوشکاری زیرپودری، پودرها یا همان فلاکسهای مورد استفاده غالبا شامل یک سری مواد معدنی گدازنده دانه ای با شکلهای مختلف هستند که معمولا شامل اکسیدهای منگنز، تیتانیوم، سیلیسیم، آلومینیوم، زیرکونیم، منیزیم، کلسیم و یک سری ترکیبات دیگر مانند فلوئورید کلسیم میباشند. این فلاکسها به طور ویژه ای فرمول بندی میشوند تا با سیم الکترود مورد استفاده سازگاری داشته باشند. همچنین ترکیب این فلاکسها و سیم جوش خواص مکانیکی مطلوب را نیز فراهم کند. از این نظر انواع فلاکس برای جوشکاری زیرپودری دو نوع اصلی را شامل میشوند؛ که عبارتند از:
- فلاکسهای باند شده: این نوع فلاکسها اکسیدزُداهای فلزی را شامل میشوند که در جلوگیری از تخلخل در جوش موثر میباشند.
- فلاکسهای پیش ذوب شده: این نوع فلاکسها نیز با ذوب کردن مخلوط اجزا در یک کوره الکتریکی به منظور تشکیل یک محصول شیمیایی همگن تولید میشوند. پس از آن خنک و خرد شده تا اندازه ذرات موردنیاز را داشته باشند. این فلاکسها قوس نرم و پایداری ایجاد میکنند.
اما در یک دسته بندی دیگر، پودرهای جوشکاری زیر پودری را میتوان بر اساس شکل ظاهری شان، در سه مورد خلاصه کرد؛ که عبارتند از:
- پودرهای ترکیب شده یا پیش ذوب شده (Prefused Flux)
برای تولید این پودرها، اجزاء مورد استفاده ابتدا به صورت خشک مخلوط شده و سپس در یک کوره الکتریکی ذوب میشوند. پس از ذوب شده نیز روی آنها آب سرد پاشیده شده یا روی یک یک صفحه سرد منتقل میشوند تا منجمد شوند.
این پودرها ترکیب شیمیایی کاملا یکنواختی دارند و میتوان خاک آنها را بدون تغییر در ترکیب شیمیایی شان جدا کرد. همچنین پودرهای ترکیب شده رطوبت گیر نیستند و ذخیره سازی و نگهداری انها ساده تر است. از دیگر ویژگیهای این پودرها میتوان به استفاده مجدد از پودرهای ذوب نشده، بدون تغییر قابل توجه در انها اشاره کرد. همچنین برای جوشکاری با بیشتری سرعت نیز مناسب میباشند.
اما به دلیل دمای حلالیت بالای پودرهای ترکیب شده، امکان افزودن اکسیدزداها و فروآلیاژها به آنها وجود ندارد.
- پودرهای چسبیده شده (Bonded Flux)
برای تولید این پودرها نیز مواد خام ابتدا آسیاب شده، به صورت خشک با یکدیگر مخلوط میشوند و سپس با افزودن سیلیکات پتاسیم به این مخلوط، به یکدیگر میپسبند. مخلوط حاصل، به شکل گلوله در آمده و در دمای پایین خشک میشود. سپس به صورت مکانیکی خرد و دانه بندی میشود.
این پودرها دمای تولید پایینی دارند و به همین دلیل امکان افزودن اکسیدزداها و فروآلیاژها در آنها وجود دارد. چگالی این پودرها نیز پایین تر است و امکان استفاده از لایه ضخیم تر از این پودر روی منطقه جوش وجود دارد. پس از سرد شدن جوش نیز سرباره ایجاد شده روی آنها بهتر و راحت تر جدا میشود.
اما در این پودرها امکان جدا کردن خاکه بدون تغییر در ترکیب شیمیایی آنها وجود دارد و حساسیت بالایی نیز به جذاب رطوبت دارند.
- پودرهای آگلومره یا زینتر شده (Agglomerated Flux)
این نوع پودرها همانند پودرهای چسبیده شده تولید میشوند با این تفاوت که در تولید آنها از یک الک سرامیکی استفاده میشود. همچنین در این نوع پودرها مانند پودرهای ترکیب شده برای استفاده از اکسیدزداها و فروآلیاژها، به دلیل دمای بالای الک، محدودیت وجود دارد.
عوامل موثر و متغیرهای اصلی در جوشکاری زیر پودری
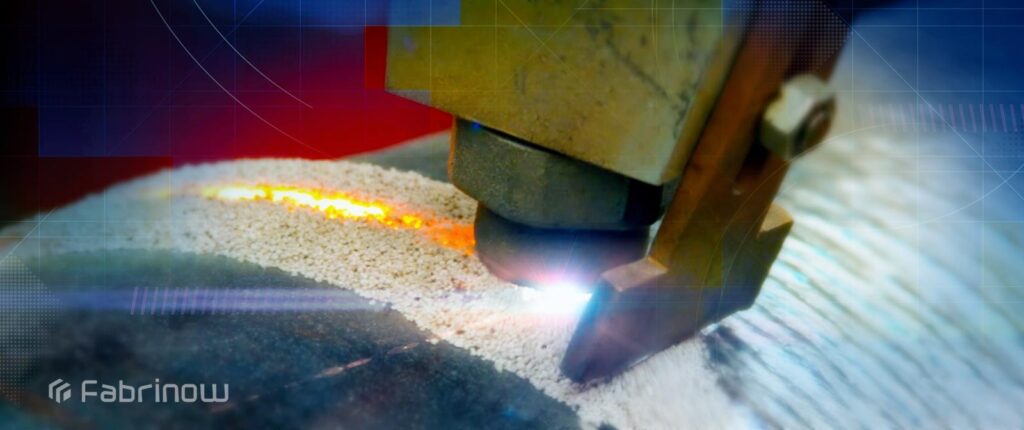
در جوشکاری زیرپودری، توجه به یک سری پارامترها در کیفیت جوشکاری و جوش نهایی تولید شده، اهمیت دارد. این پارامترها و متغیرهای اصلی جوشکاری زیرپودری عبارتند از:
- جریان الکتریکی
شدت جریان الکتریکی جوشکاری زیرپودری، روی فرایند جوش، هم تاثیر کیفی و هم تاثیر کمیدارد. تاثیر کمیجوشکاری همان عمق جوش است و تاثیر کیفی نیز میزان حرارت داده شده به جوش میباشد. در جوشکاری زیرپودری، غالبا از جریان با قطبیت معکوس (DCEP)، به دلیل امکان بالاتر بازیابی عناصر الکترود و اکسیداسیون کمتر، استفاده میشود. اما در صورتی که عمق جوش بیشتری مورد نیاز باشد، از جریان با قطبیت مستقیم (DCEN) استفاده میشود.
- ولتاژ
ولتاژ مورد استفاده در جوشکاری زیرپودری روی پهنای جوش و حجم ذوب شدن مواد بسیار موثر است. همچنین ولتاژ میتواند روی حرارت داده به جوش نیز کمیموثر باشد. در این صورت هرچه ولتاژ بیشتر شود، پهنای جوش نیز افزایش مییابد. در ولتاژهای بالا، جرقه و ترشح جوش زیاد است و در جوش نیز تمایل به جذب نیتروژن از هوا افزایش مییابد. با این کار، در جوش حباب یا خلل و فرج ایجاد شده و گرده جوش نیز شکل مناسبی نخواهد داشت.
اما در برابر، ولتاژ کم اندازه قطرات مذاب در نوک الکترود را افزایش داده و احتمال ایجاد مدار بسته متناوب با کاهش ولتاژ را بالا میبرد. همچنین با ولتاژ کم، ممکن است گرده جوش نامنظم و بدون نفوذ کافی تولید شده و تمایل به حبس سرباره در جوش افزایش یابد.
تاثیر ولتاژ روی حرارت نیز در برخی موارد اتفاق میافتد و با ولتاژ، گرم و سرد شدن جوش تغییر میکند. در نتیجه آن، ساختار و خواص مهندسی جوش تغییر میکند. در این صورت با افزایش ولتاژ، طول قوس افزایش یافته و قسمت عمده قو بالای سطح نمونه خواهد بود. در نتیجه آن، پودر جوش بیشتری ذوب شده، سطح جوش بیشتر شده و صاف تر میشود.
- سرعت جوشکاری
با افزایش سرعت جوشکاری، زمان جوشکاری کاهش مییابد. در این صورت حرارت ورودی نیز کمتر شده و حجم جوش یا پهنا و عمق جوش نیز کمتر خواهد بود. در واقع، سرعت جوش بالا باعث ایجاد گرده جوش لاغر میشود. از طرفی، حوضچه جوش نیز، حاصل از ذوب الکترود همراه با ذوب سطحی قطعه کار خواهد بود.
برجسته شدن گرده جوش نیز با افزایش سرعت تغییر میکند و با افزایش سرعت حرارت کمتری در قطعه توسط مکانیزم هدایت هدر میرود. در این صورت میتوان گفت که در سرعت بالاتر، بازدهی حرارت نیز بیشتر میشود.
- سیم جوش
ترکیب شیمیایی جوش، همان ترکیب قطعه کار و سیم جوش است. در این صورت، با تغییر نوع سیم جوش، ترکیب فلز جوش و خواص مهندسی آن نیز تغییر میکند. در کنار آن، شکل مقطع سیم جوش نیز مهم است؛ زیرا جوشی که از سیم جوش با مقطع گرد حاصل میشود، پهنای جوش کمتر و عمق نفوذ بیشتری نسبت به سیم جوش نوع تسمهای دارد.
در صورتی که سطح مقطع الکترود یا سیم جوش گرد باشد، با کاهش قطر آن، چگالی جریان و عمق نفوذ جوش بیشتر میشود. از دیگر پارامترهای مربوط به سیم جوش نیز میتوان به زاویه و میزان راندن سیم جوش اشاره کرد که توجه به آنها نیز در مراحل انجام جوشکاری زیرپودری اهمیت دارد.
- طول موثر الکترود
فاصله مکانی که جریان برق به سیم وصل میشود تا مکانی که سیم به سطح کار میرسد، همان طول موثر الکترود است. با افزایش این طول، مقاومت الکتریکی سیم افزایش یافته و در نتیجه آن حرارت تولیدی نیز افزایش یابد. در نتیجه، نرخ رسوب و ذوب نیز بالاتر خواهد رفت.
افزایش طول موثر سیم جوش، روی کاهش نفوذ جوش نیز تاثیرگذار است. در واقع اگر طول موثر الکترود کم باشد، یعنی نازل بیش از اندازه پایین آمده و با حرکت نازل و جارو کردن پودر اطراف آن، در محافظت قوس توسط پودر خلل وارد میشود. همچنین ممکن است به دلیل حرارت ایجاد شده، نازل ذوب شود.
- پودر فلاکس مورد استفاده
در رابطه با پودر جوش یا همان فلاکس، عدد بازیسیته اهمیت دارد. هرچه این عدد بیشتر باشد یعنی ترکیبات قلیایی موجود در پودر مانند CaO بیشتر است و تصفیه مذاب بهتر انجام میشود. از جمله رایج ترین پودرهای فلاکس مورد استفاده در جوشکاری زیر پودری میتوان به پودر سیلیکات منگنز (MS)، پودر سیلیکات کلسیم (CS)، پودر سیلیکات زیرکونیوم (ZS)، پودر سیلیکات روتیلی (RS)، پودر آلومینات سیلیکات (AS)، پودر آلومینات قلیایی (AB)، پودر آلومینات روتیلی (AR)، پودر قلیایی آلومینات فلوراید (AF)، پودر فلوراید قلیایی (FB) و پودر آهن (IP) اشاره کرد.
مزایا و معایب جوشکاری زیرپودری چیست؟
جوشکاری زیرپودری به دلیل ویژگی متعددی که دارد در صنایع مختلفی مورد استفاده قرار میگیرد. از جمله مهمترین ویژگیها و مزایای این فرایند میتوان به موارد زیر اشاره کرد:
- در فرایند این جوشکاری میتوان از دستگاه جوشکاری به صورت خودکار و اتوماتیک استفاده کرد. در این صورت تنها نیاز به حضور یک متصدی دستگاه خواهد بود و به این واسطه، احتمال خطاهای انسانی کاهش مییابد.
- این فرایند جوشکاری، بیشترین نرخ رسوب را شامل شده و به این واسطه سرعت بالایی را نیز شامل میشود.
- نسبت به روکش الکترود در جوشکاری دستی، ذرات فلاکس مورد استفاده در این فرایند، حفاظت بهتری از نوار جوش را فراهم میکنند.
- در فرایند جوشکاری زیرپودری، اتصالات را میتوان با شیار کم عمق آماده کرد که این مورد باعث مصرف کمتر فلز پرکننده میشود. حتی در برخی موارد برای اتصالات بین ورقهای با ضخامت کمتر از 1.4 نیاز به استفاده از شیار نخواهد بود.
- در این فرایند میتوان جوش را با سرعت حرکت و نرخ رسوب بالا، روی سطح صاف، استوانه ای یا لوله ای، با هر اندازه و ضخامتی انجام داد و در این موارد محدودیتی وجود کرد. حتی جوشکاری زیرپودری برای ساخت کردن سطحی نیز مناسب است.
- فلاکس مورد استفاده در این فرایند به عنوان اکسیدزدا و آخال زدا عمل کرده و برای خارج کردن ترکیبات ناخواسته از حوضچه جوش مورد استفاده قرار میگیرد تا جوشی سالم با خواص مکانیکی مناسب ایجاد شود.
- در این فرایند میتوان برای جوش فولادهای غیر آلیاژی از سیمهای الکترود ارزان و کم کربن استفاده کرد. سیمهای فولادی کم برن بدون پوشش یا با پوشش نازک مسی برای هدایت بهتر و جلوگیری از خوردگی بسیار موثر عمل میکنند.
- امکان انجام جوشکاری زیرپودری در شرایطی با وزش بادهای نسبتا شدید نیز وجود دارد. در این شرایط نیز فلاکس مورد استفاده حفاظت مناسب را فراهم میکند.
- فرایند جوش زیر پودری یک فرایند پیوسته است که سرعت تولید و نرخ یا بازدهی رسوب بالایی دارد.
- این فرایند به دلیل حرارت ورودی بالا و عمق نفوذ زیاد برای جوشکاری قطعات با ضخامت بالا نیز مناسب است.
در کنار تمامی این مزایا، فرایند جوش زیرپودری یک سری محدودیتها و معایب را نیز شامل میشود؛ که عبارتند از:
- از این فرایند نمیتوان برای تمامیفلزات و آلیاژها استفاده کرد.
- در طی این فرایند امکان ایجاد ترک انقباضی به دلیل شکل گرده جوش، طرح نامناسب اتصال و یا انتخاب مواد جوش نامناسب وجود دارد.
- در این فرایند همچنین امکان ایجاد ترکهای هیدروژنی نیز وجود دارد. برای جلوگیری از ایجاد این ترکها نیز بهتر است روغنها و آلودگیهای موجود در فلاکس الکترود و سطوح اتصال حذف شوند و ورق فلاکس و الکترود نیز کاملا تمیز و خشک باشند.
- جوشکاری زیرپودری نیاز به تجهیزات پیچیده و گران دارد.
- این فرایند برای جوشکاری قطعاتی که ضخامتی کمتر از 4.5 میلیمتر دارند، مناسب نیست.
برای اینکه در فرایند جوشکاری زیرپودری نتیجه مطلوبی حاصل شود، فلز پایه باید کاملا یکنواخت بوده و بدون پوسته اکسیدی، غبار، روغن، زنگ زدگی و یا سایر آلودگیها باشد.
دستگاه و تجهیزات جوش زیر پودری کدامند؟
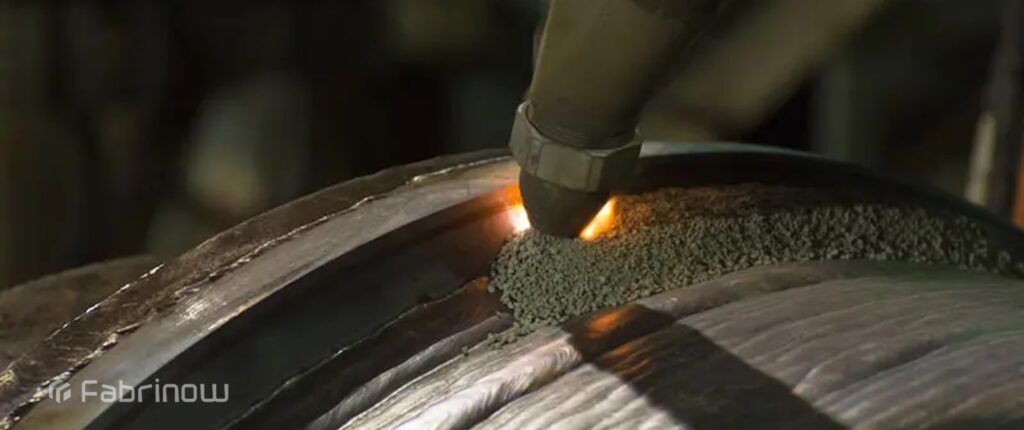
برای انجام فرایند جوش زیرپودری نیاز به استفاده از دستگاه مخصوص وجود دارد. کار با این دستگاه غالبا ساده است و فرایند جوش با استفاد از آن غالبا به صورت اتوماتیک یا مکانیزه انجام میشود. دستگاه جوش زیر پودری باعث ساده تر شدن فرایند جوشکاری شده و همچنین باعث میشود که جوش الکتریکی در محفظه ای از مواد معدنی خاص قرار بگیرد. در کنار آن به کمک یک قوس الکتریکی از پخش شدن مواد مذاب جلوگیری کرده و باعث ذوب شدن فلز میشود.
با استفاده از دستگاه جوش زیرپودری میتوان نرخ پر کردن فرایند را افزایش داده و تا 45 کیلوگرم درصد مواد مذاب تولید کرد. با این کار هر شکافی به سادگی پر میشود. آمپر مصرفی دستگاه نیز غالبا بین 300 تا 2000 آمپر است و حتی با برخی از دستگاههای خاص جوش زیرپودری میتوان از 5 هزار آمپر نیز بهره گرفت.
دستگاههای جوش زیرپودری خود شامل دو نوع خودکار و نیمه خودکار هستند. در دستگاههای نیمه خودکار انتقال قوس الکتریکی و پودر محافظ توسط جوشکار انجام شده و فرایند نیز به صورت خودکار توسط دستگاه انجام میشود.. همچنین در روش نیمه خودکار، محافظ در اثر نیروی گرانش روی محل ذوب شده قرار میگیرد که این دستگاه مناسب کارهای معمولی و متوسط و الکترودهایی با قطر کم است.
اما دستگاههای خودکار جوشکاری دستگاههای بزرگ صنعتی هستند که شامل کنترل کنندههای خودکار و اتوماتیک میباشند. با استفاده از این دستگاهها فرایند جوش به صورت خودکار و با تعریف عملیاتهای کامپیوتری انجام شده و نیازی به دخالت اپراتور وجود ندارد.
از جمله سایر تجهیزات مهم و رایجی که در فرایند جوشکاری زیرپودری مورد استفاده قرار میگیرند نیز میتوان به مولد، مخزن پودر، نازل پودر، انبر، سیستم نگهداری و هدایت الکترود لخت و روبات هدایت انبر و ریلهای مربوطه اشاره کرد.
سوالات متداول
اهمیت دانه بندی در جوشکاری زیرپودری چیست؟
به دلیل تاثیر اندازه دانههای پودر جوش بر مصرف بهینه آن در جریانهای جوش، اندازه این دانهها در فرایند جوشکاری بسیار اهمیت دارد. برای این منظور توصیه میشود در جریانهای بیشتر از 1500 آمپر از درصد ذرات ریز بیشتر و ذرات درشت کمتر استفاده شود.
پودرهای چسبیده شده که در جریانهای کمتر مورد استفاده قرار میگیرند، به اندازه ذرات کمتر بستگی دارند و غالبا در یک سایز تولید میشوند. برای این نوع پودرها نیز حداکثر جریان مناسب بین 800 تا 1000 آمپر است. برای برخی انواع پودر ترکیب شده نیز مانند انواع سیلیکات کلسیم اصلاح شده میتوان جریانی تا 2000 آمپر را به کار برد.
آیا در جوشکاری زیرپودری میتوان از ترکیب پودرهای جوش استفاده کرد؟
در فرایند جوشکاری زیرپودری از برخی ترکیبهای پودرهای جوش برای دستیابی به خواص پیشرفته تر و هزینه اقتصادیتر و همچنین ظاهر مناسبتر گرده جوش استفاده میشود. به عنوان مثال، برخی ترکیبات پودرها با بازیسیته بیشتر که شامل مقادیر CaF2 یا CaO هستند، خواص مکانیکی بهتری در فلز جوش ارائه میدهند.
همچنین افزودن تیتانیوم به ترکیب پودرها باعث پایداری قوس بیشتر و بهبود ظاهر جوش اکسید فلزات خاص در فولادهای آلیاژی میشوند. در واقع میتوان از فلاکسهای کاربردی خاص و ترکیب شده برای منظورهای خاص طراحی در جوشکاری استفاده کرد.
چه عواملی در کیفیت جوشکاری زیر پودری موثرند؟
از جمله عوامل و پارامترهای موثر در کیفیت جوشکاری زیرپودری میتوان به جریان الکتریکی، ولتاژ، سرعت جوشکاری، سیم جوش، طول موثر الکترود و نوع پودر فلاکس اشاره کرد.
جوشکاری زیرپودری چه کاربردی در صنعت دارد؟
جوشکاری زیر پودری در صنایع مختلف کاربردهای بسیاری دارد که از جمله رایج ترین این کاربردها میتوان به ساخت تیر ورق، جوشکاری مخازن ذخیره، ساخت سازههای سنگین، ساخت واگنهای راه آهن، ساخت و اتصال خطوط لوله، ساخت قطعات کشت و ساخت مخازن تحت فشار اشاره کرد.
چرا استفاده از فرایند جوشکاری زیرپودری اهمیت دارد؟
این فرایند برای لایه گذاری و انجام ترمیمهای سطحی بسیار مناسب است. همچنین یک روش کاملا مقرون به صرفه مورد اطمینان محسوب میشود که علاوه بر کیفیت بالای جوش، حفاظت بالایی را برای اپراتور نیز فراهم میکند. جوشکاری پودری قابلیت نفوذ بالایی را نیز شامل میشود. به همین دلیل در صنایع و کاربردهای مختلف مورد استفاده قرار میگیرد.
جمع بندی
جوشکاری زیر پودری یکی از فرایند جوشکاری قوس و از فرایندهای رایج صنعتی است.در این فرایند نوک الکترود درون پودری از مواد معدنی ویژ قرار گرفته و یک یا چند قوس زیر این پودرهای مواد معدنی تشکیل میشود. در این صورت از قوس به وجود آماده به عنوان یک منبع حرارتی مفید برای جوشکاری استفاده میشود. این فرایند مزایا و ویژگیهای متعددی را در جوشکاری فلزات و برخی از آلیاژهای رایج ارائه میدهد. به همین دلیل در صنایع مختلف به طور گسترده مورد استفاده قرار میگیرد.