برای ساخت و تولید قطعات روشهای متنوعی مورد استفاده قرار میگیرند. یکی از روشهایی که در این زمینه قدمت بالایی دارد، متالورژی پودر است که در تولید قطعات پیچیده و تولید قطعات با مقیاس تولید بالا، قابلیتهای منحصر به فردی ارائه میدهد و یک روش بسیار کاربردی محسوب میشود. در گذشتههای دور از تکنیکهای متالورژی پودر برای شکل دادن به فلزاتی با نقطه ذوب بالاتر استفاده میشد و امروزه از این روش در صنعت برای انواع فلزات در صنایع مختلف استفادههای متعددی میشود.
اگر میخواهید با متالورژی پودر، ویژگیها و کاربردهای آن بیشتر آشنا شوید، مطالعه این مقاله از فبرینو را از دست ندهید.
متالورژی پودر چیست؟
متالورژی پودر (Powder metallurgy) یکی از روشهای رایج برای تولید فلزات با استفاده از تکنیک فشرده سازی است که در آن از پودر فلز استفاده میشود. در فرایند این تکنیک، پودر فلز قالب گیری شده و تحت فشار قرار میگیرد تا فلز مورد نیاز ایجاد شود. در این صورت با استفاده از ضایعات نیز میتوان قطعات مورد نیاز را تولید کرد. این روش بر مبنای فشردن، شکل دهی و تف جوشی ذرات به یکدیگر طراحی شده و منجر به ایجاد یک قطعه مستحکم و صلب میشود.
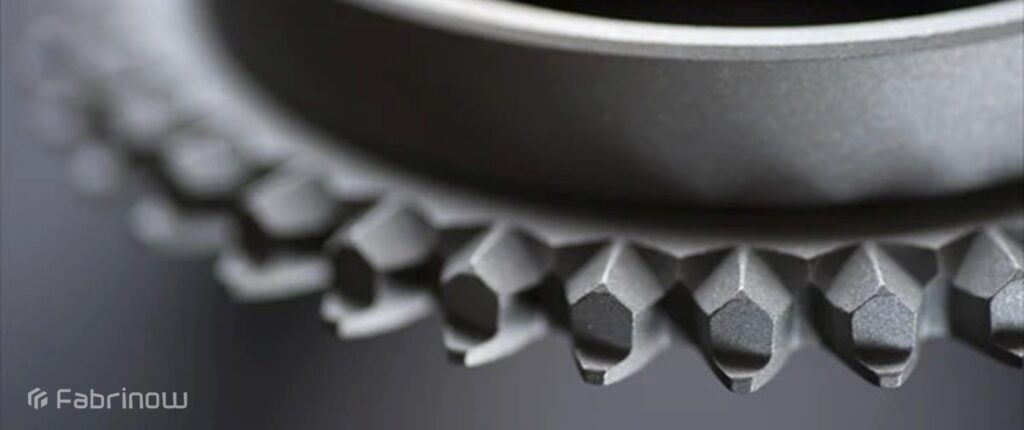
در فرایند متالورژی پودر، عملیات تف جوشی زیر نقطه ذوب انجام شده و تحت این شرایط، ذرات پودر یک سری پیوندهای قوی تشکیل شده و در اصطلاح به یکدیگر جوش میخورند. در این صورت باعث ایجاد یک ساختار همگن و مستحکم میشوند. این فرایند در شکل دهی فلزاتی که انعطاف پایینی داشته و نقطه ذوب بالایی دارند، مانند تنگستن، مولیبدن و تانتالیوم کاربرد زیادی دارد. تولید قطعات با این فلزات از طریق روشهای ذوب و ریخته گری بسیار دشوار است.
متالورژی پودر برخی از محدودیتهای روشهایی مانند ریخته گری، نورد، اکستروژن و آهنگری را حذف کرده است و از آن میتوان برای تولید محصولاتی که قابلیت تولید با این روشها را ندارند، استفاده کرد. همچنین اکثر قطعات و محصولاتی که با استفاده از این روش تولید میشوند، نیازی به ماشین کاری یا عملیات حرارتی تکمیلی ندارند.
کاربرد متالورژی پودر چیست؟
همانطور که گفته شد، متالورژی پودر از روشهای تولید رایج صنعتی است که امروزه به طور گسترده ای مورد استفاده قرار میگیرد. این روش در موارد مختلفی کاربرد دارد که رایجترین آنها عبارتند از:
- آلیاژ کردن فلزهای غیرقابل آلیاژ بخصوص برای صنعت برق و استفاده از پودرهای مس، گرافیت، نیکل و ترکیب تنگستن و مس
- ترکیب کردن فلزها و غیر فلزات اعم از تولید مواد اصطکاکی ساخته شده از آهن، آزبست و مس
- ترکیب کردن فلزاتی که نقطه ذوب بالایی دارند برای استفاده در ریخته گری مانند تنگستن و مولیبدن
- ساخت قطعات فلزی با خواص مکانیکی عالی مانند تولید یاتاقانهایی که به دلیل وجود شبکهای از خلل و فورج پیوسته به طور خودکار روغن کاری میشوند.
- ساخت قطعات ظریف و دقیق مانند بوشنها، بادامکها و چرخ دندهها
مراحل فرایند متالورژی پودر چیست؟
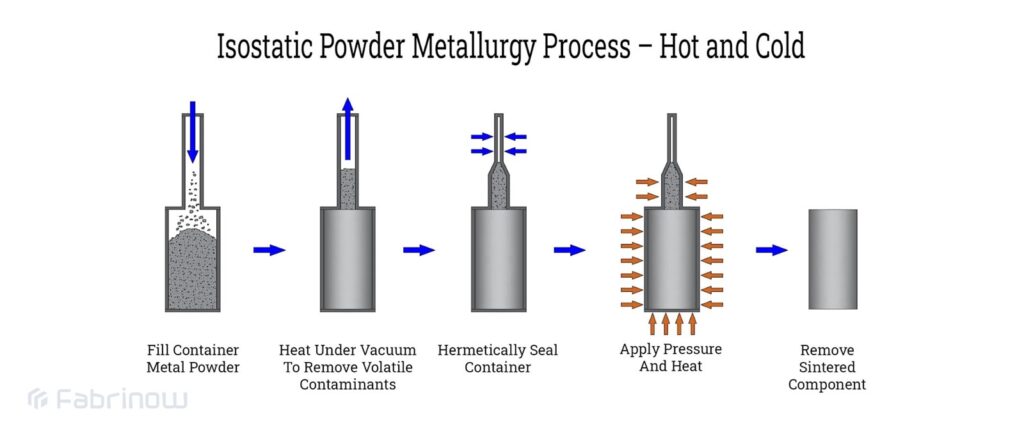
ساخت قطعات با استفاده از روش متالورژی پودر مراحل مختلفی را شامل میشود؛ که عبارتند از:
- تولید و آماده سازی پودر فلز
اولین مرحله از فرایند متالورژی پودر، تهیه و تولید پودر فلز است. برای این منظور، پودر فلز به سه روش مکانیکی، شیمیایی و فیزیکی تولید میشود. یکی از مهم ترین تکنیکها برای تولید پودر، استفاده از تکنیک افشاندن مذاب (اتمایزینگ) میباشد که بسیار پرکاربرد بوده و از روشهای مکانیکی محسوب میشود. در این روش، توسط گاز یا مایعی که از یک افشانک خارج میشود، فلز مذاب اتمیزه شده و پودر میشود. پودر ایجاد شده نیز پس از جمع آوری و مش بندی مورد استفاده قرار میگیرد. در این فرایند از انواع فلزات میتوان استفاده کرد.
- ترکیب و مخلوط کردن پودر
معمولا پودرهای خالص تولید شده در مرحله قبل، تمام ویژگیهای خوب را ندارند. به همین دلیل از آنها در مخلوط با سایر پودرها که نقش روانساز را دارند، استفاده میشود. در این صورت، پودر دو یا چند ماده برای روان سازی و حتی رسیدن به آلیاژی با استحکام بالا، با پودر فلز مخلوط میشود. در فرایند مخلوط سازی، توزیع یکنواخت پودر با مواد افزودنی اعم از چسب و یا سایر مواد روان ساز نیز امکان پذیر است.
در کیفیت محصول نهایی یا فرآورده متالورژی پودر، یکنواختی مخلوطی که از این مرحله به دست میآید، بسیار اهمیت دارد.
- فشرده سازی
پودر مورد نیاز پس از آماده سازی و مخلوط کردن، در یک سری قالبهای مشخص با فشار یا پرس فشرده میشود. برای این منظور، جکهای قالب پرس، از دو جهت، فشار لازم را به مواد پودری وارد میکنند و بالا بردن چگالی آنها امکانپذیر میشود. یکنواختی و چگالی بالا ویژگی مطلوبی است که توسط پرسهای هیدرولیکی-مکانیکی یا ترکیبی از آنها و با فشردن سراسری قطعه ایجاد میشوند.
این مرحله برای کاهش تخلخل و اجتناب از آن و همچنین برای افزایش دانسیته انجام میشود. فشاری که در این مرحله به پودر اعمال میشود، بین 80 تا 1600 مگاپیکسل متغیر است که متناسب با خواص پودر و چسب اعمال میشود. به دلیل تمایل بالای ذرات پودر به سایش و وجود فشار، معمولا قالبهای مورد استفاده در این فرایند از جنس فولاد ابزار سخت ساخته میشوند. همچنین برای پودرهایی که سایش بیش از حد تولید میکنند یا برای تولید انبوه قطعات، غالبا از کاربیدهای سمانیت برای ساخت قالب استفاده میشود.
- زینترینگ یا تف جوشی
در مرحله فشرده سازی اولیه، استحکام کافی در قطعات ایجاد نمیشود. به همین دلیل در این مرحله، یک فشار پایانی اعمال میشود تا قطعه خام شکل گرفته از فشرده سازی مرحله قبل، بتواند تنشهای کاری را تحمل کند. زینترینگ (sintering) یا تف جوشی عملیاتی است که با استفاده از یک سری پیوند قوی بین ذرات ایجاد میشود. تحت این عملیات، قطعه فشرده شده در دمای بالا و با جو کنترل شده قرار میگیرد. دمای این عملیات غالبا بین 70 تا 90 درصد دمای ذوب پودر فلز است و در این حالت مواد زودگداز ذوب شده و مواد دیرگداز حفرههای خالی را پر میکنند.
پس از اتمام فرایند متالورژی پودر، غالبا یک سری عملیات اولیه شامل پرسکاری مجدد مواد برای رسیدن به دقت ابعادی بالا، کیفیت سطح مطلوب، افزایش دانسیته و افزایش مقاومت به خوردگی در فرآورده متالورژی پودر، انجام میشوند. از فرایند متالورژی پودر علاوه بر ساخت رشتههای مقاوم تنگستنی میتون برای ساخت قطعاتی که امکان ساخت آنها با سایر روشهای صنعتی وجود ندارد، استفاده کرد.
انواع فلزات مورد استفاده در متالورژی پودر چیست؟
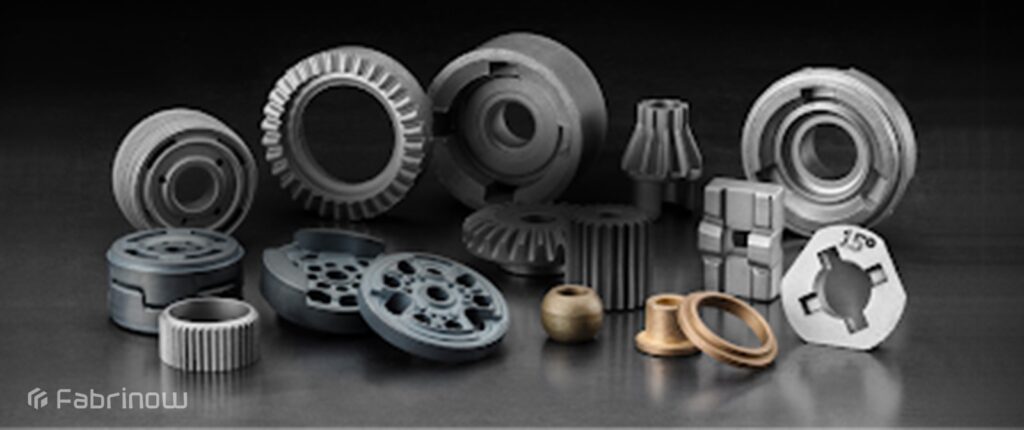
برای فلزات مورد استفاده در فرایند متالورژی پودر، محدودیتهای کمی وجود دارد و میتوان در این فرایند از انواع مختلف فلزات استفاده کرد. گرچه برخی از فلزات به دلیل خواص و ویژگیهایی که دارند، بیشتر از سایر فلزات در این فرایند استفاده میشوند. برخی از رایجترین فلزات مورد استفاده در متالورژی پودر عبارتند از:
- فولاد ضد زنگ
این فولاد ویژگیهای مثبت فراوانی دارد. این فولاد در تولید قطعاتی که مقاومت بالا در برابر خوردگی و مقاومت در برابر زنگ زدگی، در تولید آنها اهمیت دارد، بسیار مورد استفاده قرار میگیرد. سریهای 300 و 400 از فولادهای ضد زنگ، رایج تر از سایر سریها مورد استفاده قرار میگیرند.
همچنین فولاد ضد زنگ گرید L316، به دلیل مقاومت بالا در برابر خوردگی، چقرمگی مطلوب و مقاومت در برابر اسیدها به طور گسترده در تولید قطعات هوافضا، ابزار پزشکی، قطعات کشتی و قطعات خودرو استفاده میشود. در واقع، ویژگیهای مطلوب و تطبیقپذیری فولاد ضد زنگ باعث استفاده گسترده آن در کاربردهای مختلف و تولید قطعات با متالورژی پودر شده است.
- فلز مس
پودر مس و آلیاژهای آن در برابر زنگزدگی و خوردگی مقاوم هستند. به همین دلیل در کاربردهایی که رطوبت زیادی در آنها وجود دارد، بسیار کاربرد دارند. پودر فلز مس و یا آلیاژهای آن میتوانند به صورت پودرهای پیش آلیاژی یا مخلوط عنصری نیز مورد استفاده قرار میگیرند. یکی از آلیاژهای رایج فلز مس، آلیاژ برنز است که از ترکیب مس با قلع ساخته شده و در تولید بلبرینگهای خود روان کننده در فرایند متالورژی پودر بسیار کاربرد دارد.
- فلز نیکل
نیکل نیز از فلزاتی است که در برابر خوردگی و در برابر دمای بالا مقاوم است. یکی از آلیاژهای پر کاربرد نیکل نیز آلیاژ مونل است که از ترکیب مس و نیکل ساخته شده و بسیار سخت است. این آلیاژ در برابر اثرات آب شور نیز مقاوم میباشد. فلز نیکل خود انعطاف پذیر و سخت بوده و قابلیت چکش خواری دارد. همچنین یک رسانای خوب الکتریسیته و گرما میباشد که به آرامیدر اسیدهای رقیق حل میشود. از فلز نیکل در ساخت قطعات توربینهای گازی و موتورهای موشک در فرایند متالورژی پودر بسیار استفاده میشود.
فلز آلومینیوم
آلومینیوم خام بسیار نرم، انعطافپذیر و سبک است؛ به همین دلیل اکثر قطعات آلومینیومیبا استفاده از آلیاژهای آلومینیوم ساخته میشوند. آلومینیوم را میتوان به سادگی شکل داد و به دلیل وزن سبکی که دارد تقریبا در تمامیصنایع بخصوص صنایع هوافضا و خودروسازی بسیار کاربرد دارد.
- فلز آهن
پودر آهن، یک پودر کریستالی است که رنگ سیاه خاکستری دارد. نقطه ذوب این پودر غالبا 1837 درجه سانتی گراد و چگالی آن حدودا 7.694 گرم بر سانتی متر مکعب است. پودر آهن، برای فرایند متالورژی پودر، با استفاده از اتمیزه کردن آب با فشار بالا تولید میشود. برای این منظور، پودر آهن در دمای بالا در حدود 1121 درجه سانتی گراد پخته میشود.
فلز آهن نیز یک فلز نرم است و معمولا با کربن مخلوط میشود تا فولاد تشکیل شود.
فلز آهن یکی از رایج ترین فلزاتی که در فرایند متالورژی پودر برای تولید قطعات خودرو اعم از شفت، بازوهای راکر و روتورهای پمپ روغن به طور گسترده استفاده میشود.
فلز تیتانیوم
از میان انواع فلزاتی که در فرایند متالورژی پودر مورد استفاده قرار میگیرند، تیتانیوم گران ترین فلز است. این فلز یک ظاهر نقره ای داشته، بسیار مستحکم است و در برابر خوردگی مقاومت بالایی دارد. فلز تیتانیوم نیز همانند سایر فلزات با استفاده از فرایندهای مختلفی تولید میشود و زمانی که به پودر تبدیل میشود، رنگ خاکستری یا سیاه دارد. از این پودر در فرایند متالورژی پودر برای تولید قطعات هواپیما، موشک و پردازش شیمیایی استفاده میشود.
همانطور که گفته شد، برای انواع فلزات قابل استفاده در فرایند متالورژی پودر، محدودیتهای کمیوجود داشته و انتخابهای متعددی وجود دارد. فلزات گفته شده به دلیل خواص و ویژگیهایی که دارند در این فرایند به طور رایج و بیشتر از سایر فلزات مورد استفاده قرار میگیرند. انتخاب این فلزات به ویژگیهای مورد نیاز و عوامل مورد توجه در تولید قطعات بستگی دارد.
تکنیکهای شکلدهی و پردازش پودر چیست؟
همانطور که گفته شد، پودر فلزات با استفاده از روشهای مختلفی تولید میشود که انتخاب این روشها به اندازه، شکل، ریز ساختار، ترکیبات شیمیایی و هزینههای تولید بستگی دارد. انواع روشهای تولید پودر عبارتند از:
- روش مکانیکی
در این روش، ترکیبی از فرایندهای مکانیکی سایش، ضربه، برش و تراکم برای تولید پودر مورد استفاده قرار میگیرند که مهم ترین آنها عبارتند از:
- ماشین کاری
از فلزات ماشین کاری شده و برادههای حاصل از آنها برای تولید پودرهای درشت دانه و نامنظم استفاده میشود. از روش ماشین کاری غالبا برای فلزات فعالی مانند برلیوم، نقره و منیزیم استفاده میشود. پودرهایی که با استفاده از این روش تولید میشوند، غالبا کیفیت بالایی ندارند.
- خرد کردن
با استفاده از این روش، فلز جامد به قطعات کوچک تجزیه میشود و از آن برای تولید پودر فلزات سخت و ترد و پودرهای اکسیدی استفاده میشود. در این روش، از تکنیکهای غلتکی، فکی و چکشی برای تولید پودر استفاده شده و پودرهای تولید شده نیز غالبا غیر یکنواخت و درشت هستند.
- آسیاب کردن
در این روش از نیروهای ضربه، سایش، برش و فشار برای اعمال نیرو به پودرها استفاده شد و یکی از روشهای کلاسیک برای تولید پودرهای ترد محسوب میشود. همچنین غالبا در این روش از آسیابهای گلوله ای، آسیابهای سیاره ای و آسیابهای لرزشی استفاده میشود.
- آلیاژسازی مکانیکی
در این روش، از حرکت تلاطمیبین گلولهها برای تولید دانههای پودر آلیاژی استفاده میشود. به این صورت که مخلوطی از گلولههای ساینده و پودرهای عنصری در محفظه آسیاب ریخته شده و با تکرار ضربه، جوش سرد بین دانهها ایجاد میشود. سپس دانههای جوش خورده مجددا خرد شده و در نهایت پودرهای مرکب تولید میشوند. آلیاژسازی مکانیکی دقیق ترین و موفق ترین روش برای تولید آلیاژهای دارای توزیع دانههای اکسیدی زیر میکرون است که در فرایند متالورژی پودر مورد استفاده قرار میگیرد.
- روش فیزیکی
از دیگر روشهای تولید پودر میتوان به روشهای فیزیکی اشاره کرد که مهم ترین و رایج ترین تکنیکهای آن عبارتند از:
- گرانوله کردن
در این روش، مواد مذاب مورد استفاده از روی صفحات مشبک عبور کرده و قطرات سقوط میکنند. در نهایت نیز قطرات منجمد میشوند. تحت این فرایند، پودرها باید فشرده سازی و متراکم شده و تحت فشار زیاد گرانوله میشوند.
- اتمیزاسیون
در تکنیکهای این روش، قطرات مذاب فلز از طریق جدا کردن از جریان مذاب یا هر روش دیگر و انجماد قطرهها قبل از رسیدن به یک سطح جامد، تولید میشوند. در این روش، برخلاف سایر روشها میتوان پودر آلیاژهای همگن یا مواد پیش آلیاژ شده را تولید کرد.
از جمله تکنیکهای مهم اتمیزاسیون میتوان به اتمیزاسیون گازی، اتمیزاسیون با سیال آبی یا روغن، اتمیزاسیون با نیروی گریز از مرکز، اتمیزاسیون در خلاء، اتمیزاسیون التراسونیک و اتمیزاسیون نوسانی اشاره کرد.
- روش شیمیایی
روشهای شیمیایی تولید پودر برای تمامی فلزات مورد استفاده قرار میگیرند. این روش شامل واکنشهای فاز جامد، مایع و گاز است که مهمترین و رایجترین تکنیکهای آن عبارتند از:
- الکترولیز
در این روش، پودر فلزات تحت شرایط مناسب بر سطح کاتد یک ظرف الکترولیز رسوب داده میشود.
- احیا در حالت جامد
در این روش، از اکسیدهای یا نمکهای فلزی مانند کربناتها یاهالیدها به عنوان مواد اولیه استفاده شده و پس از خالص شدن، این مواد توسط عوامل احیاکننده در دماهای زیر نقطه ذوب تحت فرایند قرار میگیرند.
- رسوب از فاز گازی
در این روش، رسوب ذرات فاز بخار فلزات یا ترکیب آنها برای تولید پودر استفاده میشود که دو تکنیک رسوب دهی شیمیایی بخار و رسوب دهی فیزیکی بخار را شامل میشود. در رسوبدهی شیمیایی بخار، واکنشهای شیمیایی روی سطح گرم رخ داده و در نتیجه آن رسوب به صورت لایهای نازک روی زیر لایه تشکیل میشود.
در رسوبدهی فیزیکی بخار نیز از تبخیر استفاده شده و مواد از یک منبع جامد یا مایع به شکل اتم یا مولکول تبخیر میشوند. در نهایت نیز، بخار در محیط خلاء، گاز فشار پایین یا پلاسما زیر لایه را در بر میگیرد.
از روش رسوب از فاز گازی میتوان برای تولید پودرهایی از فلزات فرار مانند روی، کادمیوم، سرب و منیزیم استفاده کرد. این روش یک روش بسیار اقتصادی محسوب میشود.
- تجزیه حرارتی کربنیلهای فلزی
در این روش کربنیلهای فلزی تولید شده و این کربنیلها در اثر حرارت به کربن مونوکسید و فلز تجزیه میشوند. تجزیه حرارتی این کربنیلها یک فرایند گرماگیر است و با افزایش مقدار، کیفیت محصول نیز افزایش مییابد. به همین دلیل در فشارهای پایین و دماهای بالا بسیار کاربرد دارد. این روش مصرف کامل ماده خام، نیاز به انرژی کم و قابلیت اجرا به صورت تمام اتوماتیک را شامل میشود اما برای تعداد محدودی از فلزات قابل انجام است.
تجهیزات مورد استفاده در فرایند متالورژی پودر چیست؟
فرایند متالورژی پودر در مراحل مختلفی انجام میشود که هر مرحله نیاز به تجهیزات خاصی داشته و بسته به تکنیک مورد استفاده، متفاوت است. در این صورت تجهیزات مهم این فرایند را میتوان در موارد زیر خلاصه کرد:
- تجهیزات تولید پودر اتمیزه
برای تولید پودر در فرایند متالورژی پودر غالبا از روش اتمیزه کردن استفاده میشود. برای اتمیزه کردن نیاز به دستگاه مخصوصی وجود دارد که این دستگاه از جریان آب با سرعت بالا برای اتمیزه کردن فلز مذاب به ذرات استفاده میکند. همچنین این دستگاه قادر است در هر مرحله بین 10 تا 10000 کیلوگرم پودر تولید کند.
- دستگاه فشرده سازی (پرس)
دستگاههای پرس که برای فرایند متالورژی پودر مورد استفاده قرار میگیرند از لحاظ ساختار و پیکربندی مشابه با پرسهای مورد استفاده برای شکل دادن به فلز هستند. در این صورت این دستگاهها نیز شامل انواع مختلفی اعم از دستگاههای پرس مکانیکی، هیدرولیک، سندان، دورا، ایزو استاتیک و انتقالی میباشند. این دستگاههای پرس میتوانند مواد زیادی را به شکلها، اندازهها و تراکمهای مورد نیاز هر قسمت فشرده کنند.
- تجهیزات زینترینگ (تف جوشی)
قطعات غالبا پس از فشرده سازی به طور کامل تولید میشوند اما به اندازه کافی پایدار نیستند. فرآورده متالورژی پودر برای تبدیل شدن به یک فرم جامد باید تحت فشار و حرارت قرار بگیرند که این عملیات توسط دستگاه زینترینگ انجام میشود. تحت زینترینگ یا تف جوشی قطعه در اثر حرارت و فشار بدون ذوب یا مایع شدن، فشرده میشود.
خواص پودر فلز به چه عواملی بستگی دارد؟
برای انتخاب پودر فلز مناسب برای تولید یک قطعه در فرایند متالورژی پودر، عوامل و پارامترهای مختلفی تاثیرگذار هستند که از جمله مهمترین آنها عبارتند از:
- اندازه و توزیع ذرات: شکل ذرات به روش مورد استفاده در تولید پودر بستگی دارد. ذرات پودر کروی شکل خاصیت زینترینگ عالی دارند. همچنین ذرات نامنظم نیز برای قالب گیری مناسبتر هستند. در فرایند متالورژی پودر غالبا از پودرهایی با سایز 100 میکرون استفاده میشود.
- چگالی پودر: چگالی ظاهری پودر همان جرم پودر در واحد حجم واقعی پر شده توسط پودر است که به شکل ذرات بستگی دارد. پودرهایی که چگالی ظاهری بالایی داشته کمتر نیاز به فشرده سازی دارند تا پودرهای فشرده ای با چگالی و اندازه معین ایجاد شوند.
- نرخ جریان: زمان مورد نیاز برای خروج مقدار اندازهگیری شده پودر باید از سرعت جریان استاندارد بیشتر باشد تا نرخ تولید بالایی ایجاد شود.
- تراکم پذیری و نسبت تراکم: اندازه شکل و توزیع اندازه ذرات با تراکم پذیری و نسبت تراکم پودر در ارتباط هستند. تراکم پذیری همان نسبت حجم اولیه پودر یا حجم فشرده نشده به حجم نهایی استحکام خام پودر است. این معیار همچنین به عنوان مقاومت مکانیکی فرآورده متالورژی پودر فشرده شده شناخته میشود.
برای انتخاب پودر مناسب در تولید یک قطعه با فرایند متالورژی پودر عوامل کلیدی دیگری مانند مقاومت در برابر خوردگی، سختی، استحکام کششی، چقرمگی ضربه و استحکام خستگی نیز تاثیرگذار هستند. انواع فلزات برخی از این ویژگیها یا تمام آنها را دارند و ویژگیهای مورد نیاز برای فرآورده متالورژی پودر، تعیین کننده نوع فلز انتخابی خواهد بود.
کاربرد متالورژی پودر در صنعت چیست؟
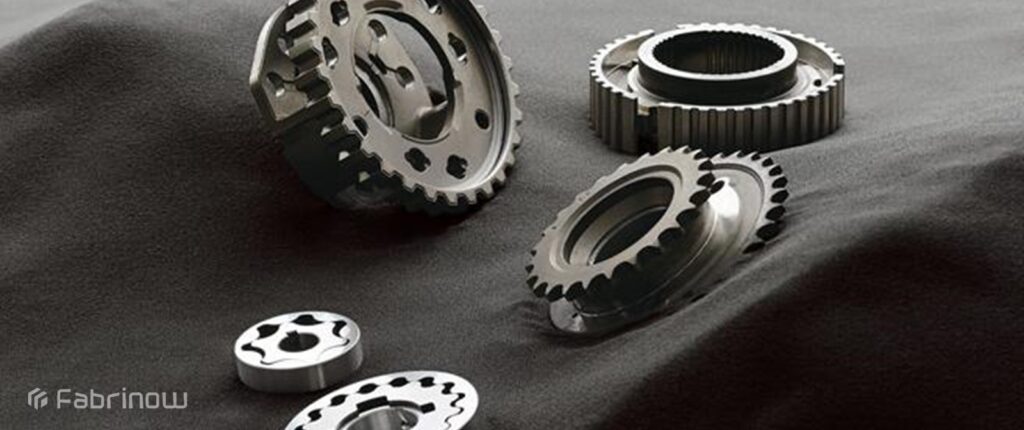
متالورژی پودر یکی از فرایندهای پرکاربرد صنعت است که استفاد از آن در تولید قطعات پیچیده و ساخت محصولاتی که با استفاده از روشهای دیگر امکان تولید ندارند، بسیار اهمیت دارد. برخی از مهم ترین صنایعی که به صورت رایج از این فرایند استفاده میکنند، عبارتند از:
- صنعت خودروسازی برای تولید قطعات خودرو اعم از چرخ دنده، یاتاقان، ذغالهای استارت و دینام، بادامکها، بوشها، پیستون، کمک فنر و هسته استاتور دینام
- صنعت تولید ماشین آلات صنعتی برای تولید قطعات مورد استفاده در ماشین آلات نساجی و سایر ماشینهای صنعتی
- صنعت هوافضا برای تولید موتورهای جت، نازل راکتها، موشکها و حفاظهای گرمایی
- صنعت جوشکاری برای لحیم، الکترود جوشکاری و فیلتر جوشکاری
- صنعت مغناطیسی برای تولید رله، مگنت و هسته
- صنعت پزشکی برای تولید آمالگامهای دندانی، پنسها و انبرک جراحی
- صنعت متالورژی برای بازیابی فلزات، ساخت کامپوزیت و آلیاژسازی
- صنعت عملیات حرارتی برای تولید ترموکوپلها، کورهها و سینیهای حمل
- صنعت پلاستیک برای تولید قالبهای پرکننده، ابزارآلات و سطوح سایشی
- صنعت چاپ برای تولید جوهر، پوشش و ورقههای چندلا
از دیگر قطعات رایجی که به روش متالورژی پودر تولید میشوند میتوان به بوشهای الکتریکی موتورها با ترکیب مواد فلزی و غیر فلزی و چرخهای سنگ با ترکیب فولاد و پودر الماس، اشاره کرد.
محدودیتهای متالورژی پودر چیست؟
برای استفاده از فرایند متالورژی پودر یک سری محدودیتها و معایب وجود دارد که عبارتند از:
- برای استفاده از این روش در اندازه و شکل قطعات تولیدی محدودیت وجود دارد و برخی قطعات پیچیده را نمیتوان با استفاده از این فرایند تولید کرد.
- تجهیزات مورد استفاده برای متالورژی پودر غالبا گران هستند و برای تولید در مقیاس کم از لحاظ اقتصادی به صرفه نیستند.
- در این فرایند قیمت مواد اولیه مورد استفاده در مقایسه با سایر روشهای تولیدی بالاتر است.
- در این فرایند در سطح و درون قطعه اکسیداسیون ذرات اتفاق میافتد؛ به همین دلیل میزان تخلخل قطعات تولیدی بالا خواهد بود و امکان تولید قطعات با تکنواختی تخلخل در کل قطعه وجود ندارد.
- در اثر ایجاد تخلخل در قطعات، سطح آنها غالبا زبر میشود.
- قطعات تولیدی با این روش خواص مکانیکی مانند خستگی و چقرمگی پایین دارند.
- با فرایند متالورژی پودر، تهیه فلزات با نقطه ذوب پایین غالبا دشوار است.
مزایای متالورژی پودر چیست؟
متالورژی پودر یکی از فرایندهای رایج و کاربردی در صنایع مختلف است که ویژگیهای متعددی را ارائه میدهد. از جمله مهم ترین مزایای این روش که باعث کاربرد گسترده آن در صنایع شده است؛ میتوان به موارد زیر اشاره کرد:
- متالورژی پودر یک فرایند سازگاری با محیط زیست است و تقریبا 97 درصد از موادی که برای تولید قطعات با فرایند متالورژی پودر مورد استفاده قرار میگیرند، بخشی از محصول نهایی خواهند بود. در نتیجه این روش ضایعات بسیار کمیداشته و علاوه بر صرفه جویی در هزینهها، برای محیط زیست نیز خطری نخواهد داشت.
- فرایند متالورژی پودر میتواند برای فلزات و غیر فلزات به صورت ترکیبی مورد استفاده قرار گرفته و در این زمینه یک فرایند کاملا انعطاف پذیر است.
- همچنین امکان تولید قطعات با انواع اشکال و اندازهها با استفاده از فرایند متالورژی پودر وجود دارد.
- قطعات و محصولات تولیدی با متالورژی پودر غالبا دقت ابعادی بالایی داشته و نیاز به پردازش ثانویه ندارند.
- مواد اولیه مورد نیاز برای متالورژی پودر به راحتی در دسترس بود و ارزان قیمت هستند. در واقع فلزات پودری مواد بسیار رایج و معمولی هستند که به سادگی تهیه میشوند.
- فرایند متالورژی پودر یک فرایند یکنواخت است ک قابلیت تکرار پذیری دارد و در تولید انبوه بسیار کاربرد دارد.
- قطعات تولید شده در فرایند متالورژی پودر مقاومت سایشی و ضریب اصطکاکی بالایی داشته و در برابر سایش مقاوم هستند؛ به همین دلیل در طولانی مدت نیاز به تعمیر و یا تعویض نخواهند داشت.
- با فرایند متالورژی پودر امکان ترکیب فلزات مختلف برای ساخت و تولید اجزای مغناطیسی و همچنین کنترل خواص مکانیکی فراهم میشود.
- قطعات تولیدشده با فرایند متالورژی پودر همگنی شیمیایی دارند و خواص آنها در سراسر ساختار آن سازگار است.
- فرایند متالورژی پودر نرخ تولید بالایی دارد و امکان تولید 500 الی 1000 قطعه در ساعت توسط این فرایند فراهم میشود.
سوالات متداول
متالورژی پودر آهن چیست؟
یکی از عناصری که با تناژ بالا با فرایند متالورژی پودر تولید میشود، پودر آهن است. پودر آهن به دلیل هزینه تولید کمتر در مقایسه با سایر فلزات، داشتن خواص بهتر مانند استحکام بالا تر در مقایسه با سایر فلزات یا غیر فلزات، امکان آلیاژ راحت تر بخصوص در ترکیب با کربن و همچنین به دلیل دسترسی آسان، کاربرد زیادی در تولید قطعات با فرایند متالورژی پودر دارد.
در انتخاب فلز مورد استفاده در فرایند متالورژی پودر چه عواملی اهمیت دارند؟
مقاومت در برابر خوردگی، سختی، استحکام کششی، چقرمگی ضربه و استحکام کششی از جمله مهمترین عوامل و پارامترهای تعیین کننده در انتخاب پودر فلز مورد استفاده در فرایند متالورژی پودر هستند. گرچه در نهایت الزامات قطعه مورد نیاز برای تولید تعیین کننده نوع فلز انتخابی خواهد بود.
چرا استفاده از فرآورده متالورژی پودر اهمیت دارد؟
در برخی موارد امکان استفاده از سایر فرایندهای صنعتی به دلیل محدودیتهای ابعادی، هندسه قطعه با نوع آلیاژ مورد استفاده وجود ندارد. در اینگونه موارد استفاده از متالورژی پودر اهمیت پیدا میکنند.
همچنین برای تهیه آلیاژهایی از دو فلز که نقطه ذوبشان با یکدیگر تفاوت دارد، تولید قطعات از ترکیب فلزات و غیر فلزات و تولید انبوه قطعات استفاده از فرایند متالورژی پودر اهمیت پیدا میکند. در واقع این فرایند مزایای زیادی را ارائه میدهد که باعث کاربرد گسترده آن در صنایع مختلف شده است.
جمع بندی
متالورژی پودر روشی برای ساخت و تولید قطعات فلزی و غیر فلزی است که براساس فشردن پودر مواد، قطعه را تولید کرده و آن را زینترینگ میکند. در این روش، ضایعات تولید شده از سایر روشها بسیار کمتر است. این روش کاربردهای زیادی در صنعت دارد. بخصوص زمانی که نیاز به تولید محصولات با کیفیت مطلوب وجود داشته و امکان استفاده از سایر روشها وجود ندارد، میتوان از متالورژی پودر استفاده کرد.
متالورژی پودر همچنین به دلیل قابلیت اتوماسیون و سرعت بالا بخصوص برای قطعات کوچک و متوسط در تولید انبوه قطعات بسیار کاربرد دارد.
به طور کلی میتوان گفت که داشتن ویژگیهای مثبت و متعدد متالورژی پودر در کنار عملکرد مطلوب آن منجر به کاربرد متنوع و گسترده آن در صنایع مختلف شده و آن را به یکی از رایجترین فرایندها در صنعت مبدل کرده است.