در حالت کلی، جوشکاری با دو روش ذوبی و غیر ذوبی انجام میشود. جوشکاری مگ (MAG) از جمله تکنیکهای جوشکاری ذوبی است که در آن عملیات ذوب توسط قوس الکتریکی و یک الکترود انجام میشود. این فرایند در آغاز دهه 1980 میلادی منجر به ایجاد توسعه و پیشرفت چشمگیری در تکنولوژی جوشکاری و برش کاری شد. همچنین در اوایل دهه 1970 میلادی، جوشکاری مگ جایگزین جوشکاری با الکترود دستی شد تا جایی که در اواسط این دهه استفاده از جوشکاری قوسی با الکترود دستی به حد چشمگیری کاهش پیدا کرده و استفاده از فرایند جوشکاری با گاز محافظ مگ رونق پیدا کرد.
اگر میخواهید با فرایند جوشکاری مگ (MAG)، ویژگیها و کاربردهای آن بیشتر آشنا شوید، مطالعه این مقاله از فبرینو را از دست ندهید.
جوشکاری مگ چیست و چه کاربردهایی دارد؟
همانطور که گفته شد، جوشکاری مگ (Metal Active Gas) یا به اختصار جوشکاری (MAG) از تکنیکهای جوشکاری ذوبی است که فرایند جوش در آن توسط قوس الکتریکی انجام میشود. در این فرایند از Active Gas یا گاز فعال استفاده میشود. گاز فعال گازی است که در واکنش حوضچه مذاب مورد استفاده قرار میگیرد. در فرایند جوشکاری مگ گاز CO2 به کار میرود که معمولا برای جوشکاری فولاد ساده یا فولادهای کم آلیاژ مورد استفاده قرار میگیرد.
در فرایند جوشکاری MAG، گاز CO2 به گازهای CO (مونوکسید کربن) و O2 (اکسیژن) تجزیه میشود. گاز CO یک گاز خنثی و بی اثر است که از حوضچه جوش محافظت میکند. گاز O2 نیز با عناصر اکسید شونده قوی مانند Si و Mn که در سیم جوش پایه قرار دارند ترکیب میشود و به صورت سرباره ای نازک روی سطح جوش قرار میگیرد. امروزه در صنایع مختلف بیشتر از ترکیب گازهای خنثی و فعال استفاده میشود.
همچنین در طی فرایند جوشکاری مگ، گاز CO2 در مسیر حرکت خود حرارت را جذب کرده و باعث سرد شدن محیط میشود؛ به همین دلیل در حین جوشکاری گان و یا تورچ (مشعل) جوشکاری مگ حتی تا 400 آمپر به صورت سیستم خنک کننده با هوا مورد استفاده قرار میگیرند. این ویژگی نیز باعث کاربرد مفید این گاز در حین فرایند جوشکاری مگ (MAG) در صنایع مختلف شده است.
نحوه انجام جوشکاری مگ چگونه است؟
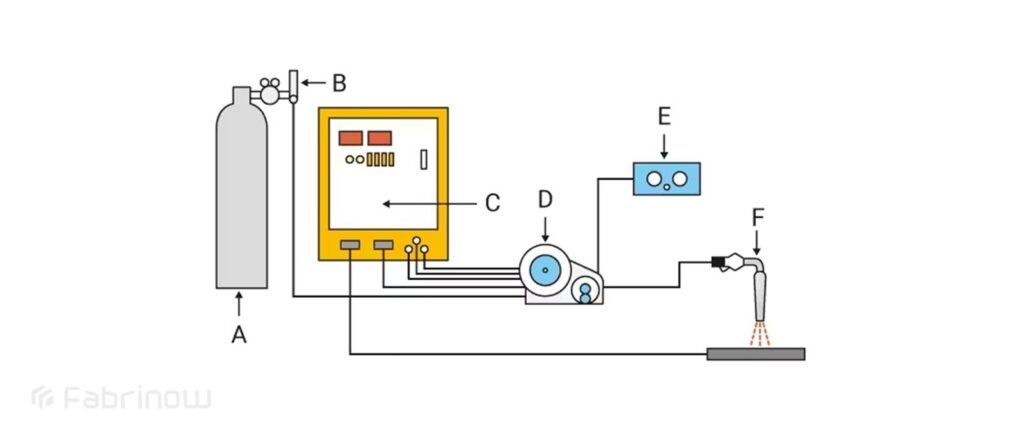
همانطور که گفته شد، در فرایند جوشکاری مگ (MAG) برای انجام عملیات از دی اکسید کربن یا همان گاز CO2 استفاده میشود که نسبت به سایر گازهای مورد استفاده در فرایندهای جوشکاری قوس الکتریکی، ارزان تر است. از این گاز هم میتوان در دستگاههای اتوماتیک و هم در دستگاههای نیمه اتوماتیک جوشکاری استفاده کرد. دی اکسید کربن همچنین خاصیت حفاظتی خوبی دارد اما به طول قوس بسیار حساس است. به همین دلیل در حین استفاده از این گاز، طول قوس باید ثابت نگه داشته شود.
در طی فرایند جوشکاری مگ (MAG) برای ثبات قوس و پیشگیری از ایجاد آسیب در آن، از الکترودهای روکش دار یا تنه کار استفاده شده و غالبا جریان مستقیم با قطب معکوس به کار میرود. جلوگیری از ورود گازهای موجود هوا یا همان گازهای اکسیژن و نیتروژن به منطقه جوش، در این فرایند منجر به ایجاد خواص شیمیایی و فیزیکی بهتری در جوش ایجاد شده میشود. در این روش همچنین قوس الکتریکی و حوضچه جوشکاری کاملا واضح است و در برخی موارد، یک لایه نازک سرباره روی گرده جوش را میپوشاند که این لایه در نهایت باید از روی سطح جوش برطرف شود.
از فرایند جوشکاری مگ (MAG) هم برای جوشکاری فلزات سخت و هم برای جوشکاری فلزات غیر سخت در تمامیضخامتها میتوان استفاده کرد و حتی برای جوشکاری صفحات فلزی نازک و مقاطع نسبتا ضخیم فلزات غیر سخت نیز بسیار کاربرد دارد.
تجهیزات مورد نیاز برای جوشکاری مگ
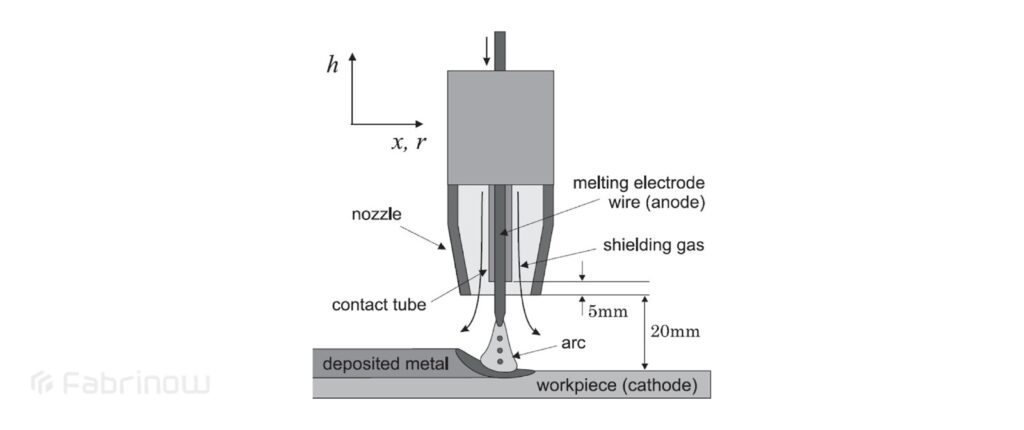
در جوشکاری مگ (MAG) برای انجام فرایند جوشکاری از یک سری تجهیزات و ابزارهای مختلف استفاده میشود؛ که مهم ترین و اصلی ترین آنها عبارتند از:
- منبع نیرو
در فرایند جوشکاری مگ (MAG) منبع نیرو ولتاژ مناسب برای تشکیل قوس و آمپر لازم برای ذوب را فراهم میکند. در این فرایند،از دستگاههای ولتاژ ثابت استفاده میشوند. همچنین غالبا تنها میتوان از جریان مستقیم با قطبیت معکوس DCRP استفاده کرد. البته در برخی موارد خاص، برای سیم جوشهای توپودری FCAW میتوان از جریان با قطبیت مستقیم DCSP استفاده کرد.
منبع نیروی مورد استفاده در این فرایند باید قابلیت تنظیم ولتاژ در محدوده کاری مناسب را داشته باشد. در برخی دستگاههای جوشکاری مگ (MAG)، تنظیم ولتاژ توسط کلیدهای پله ای در سایر دستگاهها توسط پتانسیومتر به صورت پیوسته تنظیم میشود. دستگاه جوشکاری با داشتن جریان پایین و انتقال اتصال کوتاه، باعث مهار سریع تر جریان شده و در نتیجه آن، جرقه کمتری پاشیده شده و سطح جوش بهتر میشود.
همچنین در صورتی که ضریب خودالقایی کم باشد، سیم الکترود به داخل حوضچه جوش فرو رفته و عمل اتصال کوتاه صورت میگیرد. در این حالت نیز جریان جوشکاری افزایش یافته و باعث انفجار مذاب و پاشش زیاد جرقه به اطراف میشود. در صورتی که ضریب خود القایی زیاد باشد نیز جریان اضافی به مدار اعمال شده، طول قوس افزایش یافته و طول الکترود کاهش مییابد. به همین منظور برای تنظیم ضریب خود القایی در قسمت جلوی دستگاه چندین فیش اتصال تعبیه شده است که اپراتور جوشکاری باید ضریب خودالقایی مناسب را توسط آنها تنظیم کند.
- سیستم تغذیه سیم
با استفاده از این سیستم، سیم جوش با یک سرعت ثابت به حوضچه جوش تغذیه میشود. سیستمهای تغذیه انواع زیادی دارند که اکثر آنها دارای سرعت ثابتی هستند. به این صورت که سرعت تغذیه سیم در آنها قبل از جوشکاری تنظیم شده و در حین فرایند جوشکاری این سرعت ثابت میماند. در مشعلهای دستی جوشکاری نیز، تغذیه سیم توسط یک کلید تعبیه شده در مشعل کنترل میشود.
اما سیستمهای تغذیه سیم که سرعت متغیری دارند، غالبا به همراه دستگاههای جریان ثابت استفاده میشوند. سیستمهای تغذیه سیم همچنین در انواع فشاری، کششی و فشاری-کششی موجود هستند که نوع تغذیه سیم در این دستگاهها غالبا به قطر سیم جوش، جنس سیم و طول مشعل بستگی دارد.
- سیستمهای تغذیه سیم فشاری: در این سیستمها، سیم جوش از قرقره توسط غلطکهای کشنده سیم با فشار به داخل مشعل رانده میشود. طول مشعلها در این سیستمها نیز تا 3.5 متر برای سیم جوشهای فولادی و تا 2 متر برای سیمهای آلومینیومیاست که به مقاومت و قطر سیم مصرفی بستگی دارد. از این سیستم میتوان برای سیم جوشهای سخت از قطر 0.8 تا 3.2 میلی متر و سیمهای نرم مانند آلومینیوم از قطر 1.2 تا 2.5 میلی متر استفاده کرد.
- سیستمهای تغذیه سیم کششی: از این سیستمها غالبا زمانی استفاده میشود که وزن رسوب جوش کم بوده و جوشکاری در یک فضای محدود انجام میشود. همچنین این سیستم برای جوشکاری ورقهای نازک نیز بسیار کاربرد دارد. در واقع سیستمهای تغذیه کششی خود بسیار ظریف و کم حجم هستند و میتوان به سادگی با آنها کار کرد. این سیستمها به مکانیزم تغذیه سیم مجهز هستند.
- سیستمهای تغذیه سیم کششی-فشاری: در این سیستمها مشعل به یک موتور و غلطکهای تغذیه سیم مجهز است که به عنوان یک راهنما برای کنترل سرعت تغذیه عمل میکند. در واقع، سرعت تغذیه سیم با کشش سیم موتور مشعل تنظیم میشود. از این سیستمها غالبا برای سیمهای نرم مانند سیمهای آلومینیومیبا قطر کم تا طول 15 متر و یا بیشتر و همچنین برای مشعلهایی با طول بلند استفاده میشود.
- مشعل (تورچ) جوشکاری: این ابزار وظیفه رساندن جریان الکتریکی، گاز محافظ و سیم جوش به حوضچه جوش را برعهده دارد که به عنوان انبرهای جوشکاری نیز شناخته میشوند. سیم جوش یا همان الکترود جوشکاری از وسط مشعل عبور کرده و سرعت آن نیز از قبل تنظیم میشود. انتقال جریان الکتریکی به سیم جوش نیز هنگام خروج سیم از مشعل انجام شده و گاز محافظ نیز از سر مشعل خارج میشود.
مشعلهای جوشکاری مگ (MAG) بسته به سیم خنک کننده دارای دو نوع آب خنک و هوا خنک هستند که مشعلهای هوا خنک ارزان تر و سبکتر بوده و برای آمپرهای کمتر از 200 و کارهای غیرمداوم مورد استفاده قرار میگیرند. مشعلهای آب خنک نیز برای آمپرهای بالا و کارهای مداوم استفاده میشوند.
سیستم گاز محافظ: این سیستم نیز در جوشکاری مگ (MAG) وظیفه محافظت از حوضچه جوش را برعهده دارد. در واقع این سیستم از حوضچه جوش در برابر عناصر مضر هوا محافظت میکند.
تفاوت جوشکاری میگ و مگ
جوشکاری میگ و مگ هر دو جزو فرایندهای جوشکاری ذوبی هستند که با استفاده از گاز محافظ انجام میشوند. تفاوت این دو روش جوشکاری در نوع گاز محافظ مورد استفاده است. در جوشکاری (MAG) از گاز محافظ فعال (Active Gas) مانند گاز کربن دی اکسید و یا گازهای فعال ترکیب شده با گاز خنثی استفاده میشود. اما در جوشکاری میگ MIG (Metal Inert Gas) گازهای خنثی (Inert Gas) برای جوشکاری مورد استفاده قرار میگیرند.
از جمله گازهای فعال پرکاربرد در جوشکاری مگ (MAG) میتوان به گازهای دی اکسید کربن، اکسیژن، هیدروژن و نیتروژن اشاره کرد. استفاده از این گازها در طی فرایند جوشکاری منجر به افزایش پایداری قوس، کاهش سیالیت حوضچه مذاب و افزایش دمای قوس میشود.
در جوشکاری میگ (MIG) نیز غالبا از 100% گازهای خنثی و محافظ آرگون و یا هلیوم استفاده میشود که معمولا کیفیت بهتری نسبت به جوشکاری مگ ارائه میدهد اما قیمت آن بالاتر است. در واقع این گازها هیچ واکنشی با حوضچه مذاب جوشکاری ندارند.
انتخاب تکنیک مگ (MAG) یا تکنیک جوشکاری میگ (MIG) کاملا به دستورالعمل جوشکاری WPS بستگی دارد و بهتر است انتخاب این روشها براساس این دستورالعمل و یا زیر نظر متخصص انجام شود.
صنایع پرکاربرد جوشکاری مگ
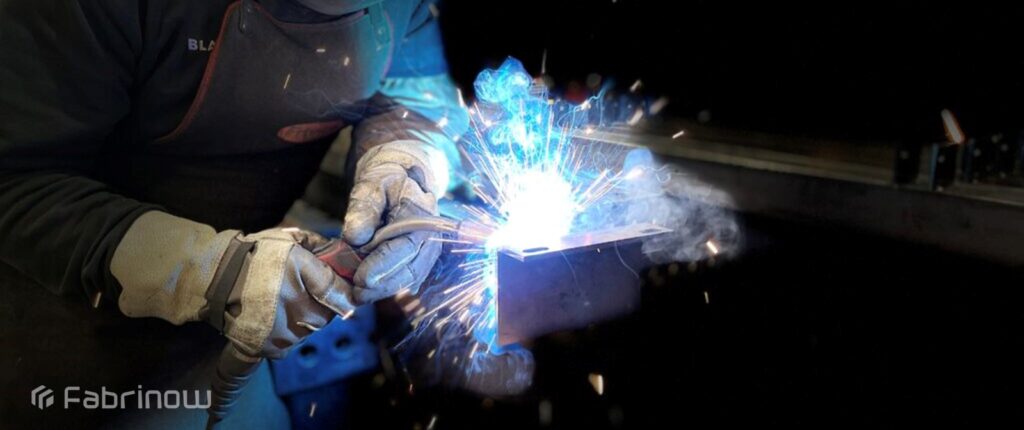
جوشکاری مگ (MAG) ویژگیهای متعددی اعم از کارایی، کیفیت مطلوب، سرعت بالا و انعطاف پذیری در استفاده از فلزات مختلف دارد. به همین دلیل در صنایع متعددی مورد استفاده قرار میگیرد. از جمله مهم ترین صنایع ترین پرکاربرد جوشکاری مگ میتوان به موارد زیر اشاره کرد:
- صنایع دریایی: برای تولید و تعمیر کشتیها و سازههای دریایی مانند پلتفرمهای نفتی زیر دریا و یا سایر سازههای دریایی با امکان استفاده در شرایط زیرآبی
- صنعت تولید و تعمیر هواپیما: برای تولید و یا تعمیربخشهای مختلف فلزی هواپیما بخصوص برای تولید بدنه هواپیما و اتصالات مورد استفاده
- صنعت برق و الکترونیک: برای اتصال بخشهای مختلف فلزی در تولید اجزای الکترونیکی و تجهیزات برقی
- صنایع نظامی: برای تولید و یا تعمیر تجهیزات و اتصالات نظامی
عیوب شایع در جوشکاری مگ
در برخی مواقع، به دلیل استفاده از پارامترها و موارد نامناسب و یا به دلیل انجام نادرست فرایند، یک سری عیوب در جوشکاری مگ (MAG) ایجاد میشوند که در قسمت کنترل کیفیت از طریق آزمایشات مختلف این عیوب با استانداردهای مربوطه مقایسه شده و قبول یا رد میشوند.
دلایل ایجاد این عیوب شایع که میتوانند در ایستگاه جوشکاری مگ ایجاد شوند عبارتند از:
- عیوب مربوط به قطعه گذاری نامناسب
- عیوب مربوط به تورچ و شعله پوش
- عیوب ناشی از نامناسب بودن سطح کار مانند آغشته بودن سطح به روغن، رنگ، زنگ زدگی سطح و یا آبکاری نامناسب
- عدم مهارت جوشکاری در اجرای فرایند جوشکاری
- عیوب مربوط به خارج از اندازه بودن ابعاد جوش
- مشکلات مربوط به تغییر حالت سرشاسی و دفرمگی قطعات و فاصله هوایی آنها
- تنظیم نبودن پارامترهای دستگاه جوش اعم از جریان، ولتاژ، سرعت تغذیه سیم و میزان عبور گاز محافظ
به این دلایل عیوب مختلفی روی جوش نهایی فرایند جوشکاری مگ (MAG) ایجاد میشوند که از جمله مهم ترین و شایع ترین این عیوب میتوان به موارد زیر اشاره کرد:
- سوراخ شدن و ریزش جوش: در صورتی که فلز جوش بیش از اندازه در قطعات جوش نفوذ کند، حوضچه مذاب باعث سوراخ شدن ریشه جوش شده و پایین میریزد. تولید گرمای بیش از حد نیز منجر به سوختن سیم جوش و احتمالا سوختن قسمتی از سطح قطعه کار خواهد شد. این مورد غالبا به دلیل عدم تنظیم صحیح پارامترهای دستگاه جوشکاری و یا عدم مهارت جوشکار ایجاد میشود.
- نفوذ بیش از جد یا ناقص مذاب در قطعه کار: در صورتی که فرایند جوشکاری با سرعت بالا انجام نشود، سیم جوش CO2 به طور کامل به محل اتصال دو قطعه کار نمیرسد و در صورت قطعه کار پیش از حد گود شده و مذاب نیز بیش از اندازه به قطعه کار نفوذ میکند.
- ایجاد خوردگی: زمانی که جوش پایین تر از کنارههای لبه جوش قرار بگیرد، عیب خوردگی ایجاد میشود. این مورد غالبا به دلیل تمرکز زیاد حرارت در محل جوش و یا بکارگیری روش نامناسب برای انجام پروسه جوشکاری موردنظر ایجاد میشود.
در برخی موارد برای انجام جوشکاری مگ (MAG) از ورقهای گالوانیزه استفاده میشود. این ورقها حین جوشکاری از طریق پوشش گالوانیزه وارد مذاب شده و غالبا باعث ایجاد عیوب زیر میشوند:
- باعث تردی و بالا بردن میزان حساسیت در برابر ترک برداشتن میشود.
- سوختن و بخار شدن این ورقها منجر به ایجاد دود سفیدی میشود که این دود منجر به عدم رویت کامل عملیات جوشکاری برای جوشکار شده و حتی باعث ایجاد مشکلات تنفسی میشود.
- در گرده جوش حفره و تخلخل ایجاد میکنند.
مزایا، معایب و محدودیتهای جوشکاری مگ
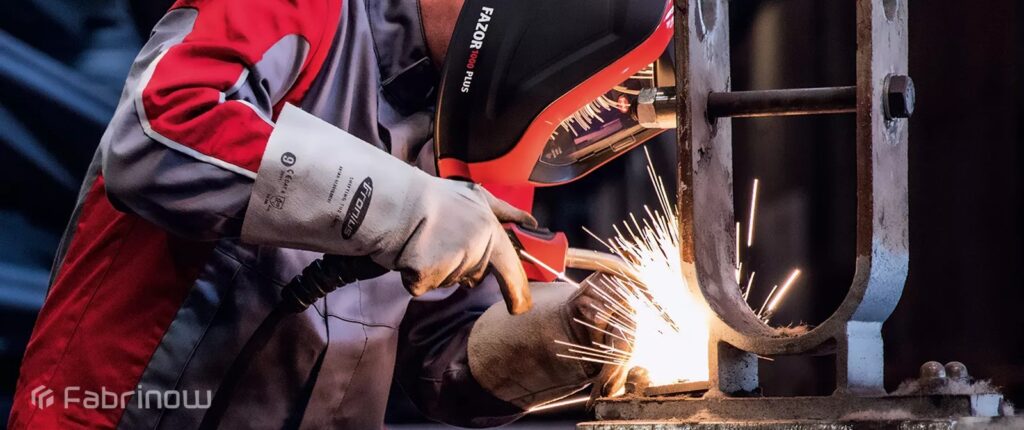
همانند تمامیفرایندهای صنعتی جوشکاری مگ (MAG) نیز دارای ویژگیهایی است که این ویژگیها منجر به کاربرد این فرایند در صنایع مختلف شده اند. از جمله مهمترین مزایای این فرایند میتوان به موارد زیر اشاره کرد:
- تغذیه سیم در این فرایند به طور مداوم انجام شده و نیاز به توقف جوشکاری برای تعویض الکترود و ابزار نخواهد بود.
- در این فرایند غالبا نیاز به برطرف کردن سرباره از سطح جوش وجود ندارد.
- در این فرایند از سیم جوش با قطر کمتری نسبت به فرایند جوشکاری دستی استفاده میشود. به همین دلیل به شدت جریان بیشتری نیاز است و در نتیجه آن نرخ رسوب افزایش مییابد.
- در این فرایند هیدروژن کمتری به فلز جوش جذب میشود که این مورد در استفاده از فولادهای حساس به ترک هیدروژنی بسیار اهمیت دارد.
- با استفاده این فرایند امکان جوشکاری انواع ورقها با ضخامتهای مختلف، حتی ورقهای کمتر از 2 میلیمتر وجود دارد.
- امکان انجام این فرایند به صورت کاملا اتوماتیک وجود دارد.
- فرایند جوشکاری مگ یک فرایند نسبتا ساده است که آموزش آن نیاز به زمان کمیدارد.
- در این فرایند غالبا از گاز CO2 که یک گاز فعال است برای انجام جوشکاری استفاده میشود. این گاز همچنین قیمت بسیار کمیداشته و در محل قوس الکتریکی به گازهای CO و O تجزیه میشود.
- جریانی که در هنگام استفاده از گاز دی اکسید کربن مصرف میشود، معمولا باعث تلاطم بیشتر حوضچه مذاب شده و در نتیجه آن حبابهای گازهای موجود در داخل جوش به سطح فلز صعود میکنند و قبل از انجماد از آن خارج میشوند. در این حالت تخلخل جسم کمتر خواهد بود.
- در این فرایند گازها و سایر مواد موجود قبل از جامد شدن و سرد شدن جوش از آن خارج میشوند.
- این فرایند به سادگی میتواند در تمامیوضعیتها مورد استفاده قرار گرفته و حوضچه مذاب و قوس الکتریکی در آن به وضوح قابل مشاهده خواهند بود.
- در این فرایند از یک الکترود با قطر نسبتا کم استفاده میشود که باعث بالا رفتن چگالی جریان شده و درصد بالایی از سیم جوش در منطقه اتصال رسوب خواهد شد.
در کنار تمامیاین مزایا، فرایند جوشکاری مگ (MAG) یک سری محدودیتها و معایب را نیز شامل میشود که عبارتند از:
- تجهیزات مورد نیاز این فرایند قیمت بالاتری داشته و قابلیت حمل و نقل سخت تری دارد.
- در این فرایند مشعل باید همواره به سطح قطعه کار نزدیک باشد؛ به همین دلیل جوشکاری قسمتهایی که دسترسی به آنها مشکل است، سخت تر خواهد بود.
- در این فرایند به دلیل عدم وجود سرباره و کاهش سرعت سرد شدن، احتمال ترک در جوشکاری فولادی سخت وجود دارد.
- در این روش جوشکاری، به دلیل وزش باد، گاز محافظ از سطح حوضچه جوش پراکنده شده و فلز جوش آلوده میشود. به همین دلیل نیاز به حفاظت قوس در مقابل جریان باد وجود دارد.
در این فرایند جوشکاری به دلیل استفاده از تجهیزات بیشتر نسبت به فرایندهای جوشکاری دیگر، معایب و محدودیتهای بیشتری دارد. اما در صورت استفاده از تجهیزات مناسب و مواد مصرفی با کیفیت مانند گاز CO2 مرغوب و خالی از رطوبت، سیم جوش متناسب با زاویه جوشکاری و قطعه کار عاری از آلودگیهایی مانند چربی، زنگ زدگی، رنگ و…، این محدودیتها و معایب تا حد زیادی کاهش پیدا میکنند.
نکات پر اهمیت فرایند جوشکاری مگ (MAG)
همانطور که خواندید، فرایند جوشکاری مگ با استفاده از گاز فعال دی اکسید کربن (CO2) انجام میشود. هنگام استفاده از این گاز و حین فرایند جوشکاری مگ (MAG) توجه به موارد زیر، برای کیفیت بهتر جوش، اهمیت دارد:
- در این فرایند پس از مانومتر کپسول، باید گرمکن گاز را نصب کرد.
- قبل از شروع فرایند جوشکاری بهتر است از عملکرد صحیح گرمکن اطمینان پیدا کرد.
- در حین فرایند جوشکاری، بخصوص جوشکاریهای طولانی مدت، تمیز کردن فنر تورچ از هر گونه آلودگی بسیار اهمیت دارد؛ در غیر اینصورت فنر دچار مشکل خواهد شد.
- آمپر و ولتاژ جوش باید با یکدیگر همخوانی داشته باشند. این پارامترها زمانی همخوانی دارند که صدای ریزش قطرات سیم جوش هنگام کار به صورت مداوم شنیده شود.
- پس از تنظیم ولتاژ و آمپر دستگاه، خروجی کابل اتصال منفی روی دستگاه جوش بررسی شود.
- میزان حرارت مورد نیاز برای انتقال به قطعه باید نسبت به ضخامت قطعه انتخاب شود.
- فاصله نوک نازل سیم جوش تا نوک شعله نیز اهمیت دارد. برای این منظور غالبا بهتر هنگام استفاده از گاز دی اکسید کربن، این فاصله به میزان 2mm و هنگام استفاده از ترکیب گاز دی اکسید کربن و گاز آرگون این فاصله به میزان 8mm انتخاب شود.
- بهتر است زاویه جوشکاری نسبت به خط عمود بر کار بیشتر از 25 درجه نباشد؛ در غیراینصورت فاصله سیم آزاد افزایش پیدا کرده و امکان ریختن تمام مقدار گاز محافظ روی حوضچه جوش وجود خواهد داشت. همچنین روی جلوگیری از چسبیدن جرقهها به داخل شعله جوش و اطراف نازل سیم جوش، موثر خواهد بود.
- بهتر است در فواصل بین عملیات و بعد از تمیز کردن آثار جرقهها نیز از اسپری ضد جرقه استفاده شود.
سوالات متداول
در صنعت جوشکاری مگ (MAG) از چه فلزاتی استفاده میشود؟
غالبا از این فرایند میتوان برای جوشکاری انواع فلزات با ضخامتهای مختلف استفاده کرد. اما ورقهای گالوانیزه در حین فرایند جوشکاری مگ از طریق پوشش گالوانیزه وارد مذاب شده و در اثر سوختن و بخار شدن منجر به ایجاد دود سفید و خطرناکی میشوند.
همچنین با استفاده از این ورقها تردی جوش افزایش یافته و میزان حساسیت آن در مقابل ترک برداشتن نیز افزایش مییابد. این ورقها همچنین ممکن است باعث ایجاد حفره و تخلخل در گرده جوش شوند.
جرقههای صنعت جوشکاری مگ چگونه ایجاد میشوند؟
در این فرایند برای جلوگیری از چسبیدن جرقه به داخل ضعله پوش و اطراف سیم نازل، غالبا در ابتدا و در حین عملیات جوشکاری از اسپری ضدجرقه استفاده میشود. این قطرات ریز از منطقه جوش در بین اتصالات ذوبی به اطراف پرتاب میشوند و میتوانند از حوضچه جوش یا سیم جوش پرکننده ناشی شده باشند.
زمانی که دانههای کروی و مذاب قطرات از سیم جوش به طرف حوضچه جوش منتقل میشوند، منجر به ایجاد پوش در فاصله قوس شده که به این واسطه یک مدار بسته یا اتصال کوتاه ایجاد میشوند. عبور شدت جریان از این مدار باعث گداخته شدن این مدار شده و با انفجار آن بارانی از جرقههای گداخته به وجود خواهد آمد.
در چه صورتی جوش فرایند جوشکاری مگ سوراخ و یا ریز میشود؟
در صورتی که فلز جوش بیش از اندازه در قطعات جوش دادنی نفوذ کند، حوضچه جوش منجر به سوراخ شدن ریشه جوش شده و پایین میریزد. تولید شدن بیش از حد حرارت نیز منجر به سوختن سیم جوش و مقداری از سطح قطعه کار خواهد شد. این مشکل بیشتر به دلیل عدم انتخاب صحیح پارامترهای دستگاه جوشکاری و یا عدم مهارت جوشکار ایجاد میشود.
ضخامت فلزات مورد استفاده در جوشکاری مگ باید چقدر باشد؟
از فرایند جوشکاری مگ غالبا میتوان برای فلزات با ضخامتهای مختلف استفاده کرد. حتی امکان جوشکاری ورقهایی با ضخامت 0.5 میلی متر نیز توسط این فرایند وجود دارد. گرچه این فرایند برای جوشکاری فلزات با ضخامتهای بیشتر و حتی قطعات با ضخامت 12 میلی متر نیز قابل استفاده است اما غالبا برای جوشکاری قطعات ضخیم تر از 12 میلی متر از فرایندهایی مانند جوشکاری زیرپودری استفاده میشود.
جمع بندی
جوشکاری مگ (MAG) از جمله فرایندهای رایج جوشکاری ذوبی است که در آن از گازهای فعال برای انجام فرایند جوشکاری استفاده میشود. گاز رایج مورد استفاده در این فرایند گاز دی اکسید کربن است اما در برخی موارد برای کاربردهای مختلف میتوان از گازهای مختلف در ترکیب با گاز دی اکسید کربن برای انجام فرایند جوشکاری استفاده کرد. فرایند جوشکاری مگ غالبا سرباره نداشته و میزان جرقه آن بسیار کمتر است.
همچنین در این فرایند درصد بالایی از سیم جوش در منطقه اتصال رسوب کرده و حتی از الکترودی با قطر نسبتا کم استفاده میشود که باعث افزایش چگالی جریان میشود. این ویژگیها و سایر ویژگیهای جوشکاری مگ باعث شده است که امروزه این فرایند به عنوان یکی از فرایندهای جوشکاری شناخته شود که کاربردهای متنوعی در صنایع گوناگون دارد.